Gli ingranaggi e-drive si differenziano dagli altri componenti automotive per due punti essenziali: una maggiore qualità e la necessità di un eccellente comportamento acustico. Un nuovo concetto di ispezione sviluppato da Gleason presenta una combinazione di test di rotolamento a doppio fianco e scansione laser.
Le trasmissioni nei veicoli a trazione elettrica sono più sensibili a problemi di rumore rispetto a quelle utilizzate nei veicoli con motore a combustione interna convenzionale (ICE) per due motivi. In primo luogo, il numero di giri in ingresso del motore elettrico, che può arrivare fino a 30.000 giri/min o anche 50.000 giri/min [1], è significativamente superiore a quello di un motore a combustione, che a seconda del carburante (diesel vs benzina) arriva a max 5.000 – 8.000 giri/min. Ciò aumenta lo spettro di eccitazione potenziale di un fattore 3-10 [2]. In secondo luogo, il rumore di mascheramento della combustione stessa non è presente nel caso di propulsore elettrico, il che rende il rumore proveniente dalla trasmissione più evidente. Pertanto, comprendere e influenzare le potenziali fonti di rumore degli ingranaggi è più importante che mai.
Il rumore di un cambio inizia come una vibrazione eccitata dall’ingranamento. Questa vibrazione viene trasmessa come “rumore trasportato dalla struttura” attraverso gli elementi meccanici quali i cuscinetti gli alberi… fino a raggiungere la cassa che funge da corpo di risonanza. Da qui la vibrazione si propaga in aria fino a raggiungere l’orecchio umano.
