ISO/TS 6336-22 (Calcolo della capacità di carico di ingranaggi cilindrici a denti dritti ed elicoidali – Parte 22: Calcolo della resistenza al micropitting) è la specifica tecnica ISO contenente una proposta per il calcolo del rischio di micropitting negli ingranaggi (Prima parte)
ISO/TS 6336-22 (Calcolo della capacità di carico di ingranaggi cilindrici a denti dritti ed elicoidali – Parte 22: Calcolo della resistenza al micropitting) è la specifica tecnica ISO contenente una proposta per il calcolo del rischio di micropitting negli ingranaggi [1]. ISO/TS 6336-22 calcola un fattore di sicurezza contro il micropitting confrontando lo spessore minimo specifico del film lubrificante con uno spessore ammissibile. Sfortunatamente, ISO/TS 6336-22 non raccomanda un fattore di sicurezza minimo, ma lascia all’ingegnere confrontare i risultati calcolati con dati sperimentali.
L’approccio è stato pubblicato dal 2010 e la designazione di “specifica tecnica” del documento significa che contiene calcoli che sono ancora soggetti a ulteriori revisioni ed miglioramenti. La prossima revisione sistematica del documento richiederà che esso venga convertito in uno standard internazionale o ritirato. Per questo motivo, è importante verificare che i calcoli secondo ISO/TS 6336-22 siano in grado di prevedere in modo affidabile il rischio di micropitting.
Come è tipico di tutti gli standard di calcolo per ingranaggi, nella ISO/TS 6336-22 sono presentati due diversi metodi. Il primo, il metodo A, consente all’ingegnere di calcolare gli spessori del film lubrificante utilizzando un approccio di calcolo che modelli l’intera area di contatto dell’ingranamento (ndr. e.g. mediante analisi numeriche). Al contrario, il metodo B inizia proponendo un metodo.
Supponiamo che il micropitting inizi nella regione di scorrimento negativo e si valuti lo spessore del film in punti specifici lungo la linea d’azione. ISO/TS 6336-22 raccomanda che entrambi i metodi siano validati rispetto all’esperienza mediante valutazione dei risultati su set di ingranaggi in condizioni applicative simili.
Uno studio precedente, “Case Study of ISO/TS 6336-22 Micropitting Calculation” [2], valuta tre casi utilizzando il Metodo B. Il primo esempio è il set di ingranaggi per un compressore, il secondo è un set di ingranaggi per turbine eoliche e l’ultimo è il set di ingranaggi per test tribologici condotti dall’American Gear Manufacturers Association (AGMA). Questi esempi coprono una gamma di dimensioni di ingranaggi e condizioni di applicazione abbastanza ampia. Tutti i set di ingranaggi, in esercizio, hanno manifestato micropitting, e forniscono quindi buoni esempi per la verifica dei risultati del calcolo. Utilizzando il metodo B, però, solo gli ingranaggi del test tribologico AGMA hanno prodotto fattori di sicurezza in linea con le aspettative.
I risultati di tutti e tre i casi sono stati esaminati assieme ai membri del gruppo di lavoro ISO 6, gruppo che ha svolto un ruolo centrale nello sviluppo della ISO/TS 6336-22. Tutte le persone coinvolte hanno espresso preoccupazione riguardo al possibile utilizzo del metodo B soprattutto per condizioni applicative come quelle dei casi 1 e 2. Avendo una velocità tangenziale superiore a 80 m/s, il Caso 1 richiede necessariamente l’uso del Metodo A secondo ISO/TS 6336-22. Per il caso 2, invece, trattandosi di una applicazione per impiego eolico, lo standard di riferimento è ISO/IEC 61400-4. In questo caso la normativa richiede l’uso del metodo A per il calcolo dello spessore minimo specifico del film. Nel caso del caso B, si hanno anche indicazioni specifiche sulle temperature di esercizio, in quanto è noto come gli ingranaggi delle turbine eoliche possano funzionare a temperature più elevate di quelle tipiche delle applicazioni ingranaggistiche industriali.
Di conseguenza, le condizioni operative e i parametri di calcolo per tutti e tre i casi sono stati ulteriormente studiati e questo articolo riporta sia i risultati dell’articolo precedente (aggiornati) sia quelli nuovi relativi allo studio delle stesse configurazioni mediante il Metodo A. I risultati dei due approcci sono stati confrontati sia tra loro, sia con risultati sperimentali in modo da determinare se ISO/TS 6336-22 Metodo A sia effettivamente un approccio affidabile per la verifica a micropitting.
Descrizione di ISO/TS 6336-22
Il documento precedente conteneva già una descrizione dettagliata degli approcci disponibili in ISO/TS 6336-22. In estrema sintesi, nella norma ISO/TS 6336-22 vengono presentati due diversi metodi per il calcolo dello spessore specifico minimo del film lubrificante e dello spessore specifico ammissibile. Come altre normative ISO per ingranaggi, il metodo A prevede l’utilizzo di test o calcoli dettagliati per determinare i parametri critici. Il metodo B è un metodo analitico semplificato e questo è quello utilizzato nell’articolo precedente. Indipendentemente dal metodo scelto, noti lo spessore specifico minimo del film e lo spessore specifico ammissibile è possibile determinare il fattore di sicurezza.
Metodo B
I calcoli secondo il metodo B sono stati eseguiti utilizzando un foglio di lavoro Mathcad in modo da implementare le equazioni presenti in ISO/TS 6336-22.
Spessore specifico minimo del film
Un calcolo dello spessore specifico minimo del film utilizzando il metodo B inizia con la stima dello spessore mediante un’analisi secondo Dowson/Higginson lungo tutta la linea d’azione. Questo valore viene modificato mediante un fattore di scorrimento locale che tiene conto aree a scorrimento negativo. Per calcolare il fattore di sicurezza viene utilizzato il minimo degli spessori specifici del film calcolati lungo la linea d’azione.
Spessore specifico del film ammissibile
Lo spessore specifico ammissibile viene determinato conducendo test standardizzati con ingranaggi simili per geometria, qualità e materiale agli ingranaggi analizzati. L’ingranaggio viene fatto funzionare fino al raggiungimento del limite a micropitting. Lo spessore specifico critico del film per gli ingranaggi di prova viene calcolato secondo ISO/TS 6336-22 utilizzando i dati di carico della fase di rottura. Questo viene preso come lo spessore specifico del film consentito. Se non è possibile eseguire il test con ingranaggi reali, è possibile utilizzare lo stadio di carico che porta a cedimento il lubrificante in test standardizzati, come FVA 54 [3], e calcolare lo spessore minimo specifico del film utilizzando i parametri dell’ingranaggio analizzato.
