Con l’obiettivo di analizzare e interpretare la fase di transizione importante che la manifattura sta attraversando, Ucisap ha potuto contare, in occasione delle European Tooling Forum organizzato a Milano, su un parterre di relatori d’eccezione in rappresentanza dell’industria di settore e non solo.
Il tentativo di leggere non solo il momento presente, ma di prevedere realisticamente le direttrici del futuro sviluppo dell’industria è stato il tema portante dello European Tooling Forum 2023 organizzato a Milano dall’Unione dei costruttori di stampi e attrezzature di precisione (Ucisap). Lo ha anticipato il vicepresidente, Andrea Di Girolamo, ricordando le molte sfide che la manifattura ha dovuto affrontare e superare negli ultimi anni e le tante che ancora l’attendono prima che si possa mettere la parola fine su quella che ha definito «una crisi sistemica complessa». Il «fare gruppo e sistema» condividendo opinioni ed esperienze può essere l’ingrediente segreto per reagire alle difficoltà introdotte da fattori molteplici. Prima l’emergenza sanitaria e poi il conflitto russo-ucraino; le criticità delle catene di approvvigionamento globali e via via le spinte inflattive e naturalmente il folle rally degli energetici. Mentre in Italia ed Europa – «la più colpita dall’inflazione» – la politica resta «ondivaga» la palla e la parola debbono passare ora a chi produce.
Italia-Germania (non) solo andata
E proprio l’intensità delle attività produttive e i conseguenti elevati valori in gioco accomunano due paesi al tempo stesso concorrenti strenui e affezionati partner quali Italia e Germania. Non a caso perciò, dopo il doveroso prologo di Di Girolamo, a entrare nel vivo delle relazioni è stato Markus Heseding, significativamente impegnato in un doppio ruolo. Quello di presidente dell’Associazione delle imprese tedesche della meccanica di precisione (VDMA); e numero uno – dallo scorso anno – della sigla continentale degli stampisti ISTMA Europe. La sua panoramica ha inevitabilmente preso le mosse dall’entità e dalle dinamiche dell’interscambio commerciale fra i due stati, ancora in crescita del 18% nel 2022 a 168 miliardi di euro fra beni e servizi. Non soltanto la vocazione manifatturiera spiccata e le diffuse specializzazioni e competenze apparentano però il made in Italy e la produzione tedesca, bensì pure i problemi: energia, trasformazione delle supply chain e skill shortage per primi. Toccata quota 252 miliardi di euro di vendite lo scorso anno – col traino di un incremento del 10,5% dei prezzi – il comparto tedesco dell’ingegneria meccanica è atteso da un’annata complessa lungo la quale i volumi reali di produzione potrebbero, secondo i pronostici, decrescere del 2%. A loro volta le attrezzature di precisione tedesche hanno registrato al 31 dicembre un «accettabile» +8% di fatturato grazie alla ripresa della domanda automotive più ancora che delle esportazioni. È stato, infatti, soddisfacente l’export verso gli Stati Uniti; mentre la richiesta da parte cinese è stata debole. Auto, macchine utensili e aerospazio sono le grandi speranze del tooling come dell’engineering, che potrebbero altresì trarre beneficio dal boom delle rinnovabili nonché dalla fame di tecnologie e parti indirizzati agli impianti di distribuzione di gas naturale liquefatto (LNG) o di fracking, altrove. Nondimeno, più o meno direttamente sospinte dalla guerra ai confini orientali d’Europa dovrebbero consolidarsi le relazioni con la difesa e la sicurezza e questa considerazione ha riportato Heseding alle riflessioni sulle incognite che tuttora gravano sull’andamento del manufacturing teutonico. Nonostante il moderato ottimismo dell’oggi, non è tempo di lasciarsi alle spalle o di sottovalutare i rischi rappresentati dalla guerra, dalla carenza di materie prime e – peggio ancora – di competenze.