Sono presenti diverse fonti di eccitazione, tra cui l’ingranamento, la fluttuazione della coppia dal motore elettrico, lo squilibrio dell’albero, i cuscinetti. In questo articolo, ci si concentrerà sull’ingranamento. Le cause che portano a vibrazioni nell’ingranamento sono molteplici. Ad esempio, durante l’ingranamento si una rigidezza variabile, che può essere influenzata positivamente o negativamente dalle modifiche del fianco del dente, o da errori di fabbricazione. Inoltre, a causa del carico applicato, le deformazioni elastiche dei denti, degli alberi e dell’alloggiamento possono portare a un contatto prematuro e/o prolungato del dente e quindi ad un’ulteriore fonte di vibrazioni.
Infine, le trame superficiali del fianco e tutti i tipi di errori-irregolarità di fabbricazione portano anch’essi a piccole deviazioni e possono avere un effetto significativo sull’emissione acustica.
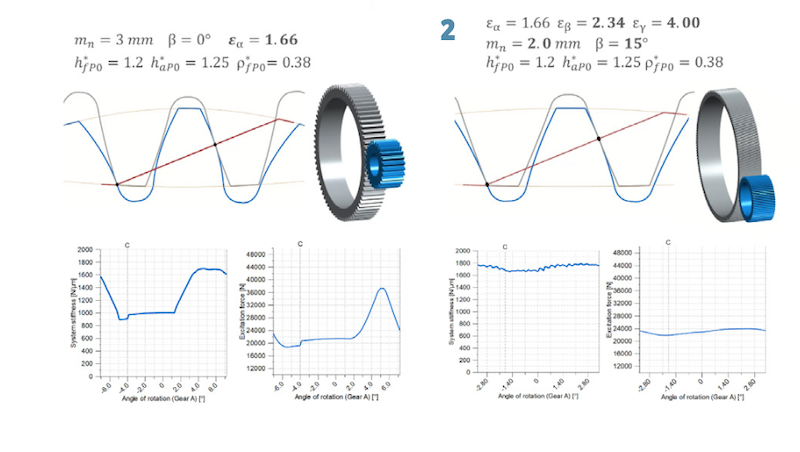
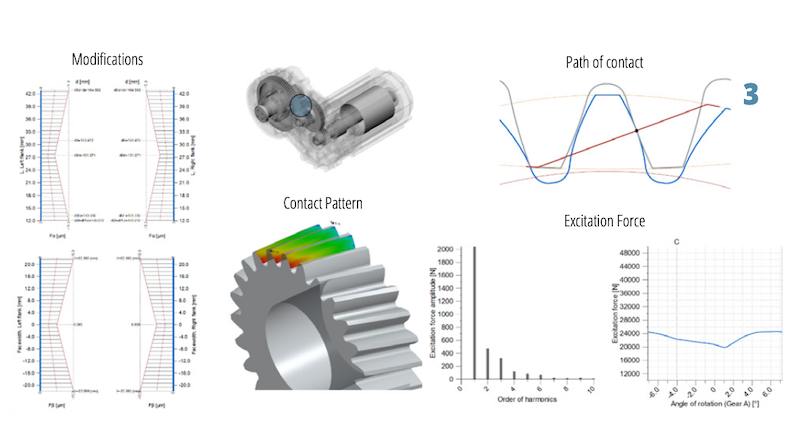
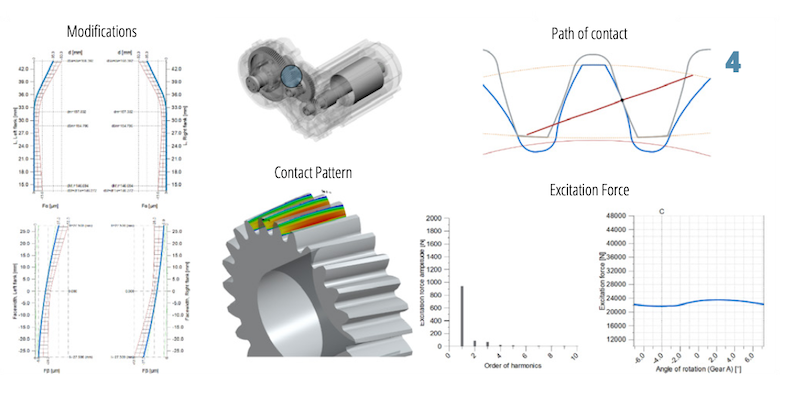
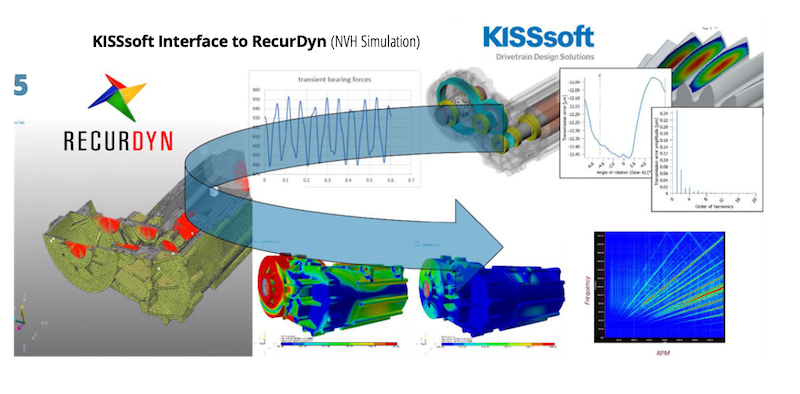
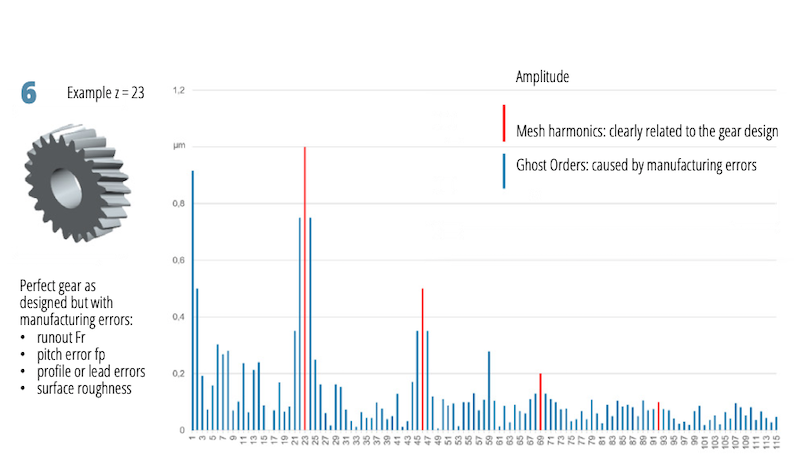
Ottimizzazione del rumore degli ingranaggi
Affinché un sistema di ingranaggi funzioni silenziosamente, deve prima essere progettato in base alle caratteristiche di carico che si avranno in esercizio. Oggigiorno sono disponibili strumenti di sviluppo specifici per questo scopo, con i quali gli ingranaggi e gli altri componenti della trasmissione possono essere progettati per un comportamento ottimizzato.