Metodo A
Spessore specifico minimo del film
Per determinare lo spessore minimo specifico del film lubrificante utilizzando il metodo A, il progettista deve calcolare il valore mediante un programma di calcolo capace di modellare l’intera area di contatto dell’ingranamento. In questa analisi vengono considerate la distribuzione del carico, le velocità di strisciamento e le condizioni di esercizio reali. I risultati appaiono come mappe di pressione e spessore del film sui fianchi del pignone e della ruota. Questi vengono utilizzati per calcolare lo spessore specifico del film lubrificante in ogni punto all’interno della zona di contatto. È importante notare come si utilizzi sempre il valore minimo per il calcolo del fattore di sicurezza contro il micropitting.
Spessore specifico del film ammissibile
Lo spessore specifico ammissibile viene determinato attraverso test su ingranaggi reali in condizioni simili all’applicazione interrotti solo quando il micropitting si manifesta. I carichi di prova e il programma di calcolo vengono quindi utilizzati per determinare lo spessore del film. Questi test possono essere eseguiti anche per ingranaggi e condizioni di servizio molto simili al set di ingranaggi di interesse. Tuttavia, test di questo tipo possono essere troppo costosi e potrebbero non essere sempre pratici se le applicazioni richiedono carichi elevati, basse velocità, e condizioni operative variabili, specialmente nel caso di piccoli lotti o applicazioni non considerate critico. In tal caso, sono disponibili metodi alternativi per approssimare lo spessore specifico del film ammissibile sulla base dei dati raccolti su ingranaggi di riferimento e test sui lubrificanti. Tuttavia, ogni approssimazione riduce l’accuratezza del fattore di sicurezza ottenibile.
Come raccomandato nella norma ISO/TS 6336-22, è importante interpretare il fattore di sicurezza a micropitting confrontandolo con le prestazioni di ingranaggi simili utilizzati sul campo in condizioni operative anch’esse simili a quelle in esame.
Applicazione del metodo A
Come si può vedere nei punti precedenti, il Metodo A richiede, per il calcolo dello spessore specifico ammissibile, che gli ingranaggi reali siano testati fino a quando non insorga micropitting. Nei casi 1 e 2, per la natura dell’applicazione, le dimensioni e le condizioni di carico, ciò non è stato possibile. I calcoli sono stati quindi eseguiti utilizzando il metodo A solo per lo spessore specifico minimo del film mentre per determinare il valore ammissibile (al denominatore del calcolo del fattore di sicurezza) si è impiegato il metodo B.
Programma di calcolo degli ingranaggi Metodo A – WindowsLDP
Esistono diversi programmi di calcolo per ingranaggi in grado di determinare le sollecitazioni hertziane nella zona di contatto tra ingranaggi. In questo documento, per determinare le sollecitazioni, viene utilizzato il programma WindowsLDP (Load Distribution Program) dell’Ohio State University®. Il resto dei fattori segue i metodi della ISO/TS 6336-22.
WindowsLDP è uno strumento di progettazione e analisi quasi statica di ingranaggi che permette di studiare coppie di ingranaggi cilindrici ed elicoidali, esterni e interni. Impiega formulazioni semi-analitiche efficienti e accurate dal punto di vista computazionale per calcolare la distribuzione del carico tra più denti a contatto.
La distribuzione della pressione di contatto viene calcolata utilizzando un modello di contatto basato su una coppia di ingranaggi ad assi paralleli [4]. Questo modello combina:
– L’analisi del contatto tra fianchi (senza carico) proposta da Singh e Houser [5],
– Fonti di deformazione, tra cui la flessione e taglio [6],
– Rotazione della base del dente [7] e deformazione del contatto [8],
– Un vettore di separazione iniziale che include eventuali deviazioni delle superfici dai profili nominali ad evolvente (cioè modifiche della microgeometria).
La distribuzione del carico viene calcolata implementando l’algoritmo modificato proposto da Conry e Seireg [9]. WindowsLDP è stato ampliamente validato con test durante il suo sviluppo.
Utilizzando la distribuzione del carico prevista, WindowsLDP calcola l’errore di trasmissione sotto carico, le distribuzioni di pressione nel contatto e le sollecitazioni al piede, la rigidezza dell’ingranamento e le forze agenti sui denti. È inoltre possibile calcolare altri parametri di progetto, come lo spessore del film lubrificante e la temperatura delle superfici. Le modifiche di profilo possono essere inserite in modo interattivo o possono essere lette da dati misurati relativi alle superficie reali dei fianchi. I risultati sono presentati attraverso un’interfaccia grafica interattiva che offre all’utente la possibilità di elaborarli e presentarli in vari formati.
Casi di studio con il metodo A
Sono stati selezionati i casi studio operativi che hanno subito micropitting proprio per esercitare il documento ISO/TR 6336-22. Poiché c’era preoccupazione per l’influenza che operazioni operative e la manutenzione potesse avere sul micropitting, gli autori hanno valutato i risultati deii test di lubrificazione, i livelli di carico e le condizioni operative in modo molto minuzioso, in particolare per i casi 1 e 2. I dettagli dei calcoli di questi casi di studio sono piuttosto lunghi e non vengono inclusi nel presente articolo. Anche i disegni e i dettagli delle modifiche al profilo non possono essere riportati in quanto proprietari. Gli autori possono fornire dettagli specifici su richiesta.
Caso 1: set di ingranaggi per compressori ad alta velocità
Il caso 1 è rappresentato da un set di ingranaggi ad alta velocità che aziona un compressore centrifugo. Questo set ha un micropitting sul pignone, iniziato nella zona di dedendum ed estesosi poi fino all’addendum. Il micropitting è localizzato principalmente dal lato in cui il pignone è connesso al motore (lungo la larghezza di fascia). Per esperienza, questo risultato è prevedibile a causa di un aumento della temperatura di contatto del dente quando il carico viene trasmesso dal rotismo elicoidale.
Questo riduttore ha funzionato per circa 120.000 ore o 54,6×109 cicli. Il riduttore non è stato posizionato vicino a un’area salata, elevata umidità o soggetto a significative fluttuazioni climatiche di temperatura. Ha funzionato ininterrottamente per intervalli di tempo da 4 a 5 anni con carico e velocità costanti in una stanza controllata dal punto di vista ambientale. Questo funzionamento continuo impediva l’assorbimento di acqua nel lubrificante. Ogni 4 o 5 anni di funzionamento continuo, il riduttore veniva fermato, ispezionato e sottoposto a manutenzione ordinaria. Per i primi 13,5 anni di funzionamento non si è rilevato il micropitting. A questo punto però si è reso necessario sostituire il set di ingranaggi. Prima di questo drastico intervento, non era stata necessaria alcuna manutenzione significativa.