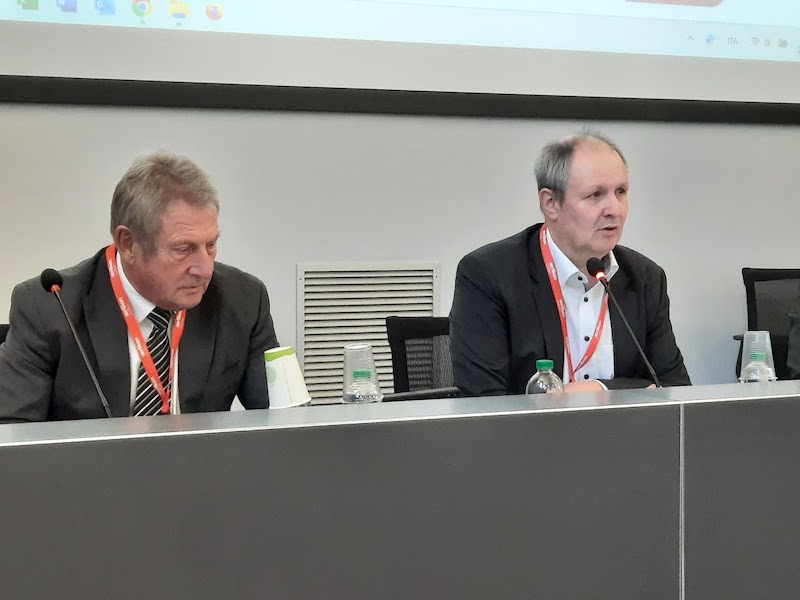
Uno spettro si aggira per l’Europa
L’estenuante ricerca di personale formato e possibilmente giovane è lo spettro che più di ogni altri minaccia l’Europa delle attrezzature di precisione – comunque in possesso di tutte le carte in regola per segnare un nuovo +8% nel 2023 – mentre in altre regioni del mondo il problema è sconosciuto. L’esempio viene da quel Sudafrica che è territorio d’origine di un altro illustre ospite del congresso e cioè il presidente di ISTMA World, Bob Williamson, e che vanta trend demografici del tutto opposti a quelli della Germania e – a maggior ragione – della Penisola italiana. Per questo non fatica a reperire fra i suoi cittadini un’alta disponibilità di manodopera dinamica e soprattutto under 30. Non esclusivamente di questo ha tuttavia discusso il presidente, giunto a Milano con l’obiettivo preciso di «dare agli stampisti un messaggio di semplicità». Il messaggio semplice è che «gli investimenti nell’industria degli stampi e delle attrezzature di precisione generano ritorni esponenziali» e che in loro assenza le nazioni «vanno incontro alla deindustrializzazione». Tooling, parola chiave dell’intervento di Williamson, in realtà è espressione onnicomprensiva che include anche le macchine, le linee di assemblaggio e gli utensili. Un insieme capace di dar vita nel 2021 a un valore di mercato pari a 218 miliardi di dollari, suscettibili di moltiplicarsi a 340 entro il 2027. Non dovessero bastare queste cifre a render ragione dell’incidenza delle aziende raccolte sotto le insegne di Ucisap e ISTMA, si deve considerare che proprio al tooling, «anello di congiunzione fra R&D e produzione», è riconducibile il 60% del costo di un prodotto finito. E gli strumenti usati per realizzarlo «non sono disponibili a scaffale», ma esito di personalizzazioni e customizzazioni. Alle loro spalle hanno un importante contenuto di «proprietà intellettuale» che deve essere difeso.