Lo strumento KISSsoft utilizza una procedura a più fasi per l’ottimizzazione degli ingranaggi. Dapprima viene progettata la macro-geometria. Lo strumento calcola centinaia di soluzioni diverse in base a criteri di progettazione specifici selezionati dall’utente. Spesso, si cercano soluzioni aventi rapporto di condotta elevati. Di norma, questa analisi preliminare porta già a rigidezze del sistema relativamente costanti durante l’ingranamento (senza eccessive fluttuazioni), a patto che vengano calcolati non solo i valori teorici ma anche quelli sotto carico. Questo passaggio è auspicabile e porta a forze più omogenee e, quindi, ad errori di trasmissione costanti. Questi sono la vera causa dell’emissione acustica.
La Figura 2 riporta il confronto tra gli effetti di due diversi design sulla rigidezza del sistema e le relative forze. La parte sinistra mostra il design di un ingranaggio cilindrico secondo un profilo rack DIN standard con altezza del dente di 2,25 x mn. Il rapporto di condotta trasversale è pari a 1,66. La rigidezza del sistema varia notevolmente da 900 a 1700 N/μm. Di conseguenza, la forza di eccitazione mostra anch’essa un andamento fortemente fluttuante. A destra, invece, viene mostrata una variante elicoidale che, con un rapporto di ricoprimento di 2,34, porta a un rapporto di condotta pari a 4. Come risultato, sia la rigidezza del sistema che le forze di eccitazione mostrano un andamento quasi costante durante tutto l’ingranamento. Tuttavia, poiché questa fase di progettazione non considera i carichi e le deformazioni dei componenti, si rende necessario uno step successivo che ne tenga conto.
Nell’analisi del contatto dei denti caricati (LTCA), la deformazione dei denti e dei componenti del sistema viene calcolata in presenza dei carichi reali con conseguente modifica del modello di contatto, dell’errore di trasmissioni, delle forze di eccitazione… In questa fase, anche il modello di contatto viene ottimizzato selezionando le modifiche più appropriate. Ad esempio, vengono incluse nel calcolo le concentrazioni di carico causate dalla deformazione dell’albero, dell’alloggiamento, del corpo dell’ingranaggio o del cuscinetto. Tali deformazioni vengono bilanciate applicando modifiche al fianco.
Le modifiche del profilo aiutano a correggere il contatto prematuro e/o ritardato dei denti causato dalla deflessione dei denti. Queste aiutano quindi ad ottenere errori di trasmissione abbastanza costanti anche per diversi livelli di coppia [4]. Tra le modifiche più utilizzate vi sono la bombatura del profilo e/o lo smusso di testa. I risultati di un’analisi del contatto del dente caricato sono mostrati nelle Figure 3 e 4.
La Figura 3 mostra il caso non modificato. Il modello di contatto vede chiaramente la presenza di carichi eccessivi sul lato I (lato sinistro), in particolare a piede dente, dove il raggio di curvatura è inferiore. Inoltre, il contatto evidenzia un impegno esteso del dente. Tutto ciò si traduce in forze di eccitazione non ottimali (come illustrato in Figura 3 in basso a destra: forza vs. angolo di rotazione). Si possono osservare chiaramente forze di eccitazione fluttuanti durante l’ingranamento, con presenza di armoniche di ordine molto elevato.
