Nelle lavorazioni meccaniche, la corretta gestione dei trucioli è molto importante ai fini della regolarità del funzionamento delle linee di produzione o delle singole macchine operatrici
Nelle lavorazioni dell’acciaio con elevate velocità di taglio e con utensili di forma normale, si produce di solito un truciolo fluente che, non soltanto è pericoloso per l’operaio ed è di difficile trasportabilità, ma nel suo svolgersi durante il lavoro può danneggiare lo spigolo tagliente.
Inoltre il più delle volte queste lunghe spirali si aggrovigliano tra pezzo, utensile e portautensile utilizzando tempo prezioso dell’operaio che deve far cadere i trucioli nella vasca di raccolta.
Questo problema diventa drammatico se si devono eseguire lavorazioni in ciclo automatico.
L’esecuzione del taglio rompitruciolo o di una scanalatura che convogli i trucioli in un avvolgimento ordinato è l’accorgimento di maggiore efficacia.
Il primo consiste in un gradino praticato sulla faccia di taglio dell’utensile che ha lo scopo di arrestare il truciolo obbligandolo ad una brusca deviazione e quindi di romperlo.
Si possono praticare diversi tipi di rompitruciolo a seconda delle esigenze e del tipo di utensile.
In alcune lavorazioni il truciolo non è continuo e quindi l’utensile non necessita di rompitruciolo, ma in molti casi sono necessarie egualmente alcune importanti avvertenze per evitare danni alle macchine operatrici o decadimento della qualità del pezzo lavorato.
Verranno presentate nel seguito le caratteristiche che deve avere il rompitruciolo nelle operazioni di tornitura.
Rompitruciolo parallelo
Si trattra in sostanza di un gradino parallelo al tagliente principale. L’angolo di spoglia superiore è in genere uguale a quello della faccia di taglio ma può essere anche diverso. Per esempio, se si vuole semplificare la costruzione dell’utensile e anche la sua riaffilatura, si può saldare la placchetta senza alcun angolo di inclinazione, il quale sarà poi ricavato mediante un appropriato rompitruciolo.
Con questo sistema si evita che – per effetto delle riaffilature – il filo tagliente si abbassi, cosa questa dannosa se la sede del portautensile ha le stesse misure dello stelo, con impossibilità quindi di spessorare l’utensile.
Ma anche negli inserti si pratica normalmente questo sistema, perché l’inserto negativo ha un numero di taglienti doppio di quello positivo. Eseguendo il rompitruciolo con angolo positivo, su un inserto negativo, si aumenta la produttività dell’l’inserto.
Il rompitruciolo parallelo (figura 2) è impiegato principalmente in finitura.
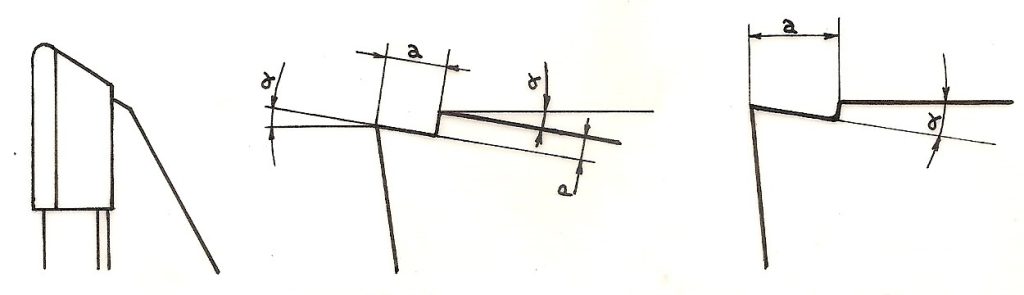
Rompitruciolo angolare
Il tipo angolare è adatto alla maggior parte delle lavorazioni ed è il più difficile da eseguire.
Il truciolo viene piegato verso la zona del pezzo da lavorare dove si rompe senza danneggiare l’utensile.
