Se applicato alla lettera, tale metodo individuerebbe la presenza di circa 8 mila macchine critiche installate sul territorio italiano e responsabili dell’80% di infortuni gravi. Ma come riconoscerle?
Il principio di Pareto, conosciuto anche come la regola dell’80/20 o il principio del 20/80, è un concetto che deriva da osservazioni fatte dall’economista italiano Vilfredo Pareto nel XIX secolo. Questo principio afferma che, in molte situazioni, circa l’80% degli effetti proviene dal 20% delle cause. La proporzione specifica può variare, ma l’idea chiave è che una minoranza di input genera la maggior parte degli output. In sintesi, il principio di Pareto è uno strumento concettuale che aiuta a identificare e focalizzare l’attenzione sulle aree più influenti o critiche, con l’obiettivo di massimizzare l’efficacia delle risorse disponibili.
Per applicare il principio di Pareto agli infortuni sulle pressopiegatrici in Italia, partiamo con l’ipotesi che il 20% delle macchine possa essere responsabile dell’80% degli infortuni gravi. Con 40 mila pressopiegatrici installate nel territorio italiano, il 20% corrisponde a 8 mila macchine. Queste 8 mila pressopiegatrici rappresenterebbero il gruppo critico su cui concentrare l’attenzione per migliorare la sicurezza.
Successivamente, possiamo suddividere ulteriormente questo gruppo in base a possibili cause di pericolo legate a mancanza di manutenzione o adeguamenti inopportuni. Ad esempio, potremmo considerare:
- Pressopiegatrici senza manutenzione regolare.
- Pressopiegatrici con adeguamenti non conformi alle norme di sicurezza.
- Analisi delle macchine che potrebbero avere modifiche o adeguamenti non conformi alle normative di sicurezza vigenti.
- Macchine coinvolte in incidenti precedenti.
- Macchine con segnalazioni di malfunzionamenti.
- Pressopiegatrici vecchie o obsolete.
Il parco macchine, analizzato nei dettagli di questi 6 punti secondo questa metodologia, deve tuttavia considerare che, dagli anni Ottanta ai giorni nostri, la normativa è cambiata più volte. Lo stato dell’arte, tanto richiesto dalle ASL, in certi casi si è “congelato” a quanto previsto dal costruttore nel periodo di immissione nel mercato. Per questo motivo, ci troviamo spesso di fronte a situazioni in cui le disposizioni di sicurezza sono presenti ma non conformi alla normativa vigente.
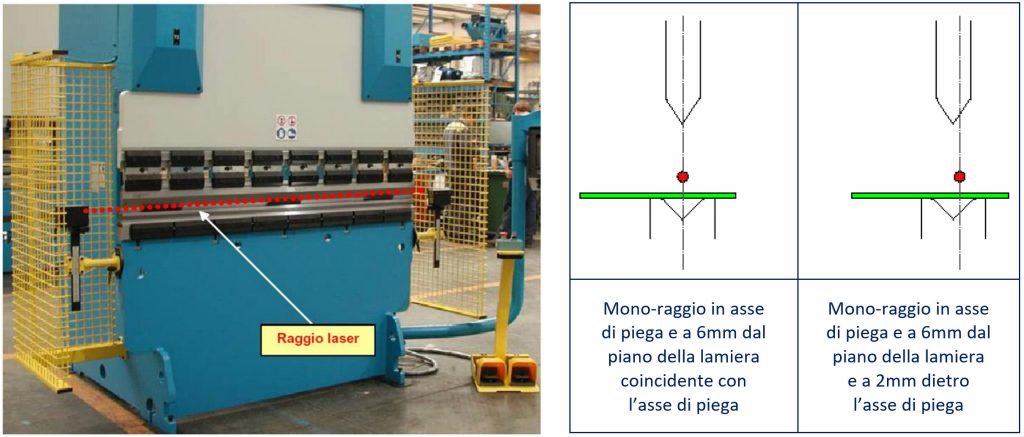
Una delle norme frequentemente violata riguarda la protezione della traversa mobile. Infatti, nelle caratteristiche delle macchine riportate nei 6 punti esposti sopra, uno dei punti comuni da adeguare è spesso la fotocellula monoraggio.