Al contrario, la Figura 4 mostra la situazione dopo un’ottimizzazione. Da un lato, si sono selezionate modifiche al fianco tali da evitare un carico eccessivo sul lato I e, dall’altro, modifiche del profilo (bombatura e smusso di testa) per ottenere un modello di contatto il più uniforme possibile. L’impegno prolungato del dente risulta così eliminato., Questo appare evidente analizzando il percorso di contatto. Inoltre, il grafico delle forze di eccitazione risultanti mostra una curva molto più costante: l’armonica del primo ordine è dimezzata, mentre le armoniche più alte sono notevolmente ridotte.
Per determinare gli effetti di queste forze di eccitazione sulla emissione acustica del cambio, KISSsoft dispone di un’interfaccia con Recurdyn, un software di simulazione multi-body. Le curve di eccitazione alle diverse velocità vengono calcolate in KISSsoft e trasferite a Recurdyn l, che simula il comportamento vibro-acustico e calcola i diagrammi di Campbel (Figura 5). Un esempio molto impressionante di tale simulazione e ottimizzazione NVH è stato descritto da Marano et al [3].
Sebbene i progressi nella simulazione del comportamento vibro-acustico siano impressionanti, non tengono ancora conto degli errori di produzione. È noto dall’esperienza pratica che le più piccole deviazioni e ondulazioni sui fianchi dei denti possono influenzare in modo importante il comportamento vibro-acustico del sistema. Oltre agli strumenti di simulazione, vengono quindi utilizzati altri metodi di analisi. Un metodo molto noto e significativo è il test sul fianco singolo (SFT). In questa tipologia di prova, l’ingranaggio da testare, con tutti i suoi difetti di fabbricazione, viene fatto ingranare con un ingranaggio master o con un altro ingranaggio reale. Le deviazioni angolari (errori di trasmissione) vengono misurate e analizzate. È comune trasformare il segnale dal dominio del tempo al dominio delle frequenze ed effettuare un’analisi degli ordini.
Un esempio di analisi degli ordini di un ingranaggio con 23 denti è mostrato in Figura 6. Prima di tutto, si possono vedere ampiezze distinte al 23° ordine e i suoi multipli (in rosso). Questi picchi sono le cosiddette armoniche della frequenza di ingranamento. Anche queste potrebbero anche essere simulate e incluse nella fase di progettazione. Tuttavia, si possono vedere anche numerosi altri ordini che si trovano tra le armoniche principali. Questi ordini sono spesso chiamati anche “Ghost Orders” (o frequenze fantasma), perché non possono essere chiaramente ricondotti alla geometria dell’ingranaggio o al numero di denti. Tutti questi ordini provengono chiaramente da errori di fabbricazione. Un tipico run-out radiale Fr si presenta, ad esempio, come la nascita di bande laterali attorno alla frequenza di ingranamento. Il 59° ordine di questo esempio potrebbe essere un ordine fantasma critico che porta all’emissione acustica. Questo metodo (SFT) consente di impostare disallineamenti degli assi, applicare e testare carichi diversi… Lo svantaggio è che sono necessarie apparecchiature di prova aggiuntive. Pertanto, negli ultimi anni sono stati sviluppati metodi per migliorare le analisi degli ordini sulla base di misure analitiche acquisite con apparecchiature standard spesso già disponibili. Un metodo noto è la cosiddetta analisi dell’ondulazione che è descritta più dettagliatamente in seguito. Lo svantaggio di questo metodo è, da un lato, che la l’ingranamento viene simulato solo sulla base dei dati di misura e, dall’altro, che il tempo di misura richiesto per questo test è molto elevato. Pertanto, questo metodo non ha visto una larga implementazione nella produzione di serie.