Componenti sensorizzati intelligenti per la trasmissione di potenza: tipologie e applicazioni dei principali sensori integrati che favoriscono il miglioramento delle prestazioni dell’intero sistema di trasmissione in un’ottica di condition monitoring avanzato
Il settore automotive deve oggi affrontare la grande sfida della mobilità elettrica. In questo contesto, le stringenti normative richiedono, da un lato, maggiore efficienza energetica e, dall’altro, una riduzione delle emissioni di CO2. Sistemi di trasmissione ottimizzati rappresentano la soluzione per raggiungere obiettivi così ambiziosi. Un sistema di trasmissione efficiente deve garantire dissipazioni e perdite energetiche ridotte ed elevati rapporti di trasmissione. Inoltre, i moderni sistemi di trasmissione devono anche supportare l’evoluzione di motorizzazione ibride, talvolta con architetture modulari e una migliore qualità del cambio di rapporto. I produttori devono impegnarsi ad apportare tali migliorie, nel rispetto di tutti gli standard di sicurezza e con la capacità di soddisfare le aspettative dei clienti in termini di prestazioni e comfort di guida. Sensori affidabili e precisi stanno diventando componenti fondamentali in molte applicazioni di trasmissione, per esempio nel caso di sensori di velocità (clutch control), sensori di posizione (parking lock e gear lever), sensori di posizione angolare (rotor sensing), e altri, come si vede nella soluzione costruttiva di figura 1.
Trasmissioni efficienti, ad alte prestazioni richiedono sistemi di azionamento intelligenti che consentono di cambiare le marce in modo efficiente e fluido. I sensori di velocità e di posizione sono essenziali per tale scopo. Inoltre, è bene considerare che le moderne trasmissioni meccaniche sono costituite da molti sottosistemi con funzioni diverse e fortemente integrate fra di loro. Di seguito esamineremo le tipologie e le applicazioni dei principali sensori integrati che favoriscono il miglioramento delle prestazioni dell’intero sistema di trasmissione in un’ottica di condition monitoring avanzato.
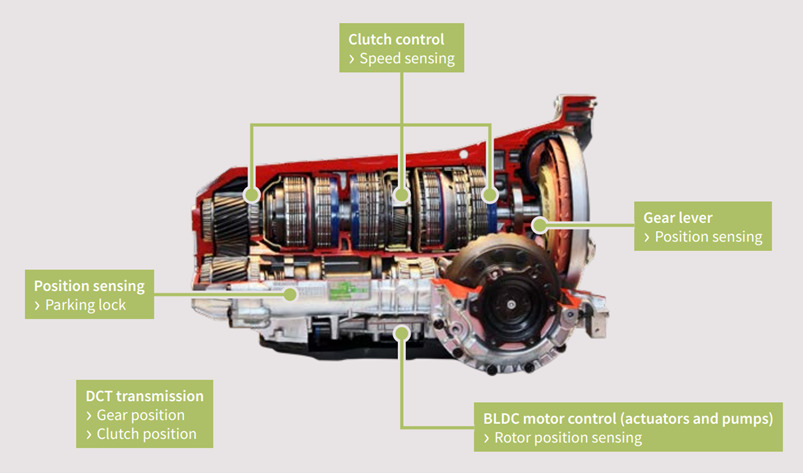
Manutenzione preventiva supportata da sensori integrati nei componenti
Impianti, macchinari e veicoli commerciali sono sottoposti ogni giorno a condizioni operative intense e carichi elevati che provocano, specie nei componenti in movimento, usura ed altri fenomeni di danneggiamento più o meno gravi. Questi, a loro volta, possono compromettere il funzionamento e la sicurezza dell’intero sistema.
