Questo è un argomento molto dibattuto e di grande attualità. Su questa tecnologia si sono concentrati gli sforzi dei produttori di creatori e di dentatrici per arrivare a soluzioni convenienti per produzioni di massa
Si può affermare, anzitutto, che il taglio a secco è possibile. Si tratta di decidere se sia anche conveniente. A questo quesito molto semplice purtroppo non corrisponde una risposta altrettanto semplice perché, come spesso accade, sono molti i fattori in gioco e sono molto diverse le situazioni all’interno delle singole aziende e dei singoli Paesi in cui queste officine operano. La scelta dell’una o dell’altra tecnologia è influenzata da tre fattori:
- lubrorefrigerazione;
- utensili;
- tipo di dentatrice.
Lubrorefrigeranti
Nel corso degli ultimi anni essi sono diventati sempre più sofisticati e ora possono risolvere meglio di un tempo problemi specifici. Si è attuata una specializzazione dell’olio refrigerante con l’impiego di additivi che esaltano particolari caratteristiche.
Si parla di additivo AW (Anti-Wear, cioè anti-usura) oppure di additivi EP (Extreme Pressure, cioè resistenti a pressioni molto alte), e poi ci sono additivi anti-corrosione, anti-nebbia, anti-dispersione ecc.
Naturalmente, per ogni singola lavorazione deve essere scelto il refrigerante più adatto e questo a volte non è semplice. È quindi vero che oggi si dispone di refrigeranti che possono elevare in modo sensibile il rendimento degli utensili, ma è anche vero che il loro costo è aumentato, sia per ragioni tecniche e sia per ragioni legate alla protezione dell’ambiente.
Ecco il punto chiave del discorso: il costo del refrigerante. Costo del refrigerante inteso come costo d’acquisto, come costo del suo consumo specifico e come costo di smaltimento dell’olio esausto e dei trucioli.
A questo si devono aggiungere un più elevato costo degli investimenti che su una linea di produzione devono comprendere: impianto refrigerante, impianto di aspirazione delle nebbie oleose, impianto di lavaggio dei pezzi prodotti, impianto di depurazione e di smaltimento degli oli esausti.
Per finire bisogna includere anche qualche considerazione di carattere ecologico che interessa l’intero ambiente e qualche rischio per la salute degli operatori.
Tutto ciò si traduce in un maggiore costo del pezzo prodotto. Recenti studi hanno dimostrato che il costo dei refrigeranti incide per il 10 – 15% sul costo totale di produzione. La conclusione ovvia sarebbe quella di eliminare il refrigerante e di lavorare a secco, ma le cose non sono così semplici.
Infatti l’impiego del refrigerante, se correttamente eseguito, ha molti effetti benefici sulla lavorazione e quindi sul rendimento degli utensili, e in particolare sui creatori.
In primo luogo, si ha una riduzione dell’attrito tra le parti in contatto.
Una corretta lubro-refrigerazione riduce l’effetto deleterio dello strisciamento del dorso e dei fianchi dei denti del creatore sulle superfici appena tagliate, con un minore sviluppo di calore, con una minore possibilità di saldatura di materiale sullo spigolo tagliente e quindi con una minore velocità di formazione dell’usura per abrasione.
Si riduce notevolmente anche l’attrito del truciolo sul petto del dente del creatore e questo riduce la formazione del tagliente di riporto e riduce la velocità di formazione dell’usura per craterizzazione.
L’azione refrigerante vera e propria dell’olio da taglio ha come lo scopo di asportare il più velocemente possibile il calore prodotto durante la lavorazione. Esso agirà sull’utensile, sul pezzo, sui trucioli e sulla macchina.
L’effetto sull’utensile sarà quello di ridurre l’aumento della temperatura del tagliente, sia in generale e sia nelle zone a più diretto contatto con il pezzo ed il truciolo, evitando che, per effetto dell’alta temperatura, le caratteristiche del materiale costituente l’utensile si deteriorino.
Qui un ruolo importante lo gioca il corretto invio del refrigerante nella zona di lavoro. La sua quantità, la sua direzione e la sua velocità devono essere attentamente studiate affinché non ci siano momenti di discontinuità nell’azione refrigerante. Infatti in questo caso i taglienti sarebbero soggetti a forti sbalzi di temperatura particolarmente dannosi se si lavora con creatori in Metallo Duro.
Se l’azione di refrigerazione dell’utensile è importante per il suo rendimento, è altrettanto importante l’azione refrigerante sul pezzo per la sua precisione.
Un pezzo che rimane più o meno alla stessa temperatura dall’inizio alla fine del ciclo procurerà meno problemi dal punto di vista della precisione.
Infine l’azione del refrigerante ha un effetto molto importante sulla stabilizzazione termica della macchina, evitando deformazioni localizzate che potrebbero compromettere la costanza dimensionale dei pezzi prodotti. Anche l’azione meccanica del trasporto dei trucioli non è trascurabile. La pulizia della zona di lavoro è molto importante, per il corretto posizionamento del pezzo, specie se si è in presenza di carico e scarico automatici. Inoltre, un abbondante flusso di refrigerante convoglierà i trucioli, che saranno a una temperatura accettabile, in zone di raccolta e di smaltimento adeguate.
