Le principali acciaierie del vecchio continente stanno avviando la produzione di acciaio a zero CO₂. Obiettivo: rendere la siderurgia un settore non inquinante entro i prossimi decenni. La tecnologia c’è; quello che manca è l’energia.
Siccità estrema, nubifragi, allagamenti, grandine grossa come arance: gli eventi meteo di questi ultimi mesi hanno reso ancora più evidente come il clima stia dando sempre più segni di squilibrio. Il cambiamento climatico è una realtà che peggiora anno dopo anno, anche in Paesi come l’Italia.
Fino a un paio di decenni fa, eventi eccezionali come quelli a cui abbiamo assistito erano, nel nostro immaginario, relegati a terre lontane come le pianure americane, l’Africa, o i tropici. Ridurre le nostre emissioni di anidride carbonica è un obiettivo imprescindibile, e a questa sfida deve partecipare anche il settore metalmeccanico. La siderurgia è infatti responsabile del 7÷9% della CO₂ prodotta.
L’Unione Europea si è già espressa in tal senso, varando iniziative ambiziose per affrontare le sfide delle emissioni di CO₂ nel settore siderurgico. Attraverso il “Patto Verde Europeo“, l’UE mira a raggiungere la neutralità climatica entro il 2050. Nel settore siderurgico, ciò implica una transizione verso tecnologie innovative e processi a basse emissioni di carbonio.
L’UE ha istituito il “Fondo per una transizione giusta”, che sostiene le regioni industriali nell’adottare pratiche sostenibili. Inoltre, sono state introdotte normative più rigorose per promuovere l’efficienza energetica e incoraggiare l’adozione di tecnologie pulite, come l’idrogeno verde, per ridurre le emissioni di CO₂ nel processo di produzione dell’acciaio. Queste iniziative riflettono l’impegno dell’UE nel trasformare il settore siderurgico in un attore chiave nella lotta al cambiamento climatico.
La riduzione diretta a idrogeno
Il grosso della CO₂ viene emessa durante la fase di riduzione del minerale ferroso nell’altoforno: qui il carbonio presente nel carbone sottrae ossigeno all’ossido di ferro. In questo modo si ottiene ferro metallico, insieme ad una grande quantità di anidride carbonica. All’atto pratico, quasi 2 t di CO₂ per ogni t di acciaio prodotto.
Questa riduzione può avvenire anche impiegando idrogeno gassoso; ne abbiamo parlato in questa rivista già due anni fa, in un articolo dal titolo “La siderurgia europea accende i motori ad idrogeno”. Il piano Europeo H2FUTURE, finalizzato ad incentivare l’economia all’idrogeno, trova applicazione anche nelle acciaierie.
Gli effetti di queste politiche sono già visibili, e anche qui l’apparato industriale del Vecchio Continente si mostra all’avanguardia nel tracciare la strada. Alcuni colossi della siderurgia stanno infatti avviando progetti sperimentali per la produzione di acciaio “Net-Zero”, ovvero quello prodotto con un bilancio neutrale nelle emissioni di gas serra.
Due a (net) zero per la Svezia
Il produttore svedese SSAB ha iniziato la commercializzazione del primo acciaio prodotto senza l’uso di combustibili fossili già nel 2021. Destinataria della prima fornitura, un’azienda connazionale, Volvo AB. Si trattava però di una produzione pilota, denominata SSAB Fossil-free e ottenuta tramite il processo HYBRIT. HYBRIT sfrutta l’idrogeno per la riduzione diretta dell’ossido di ferro; anche di questo progetto abbiamo parlato nell’articolo già citato.
La tecnologia è ancora allo stadio sperimentale e le quantità prodotte si aggirano su qualche centinaia di tonnellate. La produzione su larga scala è prevista per il 2026.
Per far fronte alla richiesta di metallo con una minore impronta ambientale, SSAB ha recentemente affiancato all’acciaio Fossil-free il nuovo SSAB Zero™. Non si tratta di ferro primario, bensì di acciaio riciclato prodotto con forni elettrici ad arco. L’energia elettrica è ottenuta da fonti rinnovabili.
Secondo SSAB, la produzione dell’acciaio SSAB Zero™ emette l’equivalente di circa 50 kg di CO₂ in tutta la produzione, compreso il trasporto. La qualità e le proprietà di SSAB Zero™ saranno equivalenti agli acciai convenzionali di SSAB. L’obiettivo del produttore svedese è fornire 40.000 tonnellate di SSAB Zero™ al mercato nel 2023, aumentando a circa 100.000 tonnellate nel 2025.