E allora, formiamo
Benché «semplice» – appunto – il concetto sembra esser passato in secondo piano negli ultimi quarant’anni nelle regioni nordoccidentali e industrializzate del pianeta che alla tutela del copyright e alle politiche di largo respiro hanno preferito gli interessi dell’immediato. Si sono rivolti così alla Cina e all’Oriente consentendo loro di emergere come principali concorrenti in virtù di uno know how che proprio in Occidente affondava le sue radici ed è stato al contrario barattato sull’altare della manodopera low cost. Le possibilità di un’inversione di rotta ci sono ma il cambio di direzione dev’essere in primo luogo di natura culturale e prender così le mosse da una volontà politica chiara. «Accendere i riflettori sulla bellezza» del lavoro di fabbrica – anziché su altri impieghi a prima vista più spettacolari e scintillanti – è la missione da perseguire per tornare ad attrarre i millennial nei reparti, almeno nella visione del segretario generale di Federmeccanica, Stefano Franchi. Questi, sottolineando come alla metalmeccanica sia attribuibile il 50% circa (300 milioni di euro) del volume d’affari dell’export nazionale, ha suggerito che in tema di formazione qualcosa, presso le imprese di casa nostra, stia cambiando. Fra gli 1.5 milioni di occupati sempre meno numerose sono quelle che un tempo si etichettavano come tute blu. L’impiego di fabbrica è sempre più di concetto e sulla testadopera – felice neologismo di Franchi, da contrapporre a manodopera, naturalmente – si vuol scommettere con crescente decisione in avvenire. Lo dicono i sondaggi della Federazione: degli investimenti preventivati dal 70% delle associate il 19% dovrebbe andare alla ricerca e sviluppo; il 25% all’innovazione tecnologica e il 32% ai beni strumentali. Ma il 21% al training. Un segnale forte, che Federmeccanica cerca dal canto suo di corroborare continuando sul percorso di incontri con scuole e famiglie, iniziando dalle primarie, perché sentite e profonde sono le esigenze.
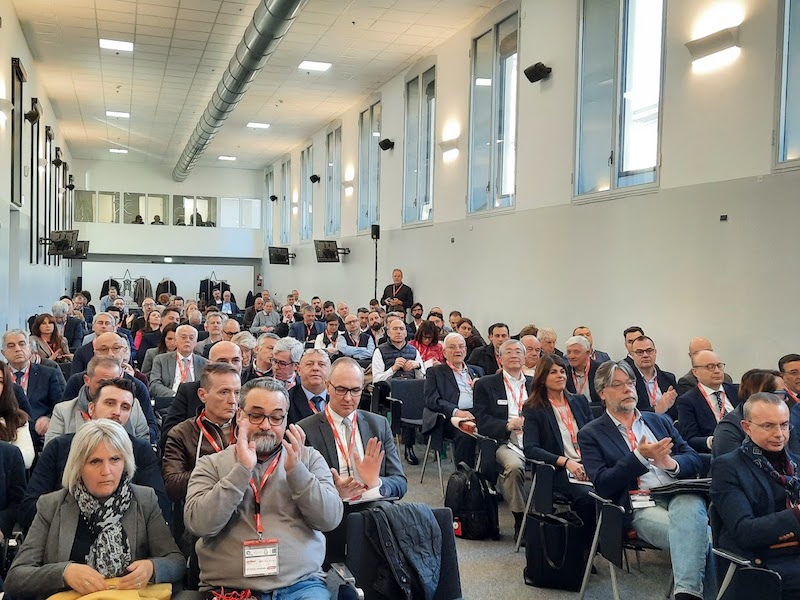
Alla larga dai condizionamenti
È stato infatti il 71% dei partecipanti alla survey tematica già menzionata in precedenza a lamentare gravi difficoltà nel reclutamento di personale fornito di competenze di base – per poco meno del 50% – o avanzate. In questo contesto ha preso forma il progetto Eureka! Funziona! approntato da Federmeccanica in collaborazione col Ministero per l’Istruzione, l’Università e la Ricerca (MIUR) e finalizzato all’educazione all’imprenditorialità per i bambini dell’ultimo triennio delle elementari. L’intenzione dichiarata non è certamente quella di condizionare le scelte degli alunni; quanto piuttosto di «evitare che essi subiscano i condizionamenti in negativo di altri». Dai report è emerso non a caso che il valore dell’occupazione di operaio non viene affatto percepito, quando addirittura non è sminuito; mentre i passi avanti compiuti con le iniziative di alternanza scuola-lavoro sono stati erosi dai ripensamenti della politica. Al contrario, bisognerebbe progettarne di più ambiziosi e puntare al bersaglio grosso della «didattica laboratoriale» trasformando ogni istituto in un «laboratorio permanente di idee». Cruciale da questo punto di vista è o dovrebbe essere il contributo delle istituzioni e delle partnership pubblico-privato, in un’ottica di «apprendimento continuo». Allo stesso tempo è auspicabile che si coltivino modelli imprenditoriali diversi e innovativi perché robusto è il bisogno di «aziende più strutturate e organizzate in maniera differente». In altre parole, di un paradigma d’impresa alternativo a quello attuale. Perché il paradosso è che anziché diminuire numericamente le realtà con meno di cinquanta addetti crescono attestandosi al 95,4% del totale; e si assottiglia il novero di quelle con una forza lavoro oltre le 250 teste, passate dal 2% allo 0,6%.
