sempre più barrette in metallo duro
Per la dentatura degli ingranaggi conici spiroidali di media-grande dimensione e, soprattutto nelle produzioni di grandi volumi, si usano sempre più le barrette in metallo duro. Qual è la precisione raggiunta da questi utensili?
L’utilizzo delle dentatrici a controllo numerico che usano le barrette in metallo duro ha permesso un notevole aumento delle velocità di taglio e il taglio a secco, accompagnato da una drastica riduzione dei tempi ciclo.
Oltre a ciò le barrette permettono un numero elevato di riaffilature e quindi il numero di pezzi eseguibili con un set di barrette è molto grande.
Tuttavia le moderne dentatrici Cnc hanno un costo notevole; inoltre, per il corretto impiego delle barrette in metallo duro, sono necessarie delle affilatrici speciali e apparecchi di controllo altrettanto costosi; ragion per cui solo grandi produttori di ingranaggi che operano in specifici ambiti hanno adeguato al meglio la loro tecnologia di dentatura.
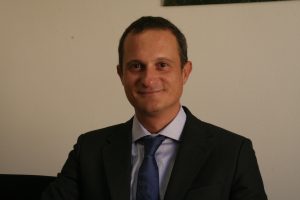
Le aziende che producono barrette in metallo duro per ingranaggi conici non sono molte. Fra queste c’è miniToolsCoating di Padova, che ha investito molto in macchinari specifici per la produzione, il controllo e i servizi di rigenerazione utensili, come ci racconta il direttore generale Giovanni Chinaglia.
Esistono diversi tipi di barrette con differenti profili di affilatura e diverse dimensioni dello stelo. Ciò moltiplica i problemi tecnici della loro costruzione.
In linea di massima, le barrette si differenziano perché le due principali aziende che producono le macchine dentatrici per ingranaggi conici, cioè Gleason e Klingelnberg (Oerlikon), usano tecnologie diverse.
Le barrette attualmente utilizzate sulle macchine Gleason hanno la sezione del corpo pentagonale, mentre quello montate sulle macchine Klingelnberg hanno un corpo con sezione rettangolare.
Dentatura di ingranaggi conici: sempre più barrette
La fabbricazione delle barrette in metallo duro presenta delle difficoltà che possono essere risolte solo da chi possiede una lunga esperienza nel settore.
Queste difficoltà derivano in sintesi dalla precisione geometrica richiesta che è, nelle varie quote, dell’ordine del micrometro. Si parte da una barretta grezza ottenuta per sinterizzazione che evidentemente ha delle tolleranze molto ampie. Si tratta di rettificare le varie facce, quattro nelle barrette a sezione rettangolare e cinque nelle barrette a sezione pentagonale, in modo che siano rispettate le quote dimensionali e le tolleranze geometriche con precisione di pochi micrometri.
In quelle a sezione rettangolare, con le stesse tolleranze, deve essere rispettato il parallelismo tra due facce contrapposte e l’ortogonalità tra le facce adiacenti.
Mentre è relativamente facile rispettare la tolleranza di parallelismo tra due facce contrapposte, è più problematico avere la stessa precisione nell’ ortogonalità tra le altre due coppie di piani.
Bisogna evidenziare che, poiché gli utensili vengono realizzati impiegando dei set di barrette con numero variabile tra i 12 ai 40 pezzi, è particolarmente rilevante che le barrette siano tutte “una uguale all’altra”, pezzo dopo pezzo, lotto dopo lotto, anno dopo anno.
La miniToolsCoating ha raggiunto un notevole grado di sofisticazione nello sviluppo di tecnologie di lavorazione in grado di mantenere costante la qualità del prodotto in ogni singolo lotto e nel complesso della produzione.
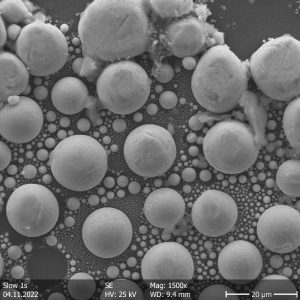
La precisione dello stelo è molto importante ai fini della qualità degli ingranaggi prodotti con il taglio a barrette.
Infatti, errori su parallelismo, quadratura e dimensioni generano errori in fase di esecuzione del profilo e scostamenti nel posizionamento delle barrette una volta montate sul corpo fresa.
La rettifica del corpo delle barrette a sezione pentagonale è ancora più difficoltosa dal punto di vista tecnico, perché bisogna rispettare la posizione angolare di ogni singola faccia, anche qui con tolleranze dell’ordine del micrometro.
Quando la rettifica delle facce è conclusa si devono eseguire i profili di taglio veri e propri.
L’utilizzatore può scegliere tra tre opzioni:
- utilizzare barrette profilate internamente;
- utilizzare barrette con un profilo sbozzato per facilitare le lavorazioni di finitura;
- acquistare barrette complete di profilo finito e rivestite.