In genere, le aziende eseguono regolarmente interventi di manutenzione sui loro macchinari ed attrezzature, per garantirne il corretto funzionamento. Tuttavia, spesso è molto difficoltoso possedere una conoscenza vera e propria dello stato di salute in tempo reale degli impianti e dei veicoli e, di conseguenza non si dispone di informazioni sufficienti per valutare la effettiva necessità di operazioni di manutenzione. Inoltre, i punti con maggiore effetto di usura nei componenti non vengono rilevati accuratamente, causando ulteriori problemi tra un intervento di manutenzione e il successivo. Nonostante l’accurata manutenzione periodica, i problemi si verificano continuamente e, di norma, solo in caso di guasto si procede ad indagarne la causa e si effettua la successiva riparazione. Ciò si traduce in tempi di fermo macchina generalmente più lunghi del necessario e costose perdite di produzione.
Nel contesto della digitalizzazione e dell’Industria 4.0, a questi problemi si può porre rimedio in modo efficace rendendo per così dire “intelligenti” i componenti più importanti del sistema di trasmissione: alberi, giunti, ruote dentate, etc. Questo accorgimento può fornire regolari feedback agli operatori circa lo stato di salute di questi componenti in tempo reale.
Infatti, soluzioni sensorizzate, integrate nel componente da monitorare, forniscono un flusso continuo di dati preziosi, consentendo previsioni accurate riguardanti le condizioni di deterioramento del componente stesso e di quelli collegati. Ciò aiuta non solo ad individuare precocemente i guasti e a procedere con riparazioni tempestive ma anche a prevenire questi problemi attraverso programmi di manutenzione mirati, pianificando il momento corretto in cui effettuare l’intervento ed evitando fermi produzione.
Un esempio in tal senso è rappresentato dall’albero di trasmissione Smart Sensor del gruppo Elbe, sviluppato in collaborazione con le aziende Core Sensing Gmbh ed HBK (Hottinger Brüel & Kjær), dotato di sensori intelligenti. In numerose macchine e veicoli, gli alberi di trasmissione sono soggetti a carichi elevati, soprattutto se utilizzati in contesti aggressivi e ambienti ostili. Con il trascorrere del tempo è probabile che si verifichino danneggiamenti di questo componente a causa, per esempio, di fatica e/o di usura.
Integrando sensori intelligenti con la relativa elettronica di controllo e condizionamento, per esempio sfruttando lo spazio interno di alberi cavi, si può ottenere una misurazione precisa ed in tempo reale, magari in modo indiretto, della coppia trasmessa e della forza assiale applicata, direttamente provenienti dal componente. Per misurare queste grandezze, nello specifico, si sono utilizzati sensori di deformazione (estensimetri) in grado di fornire un segnale legato alle sollecitazioni di torsione e trazione. Questi vengono compensati rispetto alle condizioni ambientali e operative specifiche dell’applicazione, con riferimento a geometria, dimensioni, materiale e temperatura operativa. In questo modo, gli utenti possono fare affidamento su dati precisi di coppia e forza assiale, integrati a loro volta con una varietà di variabili aggiuntive rilevate durante l’intera catena di misura. I dati sono trasmessi in modalità wireless dai sensori al gateway o all’app “Core Viewer”, utilizzando una connessione standardizzata a 2,4 GHz. La tecnologia di rilevamento ad elevata efficienza energetica, posizionata nella cavità dell’albero, è alimentata a batteria, con erogazione di energia per diversi mesi.
Nell’ottica di manutenzione predittiva, l’albero di trasmissione intelligente può essere integrato direttamente nel percorso di carico di una catena di organi di trasmissione, per misurare i carichi effettivi che si generano durante il funzionamento dell’intero sistema. Questi valori possono essere confrontati con parametri di progetto calcolati in precedenza al fine di ottenere un monitoraggio affidabile dell’albero e degli altri componenti. Inoltre, un componente sensorizzato posizionato all’interno della catena cinematica fornisce informazioni preziose sullo stato di salute generale della macchina. Selezionando con attenzione i punti di rilevamento, è possibile rilevare i carichi agenti su altri componenti e determinare il loro grado di danneggiamento. Disponendo di affidabili algoritmi di predizione del danneggiamento, infine, i sensori possono determinare sia la durata di vita residua dell’albero motore che quella dei componenti circostanti, e, al contempo, individuare il momento migliore per gli interventi di manutenzione predittiva. I possibili guasti possono essere previsti in modo affidabile grazie ad algoritmi di Machine Learning. I dati forniti dai sensori, grazie al condition monitoring, forniscono ulteriori informazioni sull’efficienza della macchina che consentono di ottimizzarne i consumi senza comprometterne le prestazioni.