Un’immagine del danneggiamento per micropitting è riportata nella figura 1. A parte il micropitting, il resto della superficie del dente dell’ingranaggio è risultato in ottime condizioni e non ci sono indicazioni pitting o scuffing.
La geometria, i carichi e il lubrificante per questo caso sono riassunti nella tabella 1. I denti dell’ingranaggio hanno modifiche adeguate ai carichi operativi.
Dimensione | Unità | Pignone | Ingranaggio | |
Numero di denti | – | 37 | 163 | |
Rapporto | – | 4.405 | ||
Interasse | mm | 600 | ||
Modulo normale | mm | 5.90 | ||
Larghezza di fascia | mm | 280 | ||
Diametro esterno | mm | 236.30 | 987.29 | |
Angolo di pressione | degrees | 20.00 | ||
Angolo dell’elica | degrees | 10.00 | ||
Modifica dell’addendum | – | 0.2407 | -0.0876 | |
Rugosità superficiale | mm | 0.41 | 0.40 | |
Grado di precisione ISO | – | 4 | 4 | |
Durezza superficiale | HRC | 58-64 | 58-64 | |
Velocità pignone | rpm | 7,582.0 | ||
Coppia pignone | Nm | 12,209.3 | ||
Prodotto KA Kv KHa KHb | – | 1.4170 | ||
Lubrificante | – | Mobil Teresstic AC ISO VG 32 | ||
Temperatura lubrificante in ingresso (stimata) | °C | 54 | ||
Temperatura apparente (per i calcoli) | °C | 82.93/100 |
Condizioni del lubrificante
Il lubrificante utilizzato in questa trasmissione a ingranaggi era un Mobil Teresstic AC 32. Questo è un olio antiruggine e anti-ossidazione ISO VG 32. Nei riduttori per compressori è tipico impiegare lubrificanti leggeri come questo ed esiste una lunga storia di utilizzo di successo.
Dopo aver rilevato il micropitting, un campione di questo lubrificante è stato analizzato in termini di composizione utilizzando la ferrografia e confrontandolo con un campione di lubrificante “nuovo”. Dalle analisi è emerso che:
– non vi sia nessun deterioramento significativo della composizione chimica del lubrificante,
– non vi sia nessun contenuto d’acqua significativo,
– si è osservato un miglioramento del contenuto di particelle rispetto al campione “nuovo”, il che indica un’eccellente filtrazione.
Per quanto riguarda i risultati dell’analisi ferrografica del lubrificante “usata” (figura 2), si osserva come tutti i dati indichino condizioni operative accettabili.
Questo caso è interessante perché il micropitting è stato osservato sporadicamente in riduttori di questo tipo e che operano a velocità tangenziali tra 73 m/s e 175 m/s. Nella maggior parte dei casi, il micropitting è stato osservato solo dopo molti anni di funzionamento. Questo set di ingranaggi è stato ispezionato a intervalli di 4-5 anni circa; quindi non è certo quando di preciso il fenomeno abbia cominciato a manifestarsi.
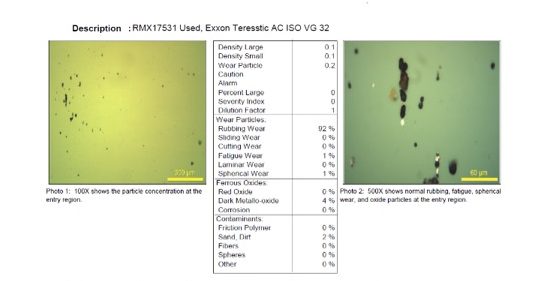
I riduttori sono installati all’interno di un edificio riscaldato. Hanno operato a carichi costanti ed in funzionamento continuo. Il produttore ha esaminato la storia della temperatura e del carico e condotto analisi dell’olio per tutte le unità che hanno manifestato micro-pitting. Non ci sono prove di temperature eccessive, lubrificante contaminato o contatto non uniforme tra i denti.
È interessante notare come il test di Martinaglia [10] dimostri come la zona a temperatura più elevata si trovi spostata verso una estremità. Questo risultato corrisponde all’offser dell’area interessata da micropitting osservata su questo set di ingranaggi. È quindi possibile concludere come l’aumento di temperatura abbia contribuito all’insorgenza del micropitting.
In sintesi, il sistema di lubrificazione e lubrificazione per il caso 1 ha lavorato a dovere durante tutto il funzionamento del sistema. Tutti i dati associati alle condizioni del lubrificante di questo caso sono disponibili su richiesta.
Metodi di calcolo per la temperatura apparente e gli spessori del film
Le formule della ISO/TS 6336-22 sono state validate con ingranaggi aventi velocità tangenziali tra 8 m/s e 60 m/s. Il caso 1 ha però una velocità tipica pari a 88 m/s. Nell’articolo precedente, i calcoli secondo il Metodo B sono arrivati a prevedere uno spessore minimo specifico del film di 2 micron. Durante la revisione di questo esempio con i membri del Gruppo di lavoro ISO 6, è stato sottolineato come l’equazione per la temperatura di massa, θM, non sia applicabile per velocità superiori a 80 m/s a causa della significativa generazione di calore per attrito. Per i calcoli a velocità superiori a 80 m/s si consiglia dunque l’utilizzo del Metodo A.
Un calcolo approfondito utilizzando il metodo A permetterebbe di modellare sia la pressione di contatto, sia la temperatura del fianco. Sfortunatamente, WindowsLDP non calcola l’attrito o la generazione di calore all’interno dell’ingranamento e la creazione di un modello per farlo va oltre il timeframe per questo documento.
Per questo motivo, per valutare la temperatura di massa per gli ingranaggi ad alta velocità, ci se è riferiti al lavoro di Amendola [11] sullo scuffing. Questo lavoro si basa su test condotti da Akazawa [12] e Martinaglia [10]. Il risultato è un’equazione per la temperatura apparente che dipende dalla velocità tangenziale ed è valida per valori superiori a 35 m/s. Questa equazione è stata incorporata in AGMA 925-B22 [13]. Utilizzando questa equazione dell’AGMA 925, è risultata una temperatura di massa di 82,93°C, valore poi utilizzato nei calcoli secondo il Metodo A.
