Guide lineari: caratteristiche generali, metodi di calcolo e di monitoraggio mediante reti neurali
Le guide lineari sono organi di collegamento a scorrimento che impiegano elementi sferici di ricircolo posizionati in apposite sedi e collocate tra le guide stesse e una slitta. Grazie al ridotto attrito e alla elevata precisione in movimento, le guide lineari sono ampiamente utilizzate nei sistemi di movimentazione, di apparecchiature automatiche e macchine utensili. Per aumentare la capacità di carico, le guide lineari vengono opportunamente precaricate, inserendo sfere sovradimensionate all’interno delle sedi. La superficie di contatto dei corpi volventi sferici con la sede rappresenta l’anello debole del sistema. In questa regione, infatti, esiste una rigidezza di contatto non lineare rispetto al carico esterno, influenzata dal precarico che agisce sulle sfere. Si è osservato che il precarico applicato ai corpi volventi modifica in modo significativo la risposta dinamica della guida lineare. Allo stesso tempo, organi meccanici comprendenti elementi volventi, conferiscono caratteristiche statiche e dinamiche della macchina utensile differenti in base alle caratteristiche della interfaccia di contatto e del precarico applicato ai corpi volventi. Ovviamente va aggiunto il fatto che, in caso di funzionamento prolungato, gli elementi volventi e le piste di rotolamento delle guide lineari sono soggetti ad usura ed alla variazione delle loro proprietà originarie.
Attualmente si può osservare l’ampio utilizzo di varie metodologie “data-driven” per il cosiddetto PHM (prognostics and health management), ovvero per il condition monitoring di macchine utensili, la prevenzione dei loro guasti e l’analisi del degrado delle prestazioni del sistema. Grazie all’analisi delle vibrazioni, ad esempio, eventuali anomalie possono essere rilevate dagli accelerometri collegati alla macchina e confrontate direttamente con i valori accertati in condizioni di progetto. La determinazione delle caratteristiche della macchina a partire dai segnali di vibrazione è un prerequisito fondamentale per la diagnosi delle modalità di guasto dei componenti o dei corpi volventi presenti,ad esempio, in guide lineari poste all’interno della macchina stessa. Alcuni degli algoritmi per il calcolo delle condizioni dei sistemi includono la trasformata Wavelet, il processo di decomposizione in modalità empirica (EMD) e la trasformata di Hilbert-Huang (HHT).
Le caratteristiche estratte diventano efficaci input per lo sviluppo di reti neurali capaci di identificare situazioni di guasto. Inoltre, algoritmi di intelligenza artificiale, come algoritmi genetici, logica “fuzzy” e reti neurali artificiali, sono impiegati per sviluppare modelli predittivi per il rilevamento dei guasti dei meccanismi rotanti con cuscinetti.
Numerosi studi dimostrano quanto l’accuratezza di una diagnosi di guasto dipenda dall’estrazione corretta delle caratteristiche della macchina e dai loro metodi di classificazione. Algoritmi di apprendimento automatico (come, ad esempio, il SVM – Support Vector Machines) sono considerati appropriati per stabilire il modello di classificazione. Tali approcci possono essere ulteriormente implementati ed integrati con un filtro intelligente capace di individuare le caratteristiche ottimali per alimentare il modello di classificazione dei guasti.
Come i cuscinetti volventi, anche le guide lineari sono soggette a guasti e ad usura superficiale in caso di carichi prolungati e la diagnosi dei guasti può essere condotta mediante l’analisi del segnale di vibrazione. Considerando che le caratteristiche di vibrazione possono essere significativamente correlate al precarico della guida lineare, la diagnosi dei guasti di una guida lineare può essere condotta in modo efficace monitorando la variazione delle frequenze di vibrazione e delle caratteristiche acustiche dello stage in movimento.
Modelli di classificazione basati su un approccio di apprendimento automatico vengono ampiamente adottati nella diagnosi dei guasti dei meccanismi rotanti con cuscinetti a sfera. Per i meccanismi con cuscinetti lineari, invece, i corpi volventi sono soggetti a molteplici tipologie di guasti potenziali. I loro modi di vibrare sono generalmente complessi per via delle caratteristiche non lineari intrinseche che interagiscono con il precarico, per le condizioni di lubrificazione e per le forzanti esterne. Considerando l’influenza del precarico di una guida lineare sulle caratteristiche dinamiche di un sistema di posizionamento lineare, quantificare la variazione del precarico e del degrado delle caratteristiche meccaniche è un obiettivo fondamentale per garantire le prestazioni del sistema. A tal fine, una rete neurale basata sull’apprendimento automatico può risultare un approccio appropriato per lo sviluppo di un sistema di monitoraggio volto a quantificare il degrado dei cuscinetti lineari.
