Anche il più corretto processo di saldatura può nascondere il rischio di tensioni residue. Ma come nascono e che effetti hanno questi pericolosi anticipatori di failure inattese?
Per chi abbia una certa dimestichezza con la filosofia della scienza, sa bene come il metodo del “rasoio di Occam” sia spesso indicato come la base del moderno pensiero scientifico. Premesso che in realtà questo monaco francescano del XIV secolo fu più il primo utilizzatore sistematico che l’elaboratore del concetto (e per di più applicandolo al contesto meno scientifico che ci sia, la teologia), in cosa consiste questo “rasoio di Occam”?
È quel rasoio che va usato per “tagliare via” dal problema che affrontiamo tutto quello che può essere eliminato senza pregiudicare la possibilità di capire il problema stesso.
Applicando questo approccio a una rottura, qualunque essa sia, si ha che ogni failure (e utilizzo questo termine perché di significato più ampio del termine “rottura”) avviene perché il livello delle sollecitazioni ha superato il limite di resistenza del materiale.
E quando la rottura è imprevista, le opzioni possibili da cui partire per la failure analysis sono solo due:
- il materiale ha una resistenza inferiore al previsto;
- le sollecitazioni sono superiori al previsto.
E come direbbe il buon Occam, tertium non datur cioè altre ipotesi non ce ne sono…
Quelle rotture inspiegabili
Premesso che è sempre difficile generalizzare (e che l’eccezione è sempre nascosta dietro l’angolo) non credo di esagerare affermando che niente come le saldature sembra essere soggetto a failure inattese, talvolta senza neanche attendere l’entrata in esercizio del componente, anche quando il processo di saldatura sembra essere stato fatto in maniera tecnicamente corretta.
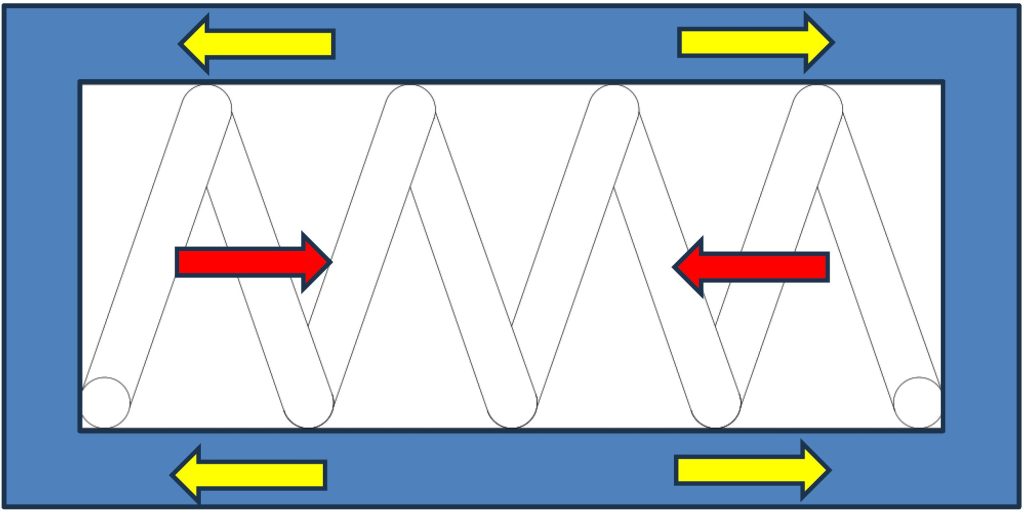
Come ben noto, per definizione la saldatura è un procedimento tecnologico con il quale si ottiene un collegamento continuo tra parti inizialmente separate mediante una continuità fisica ottenuta attraverso la fusione e successiva risolidificazione di materiale, materiale che può essere riportato (saldatura eterogena) o provenire direttamente dai componenti da unire (saldatura autogena).