Il precedente lavoro di Amendola [14] ha cercato di correlare i risultati relativi ad ingranaggi MAAG alle normative AGMA 925-A03 [15] e AGMA 6011-J14 [16] utilizzando 100°C per la temperatura di massa. Pertanto, al fine di osservare la variazione dello spessore del film previsto in funzione della temperatura, è stata svolta una seconda serie di calcoli (Metodo A) a 100°C.
Per ingranaggi FVA 54, lo spessore specifico del film ammissibile per il lubrificante Mobil Teresstic AC 32 è anche stato calcolato utilizzando il metodo B. Sfortunatamente, non è stato possibile trovare alcun test di micropitting FVA 54 per questo lubrificante. Tuttavia, il produttore ha riferito che in passato è stato testato un lubrificante simile (Mobil DTE Light, VG 32) ed i test sono stati condotti fino alla fase di carico 8. Entrambi questi lubrificanti si sono dimostrati sufficientemente performanti in applicazioni simili. Pertanto, è stato utilizzato lo stadio di carico 8 che ha portato a cedimento gli ingranaggi FVA 54 ad una temperatura di prova di 600°C.
Risultati del metodo A
I risultati ottenuti con il metodo A sono riportati nella tabella 2.
Metodo qM | ||||
Nome | Simbolo | Unità | PLV secondo Amendola | Appross. MAAG |
Temperatura apparente | qM | °C | 82.93 | 100.00 |
Spessore specifico minimo | λGFmin | – | 1.574 | 1.149 |
Spessore specifico ammissibile | λGFP | – | 0.127 | 0.127 |
Fattore di sicurezza | Sλ | – | 12.39 | 9.04 |
La distribuzione della pressione e lo spessore specifico del film nella zona di contatto possono essere visti in figura 3. La zona di massima pressione e di spessore minimo del film si trova nel dedendum del pignone, che corrisponde alla posizione in cui si è osservato il micropitting. La variazione della temperatura apparente sulla del pignone non può essere modellata da WindowsLDP, quindi non prevede che il micropitting sarà predominante da una parte della faccia.
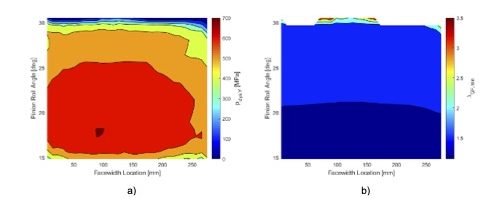
Risultati aggiornati del metodo B
Nella tabella 3, sono riportati i dati relativi al caso 1 ricalcolati utilizzando il metodo B per lo spessore specifico minimo del film e temperature apparenti di 82,93°C e 100°C. Questo nuovo calcolo è stato fatto al fine di avere un confronto più realistico con i risultati di WindowsLDP.
Metodo qM | |||||
Nome | Simbolo | Unità | ISO/TS 6336-22 B | PLV secondo Amendola | Appross. MAAG |
Temperatura apparente | qM | °C | 60.00 | 82.93 | 100.00 |
Spessore specifico minimo | λGFmin | – | 2.12 | 1.29 | 0.95 |
Spessore specifico ammissibile | λGFP | – | 0.157 | 0.127 | 0.127 |
Fattore di sicurezza | Sλ | – | 13.48 | 10.18 | 7.50 |
I fattori di sicurezza
I fattori di sicurezza che emergono dai calcoli, sia che si utilizzi il metodo A, sia che si utilizzi il metodo B, risultano molto elevati. Ciò si verifica quando lo spessore specifico del film è molto maggiore dello spessore specifico ammissibile. Tuttavia, ci sono due aspetti da considerare:
– Lo spessore specifico minimo del film dipende fortemente dalla temperatura apparente e va sottolineato come nell’ambito di questa ricerca non si avesse un programma in grado di calcolare con precisione questo valore. Inoltre, non è stato nemmeno possibile misurarlo durante l’effettivo funzionamento della trasmissione. Si è dunque ipotizzato valori abbastanza elevati per la temperatura apparente, ma un modello ottimale necessiterebbe dei valori misurati lungo tutto il contatto, richiedendo quindi test con ingranaggi reali in condizioni operative.
– Lo spessore specifico del film ammissibile si basa sulle prestazioni presunte di Teresstic con VG 32 nei test su geometrie FVA 54. Un valore più accurato potrebbe essere derivato da test standard con ingranaggi simili. Man mano che il valore ammissibile diventa meno accurato, i fattori di sicurezza calcolati con ISO/TS 6336-22 saranno anch’essi meno affidabili.
– Il set di ingranaggi considerato (Caso 1) ha funzionato per miliardi di cicli di carico prima che si notasse l’insorgenza di micropitting. In una vita così lunga, altre applicazioni possono essere soggette a carichi torsionali dinamici dovuti ai transitori di avviamento ed arresto che portano a riduzioni momentanee dello spessore del film. Questo set di ingranaggi è stato fatto funzionare a carichi uniformi ininterrottamente per diversi anni. Sulla base delle immagini dei denti dell’ingranaggio, dei dati operativi e delle osservazioni al microscopio, questo particolare riduttore sembra aver funzionato sempre in regime di lubrificazione elastoidrodinamica completa (EHL). Pertanto, una lambda maggiore di uno non è una buona base iniziale per prevedere il micropitting. Questo esempio suggerisce piuttosto come l’interazione tra asperità non sia un fattore determinante per il micropitting. Inoltre, sembrerebbe che il micropitting possa emergere a seguito delle pressioni hertziane cicliche anche in condizioni di lubrificazione EHD completa. Sembra siano necessari un numero sufficiente di cicli di carico. Lo sviluppo di un modello predittivo che incorpori questo meccanismo di formazione del micropitting è importante poiché le aspettative del ciclo di vita della trasmissione a ingranaggi continuano a crescere.
Caso 2: set di ingranaggi per turbine eoliche
Il caso 2 è rappresentato dal set di ingranaggi di una turbina eolica da 1,5 MW – il National Renewable Energy Laboratory (NREL) Flatirons Campus in Colorado. Questo esempio è rappresentativo di micropitting minore in ingranaggi di turbine eoliche che abbiano funzionato per almeno 5 anni. Il micropitting è stato riscontrato all’inizio del profilo attivo (SAP) di tutti i denti del solare. Sono stati osservati sia micropitting, sia alcune abrasioni (anche più in alto lungo i fianchi dei denti del pignone). Il set di ingranaggi era stato installato poco più di 8 anni orsono. Ha prodotto circa 6 milioni di kWh di energia in 14.170 ore di funzionamento, pari a circa l’8% della sua vita (minima) di progetto. Il micropitting è stato osservato a partire dal sesto anno di funzionamento, il che rappresenta un numero relativamente basso di cicli carico.