Eseguire il profilo partendo dalla barretta grezza è un’operazione lunga e dispendiosa; più logica è la seconda opzione e, ancora migliore, è l’impiego di barrette finite e pronte all’uso, anche perché per performance ottimali le barrette vanno alla fine rivestite.
L’importanza di una buona rigenerazione
La corrispondenza tra il profilo realizzato sulla barretta con quello previsto dal progetto permette di ottenere il massimo rendimento dell’utensile e la massima precisione sui pezzi dentati. Questo vale naturalmente per ogni tipo di utensile, ma è particolarmente vero se parliamo delle barrette in metallo duro.
La ripetitività entro pochi micron dei profili di tutte le lame che compongono un set è fondamentale. La perfezione assoluta non esiste, ma può essere molto vicina se si dispongono i mezzi adeguati.
Le barrette montate precisamente su un corpo fresa e devono avere tutte i profili previsti dal progetto dell’utensile, solo così si evitano errori sugli ingranaggi dentati e un decadimento del rendimento delle barrette stesse.
«miniToolsCoating dispone di affilatrici Klingelnberg mod. B27 che, attualmente, sono tra le più avanzate nel mondo», dichiara Giovanni Chinaglia. «Il potente controllo numerico Fanuc Series 31i mod.A5 è in grado di gestire 9 assi con precisione quasi assoluta», prosegue Chinaglia.
Il caricatore automatico è integrato nella macchina ed è composto da un magazzino di 24 cassette che possono contenere al massimo 18 barrette cadauna, per un totale di 432 barrette. Ogni cassetta può essere caricata con una diversa tipologia di barretta e quindi il controllo numerico cambierà automaticamente il programma di affilatura in accordo con il tipo di barretta presente in ogni singola cassetta.
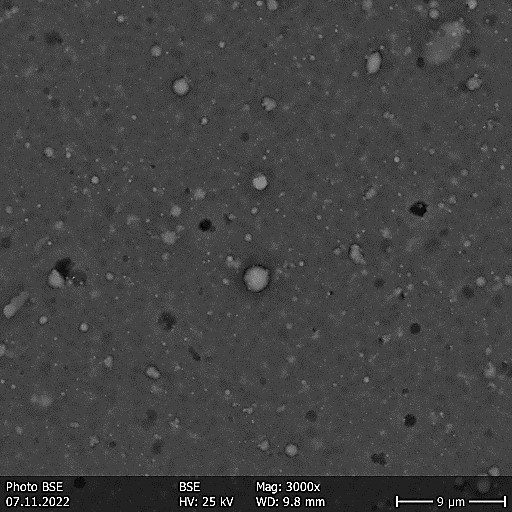
La macchina monta una mola diamantata elettro-deposta di 400 mm di diametro (brevettata) e specifica per questa macchina e per questo tipo di lavorazione.
Dopo ogni pezzo eseguito, un sensore controlla l’usura della mola e, se è il caso, il controllo numerico modifica la sua posizione per mantenere costanti i parametri di affilatura previsti dal programma.
Per limitare la possibilità di errori, la sgrossatura viene eseguita con una parte della mola, mentre per la finitura viene impegnata una superficie diversa. In questo modo si limita l’usura della parte di mola che stabilisce la precisione di affilatura e inoltre si possono ottenere superfici con rugosità inferiore a Ra = 0,1 µm. La macchina è abbinata all’apparecchio di controllo Klingelnberg BC12.
I dati del profilo controllato vengono confrontati con quelli teorici e, in caso di scostamento, il controllo numerico esegue automaticamente le opportune correzioni. In pratica il sistema funziona con il metodo Closed Loop garantendo una assoluta precisione su tutte le barrette affilate in modo automatico senza intervento dell’operatore. Lo scostamento dalle quote teoriche sul totale delle barrette caricate in macchine è dell’ordine del micrometro.
Le moderne tecnologie di taglio a secco con barrette in metallo duro prevedono una precisione esasperata nel montaggio delle lame nel disco, e questa operazione è possibile solo impiegando barrette realizzate con tolleranze geometriche e dimensionali strettissime, sia per quanto riguarda la realizzazione del corpo lama che dei profili attivi.
L’esatto profilo da eseguire sulle barrette viene definito dal team di progettazione della coppia conica, e definisce un set di parametri che definiscono il percorso utensili, questi set di dati vengono generalmente chiamati “summary” o “neutral data”, ma è possibile anche ricavare questi dati partendo da un profilo esistente già realizzato su barrette chiamate “master”.
Un buon rivestimento è essenziale
La necessità di eseguire il rivestimento dopo l’affilatura comporta complicate movimentazioni degli utensili da e verso i centri di rivestimento.
L’azienda miniToolsCoating è fortemente specializzata nei ricoprimenti e ha investito moltissimo in impianti, attrezzature e personale altamente specializzati ed oggi è in grado di soddisfare le varie esigenze dei clienti garantendo le massime performances degli utensili ricoperti.