Vedremo tuttavia che nonostante questi evidenti punti a favore della refrigerazione il taglio a secco si è diffuso notevolmente nelle produzioni di massa.
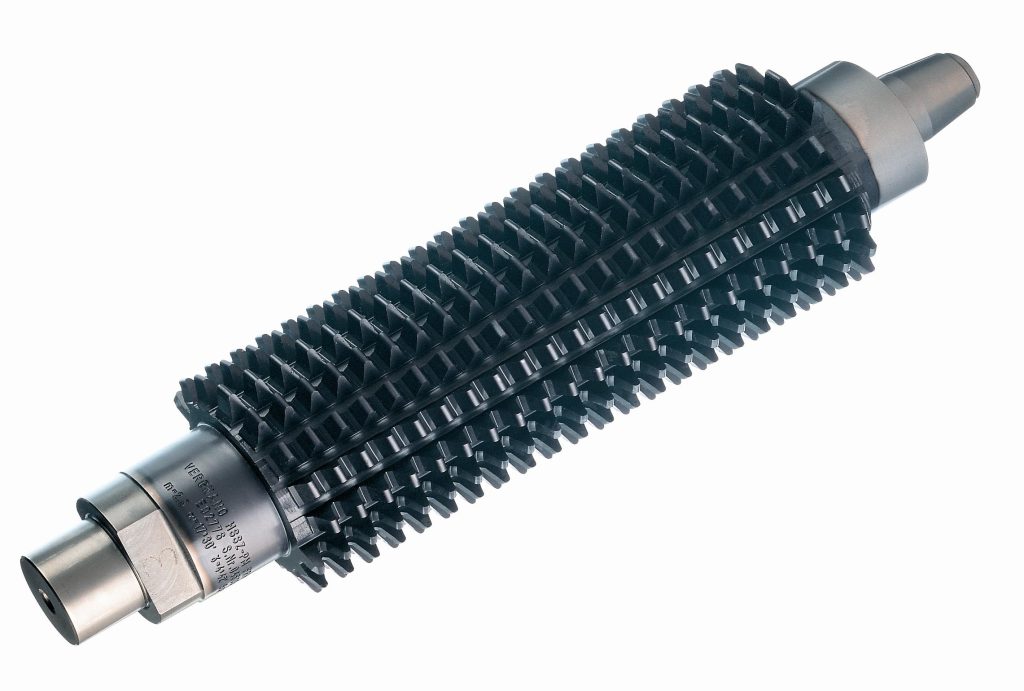
Utensili
I creatori si differenziano in primo luogo per il materiale con cui sono costruiti, infatti possono essere in HSS (High Speed Steel) oppure in Metallo Duro (Carbide).
I più moderni acciai per la costruzione di utensili hanno un’alta percentuale di componenti di lega, anche oltre il 30%%, e sono normalmente ottenuti con la sinterizzazione (Powder Technology).
Con questi creatori si può lavorare con velocità di taglio anche superiori a 150 m/min, con avanzamenti per giro notevoli che dipendono dalla struttura del creatore stesso (diametro, numero di principi, numero di solchi di affilatura e modulo).
L’alta velocità di taglio possibile è anche conseguenza dei più moderni ricoprimenti oggi possibili, specialmente quelli a base di alluminio-cromo-titanio,
Bisogna subito notare che il diametro dei creatori impiegati per la produzione di ingranaggi fino a modulo 3 mm può essere anche di 50 – 60 mm in quanto con piccoli diametri si ottengono tempi di lavoro minori.
Il numero di principi nei creatori in acciaio può essere molto alto, anche 6 – 7 principi, con la conseguenza che l’angolo del filetto, e quindi dei solchi di affilatura, assume valori elevati. In questi casi l’affilatura deve essere fatta con mole in ceramica perché la mola deve poter essere modificata sul profilo.
I creatori in Metallo Duro possono lavorare a velocità di taglio molto superiori, anche 300 m/min, però questi creatori non possono avere molti principi, al massimo 2-3, perché devono avere un angolo di filetto non superiore a 3 – 5 °. Infatti il Metallo Duro può essere affilato solo con mole in CBN o mole diamantate, che non possono essere modificate sul profilo a ogni affilatura.
Questi creatori in Metallo Duro in genere lavorano a secco anche perché l’eventuale getto dell’olio refrigerante avrebbe difficoltà a raggiungere la zona di lavoro in modo continuo, infatti, l’alto numero di giri del creatore polverizza il liquido refrigerante prima che questo arrivi nella zona di contatto tra utensile e pezzo. Per questo motivo nella lavorazione a umido con creatori in metallo duro si possono raggiungere velocità di taglio mediamente inferiori a quelle raggiungibili con taglio a secco (figura 2). La discontinuità della refrigerazione è particolarmente pericolosa sul Metallo Duro.
I creatori destinati a lavorare a secco devono avere dei solchi di affilatura più ampi e molto ben raccordati in modo da non creare impedimenti al libero deflusso dei trucioli che, essendo incandescenti, sono più plastici e tendono ad incollarsi sulle superfici del solco.