Le immagini del micropitting sono riportate nella figura 4. Nel framework di questa attività, sono stati esaminati tutti i registri di manutenzione. Inoltre, sono stati acquisiti e analizzati numerosi dati operativi dal sistema di controllo, supervisione e acquisizione della turbina. Il riferimento [18] è disponibile al pubblico e contiene la documentazione completa.
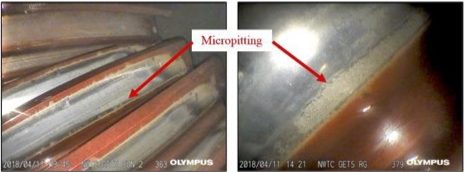
La geometria e il lubrificante per questo caso sono riassunti nella tabella 4. I denti dell’ingranaggio hanno modifiche adeguate al profilo e ai carichi operativi.
Dimensione | Unità | Pignone | Ingranaggio | |
Numero di denti | – | 27 | 88 | |
Rapporto | – | 3.2593 | ||
Interasse | mm | 487.51 | ||
Modulo normale | mm | 8.0609 | ||
Larghezza della faccia | mm | 200.9 | ||
Diametro esterno | mm | 247.955 | 759.079 | |
Angolo di pressione | gradi | 22.5 | ||
Angolo dell’elica | gradi | 17.584 | ||
Modifica dell’addendum | – | 0.0804 | 0.0804 | |
Rugosità superficiale | mm | 0.22 | 0.55 | |
Grado di precisione ISO | – | 6 | 6 | |
Durezza superficiale | HRC | 59-63 | 58-62 | |
Prodotto KA Kv KHa KHb | – | 1.478 | ||
Lubrificante | – | Castrol Optigear A320 | ||
Temperatura lubrificante in ingresso | °C | 50 e 70 (si vedano i dati misurati in figura 3) |
Dati SCADA e analisi dei lubrificanti
Nell’esaminare i risultati del Metodo B del documento precedente, sono state sollevate questioni riguardanti la temperatura di esercizio della trasmissione e le condizioni del lubrificante. Questa trasmissione a ingranaggi è stata monitorata durante l’intero funzionamento. Al fine di comprendere meglio l’influenza delle sue condizioni applicative sull’insorgenza di micropitting, sono stati esaminati tre diversi fattori:
- Temperature di esercizio. I dati erano disponibili per la temperatura del bagno d’olio per circa 7,5 anni degli 8 anni di funzionamento. Le temperature del bagno d’olio variavano da 20 °C a 66 °C, con la maggior parte delle misure compresa tra 40 °C e 60 °C, come mostrato nella figura 5 [16]. Misurazioni successive su un riduttore sostitutivo hanno mostrato come la temperatura della pista esterna del cuscinetto dell’albero ad alta velocità, una delle temperature di esercizio più elevate nel cambio, non superasse mai i 70°C [19]. Sulla base di questa evidenza, i calcoli per il pignone del solare sono stati eseguiti sia con una temperatura “normale” dell’olio di 50°C, sia considerando la condizione limite temperatura di 70°C.
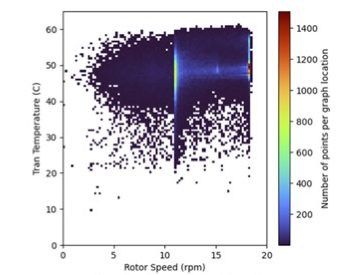
- Casi di carico. Le turbine eoliche funzionano in condizioni di carico variabili. Per calcolare il fattore di sicurezza a micropitting, nell’articolo precedente si considerava la condizione di carico medio. Al fine di ottenere una comprensione migliore dei carichi di funzionamento che influenzano l’ingranaggio, i dati di coppia e velocità sono stati estratti sia a intervalli di 1 secondo, sia con cadenza di 10 minuti [18]. La maggior parte del tempo la turbina era in modalità inattiva, in cui la velocità del rotore è compresa tra 0 e 1 giri/min ed il carico è nullo. Va però notato come si sia anche misurato un intervallo di tempo in cui la velocità del rotore risultava essere di 11 giri/min (velocità di inserimento) e carichi inferiori al 20% ed un intervallo in cui la velocità saliva a 18 giri/min (velocità nominale) con carichi compresi tra il 40% e poco più del 100%. Un’ulteriore serie di punti è stata acquisita a 13 giri/min e carichi relativamente bassi (sotto il 25%). Sulla base di ciò, si è deciso di eseguire i calcoli in questi tre casi di carico, riassunti nella tabella 5.
Unità | Originale | Vel. inserimento | Vel. media | Vel. nominale | |
Velocità del rotore | rpm | 18.3 | 10.91 | 12.73 | 18.3 |
Velocità del solare | rpm | 254.17 | 140.62 | 164.08 | 254.17 |
Copia solare | N-m | 20,880 | 3,840 | 4,080 | 20,880 |
3.Condizione dell’olio. Il rapporto NREL sulle condizioni della trasmissione a ingranaggi [17] menziona come sia stata trovati morchia nel filtro durante un’ispezione a fine 2017 – poco prima della sostituzione del riduttore. Per determinare se le condizioni dell’olio abbiano influenzato l’insorgenza del micropitting, in particolare per quanto riguarda il contenuto d’acqua, sono stati esaminati i registri di manutenzione della trasmissione. A parte un breve picco inspiegabile nel contenuto d’acqua registrato nel 2012, le condizioni del lubrificante sono sempre rimaste normali fino all’ispezione di fine 2017. La viscosità dell’olio, il numero di particelle e il contenuto d’acqua erano entro i parametri raccomandati [18]. Alla luce di ciò, si è concluso come il lubrificante fosse ben mantenuto, risultando in condizioni relativamente pulite e non abbia contribuito all’insorgenza del micropitting.
Per avere tutte le informazioni relative alla resistenza al micropitting del lubrificante è stato contattato direttamente il fornitore: Castrol Optigear A320 ha uno stadio di carico di cedimento secondo FVA 54 superiore a 10 a temperature di prova di 60°C e 90°C. Lo spessore specifico ammissibile del film per questo lubrificante è stato calcolato a una temperatura dell’olio di 60°C poiché a favore di sicurezza (calcolo più conservativo) e meglio rappresentativo dei dati operativi della turbina eolica.