Unità integrata per la diagnostica di alberi motore
Come noto, e come già commentato in precedenza, la transizione verso la propulsione elettrica dei veicoli comporta nuove sfide nella progettazione: coppie di spunto più elevate, una curva di potenza più ripida ed un baricentro del mezzo più basso determinano carichi differenti sul telaio e sulle sospensioni. Il controllo di questi carichi è fondamentale sin dalle prime fasi dello sviluppo del veicolo, poiché, in tal modo, i costi di follow-up nelle aree citate vengono ridotti al minimo. Oltre alle coppie torcenti si possono poi verificare forze laterali e momenti flettenti che possono compromettere la durata di componenti critici come i cuscinetti.
I carichi effettivi durante i viaggi su strada possono essere riprodotti mediante banchi di prova, sui quali i singoli componenti vengono testati per verificarne la resistenza a fatica e usura. Tali carichi devono essere riprodotti nel modo più realistico possibile e pertanto una delle strategie è quella di misurarne i valori durante i test drive su veicoli di prova, utilizzando ad esempio sistemi di telemetria abbinati a sensori estensimetrici.
In figura 2, un esempio di unità di misura utile a questo scopo (“coreIN”, sviluppata dall’azienda Core Sensing Gmbh), con la quale si può effettuare l’acquisizione di spettri di carico su veicoli di prova per la messa a punto dei banchi prova.
Anche in questo caso, sensore e componente sono totalmente integrati in una unità di misurazione alloggiata all’interno dell’albero motore, senza la necessità di alcun adattamento del banco prova o del veicolo prototipo. I carichi effettivi sono misurati in tempo reale ed eventuali sovraccarichi memorizzati ed analizzati in un momento successivo.
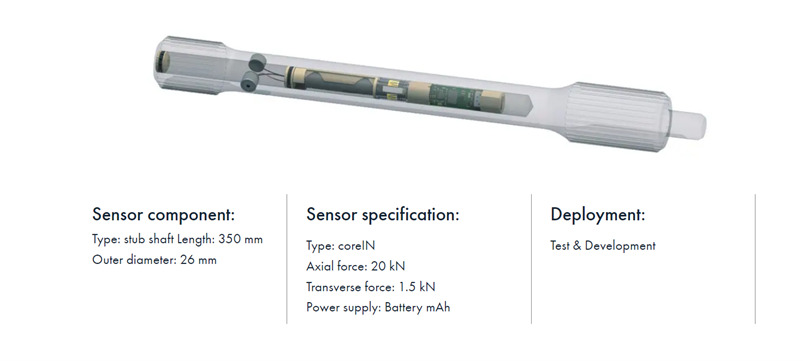
La posizione del sensore rispetto all’asse di rotazione riduce al minimo le forze centrifughe che si verificano ad elevate velocità, minimizzando il rischio di alterare i dati misurati. Nei casi più tradizionali, il consueto montaggio della telemetria all’esterno dell’albero motore genera facilmente grandi squilibri a causa della distanza dall’asse di rotazione e richiede modifiche al veicolo. Con la soluzione integrata, queste criticità vengono eliminate. Inoltre, la batteria integrata rappresenta la soluzione ottimale per rilevazioni in tempo reale in presenza di movimento rotatorio, evitando il passaggio di cavi di alimentazione intorno e attraverso gli organi di trasmissione.