Sempre usando il nostro rasoio, possiamo dire che una diminuzione della resistenza del materiale coinvolto nel processo di saldatura può avere due origini: o una diminuzione delle caratteristiche metallurgiche o una soluzione di continuità dello stesso, con conseguente riduzione della sezione utile resistente.
Per quanto riguarda le caratteristiche del materiale, un eventuale materiale di apporto viene scelto con caratteristiche di resistenza superiori a quelle del materiale di base, mentre il materiale di base al termine della risolidificazione ritorna uguale a se stesso, una condizione per altro facilmente verificabile con un semplice durometro portatile: pertanto se non è possibile avere “a priori” una certezza sul mantenimento delle caratteristiche meccaniche del materiale, è pur vero che i normali strumenti del controllo qualità possono sempre confermarcela.
Analogamente un buon controllo qualità è in grado, mediante opportune tecniche di verifica a ultrasuoni e/o radiografiche, di escludere tutti quei fenomeni che riducono la sezione resistente o possono agire da intensificatori macroscopici della sollecitazione come fessurazioni, mancanze di materiale o fusioni fredde: possiamo quindi dire con ragionevole certezza che da un punto di vista metallurgico e meccanico i materiali coinvolti in una saldatura immessa in esercizio non presentano degradi rispetto a quanto previsto, sia dal punto di vista metallurgico sia dal punto di vista strutturale.
Ma se escludiamo che nella saldatura improvvisamente collassata a degradare fosse stata la resistenza del materiale, sempre secondo il nostro monaco francescano non resta che concludere che siano state le sollecitazioni ad essere invece aumentate…
Ma considerando che talvolta queste improvvise rotture avvengono addirittura prima che i componenti entrino in esercizio, non resta che concludere che l’origine di queste sollecitazioni sia non esterna ma interna al materiale.
Per cui… benvenuti nel misterioso mondo delle tensioni residue!
Un nemico interno
Come abbiamo appena visto in precedenza, è un dato di fatto la presenza di rotture precoci, sia in forma plastica sia sotto forma di fatica, in presenza di sollecitazioni esterne che assolutamente non giustificano la rottura stessa, o addirittura sono assenti.
In realtà, visto che comunque la meccanica segue leggi che casuali non sono, perché ci sia una rottura le sollecitazioni ci devono essere e devono superare il limite di resistenza del materiale, che sia quello a rottura o a fatica.
E in effetti queste sollecitazioni ci sono, ben nascoste ma ci sono: è solo che non sono sollecitazioni applicate esternamente al corpo come quelle che siamo abituati a considerare, ma sono sollecitazioni che nascono all’interno del materiale e si equilibrano all’interno del corpo steso, senza manifestarsi esternamente.
La caratteristica di queste tensioni di svilupparsi internamente al corpo le fa definire spesso “tensioni interne”, anche se il termine più utilizzato è di solito “tensioni residue”, una denominazione che deriva dal fatto che quando il fenomeno venne individuato e affrontato scientificamente (alla fine del XIX secolo) queste tensioni interne vennero spiegate come la memoria (cioè il residuo) della sequenza di trasformazioni meccaniche, chimiche e fisiche a cui il materiale era stato sottoposto.
Ma, a prescindere dal nome che gli si vuole dare, in pratica cosa sono le “tensioni residue”?
Utilizzando una delle loro definizioni “canoniche”, si definiscono tensioni residue tutte quelle tensioni presenti all’interno di un corpo quando questo è in condizioni di equilibrio con l’ambiente circostante.
Un’immagine che credo renda bene il concetto di quelle che sono le tensioni residue è una molla inserita in un alloggiamento: un elemento che preso nel suo complesso è in condizioni di assoluto equilibrio statico, ma che se lo consideriamo nelle sue componenti troviamo che questo equilibrio nasce dalla compensazione tra la spinta esercitata dalla molla e la reazione ad essa opposta dal contenitore in cui è alloggiata. (figura 1).
