Una panoramica sulle diverse modalità di danneggiamento e guasto degli ingranaggi consente una migliore comprensione delle cause, degli effetti e delle azioni correttive da intraprendere
Le ruote dentate sono componenti strutturali essenziali per il movimento e la trasmissione di potenza nei sistemi meccanici. In base alla potenza richiesta, le ruote dentate possono assumere configurazioni differenti, a seconda che si desideri, ad esempio, moltiplicare o ridurre di velocità e le sue caratteristiche specifiche (coppia, numero di giri, etc.). Inoltre, in base ai requisiti di potenza dell’applicazione, le proprietà meccaniche delle ruote dentate sono calcolate in modo tale da garantire una resistenza sufficiente per lo svolgimento delle proprie funzioni e, al contempo, ridurre al minimo il peso ed i costi di produzione. Le ruote dentate sono progettate per resistere ai carichi di esercizio; tuttavia, diverse possono essere le modalità di guasto che le coinvolgono e che possono avere conseguenze per l’intero sistema.
Come noto, i tempi di inattività non programmati devono essere ridotti al minimo così come le conseguenti perdite di produzione. Tuttavia, è frequente constatare che anche una progettazione attenta, associata alle migliori tecniche di produzione e alle corrette modalità di installazione non sono sempre sufficienti a garantire una lunga vita del componente e delle macchine. Almeno se non vengono attuate contestualmente ben precise operazioni, considerabili come una sorta di “best practices”, sia nelle fasi operative sia in quelle di manutenzione durante l’intero ciclo di vita.
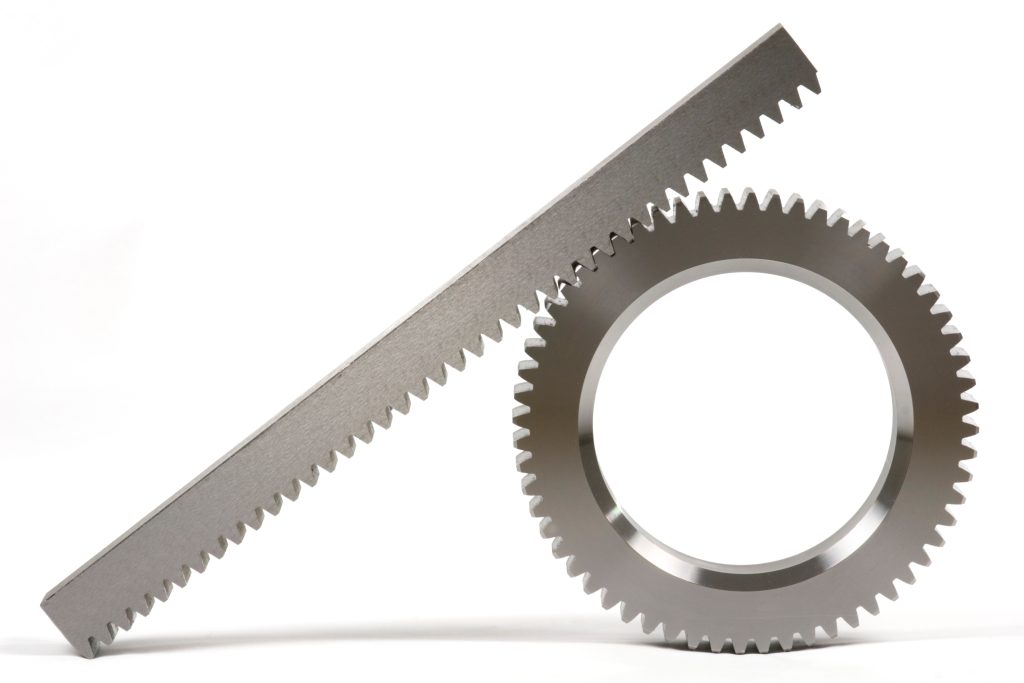
Analogamente ad altri componenti meccanici, le ruote dentate devono essere correttamente manutenute affinché possano funzionare in modo efficiente. Ciò significa eseguire regolari controlli e assicurarsi che eventuali problemi, più o meno rilevanti, vengano rilevati rapidamente e gestiti in modo efficace. Mentre i materiali di consumo, come i ricoprimenti superficiali, possono essere ripristinati più o meno frequentemente, le parti strutturali devono invece possedere durate più elevate. Questo è possibile grazie a strategie mirate di installazione, funzionamento e manutenzione, garantendo il raggiungimento dei sopracitati obiettivi di produzione. In questo contesto, sviluppare consolidati processi di manutenzione preventiva e piani di ispezione periodica per scongiurare guasti alle ruote dentate e ad altri elementi macchina è essenziale. A tal fine, una panoramica sulle diverse modalità di guasto consente una migliore comprensione delle cause e degli effetti, fornendo modalità e azioni correttive da intraprendere nel caso in cui tali problemi vengano rilevati in ritardo o a scopo preventivo.