Caratteristiche generali di un sistema di movimento lineare
Sistemi di guida lineare (o sistemi di movimento lineare) vengono utilizzati in applicazioni di precisione per movimentare o posizionare oggetti lungo una direzione rettilinea.
L’elemento di trazione può essere un componente motorizzato che converte la coppia da un motore in una spinta lineare, come una vite a sfere o una cinghia, oppure potrebbe essere idraulico, pneumatico o un motore lineare. I singoli componenti vengono combinati nella progettazione del meccanismo per raggiungere i requisiti di precisione, velocità e carico per l’applicazione. Meccanismi di questo tipo sono sviluppati soprattutto per essere installati su macchine utensili e macchine industriali.
Sul mercato sono disponibili numerose varianti di guide lineari, in grado di adattarsi alle diverse applicazioni. In generale possono essere classificate in diverse categorie in relazione alla distribuzione dei carichi e al tipo di carico supportato; altre categorie si basano poi sulla forma o altre caratteristiche specifiche.
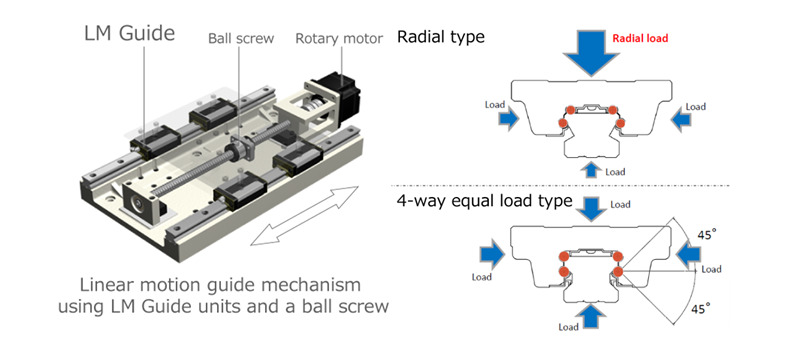
Gli elementi costitutivi di un sistema lineare sono:
- un supporto strutturale,
- un sistema di trazione,
- un elemento di guida,
- le tenute e la lubrificazione,
- altri accessori.
Il componente principale del sistema di supporto strutturale è tipicamente una estrusione di alluminio con lunghezze che non superano i 10-12 metri. La superficie di montaggio della base può essere lavorata per applicazioni che richiedono un posizionamento accurato. Le basi utilizzate in applicazioni di trasporto sono ottimizzate per resistere alla flessione sotto carico e alla distorsione durante il processo di estrusione, consentendo al sistema di essere supportato solo alle estremità.
Le principali tipologie di guide sono:
- guide a sfere,
- guide a ruota,
- guide a scorrimento o prisma.
Le guide a sfere supportano carichi elevati (fino a 40.000 N e oltre), possiedono basso attrito e un’alta rigidezza. Le guide a sfere sono disponibili sia in configurazioni a singolo che a doppio binario. Gli svantaggi delle guide a sfere includono un costo relativamente elevato e livelli di rumore elevati. Un vantaggio chiave delle guide a ruota è la loro capacità di operare a velocità eccezionalmente elevate, fino a 10 metri al secondo (m/s). Le guide a ruota offrono anche un attrito ridotto e una rigidezza molto elevata. D’altra parte, le guide a ruota hanno una resistenza relativamente bassa ai carichi d’urto. Le guide a scorrimento, invece, utilizzano boccole in polimero a forma di prisma che scorrono direttamente sulla superficie del profilo per garantire un funzionamento molto silenzioso e resistere a carichi d’urto elevati. Un vantaggio chiave delle guide a scorrimento è la loro capacità di operare in ambienti contaminati. Le guide a scorrimento si caratterizzano, inoltre, una capacità di carico e velocità inferiori rispetto alle guide a sfere o a ruota. Le soluzioni costruttive più comuni sono i sistemi a vite a ricircolo di sfere, i sistemi a vite senza fine e i sistemi a cinghia. Un sistema a vite a ricircolo di sfere è composto da una vite a sfere e una madrevite con cuscinetti. Le viti a sfere rettificate e pre-caricate forniscono un’elevata precisione di posizionamento. Il carico sulla vite a sfere è distribuito su un gran numero di cuscinetti a sfere in modo che ciascuna sfera sia soggetta ad un carico relativamente basso. Il risultato è una precisione assoluta (fino a 0.005 mm), una capacità di spinta elevata (fino a 40 kN) e una rigidezza anch’essa elevata. La precisione assoluta è definita come l’errore massimo tra la posizione prevista e quella effettiva.