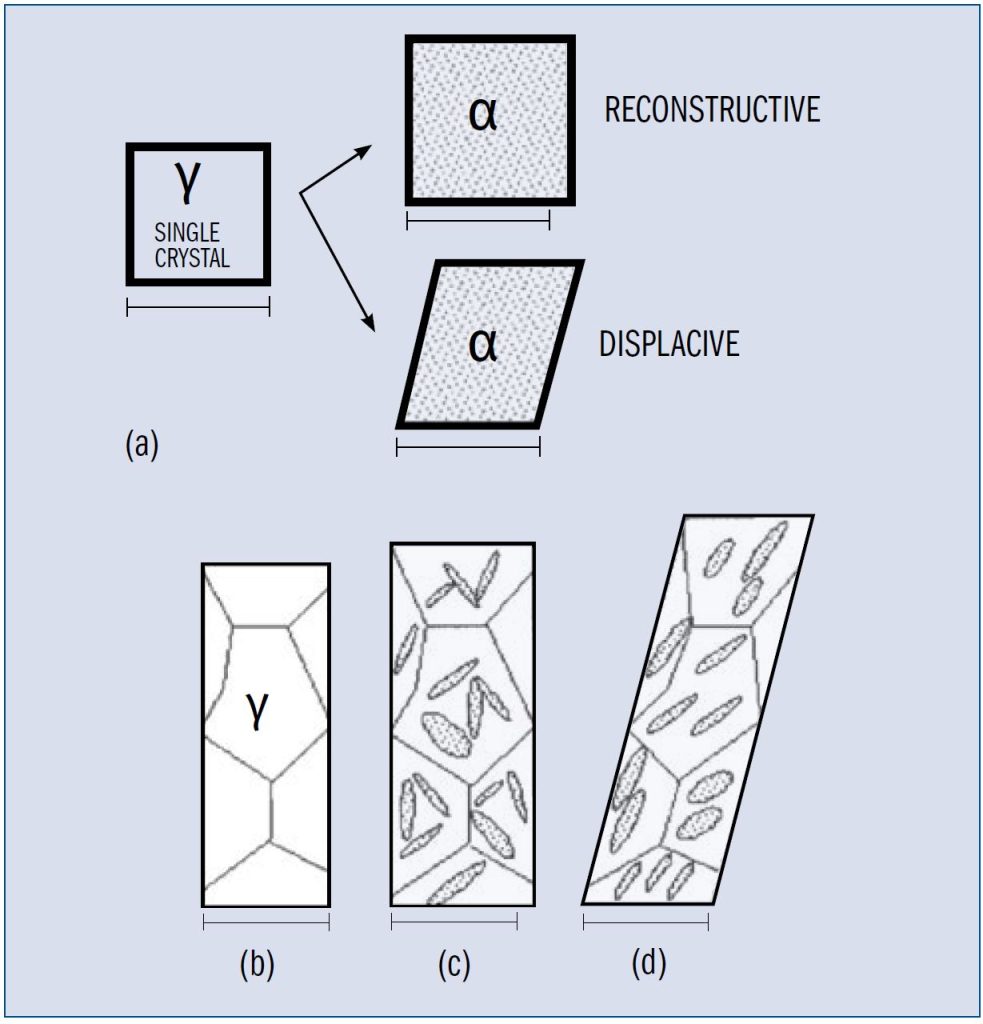
Sempre parlando in termini generali, le condizioni affinché possano instaurarsi tensioni residue all’interno di un corpo fisicamente omogeneo sono la presenza di disomogeneità nelle caratteristiche meccaniche del materiale. La natura di queste disomogeneità può essere quanto mai varia, potendo essere chimica, termica o metallurgica, e possono manifestarsi sotto forma di differenza del coefficiente di espansione termica, del modulo elastico, del limite di snervamento o di altri analoghi parametri meccanici.
Come è facile riconoscere, è una condizione che si adatta perfettamente alla saldatura!