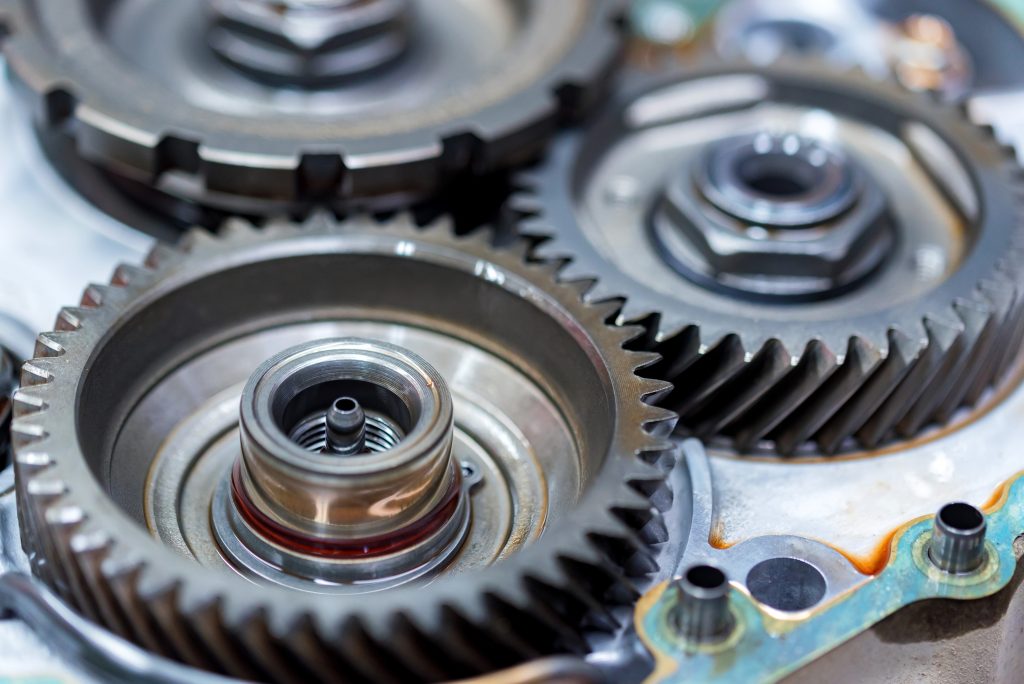
Le ruote dentate sono uno dei metodi maggiormente utilizzati per la trasmissione di potenza meccanica nelle macchine. Esse presentano vantaggi e caratteristiche peculiari rispetto alle altre soluzioni per la trasmissione di potenza, quali:
- offrono la possibilità di trasmettere elevati valori di coppia;
- possono essere utilizzate in applicazioni che richiedono basse velocità di funzionamento;
- possono essere impiegate fra alberi con piccolo interasse;
- garantiscono efficienza elevata, significativamente maggiore rispetto agli altri sistemi di trasmissione;
- la loro compattezza nella costruzione ne favorisce l’applicazione anche in piccoli alloggiamenti, garantendo l’assolvimento delle proprie funzioni e buoni risultati in termini di performance.
Tuttavia, le ruote dentate presentano anche alcune criticità, legate, ad esempio, agli elevati costi del processo di produzione, significativamente superiori rispetto alle altre modalità di trasmissione di potenza. Inoltre, si caratterizzano per scarsa flessibilità, per il rumore e le vibrazioni generati a velocità elevate, necessitano di lubrificazione e si dimostrano inadeguate in applicazioni in cui sono previsti alberi distanti tra loro.
A seconda delle esigenze e dell’applicazione prevista, esistono diverse tipologie di ruote dentate. Alcune di esse sono le seguenti: ingranaggi cilindrici (figura 1), ingranaggi elicoidali (figura 3), ingranaggi a spina di pesce, ingranaggi conici, pignone e cremagliera (figura 2) e ingranaggi cilindrici interni.
Principali fenomeni di danneggiamento di ruote dentate
I fenomeni di danneggiamento di ruote dentate si possono manifestare secondo modalità differenti. Come noto, sul mercato sono disponibili diverse tipologie di ruote dentate, pertanto, uno stesso guasto può variare ed avere un impatto diverso a seconda della tipologia selezionata per una specifica applicazione. Ruote dentate in metallo si guastano per numerose ragioni, alcune, in parte, indipendenti dagli ingranaggi stessi. In certi casi, il fenomeno di danneggiamento è associato ad un non corretto dimensionamento, conseguenza, ad esempio di un’errata progettazione geometrica, o di profili, strisciamenti e tolleranze non ottimizzate; in altri, dipende da come le ruote dentate vengono assemblate o installate; in altri, ancora, è dovuto alle condizioni di esercizio (calore, velocità di rotazione, cicli di funzionamento, etc.). I fenomeni di danneggiamento sono correlati, soprattutto, ad erronea, carente o inesistente manutenzione, e, nei casi più comuni, sono provocati da errori di lubrificazione. La valutazione del danneggiamento delle ruote dentate può essere una sfida, soprattutto nelle moderne apparecchiature industriali. A differenza dei test di laboratorio, progettati per isolare una particolare modalità di guasto, i malfunzionamenti sul campo possono combinare fra loro diverse modalità. Raramente gli ingegneri dispongono di tutti i dati necessari per una diagnosi completa. Inoltre, i danni che si verificano a seguito di un primo guasto possono alterare l’aspetto finale delle ruote dentate danneggiate, complicando ulteriormente la diagnosi.
