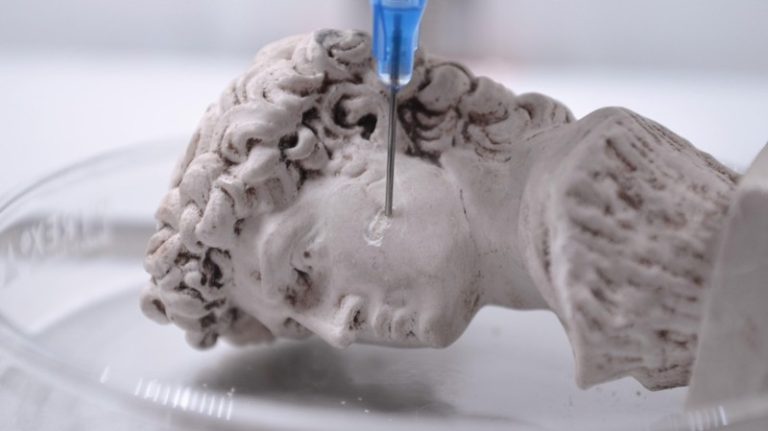
Le tecnologie di fabbricazione additiva stanno man mano uscendo dall’ambito della prototipazione. Ma potrà essere possibile un loro impiego per la produzione di massa? Quali sono i limiti che ancora oggi legano la diffusione e l’impiego di queste tecnologie? E quali sono invece le opportunità che possono aprire?
Condividi
Le richieste sempre più complesse da parte dei progettisti hanno spinto i tecnologi ad approcciarsi sempre più alla rivoluzione dell’additive manufacturing. Quest’ultima si distingue dalle tradizionali tecnologie di lavorazione perché non asporta materiale dal grezzo ma ottiene particolari tridimensionali molto complessi attraverso il deposito progressivo di strati di materiale.
I processi di additive manufacturing mirano tutti a generare un solido, per questo motivo si parte sempre da un disegno CAD 3D che viene convertito nel formato necessario a renderlo fruibile per la lavorazione. Una volta importato il solido nel software della macchina si procede generalmente ad con il dividere il modello in una successione di strati di piccolo spessore che verranno realizzati in varie “passate” dalla macchina; in contemporanea vengono aggiunti al modello 3D eventuali supporti, da creare mediante la tecnologia stessa, oppure costruiti in precedenza, che permettono al particolare di non collassare su sé stesso durante la produzione. Infine, successivamente alla produzione, i particolari ricavati possono essere se necessario sottoposti a trattamenti di post-produzione, tra i quali troviamo trattamenti chimici e termici ma anche lavorazioni di finitura alle macchine utensili.
Il nome di questa tipologia di lavorazione deriva dal nome depositato dai suoi inventori, i ricercatori del M.I.T. di Boston, 3D print, stampa 3D per l’appunto. Oggigiorno tuttavia si tende ad associare il termine stampa 3D a tutti i processi di Additive Manufacturing sui polimeri, soprattutto quelli FDM che troviamo nelle macchine a basso costo sempre più diffuse.
Questa tecnologia lavora mediante l’utilizzo di speciali agenti solidificanti viene per questo chiamata Inkjet Printing per la similitudine con l’inchiostro delle comuni stampanti. Nel dettaglio questa tecnologia prevede di solidificare selettivamente successivi strati di polvere mediante l’apporto di agenti solidificanti. Le polveri sono costituite dal materiale strutturale e da un legante che può essere organico o inorganico. Questa tipologia di lavorazione permette di lavorare senza l’utilizzo del calore, richiede però un trattamento in forno per i particolari metallici per ridurre la percentuale di legante e ottenere così migliori proprietà strutturali. Bisogna però tener conto in fase di progettazione del ritiro dei particolari se sottoposti a questo trattamento in quanto molto accentuato. Si possono realizzare con un’alta produttività particolari in polimero, metallo ma anche in ceramica o vetro. I particolari, specie quelli in polimero, possono essere creati in un’ampia gamma di colori.