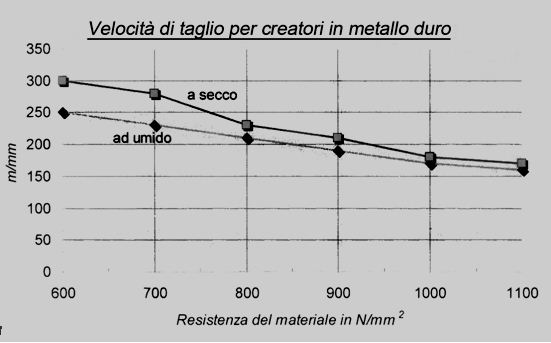
Dentatrici
Le macchine dentatrici che lavorano a secco devono essere strutturate in modo da evitare gli effetti deleteri del calore generato durante l’operazione.
Lavorando a secco ad alte velocità di taglio il truciolo diventa incandescente e deve essere allontanato immediatamente dalla zona di lavoro.
In genere le parti sottostanti la zona di lavoro permettono la caduta per gravità dei trucioli in una vasca di raccolta, da dove vengono allontanati con dei convogliatori.
In alcuni casi si usano anche dei getti di aria compressa per rendere più efficace l’azione di allontanamento dei trucioli.
Durante l’operazione di dentatura, in assenza del liquido refrigerante, si formano delle polveri che devono essere aspirate in modo che non si disperdano nell’ambiente.
Evidentemente le dentatrici che lavorano a secco non hanno vasche dell’olio, mancano gli impianti di raffreddamento e i sistemi di filtraggio dei liquidi, in sostanza sono più semplici e meno costose anche se sono progettate per lavorare con un alto numero di giri del creatore.
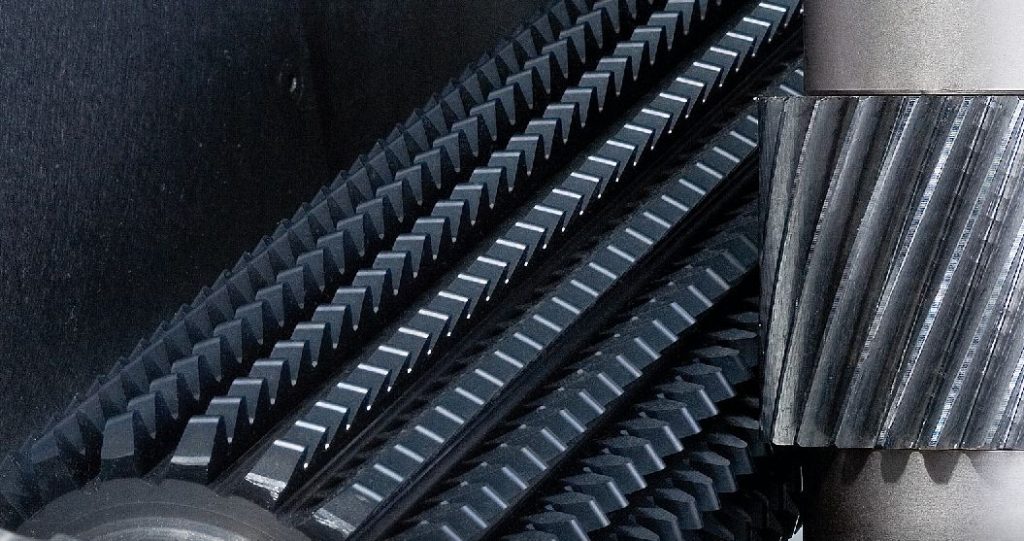
In sintesi
In considerazioni di quanto sopra esposto, la domanda è: perché in certe lavorazioni si preferisce lavorare a secco? La risposta ovvia è che in certi casi è più conveniente l’abolizione del lubrorefrigerante.
Nel taglio a secco si usano quasi esclusivamente creatori in Metallo Duro che permettono velocità di taglio almeno doppie di quelle consentite dai creatori in HSS. È vero che l’avanzamento per giro pezzo deve essere minore, ma in ogni caso il tempo di taglio è nettamente inferiore e anche la qualità della superficie dei denti è migliore.
Se in una certa realtà d’officina la riduzione del tempo ciclo è molto importante, come per esempio nelle produzioni di grandi serie, oppure per adeguare il tempo di dentatura alla cadenza della linea di produzione, oppure ancora per evitare l’acquisto di una nuova dentatrice, allora è preferibile accettare un costo utensile per pezzo un po’ maggiore e scegliere i vantaggi che un tempo ciclo minore può dare.
Sull’impiego dei creatori in HSS bisogna notare che le cose sono molto migliorate perché non è più necessario usare fluidi da taglio derivati da oli minerali, con tutte le problematiche a loro legate.
Sono sempre più diffusi i lubrorefrigeranti su base di esteri vegetali che hanno caratteristiche tecniche migliori e sono biodegradabili e quindi non sono soggetti alle stringenti normative per il loro stoccaggio e impiego.