Il libro (verde) della sostenibilità
In rappresentanza dell’Associazione tedesca dei costruttori di stampi (VDWF), e in particolare del gruppo di lavoro sulla sostenibilità, il Dott. Wolfram Heger ha presentato allo European Tooling Forum 2023 di Milano un autentico vademecum della sostenibilità a uso delle attrezzerie. L’opera in questione è “Compendium for the Evaluation and Design of Sustainable Management in tool and moldmaking“. Il suo leitmotiv è riassumibile nell’assunto per il quale la sostenibilità deve essere a tutti gli effetti parte integrante delle strategie delle imprese il cui scopo finale oggi non può più essere la sola ricerca della profittabilità. Per la VDWF la sostenibilità richiede un approccio «olistico» e deve interessare un ampio ventaglio di funzioni aziendali, per poi riflettersi nell’impegno verso le comunità d’appartenenza e su scala più vasta, sui diritti e consumi responsabili. Il volume prende in considerazione le priorità strategiche e i temi chiave coi quali le imprese sono chiamate a confrontarsi, iniziando dall’attenta valutazione dei materiali utilizzati e il ciclo di vita dei prodotti. Indica poi ricorrendo a esempi pratici i passaggi da seguire per mettere a punto un’analisi completa dell’impatto delle attività produttive – dalla progettazione al riciclo di materiali e manufatti – sulla scorta di indicatori affidabili e in ossequio ai regolamenti internazionali. Il traguardo ultimo è la decarbonizzazione; come coglierlo lo spiega il compendio, ottenibile gratuitamente su www.vdwf.de.
La manifattura che verrà, fra opportunità e sfide
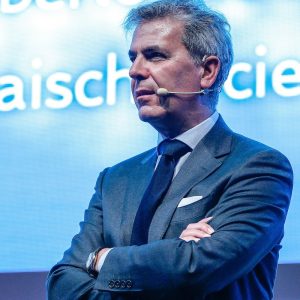
Se già il segretario generale di Federmeccanica, Stefano Franchi, ha alluso alla necessità di introdurre nuovi modelli di imprenditorialità e business per lo sviluppo dell’industria manifatturiera, alcuni di questi possibili paradigmi sono stati poi illustrati in maggiore dettaglio dal Prof. Marco Taisch. Il docente della School of Management presso il Politecnico di Milano, nonchè chairman scientifico del World Manufacturing Forum, si è soffermato – ed è intenzione di Stampi tornare sulla sua relazione nei prossimi numeri – sulle sfide che attendono l’industria: dalla caccia alle materie prime sino all’accorciamento del time-to-market, passando inevitabilmente per la sostenibilità. E ha descritto gli strumenti grazie ai quali, dandosi una nuova veste, le aziende possono vincerle. È in crescita per esempio il ricorso all’intelligenza artificiale come driver del vantaggio competitivo; e allo stesso tempo si sta viaggiando verso la servitizzazione, il primato del servizio sul prodotto in sé. La valorizzazione delle operazioni da remoto che la stessa pandemia ha promosso sospinge la crescita globale (+100% entro il 2024) dei cosiddetti advanced service contract: manutenzione a distanza e predittiva; efficientamento delle operazioni e digitalizzazione del training, fra gli altri. Le tecnologie 4.0 e l’Internet delle Cose, unitamente alle analytics e alla manifattura additiva, sono fra le risorse a disposizione delle imprese per concretizzare il sogno di un’economia smart. Ovvero fatta di un ciclo di vita e di una supply chain, infine di una fabbrica, intelligenti e perciò efficienti. Meglio rispondenti, possibilmente, alle esigenze della nuova generazione dei nativi digitali che sono anche sustainable native e che hanno dinanzi a sé la prospettiva di lanciarsi in un mercato del lavoro in larga parte popolato di professionalità – circa 200 – sorte di recente o del tutto inedite.