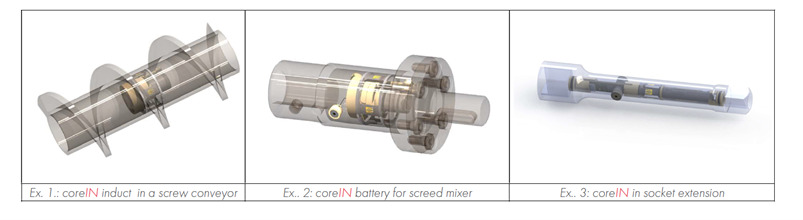
Proviamo a elencare i vantaggi della tecnologia “coreIN” che abbiamo descritto.
- Il sensore, insieme all’unità di misurazione, può essere integrato (risultando quindi protetto da ambienti aggressivi e azioni meccaniche esterne) in differenti componenti, anche non simmetrici, e comunica wireless con altri dispositivi IoT (Internet of Things) per l’ottimizzazione del sistema di monitoraggio.
- Dimensioni comparabili con quelle del componente meccanico da misurare consentono la perfetta integrazione.
- Le informazioni sono archiviate nella memoria flash integrata oppure condivise in cloud.
- Monitoraggio e manutenzione preventiva applicabile ai componenti critici coinvolti nel flusso di carico come alberi di trasmissione, ingranaggi o cuscinetti.
- Ideale anche per tubi o componenti forati con diametro interno pari o superiore a 14 mm.
- Processi monitorati in tempo reale, con rilevazione continua di dati e possibilità di gestire le informazioni anche via App, garantiscono la sicurezza, la qualità e l’affidabilità dell’intero sistema.
- Attraverso il monitoraggio della coppia, l’intero sistema è sotto controllo e l’efficienza è migliorata, con possibilità di programmare nel giusto momento gli interventi di manutenzione. Ciò si ottiene rilevando i carichi effettivi in condizioni operative, anziché lavorando con i dati di progetto.
- L’elemento deformabile che ospita i sensori di deformazione per la misura di forze, momenti flettenti e coppie è configurato a seconda dell’applicazione specifica.
- Il sensore di forza/coppia integrato è disponibile sia per singole unità che per la produzione in serie.
- Design modulare per applicazioni quasi illimitate (alcuni esempi di applicazioni sono riportati in figura 3), con varie dimensioni e opzioni energetiche (batteria, induzione, recupero di energia cinetica, cablato – figura 4).
- Misurazione di parametri meccanici specifici a seconda dell’applicazione (tra cui coppia, forze assiali, momenti flettenti o forze di taglio, velocità di rotazione, accelerazione lungo i tre assi e temperatura.
- Possibile ulteriore lavorazione dei componenti.
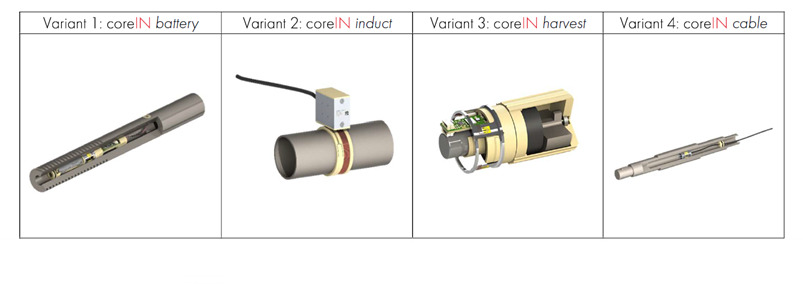
Integrazione di sensori mediante processi additivi
Fino a poco tempo fa, la sensorizzazione di componenti meccanici, mediante tecniche tradizionali prevedeva l’installazione del sensore su superfici esterne, tramite, ad esempio, l’applicazione di componenti filettate o adesivi oppure l’installazione interna, mediante operazioni di foratura e fresatura. Tuttavia, tali metodologie presentano evidenti limiti nell’integrazione sensore-componente: in primo luogo, il sensore, oltre a rimanere distante dal punto di misurazione, è esposto a disturbi ambientali, possibili urti meccanici e contaminazioni di vario genere. In secondo luogo, invece, la realizzazione di fori o canali è vincolata a forme prevalentemente cilindriche e, in ogni caso, rettilinee.