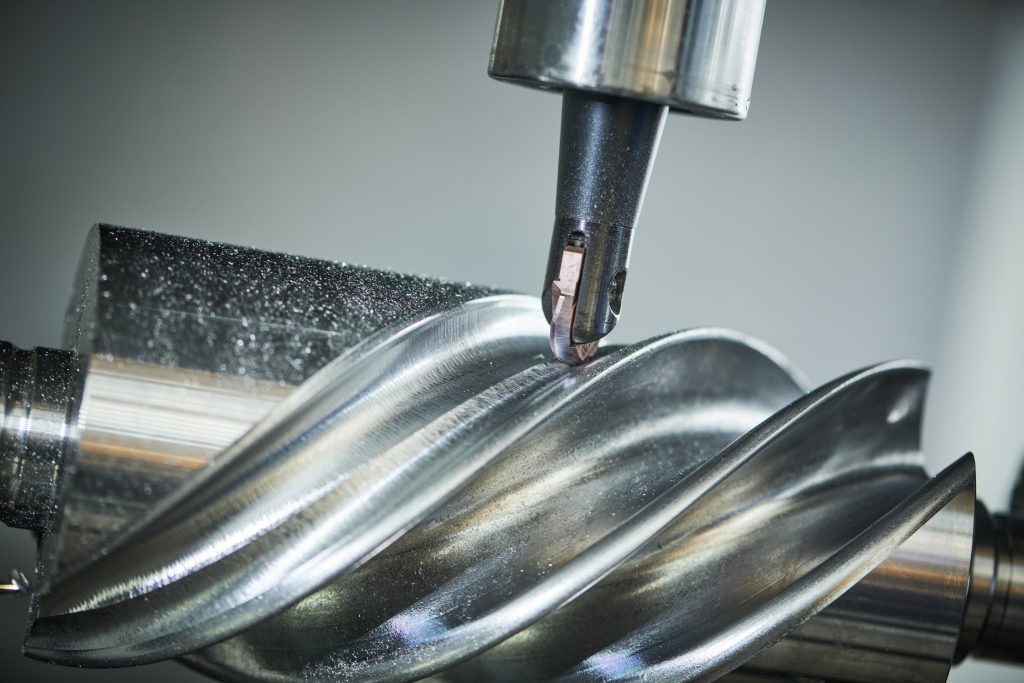
Spesso si tende a pensare che a provocare il guasto di un ingranaggio sia in prevalenza il materiale impiegato per la sua realizzazione. In effetti, alcuni microdifetti dell’acciaio o di altri materiali possono essere responsabili dell’innesco di cricche di fatica, fenomeno ulteriormente accelerato dalle cattive condizioni di esercizio che possono causare corrosione, erosione o ammaccature. In generale comunque, come vedremo in seguito, sono anche altre le cause imputabili ai fenomeni di danneggiamento di ruote dentate.