Consideriamo infatti il caso di una saldatura eterogena tra due elementi di acciaio:
- una prima disomogeneità riguarda gli stessi materiali, essendo il materiale di apporto solitamente diverso dal materiale base;
- una seconda disomogeneità è poi insita nello stesso acciaio che costituisce il materiale di base, essendo per definizione l’acciaio un sistema multifasico in cui possono coesistere martensite, austenite, perlite o bainite, ciascuna con proprie caratteristiche meccaniche e termiche;
come se non bastasse, non dobbiamo dimenticare che nella ZTA la condizione metallurgica cambia da punto a punto in funzione della distanza dalla zona fusa e dalla superficie di raffreddamento.
Vediamo quindi più in dettaglio quali possono essere i meccanismi che fanno nascere questi anomali stati tensionali in una saldatura.
Nascita delle tensioni residue per via termica
I meccanismi attraverso cui si vengono a creare tensioni residue per via termica sono essenzialmente due, eventualmente combinati tra di loro:
- nel caso di sistemi multifasici (ad esempio ferritico e austenitico), la differenza tra i coefficienti di espansione termica in caso di variazioni di temperatura come durante un raffreddamento;
- la non contemporaneità del raffreddamento tra le diverse zone dello stesso componente precedentemente riscaldato, soprattutto in presenza di forti vincoli esterni che “blocchino” la deformazione complessiva del componente.
Nascita delle tensioni residue per via metallurgica
Ogni qualvolta una trasformazione di fase implica una variazione nella struttura cristallina del materiale, questo comporta variazioni volumiche dei singoli grani, che all’interno di un contesto più o meno rigidamente vincolato porta alla nascita di tensionamenti elasto-plastici nel materiale.
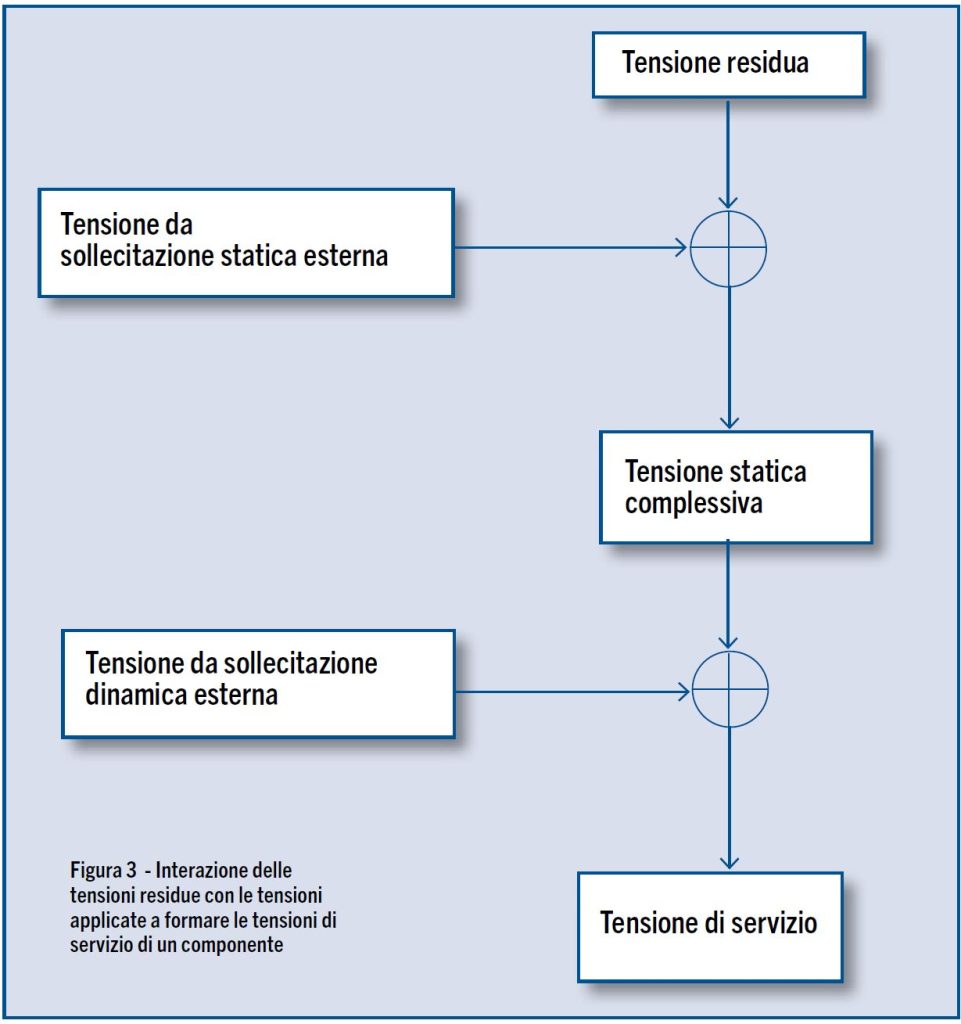
Tale effetto è ancora più accentuato nel caso di leghe multifasiche, nelle quali oltre alla variazione di volume intrinseca dei singoli grani si devono anche gestire la differenza di variazione di volume tra le diverse fasi.
È quindi facile comprendere come in una lega bifasica costituita da grani aventi diversa struttura successivamente al raffreddamento siano presenti forti stati tensionali interni.
Nella figura 2 è rappresentata prima la variazione di volume e di forma di un singolo grano di austenite che si trasforma in ferrite, con passaggio da struttura cubica a corpo centrato a