I sistemi a vite a sfere forniscono tipicamente un’efficienza meccanica del 90%, quindi il loro costo più elevato è spesso compensato da un minor consumo energetico. La velocità critica di una vite a sfere è determinata dal diametro alla radice della vite, dalla lunghezza non supportata e dalla configurazione del supporto. I supporti a vite a sfere consentono l’uso di unità azionate a vite fino a 12 metri di corsa e una velocità di ingresso pari a 3.000 giri/min.
I sistemi a vite senza fine non possono eguagliare la precisione assoluta di posizionamento dei sistemi a vite a sfere, ma offrono un’eccellente ripetibilità. La ripetibilità è definita come la capacità di un sistema di posizionamento di tornare a una posizione durante il funzionamento quando si avvicina dalla stessa direzione alla stessa velocità e con lo stesso tasso di decelerazione. I sistemi a vite senza fine sono utilizzati in applicazioni di posizionamento con cicli di lavoro bassi o medi e operano a livelli di rumore ridotti. I sistemi a cinghia sono utilizzati in applicazioni di trasporto ad alta velocità e alta produttività con velocità fino a 10 m/s ed accelerazioni fino a 40 m/s2.
Criteri per il dimensionamento
Le guide lineari subiscono un movimento reciproco invece di un movimento rotatorio come avviene invece nei cuscinetti, il che comporta accelerazioni molto più elevate rispetto a quelle tipicamente sperimentate appunto nei cuscinetti rotativi. Poiché le guide lineari sono diventate importanti principalmente grazie alla automazione robotica, spesso è necessario fare riferimento alla letteratura del produttore per le formule carico/durata.
Si riporta qui un metodo generale per il calcolo della durata di una guida a slitta lineare. Il simbolo L viene utilizzato per rappresentare la durata nominale. Essa è definita come la lunghezza di percorrenza sopportata dalla guida in condizioni specifiche. In realtà, la durata della guida varia da una guida all’altra, quindi nell’industria si fa spesso riferimento ad una valutazione chiamata L10. La valutazione L10 è definita come la lunghezza di percorrenza che il 90% di tutte le guide (dello stesso modello) completeranno prima della comparsa del primo segnale di guasto. I seguenti fattori vengono utilizzati nel calcolo delle previsioni carico/durata.
Fattore di velocità
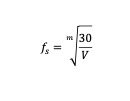
in cui V rappresenta la velocità del moto relativo tra la slitta e la guida, m è uguale a 3 per le guide a sfere e 3.3 per le guide a rulli. Quando la velocità è inferiore a 12 mm/s, fs è uguale a 1.
Fattore di temperatura
Temperature eccessive possono ridurre la durezza dei componenti a contatto che sopportano il carico ed abbassare la durata della guida a causa di usura e fatica. Definiamo il fattore di temperatura come ft, i cui valori sono riportati nella tabella 1. Si noti che i valori riportati non sono validi per sfere in polimero.
Temperatura (F) | Fattore di Temperatura “ft” con corpi a contatto in acciaio al carbonio temprato | Fattore di Temperatura “ft” con corpi a contatto in acciaio inossidabile |
220 | 1 | 1 |
300 | 0.9 | 1 |
400 | 0.75 | 0.9 |
500 | non consigliato | 0.75 |
Fattore per il tipo di carico
Il carico sopportato da una guida lineare è una combinazione di forze variabili, vibrazioni, impatti, carichi occasionali, etc. Utilizziamo il fattore per il tipo di carico fw per tener conto di queste forze variabili. I valori di fw sono riportati nella tabella 2.