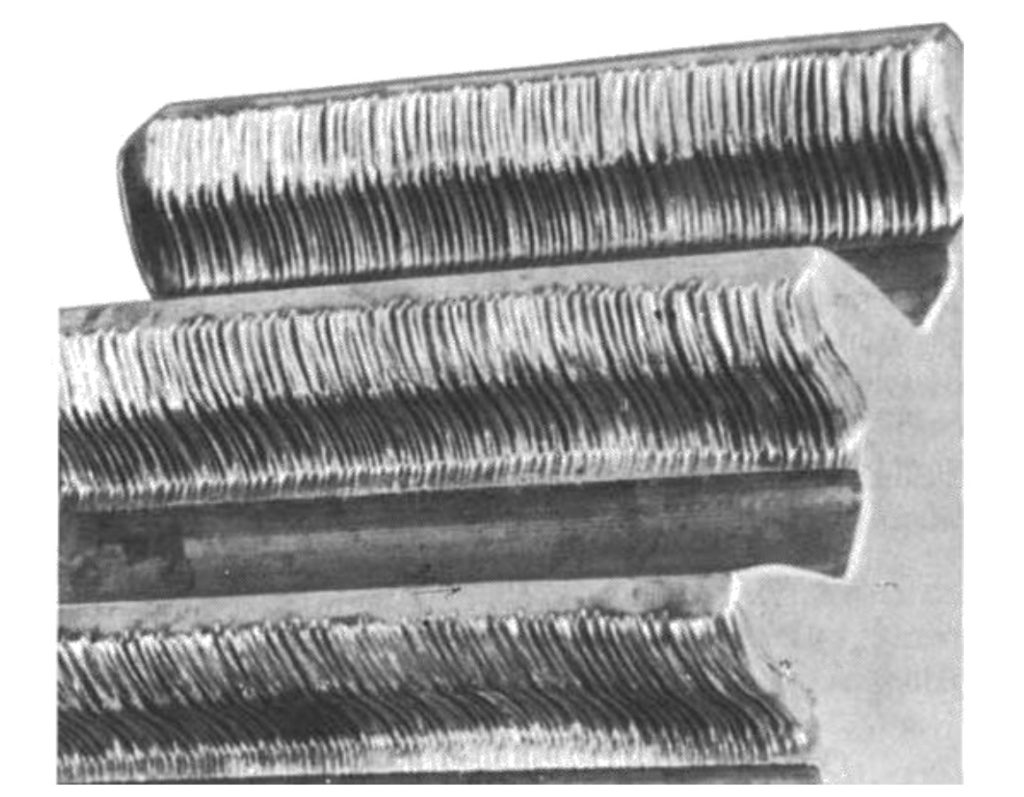
Nei moderni sistemi di trasmissione, le esigenze di riduzione del peso e contenimento dei costi, richiedono componenti alleggeriti e sempre più efficienti. Tuttavia, nel caso delle ruote dentate, design alleggeriti aumentano i rischi correlati al guasto. Basti pensare all’usura, tipicamente riscontrabile in veicoli ed altri mezzi di trasporto nonché nelle macchine utensili e altre apparecchiature industriali, fenomeno che si verifica anche in caso di regolare manutenzione. In particolare, le ruote dentate nei sistemi di trasmissione sono soggette a forti urti durante le variazioni di coppia, il che causa usura, calore e rumorosità elevati.
I fenomeni di danneggiamento che coinvolgono le ruote dentate possono essere classificati in diverse categorie e sottocategorie. Lo standard ANSI/AGMA 1010-F14 delinea sette classi e modalità di cedimento, riassunte in tabella 1.
CLASS | GENERAL MODE |
Wear | Adhesion Abrasion Polishing Corrosion Fretting Scaling White layer flaking Cavitation Erosion Electrical discharge |
Scuffing | Scuffing |
Plastic deformation | Plastic deformation |
Hertzian fatigue | Macropitting Micropitting Subsurface initiated failures Subcase fatigue |
Cracking | Hardening cracks Grinding damage Rim and web cracks Case/core separation Fatigue cracks |
Fracture | Brittle fracture Ductile fracture Mixed mode fracture Tooth shear Fracture after plastic deformation |
Bending fatigue | Low-cycle fatigue High-cycle fatigue |
Si parla di usura (figura 6) principalmente quando si ha una perdita di materiale dalle superfici, generalmente dei denti, con conseguente variazione del loro profilo. Ciò può verificarsi per vari motivi di natura meccanica, chimica o elettrica, come, ad esempio, il contatto tra due parti metalliche provocato da uno strato di lubrificante inadeguato. Oppure può verificarsi per dispersione di particelle abrasive all’interno del lubrificante, per rottura del film di lubrificante in prossimità della zona di contatto e infine per usura chimica dovuta a una errata composizione del lubrificante e dei suoi additivi, incompatibili con i materiali impiegati per la costruzione delle ruote dentate.