struttura cubica a facce centrate. A seconda che la trasformazione avvenga con meccanismo di ricostruzione o di diffusione il nuovo grano risulta semplicemente un “ingrandimento” del precedente o una sua replica distorta.
Nella seconda parte della figura 2 si vede l’effetto dimensionale macroscopico della trasformazione da austenite a ferrite su un componente: nel caso in cui il componente sia privo di vincolo esterno il risultato è una deformazione, se il vincolo è invece presente il risultato è la nascita di tensioni interne.
Gli effetti delle tensioni residue sulla resistenza a fatica del materiale
Fino a questo momento abbiamo affrontato le tensioni residue come la spiegazione delle difettosità macroscopiche presenti nella saldatura prima ancora della messa in esercizio.
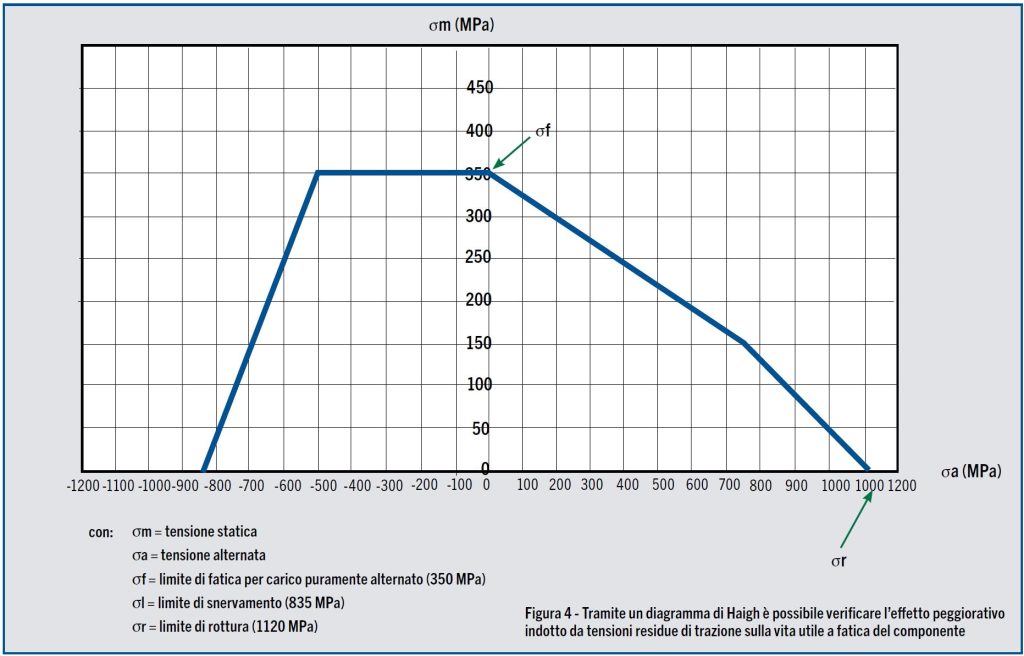
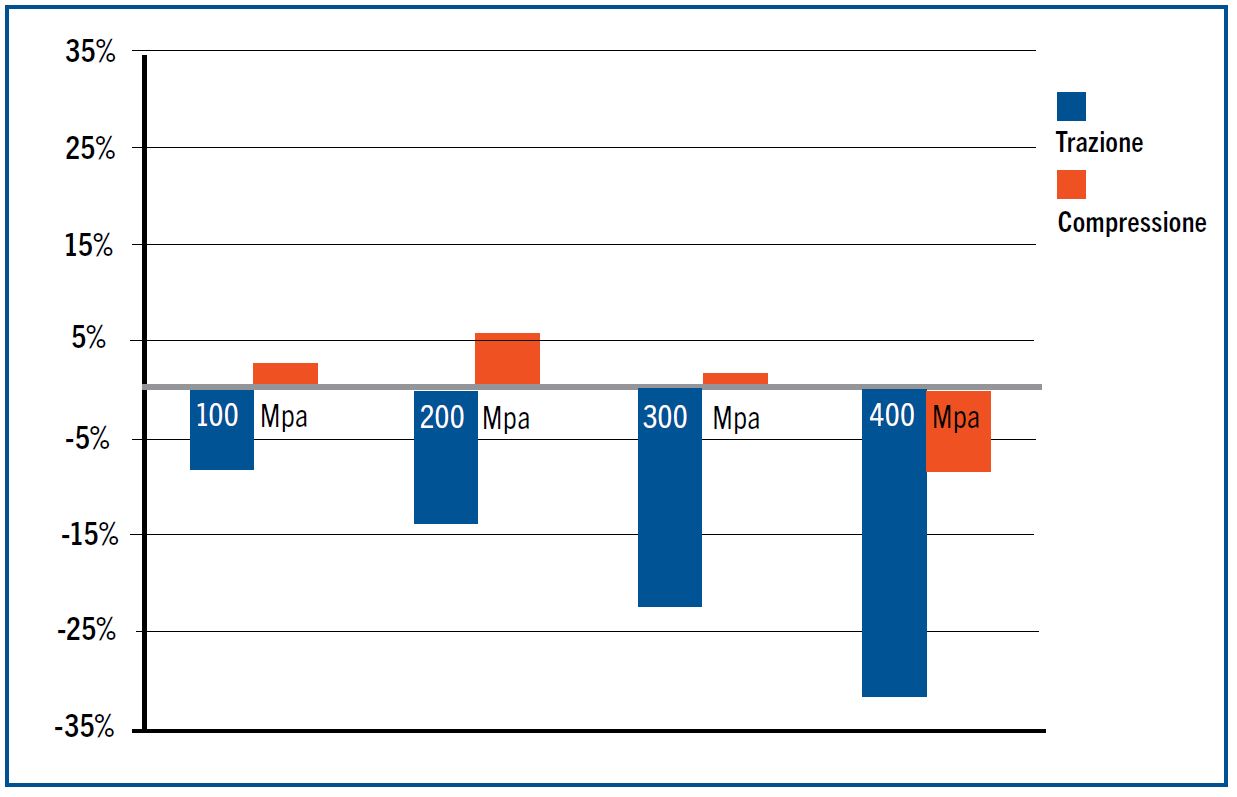
In realtà la condizione di massima pericolosità delle tensioni residue non è tanto quando esse portano alla comparsa di difettosità nella saldatura prima della messa in esercizio, ma piuttosto quando esse rimangono per così dire nascoste all’interno del componente, per poi dare luogo a rotture per fatica in esercizio apparentemente inspiegabili.