La tecnologia delle stampanti 3D diffuse ormai anche in molte case di hobbisti è la più semplice ed economica. Un filamento di polimero viene riscaldato e quindi estruso tramite un ugello, quest’ultimo ha la possibilità di muoversi nello spazio andando a generare la geometria del particolare che vogliamo ottenere. Presenta dei limiti nella precisione e finitura superficiale del manufatto in quanto il diametro dell’ugello non può essere ridotto di molto. La gamma di polimeri utilizzabili negli ultimi anni si è ampliata moltissimo e si iniziano a trovare sul mercato anche i primi polimeri tecnici oltre ai più conosciuti elastomeri. La possibilità di utilizzare materiali di colori differenti rendono questa tecnica adatta anche alla creazione di prototipi il più simili possibile al prodotto finale. Semplicità ed economicità (poche migliaia di euro, ma anche qualche centinaio in alcuni casi) di questa tecnologia hanno permesso la diffusione al grande pubblico delle tecnologie di additive manufacturing; tra i pregi di questa tecnologia troviamo infatti anche la possibilità di essere utilizzata in ambienti come uffici o case.
Questa tipologia di lavorazione si basa sulle proprietà fotosensibili di alcuni polimeri o cere speciali. Microsfere di polimero vengono depositate per strati sino a formare il modello da realizzare mentre una luce UV solidifica il deposito. Uno dei vantaggi di questa tipologia di lavorazione è la possibilità di creare particolari di più materiali, si possono così generare direttamente in materiale differente supporti alla stampa. Questa tecnologia permette di avere prototipi multicolore in diversi materiali e con una finitura superficiale di alto livello. I manufatti però sono molto delicati, di conseguenza non adatti a diventare parti strutturali.
Diversi fogli di materiale vengono impilati e laminati assieme per formare l’oggetto desiderato. La laminazione dei fogli, tagliati con una lama o mediante laser, può avvenire chimicamente, tramite adesivi, per saldatura ad ultrasuoni o brasatura (solo per i metalli). Le parti che vengono tagliate strato per strato vengono rimosse alla fine del processo. Questa tecnologia permette alta produttività a costi relativamente contenuti, permette inoltre di poter creare oggetti con delle componenti annegate nei fogli. Si possono ottenere oggetti lavorando fogli di carta, plastica e metalli.
Attualmente è la tecnologia più promettente per quanto riguarda l’additive manufacturing dei metalli in quanto permette di realizzare particolari strutturali dalle elevate prestazioni. Il processo è molto semplice, in quanto strati di polveri metalliche vengo successivamente solidificati mediante un raggio laser orientato da specchi mobili. La microfusione innescata dal laser restituisce un materiale molto uniforme ed è per questo motivo che le proprietà delle leghe lavorate in questo modo sono perfino superiori a quelle lavorate mediante tecnologie meccaniche. Si possono lavorare molte leghe metalliche dall’alluminio al titanio con geometrie complesse, le macchine lavorano però su superfici molto ridotte e con costi molto elevati. Questo genere di lavorazione inoltre non necessita di supporti in quanto è la polvere stessa degli strati precedenti a svolgere questa funzione.
Questa tipologia di lavorazione va ad apportare del materiale a solidi già esistenti, si possono quindi effettuare riparazioni o aggiunte di uno o più materiali differenti e si può affiancare a lavorazioni come il taglio laser o la fresatura. In questa tipologia di lavorazione un laser o una sorgente di elettroni aumenta la temperatura locale del punto sul quale bisogna lavorare generando un bagno fuso sul quale si andranno a fondere il filo o la polvere apportati dall’ugello di lavorazione. Si creano quindi dei cordoni di saldatura che andranno a formare la geometria desiderata sovrapponendosi fra loro. Il punto di lavorazione viene spesso inondato di gas inerte per evitare ossidazione o altre reazioni del materiale fuso localmente. Date le sue peculiarità questa tecnologia permette un rapido passaggio da un materiale all’altro (basta passare a una diversa polvere o filo) e un grande apporto di costruzione volumetrico se confrontato con le altre tecnologie additive. L’apporto di materiale dalle alte proprietà solo in punti strategici permette di risparmiare molto nella creazione di particolari molto prestanti per settori come quello navale, aereonautico e oil & gas.