Partendo da queste considerazioni, lo Smart Structures and Systems Laboratory del Politecnico di Torino, in collaborazione con l’azienda Pres-X ha sviluppato un particolare processo di manifattura additiva (AM) che consente di “annegare” sensori e circuiti elettronici all’interno di un componente. A questo scopo, i tradizionali processi di microfusione delle polveri metalliche (Laser Powder Bed Fusion – LPBF o Selective Laser Melting – SLM) hanno subìto una serie di modifiche sostanziali che hanno permesso di ottenere componenti metallici di differenti materiali, all’interno dei quali sono stati posizionati elementi elettronici “nativi”, ovvero presenti sin dalla creazione dei componenti stessi.
La tecnologia innovativa così sviluppata combina la versatilità della manifattura additiva con i vantaggi legati alla sensorizzazione interna dei componenti. Il sensore risulta perfettamente integrato nel metallo (senza giunzioni o interruzioni di sorta nel materiale), protetto ed inalterabile. La posizione del sensore è libera all’interno del volume di riferimento, non più vincolata ai canali generati per l’asportazione del truciolo e, in corrispondenza di eventuali collegamenti cablati, il cavo stesso può seguire percorsi curvilinei all’interno del componente.
Si comprende facilmente come una progettazione dedicata del componente sia fondamentale per ottimizzare il rapporto resistenza/peso, per sfruttare la libertà di forma in applicazioni di scambio termico, per integrare più parti in un unico componente, per impiegare leghe più performanti e trattamenti termici di post-processo più efficienti. Il processo è stato validato per alcune famiglie di materiali, fra cui acciaio 17-4PH, Inconel In718 e lega di alluminio AlSi10Mg. A tali materiali sono poi stati applicati trattamenti termici post-processo di diverso tipo per l’ottimizzazione delle proprietà meccaniche.
Un caso-studio del processo descritto è rappresentato dalla realizzazione di una pinza per freno a disco idraulico professionale da mountain-bike, nella quale è prevista l’integrazione di una sonda termica “nativa” per la rilevazione della temperatura delle pastiglie ed il monitoraggio delle prestazioni frenanti. Il corpo della pinza freno è modellato ottimizzando le sollecitazioni meccaniche, con ingente risparmio di materiale. Una prima geometria di riferimento, visibile in figura 5, è stata definita sulla base del calcolo di coppia frenante associata a pressione dell’olio e dimensione delle pastiglie.
In questa geometria viene predisposto il posizionamento della sonda termica, con alcuni requisiti di progetto specifici.
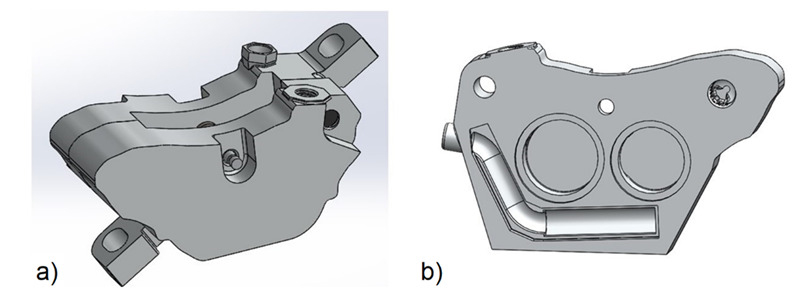
Il mercato delle trasmissioni di potenza e dei sensori
Con l’avvento dell’Industria 4.0 e dell’Internet of Things (IoT) cresce l’esigenza di una corretta gestione ed interpretazione dei dati. Questi, infatti, rappresentano un patrimonio imprescindibile per l’innovazione di cui si parla oggi in ambito industriale. In questo contesto, è determinante lo sviluppo di componenti meccanici intelligenti, che possiamo definire “smart”, ovvero in grado di interagire in tempo reale con l’ambiente circostante e capaci di rilevare e condividere parametri di vario genere: dalla misurazione della temperatura, vibrazioni, carichi e accelerazioni, fino alla possibilità di prevedere guasti. Tali informazioni sono indispensabili per valutare lo stato di salute complessivo delle strutture, confrontare carichi effettivi con quelli di progetto e rilevare condizioni di funzionamento operative.