Restando in Svezia troviamo la neonata H2greensteel, un’acciaieria innovativa che nel 2024 avvierà la produzione di acciaio sostenibile, con emissioni di anidride carbonica ridotte del 95%. Al progetto, sviluppato nel quadro del programma comunitario NextGenerationEU, partecipano aziende come Marcegaglia, Mercedes-Benz, Scania, Kobelco, Hitachi, e altre.
Austria e Italia
Il produttore austriaco voestalpine è al lavoro per convertire i propri altoforni alla produzione di acciaio fossil-free. Dal 2027 introdurrà parzialmente il processo di riduzione tramite idrogeno, con un processo “ibrido” denominato greentec. Ciò consentirà di abbattere del 30% le emissioni di gas serra, ovvero circa il 5% delle emissioni dell’intera Austria. L’obiettivo finale è arrivare all’acciaio Net-Zero entro il 2050.
Passando alla produzione secondaria e al riciclo, troviamo stavolta un’eccellenza italiana, la Arvedi di Cremona. Qui non si tratta però di una singola linea di prodotti: l’intera produzione è Carbon Neutral. Su richiesta, il laminatore lombardo emetterà la certificazione ArvZero.
La riduzione delle emissioni ottenuta è notevole: Arvedi è passata dai 2100 kg di CO₂ per ogni tonnellata di lamiera a uno stupefacente valore di soli 133 kg/t. Le chiavi per ottenere questo importante risultato sono molteplici:
- aumento della percentuale di metallo riciclato fino all’80%, con una minore quantità di componenti impure;
- utilizzo di energia al 100% proveniente da fonti rinnovabili;
- riciclo degli scarti di lavorazione.
Per finire, le emissioni residue ed inevitabili sono interamente compensate con l’acquisto di “crediti” VCS, ovvero con la riforestazione.
Fuori dall’Europa
Un approccio analogo è quello adottato dalla statunitense Nucor Steel, con la certificazione Econiq. Anche qui non si tratta di un prodotto definito ma di un’attestazione di neutralità climatica, ottenibile dal cliente su richiesta per una specifica fornitura.
Nucor Steel combina l’acquisto di crediti di riforestazione all’uso di energie rinnovabili. L’acciaieria è il settimo maggior utilizzatore di elettricità pulita degli USA, con oltre 350 MW.
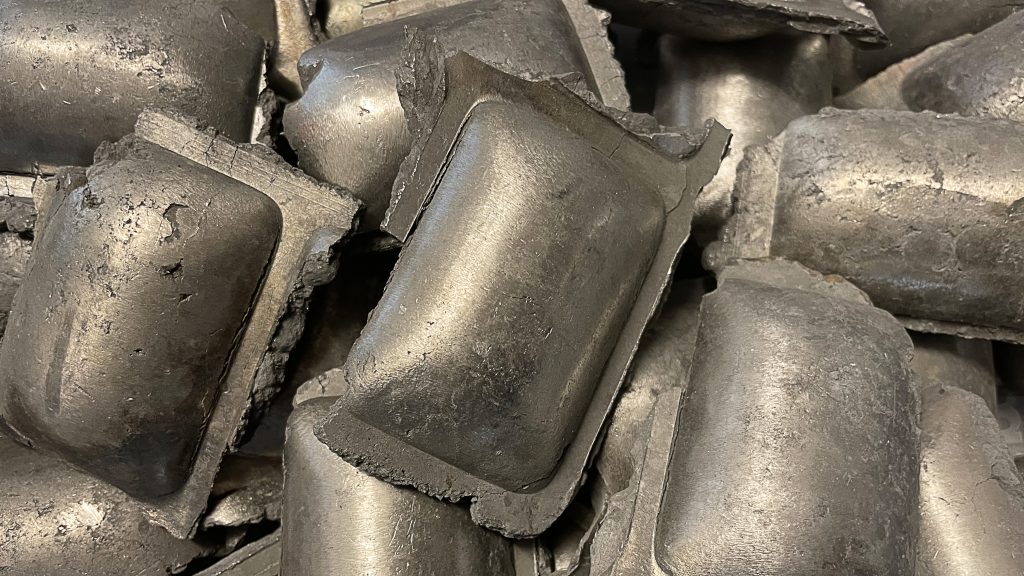
Menzione speciale per la Commercial metals company, un’azienda dell’Arizona che si occupa di riciclaggio di acciaio. In questo impianto batte un cuore italiano, o meglio friulano: la Danieli sta infatti installando un nuovo tipo di forno fusore ibrido ad alte prestazioni, in grado di funzionare sia tramite elettricità (meglio se rinnovabile) che, in futuro, ad idrogeno.
Le emissioni di anidride carbonica sono ridotte anche di 10 volte rispetto ad un altoforno tradizionale. Questo impianto pilota sta già riscuotendo molto successo anche per i ridotti tempi di avviamento e produzione del metallo fuso.