Risultati del calcolo
Risultati del metodo A
I risultati ottenuti con il metodo A sono riportati nella tabella 6.
Caso di carico | ||||||||
Nome | Simbolo | Unità | Vel inseri. | Vel media | Vel. nominale | |||
Temperatura dell’olio | qoil | °C | 50 | 70 | 50 | 70 | 50 | 70 |
Temperatura apparente | qM | °C | 50.00 | 70.00 | 50.00 | 70.00 | 50.00 | 70.00 |
Spessore spec. minimo | λGFmin | – | 1.742 | 0.921 | 1.829 | 0.964 | 1.516 | 0.769 |
Spessore spec. ammissibile | λGFP | – | 0.338 | 0.338 | 0.338 | 0.338 | 0.338 | 0.338 |
Fattore di sicurezza | Sλ | – | 5.16 | 2.73 | 5.41 | 2.85 | 4.48 | 2.28 |
Alla velocità e al carico nominali e a una temperatura dell’olio di 70°C, la distribuzione della pressione e lo spessore specifico del film nella zona di contatto possono essere visualizzati nella figura 6. La micro-geometria del dente può essere capita guardando la distribuzione della pressione. Le zone di bassa pressione si trovano al piede e in testa al fianco del pignone. La regione di spessore minore del film si trova nel dedendum del pignone tra il raccordo di piede e il diametro primitivo.
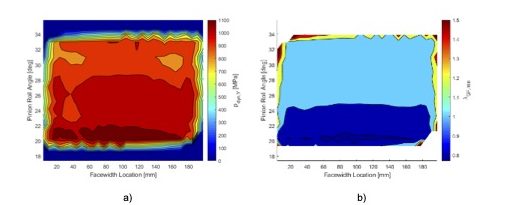
Risultati aggiornati del metodo B
A titolo di confronto, sono stati eseguiti anche i calcoli mediante Metodo B utilizzando i casi di carico e le temperature aggiuntivi. I risultati sono riportati nella tabella 7.
Caso di carico | ||||||||
Nome | Simbolo | Unità | Vel inseri. | Vel media | Vel. nominale | |||
Temperatura dell’olio | qoil | °C | 50 | 70 | 50 | 70 | 50 | 70 |
Temperatura apparente | qM | °C | 50.31 | 70.32 | 50.35 | 70.37 | 51.70 | 71.75 |
Spessore spec. minimo | λGFmin | – | 1.283 | 0.669 | 1.412 | 0.738 | 1.287 | 0.695 |
Spessore spec. ammissibile | λGFP | – | 0.338 | 0.338 | 0.338 | 0.338 | 0.338 | 0.338 |
Fattore di sicurezza | Sλ | – | 3.80 | 1.98 | 4.178 | 2.18 | 3.81 | 2.06 |
I fattori di sicurezza
La condizione di carico massima per questo set di ingranaggi è alla velocità nominale. Questo è anche il caso di carico in cui si trovano i fattori di sicurezza più bassi. Utilizzando il metodo A, il fattore di sicurezza risulta, con una temperatura dell’olio di 70°C, pari a 2,28. Tuttavia, la trasmissione a ingranaggi raramente ha funzionato a quella temperatura e ci si aspetta quindi che il fattore di sicurezza operativa sia più vicino a 4,48. Si prevede che un calcolo ISO con il metodo B risulti più conservativo rispetto al calcolo con il metodo A. In questo caso, se calcolato utilizzando la temperatura dell’olio di 70°C, il fattore di sicurezza risulta essere 2,06.
Linee guida in IEC 61400-4
Negli ultimi anni, il gruppo di lavoro congiunto IEC/ISO ha rivisto la norma IEC 61400-4 “Turbine eoliche – Parte 4: Requisiti di progettazione per i riduttori delle turbine eoliche” [20] per includere indicazioni sull’uso della ISO/TS 6336-22 per i riduttori ad ingranaggi per turbine eoliche. I calcoli contenuti in questo documento concordano con il requisito di utilizzare il metodo A per il calcolo dello spessore specifico minimo del film e il metodo B per lo spessore specifico ammissibile. Nella IEC 61400-4 si trova però un’ulteriore raccomandazione per bilanciare la rugosità del pignone e dei denti dell’ingranaggio per gli stadi critici che invece non è presente nella ISO/TS 6336-22. Questo set di ingranaggi non aderisce a questa raccomandazione, ma nemmeno molti vecchi progetti di turbine eoliche lo fanno.
La bozza del documento di progettazione delle turbine eoliche raccomanda inoltre che il fattore di sicurezza contro il micropitting sia sempre maggiore di 2,0. Tuttavia, incoraggia fortemente l’ingegnere a verificare i risultati del calcolo e fare esperienza sul campo con set di ingranaggi simili e stabilire un fattore di sicurezza minimo basato sull’evidenza sperimentale scegliendo valori compresi tra 1,5 e 2,0. I fattori di sicurezza calcolati per il Caso 2 si avvicinano a 2.0 nel caso in cui la temperatura dell’olio venga aumentata fino a 70°C. Tuttavia, la trasmissione ad ingranaggi non ha mai funzionato a questa temperatura. Come si può vedere nella figura 5, la temperatura massima raggiunta in esercizio è risultata pari a 66°C anche se solitamente rimaneva compresa tra 40°C e 60°C per la maggior parte del tempo di funzionamento. Questo è un caso in cui i fattori di sicurezza calcolati dovrebbero essere validati rispetto all’esperienza sul campo.
Come osservato sopra, la trasmissione a ingranaggi ha funzionato in una serie di condizioni operative di carico diverse in base alla velocità del vento. Solitamente è possibile utilizzare gli spettri di carico per eseguire un calcolo cumulativo del cimento a fatica (sia quando gli ingranaggi delle turbine eoliche vengono valutati in termini di resistenza a pitting, sia per i cedimenti a flessione). Questo approccio non è però possibile nel caso di micropitting poiché non è stata ancora stabilita una curva S-N per il micropitting. Un calcolo in conformità alla norma IEC 61400-4 verrebbe invece effettuato alla velocità nominale del rotore.
Caso 3: set di ingranaggi per tribologia AGMA
Il caso 3 è l’ingranaggio utilizzato nel programma di test tribologici AGMA [21]. Questo ingranaggio è simile agli ingranaggi FZG tipo “C”, ma più rappresentativo degli ingranaggi industriali, in quanto avente un passo più fine, un diverso numero di denti, topping e modifiche del profilo. Gli ingranaggi per test tribologici AGMA hanno anche una bombatura assiale per aumentare la sollecitazione di compressione al centro della larghezza di fascia.