Riconoscere le monoraggio
In questo articolo, vi aiuteremo a riconoscerle. Se avete una di queste protezioni attive nelle vostre macchine sappiate che non rappresentano più lo stato dell’arte, sono fuori normativa da quasi 25 anni e, in caso di incidente, classificano la vostra pressopiegatrice come una macchina non sicura con conseguenze spesso pesanti.
Il sistema a monoraggio laser comprende un emettitore e un ricevitore. L’operatore regola normalmente la posizione del raggio laser lungo l’asse di piega, a un’altezza di 6-8 mm dal piano della lamiera da lavorare. È possibile regolare il sistema a 2 mm dietro l’asse di piega per consentire la creazione di pezzi scatolati.
La capacità di spostare il fascio a 2 mm dietro l’asse di piega permette di lavorare su una vasta gamma di pezzi, soprattutto quelli di piccole dimensioni e gli scatolati. Tuttavia, i sistemi monoraggio, sia laser che a luce non coerente, che erano ampiamente utilizzati in passato, non sono più considerati conformi allo stato dell’arte secondo le norme EN 12622:2001 e pr EN12622:2010. Ciò è dovuto al fatto che non garantiscono una riduzione del rischio adeguata come richiesto da tali normative.
Alcuni inconvenienti di questi sistemi sono i seguenti.
- Protezione incompleta della zona pericolosa: la zona sensibile di un sensore monoraggio è spesso limitata al diametro del raggio filiforme, che è di pochi millimetri. Ciò non copre completamente la zona pericolosa, che per la maggior parte degli utensili corrisponde alla larghezza della V della matrice.
- Necessità di frequenti regolazioni della posizione del raggio: l’uso di matrici di altezze diverse o materiali di spessore variabile richiede frequenti regolazioni del sistema.
- Spazio di arresto inadeguato: per garantire la protezione contro lo schiacciamento tra gli utensili, la pressa deve essere in grado di arrestare rapidamente la traversa superiore durante la discesa rapida. Tuttavia, in alcuni casi, lo spazio di arresto potrebbe risultare inadeguato.
- Difficoltà di regolazione su lamiere non perfettamente piane: se la lamiera da lavorare non fosse perfettamente piana potrebbero verificarsi punti in cui è possibile inserire un dito senza intercettare il raggio, creando potenziali punti di pericolo.
Conclusioni
Questi problemi evidenziano le limitazioni e le sfide associate ai sistemi monoraggio, che possono influire sulla sicurezza e sull’efficacia durante l’utilizzo su presse piegatrici.
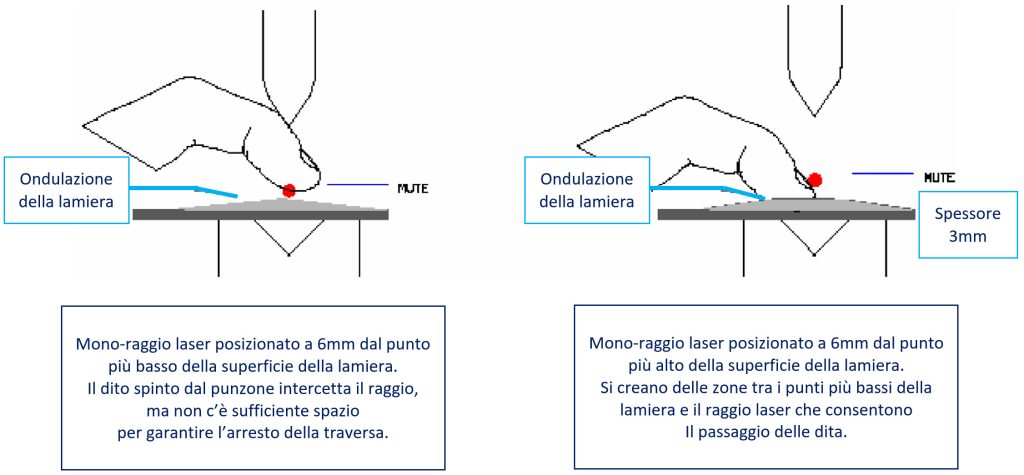
Se nella vostra azienda avete pressopiegatrici che utilizzano ancora queste protezioni sulla traversa superiore o, per alcuni modelli molto obsoleti, sulla traversa inferiore, vi consigliamo di seguire i prossimi articoli dove vi spiegheremo nel dettaglio cosa prevede il normatore e cosa dovete richiedere in fase di installazione al vostro installatore.