Infatti, nel caso in cui le tensioni residue siano presenti ma senza arrivare al limite di rottura del materiale, la loro apparentemente invisibilità le rende un “nemico” estremamente subdolo e pericoloso, individuabile unicamente mediante specifiche tecniche di misurazione.
Un nemico in quanto nel corso dell’utilizzo del componente le tensioni residue devono essere trattate come ogni altra forma di tensione statica presente sul corpo, e combinate linearmente con esse, e pertanto la presenza di tensioni residue ha effetti migliorativi o peggiorativi sulle caratteristiche di resistenza statica e a fatica di un componente, a seconda della natura trattiva o compressiva che esse assumono (figura 3).
Per esempio, in termini di vita utile a fatica l’effetto delle tensioni residue può essere considerato ricorrendo a tradizionali modelli di calcolo come quelli del diagramma di Haigh che, a partire dalla conoscenza della sollecitazione alternata σf che garantisca una vita utile pari a Nf cicli, permette di calcolare quale sia l’ampiezza σf della sollecitazione alternata che, in presenza di una sollecitazione statica di ampiezza σm, permetta la stessa vita utile. In figura 7 è riportato un diagramma di Haigh riferito ad un acciaio da cementazione 16 CrNi4, è facile osservare come:
- tensioni residue di tipo trattivo comportino sempre un significativo peggioramento del limite di fatica;
- tensioni residue di tipo compressivo comportino un medio miglioramento del limite di fatica per bassi valori delle stesse, mentre per valori più elevati l’effetto sia comunque peggiorativo.
In figura 5 è riportata una quantificazione numerica di tale effetto per valori via via crescenti di tensioni residue trattive e compressive: è facile verificare quanto possa essere deleterio, in termini di vita utile a fatica, la presenza di uno stato di tensioni residue in trazione come quello solitamente indotto dalla saldatura, soprattutto considerando che la relazione tra limite di fatica e vita utile è di tipo esponenziale, per cui, ad esempio, per una sollecitazione dinamica dell’ordine dei 600 Mpa la presenza di tensioni residue dell’ordine dei 200Mpa comportano una riduzione della vita utile attesa da 190.000 a 23.000 cicli!
Conclusioni
Le tensioni residue nascono dalla presenza all’interno di materiale di “disomogeneità”, o dalla memoria di disomogeneità presenti nel corso delle lavorazioni precedenti e poi bloccate durante le successive trasformazioni.
Tali disomogeneità possono riguardare tutte le caratteristiche meccaniche o metallurgiche di un materiale, e in pratica ogni passaggio meccanico, metallurgico, chimico o termico influisce significativamente sulle tensioni residue.
Per la sua caratteristica di processo che comporta la compenetrazione di materiali diversi mediante un processo ad alta temperatura come è la fusione, la saldatura presenta quindi tutte le condizioni preliminari per l’instaurarsi di deleterie tensioni residue, tensioni che possono dar luogo immediatamente a rotture e deformazione nei materiali coinvolti, ma ancora più spesso generare stati tensionali interni che, sovrapposti alle sollecitazioni di esercizio, possono portare a rotture a fatica precoci e apparentemente inspiegabili dei componenti saldati.
In ogni caso è evidente l’opportunità di poter procedere alla verifica sperimentale degli stati di tensione residua eventualmente presenti, e la nostra prossima pubblicazione sarà indirizzata proprio a illustrare le diverse metodologie di misurazione delle tensioni residue presenti in un componente saldato: un ausilio fondamentale sia per la verifica qualitativa di singole saldature sia, soprattutto, per la messa a punto di processi di saldatura automatizzati.