Nell’articolo precedente, il fattore di sicurezza a micropitting è stato calcolato con i lubrificanti utilizzati nel test tribologico originale. In questo articolo si fa riferimento allo studio eseguito da Houser [22]. Questo studio è stato condotto per valutare il metodo ISO/TS 6336-22 attraverso test con Dexron VI ATF per determinarne la fase di carico che porta a cedimento per micropitting. Le foto del pignone danneggiato sono riportate nella figura 7.
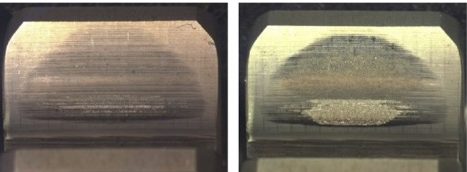
I calcoli con il metodo B nell’ultimo articolo hanno portato a fattori di sicurezza compresi tra 1,10 e 1,80, con valori decrescenti all’aumentare del carico. Questo risultato è paragonabile ad altri calcoli del fattore di sicurezza a micropitting relativi a casi in cui il micropitting è stato effettivamente osservato sperimentalmente. Questo documento confronterà i calcoli del Metodo A e del Metodo B con i risultati dei test dello studio di Houser. I calcoli sono stati effettuati utilizzando i carichi per FVA 54 relativi agli stadi 7, 8, 9 e 10 così da simulare il test eseguito sul set di ingranaggi. La geometria e il lubrificante per questo caso sono riassunti nella tabella 8. I carichi sono riportati nella tabella 9.
Dimensione | Unità | Pignone | Ingranaggio | |
Numero di denti | – | 20 | 30 | |
Rapporto | – | 1.50 | ||
Interasse | mm | 91.50 | ||
Modulo normale | mm | 3.629 | ||
Larghezza della faccia | mm | 13.97 | ||
Diametro esterno | mm | 82.042 | 116.716 | |
Angolo di pressione | gradi | 20.00 | ||
Angolo dell’elica | gradi | 0 | ||
Modifica dell’addendum | – | 0.2533 | -0.0296 | |
Rugosità superficiale | mm | 0.34 | 0.22 | |
Grado di precisione ISO | – | 4 | 5 | |
Durezza superficiale | HRC | 59-61 | 59-61 | |
Prodotto KA Kv KHa KHb | – | 1.0826 | ||
Lubrificante | – | Dexron VI ATF | ||
Temperatura lubrificante in ingresso | °C | 409 (misurato) |
SKS | Velocità pignone (giri/min) | Coppia pignone (N-m) | Pressione hertziana nominale in A (N/mm2) |
7 | 2,250 | 132.5 | 1,048 |
8 | 2,250 | 171.6 | 1,191 |
9 | 2,250 | 215.6 | 1,333 |
10 | 2,250 | 265.1 | 1,476 |
Ulteriori dettagli/discussioni su questo set di ingranaggi
La geometria di questo riduttore è molto simile a quella degli ingranaggi di prova FVA 54 e i carichi sono quelli utilizzati nella prova FVA 54. Lo spessore specifico ammissibile calcolato per il lubrificante sarà dunque rappresentativo dell’ingranaggio di prova. Si prevede che i fattori di sicurezza calcolati per questo caso siano capaci di predire il micropitting riscontrato durante il test.
Calcoli
Metodo A Risultati del calcolo
I risultati ottenuti con il metodo A sono riportati nella tabella 10.
Stadio di carico SKS | ||||||
Nome | Simbolo | Unità | 7 | 8 | 9 | 10 |
Temperatura apparente | qM | °C | 53.28 | 56.58 | 60.19 | 64.09 |
Spessore spec. minimo | λGFmin | – | 0.256 | 0.224 | 0.196 | 0.171 |
Spessore spec. ammissibile | λGFP | – | 0.189 | 0.189 | 0.189 | 0.189 |
Fattore di sicurezza | Sλ | – | 1.35 | 1.18 | 1.04 | 0.90 |
La distribuzione della pressione e lo spessore specifico del film attraverso nella zona di contatto relativi allo stadio di carico 8 sono riportati nella figura 8. L’effetto della bombatura del dente è chiaro e i carichi appaiono concentrati sul dente. L’influenza del fattore di scorrimento sullo spessore del film è anch’esso evidente dai valori più elevati in prossimità della circonferenza primitiva e dai valori più contenuti vicino al piede del dente.
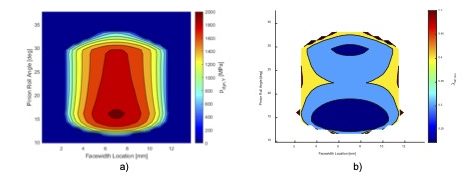
Metodo B Risultati aggiornati
I risultati dei calcoli del metodo B sono riportati nella tabella 11.
Stadio di carico SKS | ||||||
Nome | Simbolo | Unità | 7 | 8 | 9 | 10 |
Temperatura apparente | qM | °C | 53.28 | 56.91 | 60.52 | 64.47 |
Spessore spec. minimo | λGFmin | – | 0.319 | 0.273 | 0.233 | 0.200 |
Spessore spec. ammissibile | λGFP | – | 0.189 | 0.189 | 0.189 | 0.189 |
Fattore di sicurezza | Sλ | – | 1.69 | 1.44 | 1.23 | 1.06 |
I fattori di sicurezza
Sia utilizzando il metodo A, sia il metodo B, i fattori di sicurezza calcolati risultano in linea al micropitting osservato sugli ingranaggi di prova. Tra gli stadi di carico 8 e 9 è stata osservata una massiccia insorgenza micropitting: i fattori di sicurezza calcolati per queste fasi erano effettivamente molto bassi.
Conclusioni
I dettagli dei calcoli di questi casi di studio sono piuttosto lunghi. I disegni e i dettagli delle modifiche al profilo sono proprietari. Di conseguenza, gli autori possono fornire dettagli specifici solo su richiesta.