Entrambe queste tecnologie si basano sulla solidificazione di strati successivi di polimero fotosensibile liquido, vengono infatti considerate entrambe appartenenti alla tecnologia VAT photopolymerization. La stereolitografia inizia la polimerizzazione del liquido mediante un laser, quindi la sua definizione è data dalla dimensione del punto laser stesso. La tecnologia Digital Light Processing invece inizia la polimerizzazione mediante un proiettore capace di proiettare nello spazio, di conseguenza la definizione deriverà dalla dimensione dei pixel proiettati. L’accuratezza ottenibile mediante queste tecnologie è davvero elevata e permette di ottenere superfici molto lisce e definite. Con entrambe è possibile realizzare anche particolari di grandi dimensioni con una relativa velocità.
Questa particolare tecnologia permette di ottenere manufatti additivi di ceramica, argilla e altri materiali fluido densi, un cilindro ad aria compressa infatti attraverso una vite senza fine permette di estrudere attraverso un ugello della ceramica andando a depositare i vari layer come nella tecnologia FFF. Ovviamente esistono grosse limitazioni sulle geometrie ottenibili date dai collassi che possono avvenire prima della completa essiccatura. Questo genere di lavorazione è per ora più sperimentale e artistica, infatti sono molti gli artisti che si dedicano a questo genere di “scultura”.
Le tecnologie di produzione additiva permettono l’utilizzo di molti materiali e i produttori spendono ingenti risorse per implementare l’utilizzo di materiali sempre più performanti. Anche i materiali più economici hanno visto negli anni incrementare rapidamente le loro prestazioni.
I materiali per l’additive manufacturing si possono suddividere in due principali famiglie: quella dei polimeri e quella dei metalli. I polimeri garantiscono costi inferiori sia per quanto riguarda l’acquisto del materiale stesso sia in termini di tecnologie di stampa, certamente però i metalli offrono prestazioni di livello più elevato.
Il PLA deriva dall’amido, per questo viene considerato eco-friendly, presenta una buona stabilità coniugata ad un ritiro ridotto e a buone caratteristiche meccaniche. Si stampa a temperature inferiori a quelle degli altri polimeri. Risulta quindi essere un materiale molto flessibile adatto a un innumerevole numero di applicazioni.
L’ABS è caratterizzato da un’alta resistenza meccanica e al graffio e una buona resistenza al calore, è inoltre molto rigido e può essere lucidato e verniciato facilmente. Durante la progettazione è necessario però tenere conto del suo elevato ritiro. Le sue proprietà meccaniche lo rendono adatto a quelle applicazioni dove il particolare è sottoposto a sforzi rilevanti.
L’HIPS è presente in due personalità molto differenti nel mondo della stampa 3D: la prima, quella per la quale è stato introdotto in questo mondo, è quella di materiale per supporti poiché solubile in D-Lemonene (un idrocarburo). La seconda invece è quella di un polimero dalle buone caratteristiche meccaniche, quasi come quelle del blasonato ABS ma stampabile con più facilità, a temperatura ridotta e a un costo inferiore, inoltre è opaco riducendo così la visibilità dei gradini tipici della produzione per strati.
Il Nylon presenta delle proprietà meccaniche molto interessanti, si salda bene su sé stesso rendendo meno visibili gli “strati “della produzione additiva sulla superficie e si può stampare senza necessità di un piano riscaldato. Il Nylon però necessita di alte temperature di stampaggio, superiori a 250°, ed è inoltre molto sensibile all’umidità e quindi va trattato con maggior attenzione rispetto agli altri polimeri.