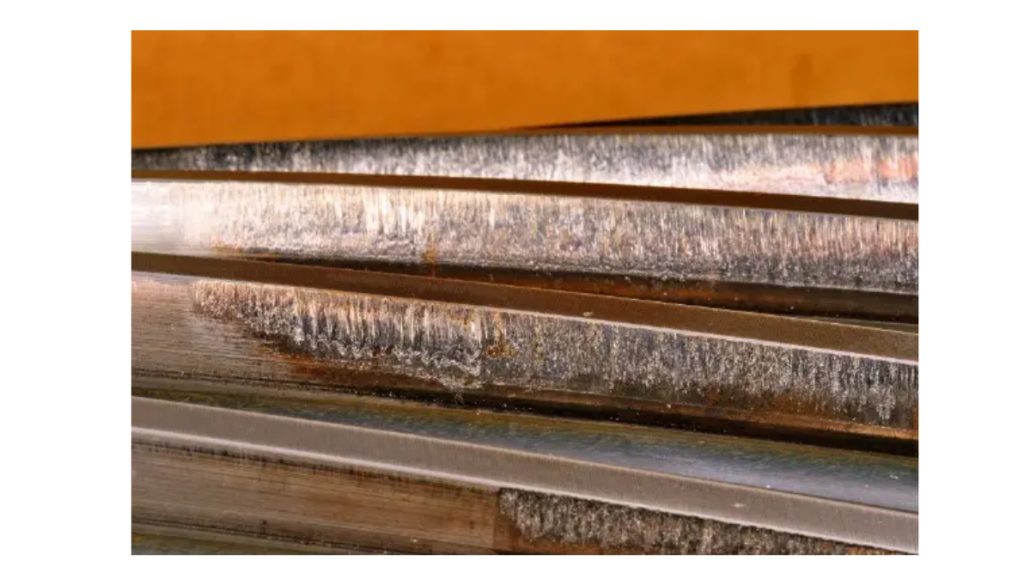
Possono verificarsi fenomeni di usura tipici che causano il trasferimento di metallo da una superficie del dente all’altra a causa di saldature e micro-abrasioni. Il danno si verifica tipicamente nell’addendum, nel dedendum o in entrambi, lontano dalla linea del diametro primitivo, in bande strette o larghe, orientate nella direzione di scorrimento. Le tracce possono presentarsi in chiazze localizzate, se dovute a concentrazioni di carico.
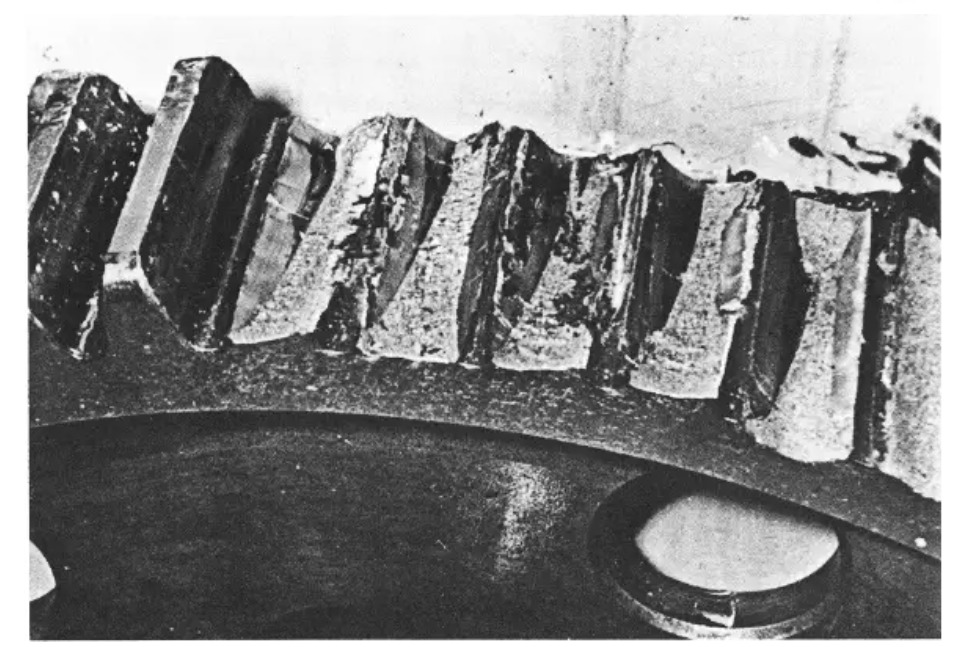
Le aree scalfite sembrano avere una consistenza ruvida o opaca. Quando il dente di un ingranaggio viene sovraccaricato, a causa di una progettazione inadeguata o di un carico locale troppo elevato, può cedere deformandosi plasticamente o fratturandosi. La deformazione plastica (figura 8) è una deformazione permanente che si verifica in caso di carico eccessivo in corrispondenza di sollecitazioni eccessive, come nel caso di urti, tali da superare il limite di snervamento del materiale. Il fenomeno può verificarsi sulla superficie o appena al di sotto di questa in corrispondenza dei denti, in seguito a pressioni hertziane elevate, oppure alla radice dei denti, a causa di elevate sollecitazioni di flessione.