Nel settore automotive, i moderni sistemi di trasmissione devono soddisfare i requisiti di efficienza e di sicurezza, oltre a garantire prestazioni elevate e comfort di guida. A tal fine e per soddisfare le esigenze dei clienti, i sistemi di attuazione intelligenti e il rilevamento preciso della posizione e della velocità sono fattori chiave.
Nel 2022, il mercato globale delle trasmissioni di potenza meccaniche ha raggiunto un valore di circa 65,25 miliardi di dollari e si prevede un aumento a un CAGR del 5,2% sino ad una valutazione di mercato pari a 108,3 miliardi di dollari entro il 2032. Gli OEM automobilistici si stanno concentrando sulla riduzione del peso dei veicoli per migliorarne l’efficienza, favorendo l’aumento della domanda di componenti leggeri e, a sua volta, quella di altri prodotti come trasmissioni a cinghia e a catena. Poiché le variabili di progettazione nei componenti di trasmissione, come i diametri di cuscinetti e ingranaggi, sono associate a determinati limiti, si stanno sviluppando strategie di progettazione integrate. Grazie alla lunga durata dei componenti, i costi operativi possono essere ridotti al minimo. Inoltre, l’esperienza nella progettazione e produzione di sistemi di trasmissione ad alta efficienza e coppia elevata è utile per lo sviluppo di veicoli elettrici ad alta potenza e nelle applicazioni per sport motoristici. Si sta assistendo progressivamente, nell’ambito delle trasmissioni di potenza, a una maggiore durata dei componenti, temperature ridotte del cambio e miglioramenti in termini di efficienza. Emergono inoltre sistemi di trasmissione di fascia alta dal funzionamento silenzioso ed esenti da vibrazioni. Lo sviluppo di sistemi di trasmissione di potenza meccanica continuerà a supportare le esigenze delle industrie pesanti. I nuovi operatori nel mercato della trasmissione di potenza meccanica avranno il compito di produrre apparecchiature di alta qualità che richiedono efficienza nei consumi e ridotta manutenzione.
Per quanto riguarda i sensori, anche in questo caso, le stime sono promettenti: il mercato globale è stato valutato a 199,50 miliardi di dollari nel 2022 e si prevede che raggiungerà i 409,10 miliardi di dollari entro il 2030, registrando un CAGR del 9,4% durante il periodo di previsione 2023-2030, dove a dominare il segmento dei componenti sono i microcontrollori, estremamente compatti ed economici, la soluzione ideale per varie applicazioni in cui i vincoli di spazio ed i costi sono fondamentali. Oggi, i sensori trovano applicazione, più comunemente nell’elettronica di consumo, seguita da settore automobilistico, IT e telecomunicazioni. Le smart cities fanno ampio uso di sensori per garantire efficienza, confort, sicurezza ed engagement. Un ulteriore fattore che alimenta la domanda di sensori è il crescente sviluppo dell’Internet of Things (IoT) e dei dispositivi connessi intorno al concetto di fabbrica intelligente. Le applicazioni IoT fanno affidamento sui sensori per raccogliere dati dal mondo fisico e consentire la connettività tra dispositivi e sistemi. I sensori sono fondamentali per consentire il monitoraggio in tempo reale, la raccolta dati e l’automazione nelle applicazioni IoT. Tuttavia, uno dei principali fattori frenanti è associato all’elevato costo per lo sviluppo e la produzione di sensori avanzati, che spesso comportano processi complessi, materiali sofisticati e tecnologie avanzate. Elevati costi di produzione possono rappresentare un limite, in particolare per le industrie sensibili al prezzo o nei mercati emergenti.