Il PET non crea odore né fumi tossici quando viene stampato, assorbe pochissima acqua e presenta una buona trasparenza e lucidità; per queste proprietà è spesso usato per la creazione di giocattoli, parti per elettronica e cosmetica.
Il PC è molto trasparente, non è tossico ma soprattutto ha un’alta temperatura di deformazione, è quindi adatto alla creazione di tutti i manufatti stampati 3D, bisogna però considerare che ha un costo mediamente superiore rispetto agli altri polimeri.
Il Polietilene ad alta densità (HPDE) è uno dei materiali plastici più diffusi, può essere utilizzato per la produzione additiva senza particolari accorgimenti. Tra le sue proprietà principali: è atossico e ha un basso assorbimento d’acqua; per questo viene utilizzato in applicazioni alimentari. Tuttavia, la sua più interessante caratteristica è la grande resistenza agli agenti chimici, il che lo rende ideale in applicazioni per l’industria chimica ed elettrica.
Questo particolare polimero con un basso punto di fusione e quindi facilmente utilizzabile nella stampa, presenta una buona stabilità termica e buona biocompatibilità, caratteristica che lo rende comune nell’ambito biomedico.
Il PVA è un materiale idrosolubile ma altrettanto resistente agli idrocarburi. Per le sue proprietà nel mondo additivo è utilizzato per la creazione di supporti da eliminare mediante immersione in acqua. Il PVA è leggermente più complesso da estrudere rispetto ad altri polimeri, anche per via dell’alta temperatura di stampa; a causa delle sue proprietà va inoltre conservato in un luogo asciutto per evitarne il degrado.
L’alluminio è molto leggero e per questo adatto ad applicazioni che richiedono un buon compromesso fra capacità termiche e peso contenuto. Tipicamente infatti lo si utilizza nel settore automotive e nell’aereonautica.
Le superleghe Cobalto-Cromo offrono proprietà meccaniche e termiche elevatissime, le proprietà meccaniche addirittura migliorano col salire della temperatura fino a 500°-600°. Oltre a questo, offrono un’ottima resistenza alla corrosione, per questo motivo vengono utilizzate in applicazioni ingegneristiche ad alta temperatura, come i motori degli aerei e in ambito biomedico.
Le leghe di Nichel resistono a temperature elevatissime e presentano un’ottima resistenza meccanica e all’ossidazione, vengono spesso utilizzate a temperature fino a 1200°. Aereospaziale e energia sono i due settori dove vede più utilizzato, ad esempio nelle turbine.
Esistono numerose tipologie di acciai per additive manufacturing che ripropongono tutte le caratteriste che possiedono i normali acciai forgiati. Troviamo infatti ad esempio quelli temprabili o quelli inossidabili. Per il suo rapporto costo prestazioni è la lega più utilizzata, anche perché presenta una notevole flessibilità applicativa.
Il titanio è famoso per essere una lega dalla bassa densità con notevoli proprietà meccaniche e resistenza alla corrosione. Queste caratteristiche lo rendono adatto a molte applicazioni in ambito motorsport e aereospaziale, infine la purezza ottenibile in alcune polveri sommata alle sue proprietà lo rendono ideale per applicazioni biomediche. Il titanio infatti presenta una buonissima biocompatibilità.
Molte delle tecnologie additive presentano la necessità del crearsi dei supporti per prevenire il collasso della struttura durante la sua creazione. A valle della lavorazione questi supporti vanno eliminati. Si possono eliminare meccanicamente, spesso a mano, semplicemente staccando il manufatto dai supporti, oppure chimicamente, ad esempio immergendo il tutto in un liquido dove solo i supporti sono solubili ed estraendo il manufatto soltanto.