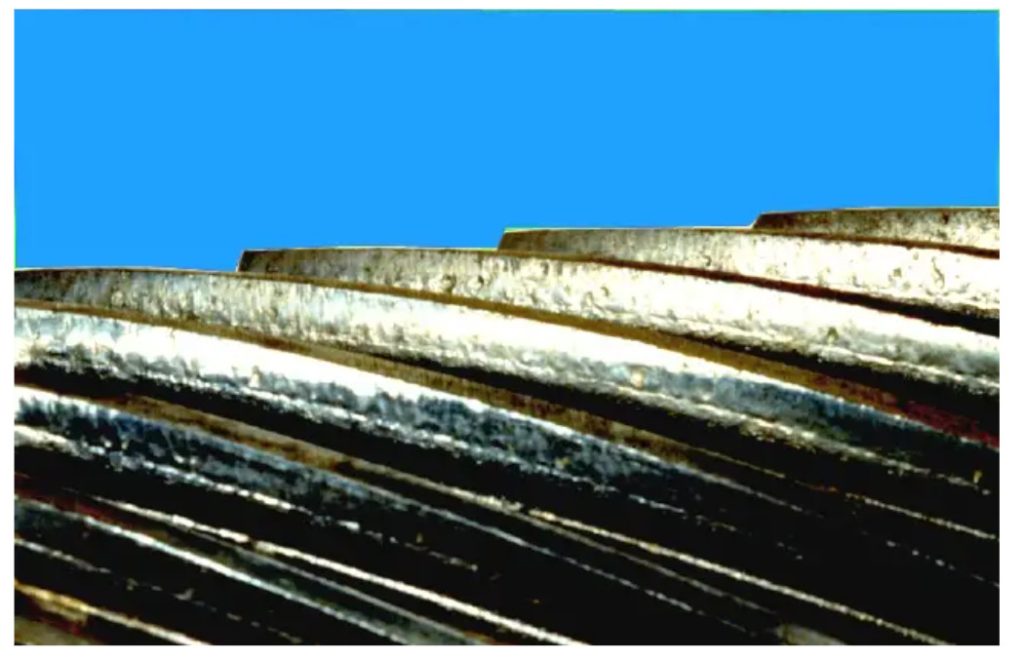
La deformazione plastica si verifica solitamente nel caso in cui il materiale di cui la ruota dentata è costituita è particolarmente morbido. Tuttavia, non è esclusa la possibilità che il fenomeno si manifesti anche con materiali più duri come l’acciaio temprato. La fatica associata al fenomeno del pitting, consiste invece in un cedimento del materiale della ruota dentata per carico ciclico. Può capitare che, durante cicli di carico ripetuti, in caso di carichi eccessivi si separino dalla superficie della ruota dentata alcuni frammenti di materiale, i quali producono vaiolature o cavità sulle superfici stesse. La fatica è un cedimento progressivo che consiste in tre stadi distinti:
- stadio 1, innesco della cricca (la deformazione plastica si verifica in corrispondenza di concentrazioni di sollecitazioni che portano alla formazione di cricche microscopiche);
- stadio 2, propagazione della cricca (le cricche crescono perpendicolarmente alla massima sollecitazione di trazione);
- stadio 3, frattura (la cricca cresce, raggiungendo una dimensione considerevole, tale da provocare una rottura improvvisa).
In generale, la maggior parte della vita a fatica è caratterizzata dagli stadi 1 e 2, fino al momento in cui le cricche non raggiungono dimensioni critiche per cui si verifica una rottura improvvisa (stadio 3). Le rotture sono classificate come fragili, duttili o miste in relazione alle loro caratteristiche macroscopiche e microscopiche (durezza del materiale ed entità della sollecitazione applicata). Si tratta di una frattura duttile se preceduta da un’apprezzabile deformazione plastica; si parla invece di una frattura fragile in corrispondenza di scarsa deformazione plastica antecedente e di una frattura mista quando presenta caratteristiche sia duttili che fragili. I guasti per fatica di solito culminano in una rottura quando le cricche di fatica crescono fino a raggiungere dimensioni tali per cui la sezione del dente rimanente non è più in grado di sostenere il carico. In questo senso, il materiale rimanente è sovraccaricato; tuttavia, la rottura è una modalità di guasto secondaria causata dalla propagazione dei difetti superficiali per fatica. Le rotture dei denti delle ruote senza precedenti criccature per fatica sono infrequenti, tuttavia possono derivare da carichi d’urto. Questi ultimi possono essere generati dalla sorgente di coppia motrice e possono anche verificarsi in corrispondenza di corpi estranei, o quando i denti delle ruote dentate risultano improvvisamente disallineati e si incastrano tra loro oppure a seguito della rottura di un cuscinetto o di un albero.
Esistono diverse variabili geometriche che possono essere ottimizzate per ridurre le sollecitazioni di flessione e aumentare la durata della flessione a fatica. Le ripetute sollecitazioni hertziane possono causare cricche da fatica superficiali e il distacco di frammenti di materiale dalla superficie del dente dell’ingranaggio. Oltre alle cricche alla radice del dente, causate da fatica per flessione, possono inoltre verificarsi cricche in altri punti della ruota dentata, provocate da sollecitazioni meccaniche, termiche, difetti del materiale o conseguenti ad una lavorazione non corretta.