Questa indagine ha esaminato i calcoli sonoco ISO/TS 6336-22 Metodo A e Metodo B, confrontando i risultati con i risultati sul campo. Nel processo di stesura di entrambi i documenti, sono state effettuate ampie revisioni della geometria, della rugosità superficiale, delle condizioni di carico e delle condizioni del lubrificante. Queste revisioni sono state effettuate per comprendere meglio le influenze del micropitting su ciascun caso studio e l’applicabilità dei calcoli ai risultati. Si possono trarre le seguenti conclusioni relativamente ai due metodi:
- I fattori di sicurezza calcolati utilizzando il Metodo A e il Metodo B non hanno predetto il micropitting per i casi 1 e 2. In entrambi i casi, sebbene gli elevati fattori di sicurezza calcolati, il micropitting si è manifestato durante l’esercizio.
- Lo spessore specifico ammissibile è un fattore significativo nel calcolo di un fattore di sicurezza a micropitting. È importante utilizzare un valore rappresentativo del set di ingranaggi in esame.
Questo valore risulta migliore se misurato direttamente con test su ingranaggi reali in condizioni di esercizio veritiere fino all’insorgenza del danneggiamento. Questo però non è sempre pratico o possibile.
Se non è possibile eseguire il test con ingranaggi reali, si può utilizzare un calcolo basato sui risultati del test FVA 54. Tuttavia, il test FVA 54 è un test per la capacità protettiva del lubrificante a che utilizza ingranaggi progettati per cedere a micropitting. Lo spessore ammissibile risultante avrà un grado di incertezza basato su quanto gli ingranaggi e le condizioni operative in esame differiscano da quelle del test FVA 54.
- Il caso 1 ha funzionato a carico e velocità costanti per molto più tempo di quello che sarebbe stato il limite di resistenza a flessione e pitting. Inoltre, le condizioni dei fianchi (non danneggiati) indicano come l’ingranaggio abbia funzionato in regime EHL completo per tutta la sua vita. L’analisi mediante WindowsLDP mostra come l’intero fianco era coinvolte nel contatto. Nonostante queste condizioni operative ottimali, i denti hanno mostrato micropitting (dopo miliardi di cicli). Questo risultato porta a chiedersi se il micropitting sia prevedibile esclusivamente attraverso lo studio dello spessore del film o se ulteriori aspetti svolgano un ruolo determinante.
- Il metodo B è un modello di calcolo generale per lo spessore minimo specifico del film. Per un’analisi più approfondita, si consiglia di utilizzare il metodo A. Tuttavia, l’ingegnere deve decidere come determinare le pressioni e le temperature all’interno della zona di contatto qualora impieghi il metodo A.
- ISO/TS 6336-22 utilizza il valore aritmetico medio di rugosità (Ra) per valutare l’influenza della finitura superficiale sugli spessori specifici del film. Recenti lavori in ambito tribologico hanno invece utilizzato la rugosità quadratica media (Rq) o l’altezza massima del profilo (Rz). Al fine di verificare se l’uso di questi parametri modificasse i risultati dei calcoli, sono stati utilizzati i valori misurati di Rz degli ingranaggi nel caso 2 ed è stato ri-calcolato lo spessore specifico del film. I valori misurati relativi agli ingranaggi di prova FVA 54 sono stati utilizzati per calcolare lo spessore specifico ammissibile. Lo spessore specifico del film risulta minore qualora si utilizzi Rz. Anche il fattore di sicurezza risulta diminuito, ma è difficile dire se vi sia un legame migliore con la vera insorgenza del micropitting. Sono necessarie ulteriori revisioni su questo argomento.
Metodo della rugosità | ||||
Nome | Simbolo | Unità | Ra | Rz |
Rugosità effettiva1 | Ra, Rz | μm | 0.385 | 4.315 |
Spessore specifico minimo del film | λGFmin | – | 0.653 | 0.058 |
Spessore specifico del film ammissibile | λGFP | – | 0.338 | 0.048 |
Fattore di sicurezza | Sλ | – | 1.932 | 1.212 |
1 La rugosità effettiva utilizzando Ra è il valore medio aritmetico. La rugosità effettiva utilizzando Rz è il valore quadratico medio. |
In generale, i metodi in ISO/TS 6336-22 funzionano meglio quando l’ingegnere ha una conoscenza completa della progettazione, della produzione, delle condizioni operative e della durata del set di ingranaggi e del lubrificante. Pinnekamp [23] ha osservato come l’affidabilità del fattore di sicurezza a micropitting si basi sulla conoscenza da parte dell’ingegnere delle condizioni operative e sulla qualità dei suoi calcoli: quando c’è una bassa confidenza nei metodi, il fattore di sicurezza deve essere confrontato con i risultati delle prove con ingranaggi simili.
Sviluppi futuri
Poiché la scienza alla base della previsione del micropitting continua a evolversi, sono necessari ulteriori studi per migliorare ISO/TS 6336-22. Lo sviluppo dovrebbe arrivare a fattori di sicurezza che non richiedano il confronto con ingranaggi simili per l’interpretazione. Ulteriori raccomandazioni sono:
– continuare a sviluppare un metodo per stabilire lo spessore specifico ammissibile del lubrificante quando non è possibile testare ingranaggi reali. Se è necessario utilizzare i risultati dei test sui lubrificanti FVA 54, sarebbe utile disporre di un metodo che consenta di scalare i dati in base alla geometria ed ai carichi dell’applicazione.
– migliorare la guida per aiutare l’ingegnere nell’uso completo del Metodo A, includendo tutti i fattori da prendere in considerazione (ad esempio, carico, temperatura, topografia superficiale, ecc.).
– sviluppare una procedura di prova per valutare la relazione S-N per il micropitting, in modo da poter stabilire l’impatto di cicli di carico ripetuti durante la valutazione del micropitting. Inoltre, lo sviluppo di un modello predittivo che incorpori questo esclusivo meccanismo di danneggiamento è importante poiché le aspettative del ciclo di vita della trasmissione a ingranaggi continuano a crescere.
Robin Olson, Regal Rexnord Corporation
David Talbot, The Ohio State University, Gear and Power Transmission Research Laboratory
Mark Michaud, REM Surface Engineering
Jonathan Keller, National Renewable Energy Laboratory
John Amendola, Sr., Artec Machine Systems
Articolo tratto da una relazione presentata all’AGMA FTM 2023 e stampato con l’autorizzazione dell’American Gear Manufacturers Association, proprietaria dei diritti d’autore. American Gear Manufacturers Association, 1001 N. Fairfax Street, 5th Floor, Alexandria, Virginia 22314. Le dichiarazioni e le opinioni espresse in questo testo sono quelle degli autori e non sono da considerarsi ufficiali dell’American Gear Manufacturers Association. Si ringrazia l’AGMA per la gentile autorizzazione alla pubblicazione (NdR).