La tecnica del coating è in continua evoluzione e al giorno d’oggi si eseguono ricoprimenti di vario tipo che differiscono dalla composizione del layer, dallo spessore e dai dati tecnici usati per la realizzazione.
Bisogna considerare che oggi si ricoprono utensili da taglio di vario tipo: stampi per la lavorazione di lamiere e plastica, parti varie soggette ad usura; ogni tipologia di prodotto richiede dei particolari requisiti del ricoprimento.
Il rivestimento, per essere eseguito correttamente, deve essere preceduto da una attenta preparazione perché il particolare da ricoprire deve essere perfettamente pulito, esente da bavature, senza tracce di ossidi sulle superfici. Sono necessarie quindi delle stazioni per il lavaggio con liquidi particolari che, tra l’altro, devono essere poco inquinanti.
Per accertarsi che il ricoprimento sia stato eseguito correttamente e non presenti imperfezioni, che ne compromettano il rendimento, sono necessari speciali strumenti di controllo.
Alta tecnologia in continuo sviluppo
In qualsiasi settore si operi, per accertarsi che un prodotto sia bene eseguito sono necessari dei controlli della qualità. Questo è tanto più vero se si tratta di utensili che a volte vengono impiegati con condizioni di lavoro esasperate.
«miniToolsCoating ha investito molto per dotarsi si apparecchiature di misura e controllo molto sofisticate, avviando anche nel 2022 l’attività di R&D», sottolinea Chinaglia che aggiunge: «L’ultimo investimento riguarda un potente microscopio elettronico (SEM) che è in grado di eseguire una serie di analisi che facilitano il percorso verso la perfezione».
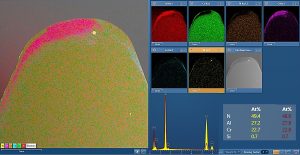
Basti pensare che questo strumento è capace di effettuare oltre 170.000 ingrandimenti, cioè si possono distinguere oggetti fino a 0,003 micrometri.
Con i diversi sensori di cui l’apparecchio è dotato, è possibile entrare ed esaminare la struttura degli oggetti in esame. Il microscopio ha tre sensori:
- Il primo è chiamato ad elettroni secondari SE, serve per vedere la morfologia del campione, i vantaggi risiedono nel fatto di poter vedere l’oggetto di interesse sempre a fuoco e si possono rilevare rugosità di 0,050±0.025 µm in funzione delle dimensioni del campione esaminato.
- Il secondo sensore è detto degli elettroni backscatterati BSE, permette di vedere gli elettroni che rimbalzano indietro e capire se un elemento è più o meno grande in base alla sua luminosità (maggiore è la luminosità più pesante è la specie chimica osservata). In questo modo si può capire se i vari elementi esaminati in superfice sono uguali o con composizione chimica diversa molto velocemente.
Per i rivestimenti è possibile analizzare se i difetti presenti sulla superficie sono buchi (mancanza di ricoprimento), droplet metalliche (macro-difetti non ben legati) e droplet ceramiche (macro difetti integrati nel ricoprimento).
Combinando i sensori si possono far risaltare i bordi di un grano del materiale, cioè fare quello che normalmente si fa in metallografia, ma senza agenti chimici di supporto.
3. La terza sonda è chiamata EDS (Energy Dispersive X-ray Spectroscopy).
Il microscopio vede il campione tramite un fascio di elettroni, il campione osservato a causa di questa radiazione genera raggi X. Ogni elemento chimico ha raggi X caratteristici che questa sonda capta individuando la composizione chimica del l’oggetto osservato.
Il SEM è particolarmente utile per analizzare le caratteristiche del metallo duro di cui sono fatte le barrette, dimensione della grana e esatta composizione chimica.
Se si attivano tutti e tre i sensori e si regolano opportunamente i fasci si può penetrare nel campione e fare mappe lungo lo spessore del pezzo. Con questo metodo, per esempio, si può determinare lo spessore di un ricoprimento, o identificarne la struttura a nanolayer, determinando la composizione chimica di ciascuno strato.
Si possono fare analisi della morfologia superficiale a livello nanometrico, dettagliando i vari tipi di difetti che si generano nella realizzazione dei rivestimenti PVD.
«Sono tanti i progressi raggiunti nelle tecnologie di produzione e di controllo e tanto ancora ancora c’è da sviluppare» precisa il manager. Le aziende che intendono mantenere posizione di preminenza sul mercato mondiale devono necessariamente adeguare i loro mezzi, con investimenti a volte molto importanti. Inoltre, queste attrezzature così sofisticate debbano essere gestite e utilizzate solo da personale altamente specializzato. «La perfezione assoluta non è teoricamente raggiungibile, ma si avvicina sempre più», conclude Giovanni Chinaglia.