Condition monitoring e manutenzione di ruote dentate
La resistenza, la tenacità e l’economicità dell’acciaio lo rendono il materiale più utilizzato nella produzione di ruote dentate. Abbiamo visto come, oltre ai fattori metallurgici, le prestazioni delle ruote dentate dipendono anche da altri elementi quali: lubrificazione, contaminazione del sistema, design della ruota dentata, disallineamento, finitura superficiale, danni provocati da lavorazioni, processi produttivi, carichi severi ed urti. Considerando i numerosi punti di attenzione nella selezione del materiale, nella progettazione, nella produzione e nell’affidabilità e durata delle ruote dentate, saper valutare correttamente un guasto diviene indispensabile non solo per individuare la causa principale del problema ma soprattutto per mettere in atto immediatamente azioni correttive per favorire una diagnostica precoce al fine di prolungare la vita utile delle ruote dentate stesse. Esistono tecniche diagnostiche come l’imaging termico, l’analisi dell’olio, l’analisi dei metalli usurati e l’analisi delle vibrazioni che consentono di rilevare precocemente le variazioni di processo, favorendo una tempestiva analisi e risoluzione dei problemi. Tuttavia, spesso quando un componente come una ruota dentata si guasta, un’analisi specifica a livello di sistema risulta la prassi consigliata per disporre di un quadro più completo.
Per iniziare è importante comprendere la struttura e il funzionamento della ruota dentata. Segue una fase critica: la raccolta di informazioni sulla lavorazione e sulla vita utile del componente. Le informazioni sul carico, sulla temperatura, sulle ore di funzionamento, sullo storico della manutenzione, sulla durata utile prevista e sul tipo di lubrificazione, nonché sul design, sulle specifiche, etc sono dati assai preziosi. È importante comprendere le specifiche della ruota dentata oggetto di analisi e se il componente è conforme ad esse. Inoltre fondamentale capire se, a loro volta, le specifiche soddisfano adeguatamente le esigenze dell’ingranaggio.
La fase immediatamente successiva consiste nell’ispezione: si parte da un esame visivo delle condizioni esterne del componente per poi procedere allo smontaggio e all’ispezione di tutte le parti interne, sia esse siano o meno danneggiate. Tutte le condizioni rilevate devono essere registrate e messe per iscritto con documentazione accurata a corredo. Il grado di danneggiamento determina le tempistiche e le modalità di analisi.
L’ispezione visiva può essere coadiuvata da test non distruttivi, come l’ispezione delle particelle magnetiche o l’ispezione con colorante penetrante al fine di verificare la presenza di cricche. Dopo l’esame visivo, si passa all’ispezione a più alto ingrandimento del campione, eventualmente con microscopia elettronica a scansione (SEM). L’ampia profondità di campo e l’elevata risoluzione dell’analisi SEM permette di identificare con precisione le modalità di rottura e di individuare il punto di innesco. Si tratta di elementi fondamentali per capire il motivo per cui il componente si è guastato. L’analisi SEM dotata di spettroscopia a dispersione di energia (EDS) consente l’analisi della composizione del componente danneggiato e può essere utilizzata per verificare la presenza di materiale non metallico nei siti di innesco. La microscopia ottica è impiegata per analizzare le asperità superficiali (come cricche, ossidazioni inter-granulari o inclusioni) e per osservare la microstruttura del componente. Un’analisi aggiuntiva dovrebbe includere test per altre proprietà specifiche come l’analisi chimica, la durezza, la profondità del caso, la profondità del prodotto di ossidazione inter-granulare, la pulizia dell’acciaio o la tensione residua. La pulizia dei componenti, ad esempio, consente di identificare segni di corrosione, contaminazioni e fenomeni da surriscaldamento. Anche l’ispezione dei cuscinetti e le modalità di contatto tra i denti dell’ingranaggio in condizioni di carico e scarico contribuiscono a fornire preziosi indizi sulle cause dei guasti alle ruote dentate.
Infine, test non distruttivi (prima) e distruttivi (poi) e calcoli di progettazione sulla base della geometria dell’ingranaggio, aiutano a formulare ipotesi circa le possibili cause del guasto. Se tali ipotesi vengono confermate, si potrà poi formalizzare tutti i dettagli in un report, che non solo suggerirà le possibili modalità di intervento, ma fornirà altresì utili raccomandazioni circa azioni preventive o correttive da intraprendere.
Conclusioni e scenari futuri
Oggi il mercato offre diverse tipologie di ingranaggi a seconda dell’applicazione prevista. Tuttavia, come noto, le ruote dentate nel corso della loro vita utile possono andare incontro ad una serie di fenomeni di danneggiamento per svariati motivi. I guasti alle ruote dentate possono, nei casi più gravi, provocare seri problemi anche ad altri componenti o apparecchiature, con conseguente compromissione della sicurezza e dell’affidabilità dell’intero sistema, oltre al ben noto impatto economico legato ai costi di fermo macchina non pianificati. Fortunatamente le moderne tecnologie rendono possibile la prevenzione di tali fenomeni. A tal fine, si rende necessario un monitoraggio in tempo reale delle condizioni di salute della macchina o dell’apparecchiatura, in un’ottica di approccio sistemico, che, unitamente a interventi di manutenzione e ispezione programmati si dimostrano, in questo contesto, “best practice” essenziali.