Andiamo ora in Asia; più precisamente in Cina, dove ha sede la più grande acciaieria del mondo, Baowu. Nata dalla fusione tra la Baosteel e la Wuhan Steel, questo colosso si è impegnato a raggiungere l’ambizioso obiettivo della completa decarbonizzazione entro il 2050. Anche qui la parola d’ordine è l’idrogeno, attraverso il processo di riduzione diretta.
La strada è ancora lunga, e al momento Baowu non dispone di prodotti Net-Zero commerciabili. Da notare però un primo timido passo, con l’acquisto di 60 camion ad idrogeno a celle combustibili.
ArcelorMittal non ha perso il treno
Il grande assente è ArcelorMittal; ma l’assenza è temporanea. Il colosso al momento non dispone di acciaio Net-Zero, ma sta portando avanti due piani strategici in questa direzione: Smart Carbon e Innovative DRI.
Nel percorso Smart Carbon, si cerca di ridurre l’uso del carbone negli altoforni con fonti alternative di carbonio circolare proveniente dai rifiuti, come biomassa sostenibile o plastica riciclata. Questo non solo ridurrebbe le emissioni di CO2, ma potrebbe anche integrare tecnologie di cattura e riutilizzo (CCU) o stoccaggio (CCS) del carbonio, rendendo il processo addirittura carbon-negative.
Dall’altro lato, il percorso Innovative DRI si concentra sulla riduzione diretta del ferro (DRI) attraverso l’uso di idrogeno come agente riducente al posto del gas naturale.
L’idrogeno, se prodotto da elettrolisi dell’acqua con energia rinnovabile, potrebbe rendere il processo di produzione di DRI completamente a emissioni zero. Questo percorso mira a realizzare acciaio senza alcuna emissione di carbonio durante la produzione. Tuttavia, l’adozione di questi percorsi non è priva di sfide.
Ad esempio, l’infrastruttura per produrre idrogeno “verde” su larga scala è ancora in fase di sviluppo, e quindi il gas naturale, dal quale si ottiene l’idrogeno “blu”, potrebbe essere utilizzato come soluzione transitoria. Inoltre, la necessità di tecnologie di cattura e stoccaggio del carbonio è cruciale per affrontare le emissioni ancora presenti nei processi.
Non tutto l’idrogeno è uguale
Già, perché c’è idrogeno e idrogeno. Quello “verde” è ottenuto per elettrolisi dell’acqua e, se l’energia elettrica proviene da fonti rinnovabili rappresenta una soluzione realmente ecologica e sostenibile.
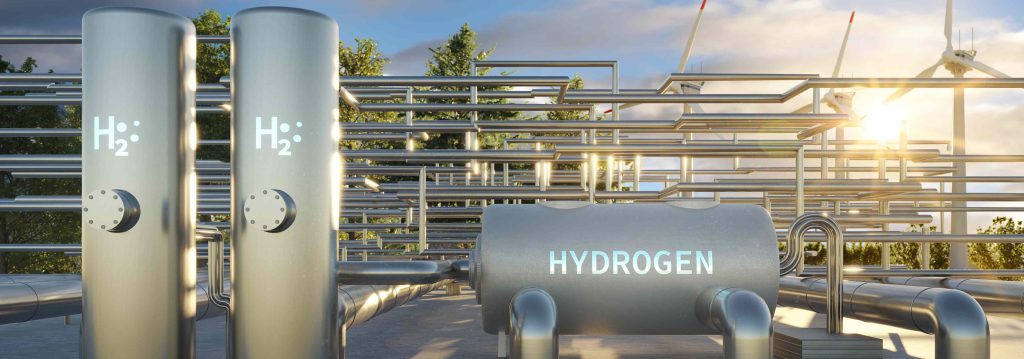
Quello “blu” invece viene prodotto estraendolo dal gas naturale, il metano, con formula CH₄. Avanza un atomo di carbonio, che attualmente viene stoccato in depositi geologici, ovvero iniettato nel sottosuolo. Lì permane bloccato senza fuoriuscire, teoricamente per almeno qualche migliaio di anni.
Molte speranze, qualche dubbio
Resta un grosso punto interrogativo, ad oscurare gli importanti passi avanti dell’industria siderurgica. La transizione all’acciaio Net-Zero richiederà una enorme quantità di energia. Secondo alcune stime, la decarbonizzazione del settore comporterà una domanda di circa ~5.000 TWh all’anno.
L’intera produzione elettrica europea si aggira attualmente attorno ai 3200 TWh. All’elettricità vanno aggiunte 40 milioni di tonnellate di idrogeno. Il dibattito su come trovare tutta questa elettricità è aperto. Più che negli altoforni, prevediamo dibattiti infuocati e temperature elevatissime anche nelle aule dei vari Parlamenti.