Condizione di carico | Valore di fw |
Movimento regolare senza urti | da 1 a 1.5 |
Movimento con urti significativi | da 2 a 3 |
Utilizzando i fattori così definiti, il valore della durata L10 può essere calcolata come:
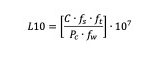
in cui L10 è la durata di vita della guida al 90% di affidabilità (come definita in precedenza), C è la capacità di carico nominale della slitta fornita nei dati di targa del componente, Pc il carico effettivo agente sulla guida.
Monitoraggio predittivo basato su reti neurali
Come detto, uno dei sistemi per il condition monitoring di componenti come le guide lineari, consiste nell’analisi delle caratteristiche dinamiche vibrazionali. Consideriamo per esempio, uno stage mobile movimentato da una guida lineare. Al fine di stabilire la correlazione tra la vibrazione dello stage in movimento e lo stato di precarico della sua guida lineare è possibile utilizzare un algoritmo basato su rete neurale. Lo stesso strumento consentirà inoltre di sviluppare un modello previsionale in grado di identificare lo stato di precarico della guida lineare, oppure di predirne il cedimento.
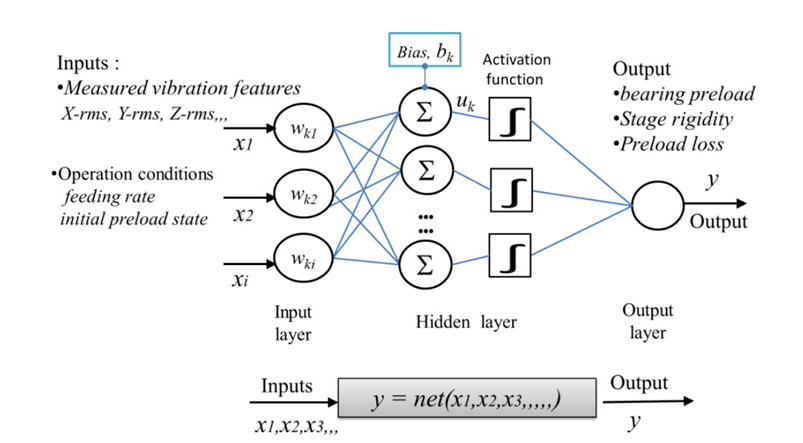
In particolare, nella modellazione ANN (Artificial Neural Network), i dati in ingresso sono raccolti a partire da alcuni test dinamici nei quali lo stage viene movimentato appositamente. In questi test, le condizioni di esercizio prevedono condizioni di precarico variabili fra basse, medie e alte. I dati misurati vengono poi suddivisi in tre gruppi corrispondenti; di questi dati, una certa percentuale (intorno al 60%-80%) viene selezionata in modo casuale per l’addestramento della rete neurale. Dei dati restanti, la metà verrà utilizzata per testare i responsi dell’algoritmo e l’altra metà per una convalida finale degli stessi risultati. Un esempio dell’architettura di un algoritmo a rete neurale come quello descritto è rappresentato in figura 2.
Applicazioni del modello di rete neurale
Consideriamo un caso applicativo del precedente algoritmo per comprenderne il funzionamento. La rete ha in questo caso lo scopo di predire il precarico applicato alle guide lineari di una macchina utensile. Il modello predittivo del precarico può essere illustrato schematicamente, considerando la fresatrice a tre assi dotata di quattro guide lineari ad elevato precarico (Z2).
Gli scenari di perdita del precarico delle guide lineari nelle guide lineari di avanzamento a tre assi possono essere identificati come segue:
- Scenario 1. In questo caso si prevede una condizione normale di precarico per la guida lineare dell’asse corrispondente della fresatrice. I modelli ANN stimano un valore di rigidezza, privo di deterioramento nelle condizioni operative applicate sulla macchina.
- Scenario 2. Sulla base delle caratteristiche di vibrazione rilevate, è previsto un moderato deterioramento del precarico della guida lineare dell’asse della fresatrice. L’algoritmo, conoscendo il valore iniziare del precarico (ad esempio “livello medio”), ne calcola la riduzione percentuale del suo valore.