Spesso la superficie dei particolari generati con queste tecnologie non è perfettamente uniforme, per questo motivo la pallinatura è un trattamento al quale si ricorre spesso. Il manufatto viene colpito con delle sfere di vetro e sabbia scagliate mediante aria compressa, ottenendo quindi una superficie più uniforme eliminando eventuali residui di supporto e i caratteristi gradini derivanti da una lavorazione per strati.
In questa tipologia di trattamento i pezzi vengono inseriti in un sistema vibrante assieme a del materiale abrasivo come la sabbia e del materiale che attua un’azione di lucidatura. Gli impatti e l’attrito generatosi levigheranno quindi la superficie ottenendo gli stessi risultati della sabbiatura. Questo genere di trattamento è utilizzato prettamente per grandi produzioni.
Il Vapor smoothing è una tecnica usata raramente per rendere lucida e uniforme la superficie di manufatti in polimero, specialmente quelli in ABS. Consiste nel esporre per qualche secondo il particolare a dei vapori di solventi. Essendo operata in questo modo permette di raggiungere anche zone non accessibili mediante sabbiatura ma non in modo ottimale, anche la rimozione dei classici gradini sulle zone a vista non è ottimale.
Per velocità, convenienza rimane uno dei trattamenti più utilizzati assieme alla sabbiatura, possiede il grande vantaggio che può essere effettuata su praticamente ogni manufatto realizzato mediante produzione additiva.
L’elettroplaccatura si esegue immergendo in un bagno di ioni di una lega un particolare con carica contraria a quella degli ioni. Questi ultimi attratti dalla carica opposta si andranno a depositare sul particolare costituendo uno strato superficiale uniforme e molto leggero. Questo genere di lavorazione rende il particolare molto più apprezzabile dal punto di vista estetico, per questo viene spesso utilizzata anche sui particolari in polimero. Le leghe più comunemente utilizzate sono oro, argento, nichel e rame.
I manufatti realizzati mediante produzione additiva sono molto limitati nelle dimensioni dalle macchine che non permettono di realizzare particolari di grosse dimensioni, per ovviare a questo limite si può dividere l’oggetto finale in più parti e unirle dopo averle realizzate. Il genere di unione varia a seconda del materiale che si sta lavorando e alla tecnologia col quale è stato prodotto: si va dalla saldatura e brasatura alla saldatura ultrasuoni all’utilizzo di resine epossidiche e altri adesivi.
Manufatti in polimero ottenuti mediante tecnologie additive sono spesso molto fragili, uno dei metodi per migliorarne le proprietà meccaniche e di resistenza alla corrosione è quello del trattamento di infiltration. Questo consiste nel ricoprire la superficie del particolare di una resina epossidica che aiutata con una pompa del vuoto penetrerà nelle cavità della superficie andandole a riempire, una volta solidificata dopo un trattamento in forno la resina avrà creato una superficie isolante fra l’esterno e il particolare. Come si può facilmente dedurre questo trattamento funziona molto bene per i materiali porosi.
Le tecnologie additive possono essere utilizzate per tre operazioni principali:
I settori trainanti delle tecnologie additive sono: automotive, aereonautico e medicale. Questi settori infatti sono disposti a spendere per ottenere manufatti dalle prestazioni superiori o efficientamento del processo produttivo. Le applicazioni di queste tecnologie non hanno però confini come si può vedere dal massivo utilizzo che inizia a farne il settore dei beni culturali dove permettono tra le altre cose restauri impensabili altrimenti.
Le moderne tecnologie di additive manufacturing si prestano perfettamente alla creazione di prototipi in tempi molto ristretti aiutando quindi non solo i designer del prodotto a verificarne e validarne le caratteristiche ma anche ad esempio facilitando trattative che possono essere discusse con un prototipo sottomano. La prototipazione non richiede inoltre particolari accorgimenti progettuali, in quanto la produzione definitiva avverrà mediante tecnologie tradizionali, e può essere quindi effettuata senza ulteriori costi e anche durante step intermedi di progettazione.