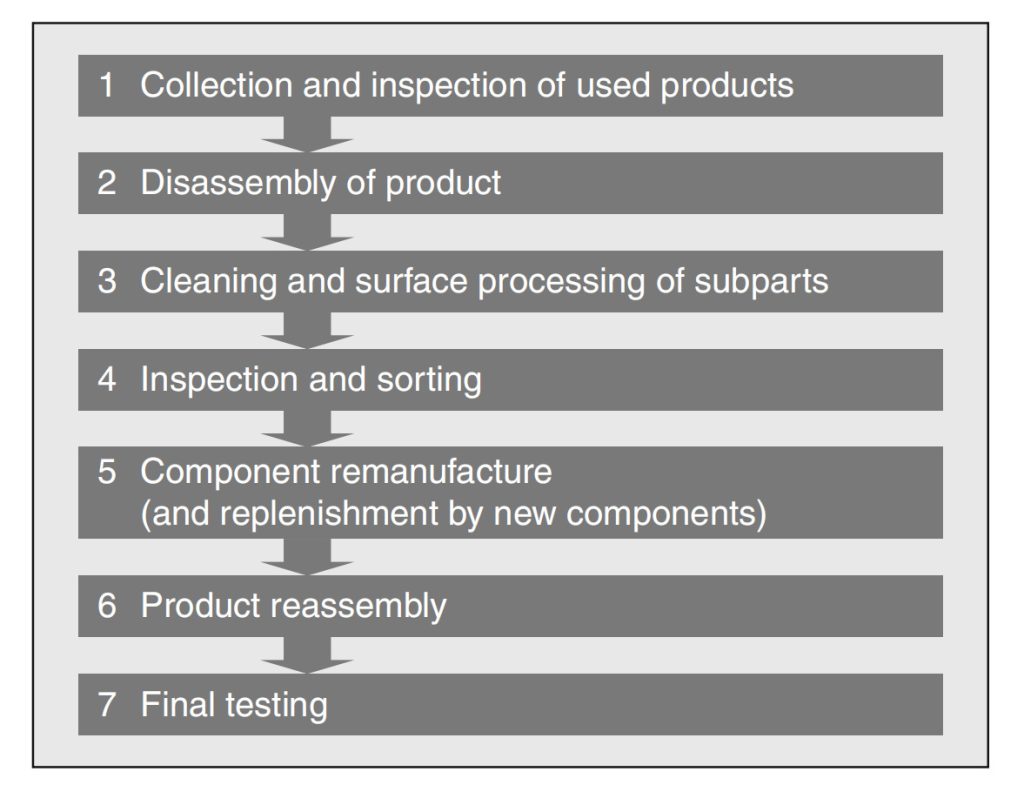
Oggi, una soluzione per realizzare prodotti di elevata qualità tecnica, garantendo al contempo, la salvaguardia dell’ambiente, è rappresentata dal re-manufacturing di componenti danneggiati. La rigenerazione è un processo che porta i componenti usati ad uno stato funzionale “pari al nuovo” con garanzia di affidabilità, qualità e ottimizzazione delle performance. Questa pratica è particolarmente adatta a prodotti meccanici complessi, come le ruote dentate. In figura 9 sono elencati i sette step per un processo di rigenerazione ottimale.

Oggi il progresso tecnologico insieme alla manifattura additiva (AM) è considerato una valida soluzione per la riparazione e il ripristino di componenti danneggiati. Si prevede che l’AM sarà la tecnologia che consentirà di sostituire la riparazione manuale con nuclei rigenerabili. I progressi nell’applicazione delle tecnologie AM sono illustrati in figura 10.
Tecnologie additive al servizio dei processi di re-manufacturing suscitano forte interesse in vari settori ed applicazioni industriali. Tuttavia, esistono numerosi problemi e sfide per una rigenerazione efficace: dalla progettazione dei componenti ai sistemi di processo. Focalizzarsi esclusivamente su elementi quali la selezione dei materiali, la compatibilità degli stessi, la configurazione della macchina, la complessità geometrica, i requisiti di pre-elaborazione e la tolleranza geometrica potrebbe non bastare. Obiettivo della ricerca è concentrarsi sul modo in cui i prodotti dovrebbero essere progettati per un’efficace riparazione e restauro al fine di estendere il ciclo di vita del componente in un’ottica di economia circolare.
(Giorgio De Pasquale, Dipartimento di Ingegneria Meccanica e Aerospaziale, Politecnico di Torino, Smart Structures and Systems Lab, Elena Perotti, Senior data analyst)