- Scenario 3. Anche in questo caso si prevede una degradazione del precarico della guida lineare sulla base delle caratteristiche di vibrazione misurate. La perdita di precarico è più elevata e viene quindi segnalata in modo più evidente, con un segnale di pericolo. Si tratta di una perdita di precarico causata, ad esempio, da un degrado da usura superficiale dei corpi volventi o delle sedi della guida lineare. In questi casi, la diminuzione dell’interferenza all’interfaccia di rotolamento provoca un brusco calo del precarico.
Quanto descritto per un potenziale algoritmo predittivo basato su intelligenza artificiale e rete neurale può essere riassunto dallo schema di figura 3.
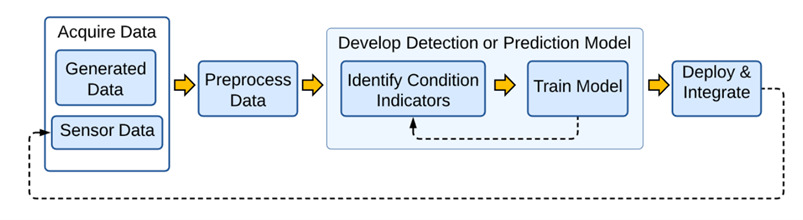
[Fonte: Shih, W.-C et al.]
L’utente può interpretare facilmente la previsione del precarico, che rappresenta lo stato di salute della guida lineare nel sistema. L’indicatore, a seconda della colorazione assunta, mostra all’utente un avviso o un messaggio che indica se la guida lineare deve essere sostituita (figura 4).
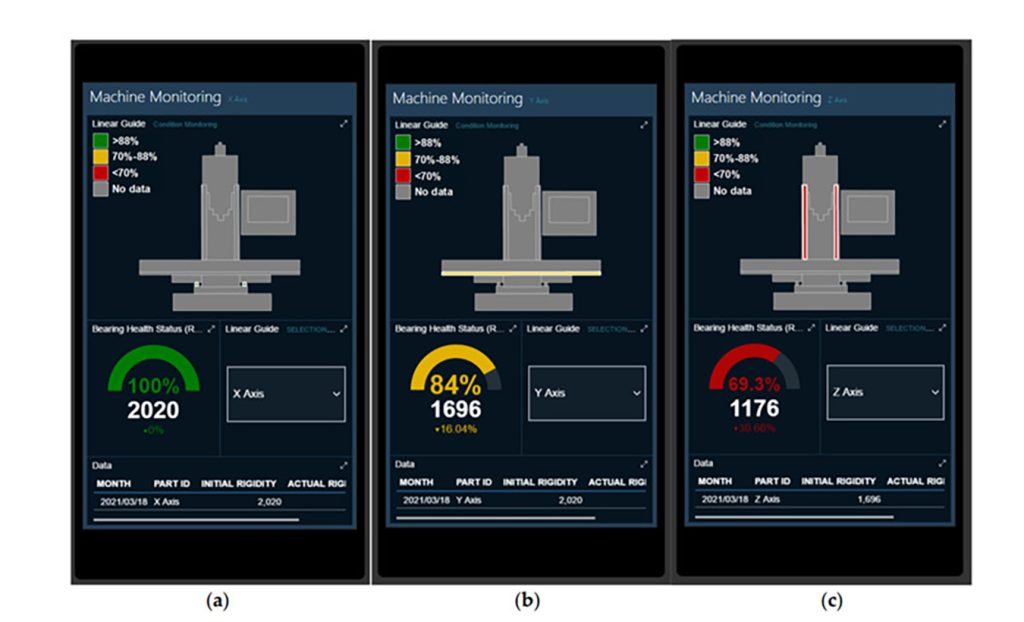
Attualmente sistemi di condition monitoring di questo tipo sono ancora in fase di sviluppo. Il lavoro futuro in questo campo prevede l’integrazione del concetto di monitoraggio online al fine di ottenere valori di previsione in tempo reale, aggiornati e visualizzati costantemente. Un flusso di lavoro completamente automatizzato, consentirebbe poi all’utente di ottenere informazioni qualitativamente migliori circa la rigidezza effettiva o lo stato di salute di una guida lineare.
Giorgio De Pasquale, Dipartimento di Ingegneria Meccanica e Aerospaziale, Politecnico di Torino, Smart Structures and Systems Lab
Elena Perotti, Senior data analyst