Con riferimento alla figura 3, il tipo N°1 è particolarmente adatto per operazioni di sgrossatura mentre i tipi N°2 e N°3 sono più idonei a finiture. La sagoma del rompitruciolo può essere semplicemente rettilinea terminante a spigolo vivo oppure, dalla parte del tagliente, può terminare con un piatto q avente inclinazione di 5 – 10° in senso negativo e dall’altra parte può essere raccordato con un raggio da 1 a 1,5 mm.
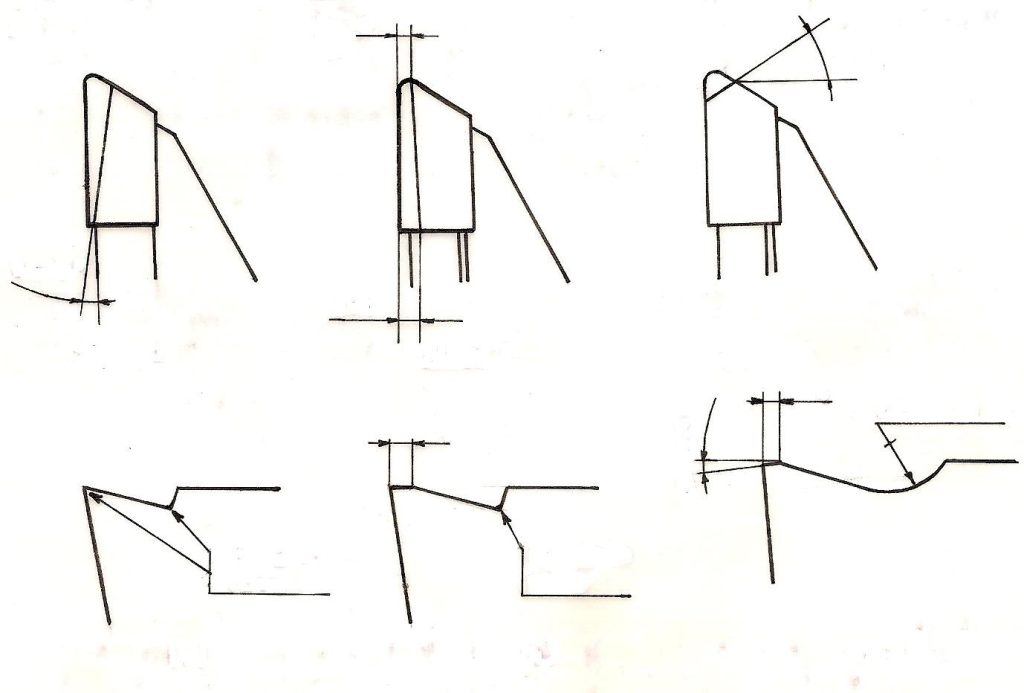
Il primo tipo a spigolo vivo o con q molto piccolo (circa 0,2 mm) è usato per lavori di finitura ed è il vero e proprio rompitruciolo in quanto ha appunto lo scopo di rompere il truciolo; il secondo tipo deve essere considerato un convogliatore dei trucioli perché l’ampio raggio di raccordo quasi sempre facilita l’avvolgimento e non la rottura del truciolo. La profondità p dei rompitrucioli dipende oltre che dal materiale anche dall’avanzamento e dalla profondità di taglio.
Il suo valore può oscillare da 0,4 mm per lavori di finitura a 1 mm per lavori più pesanti. Il quadretto q può avere un valore minimo di 0,2 mm; questo valore può essere aumentato fino ad un valore pari all’avanzamento per giro.
Il quadretto ha lo scopo di aumentare la resistenza agli urti del tagliente e di evitare che questi si scheggi o si deteriori a causa dei trucioli che escono a forte velocità.
Nelle entrate, inoltre, assume un ruolo determinante agli effetti della resistenza alla rottura del tagliente in quanto indirizza lo sforzo di taglio verso lo stelo trasformando la sollecitazione da flessione a compressione.
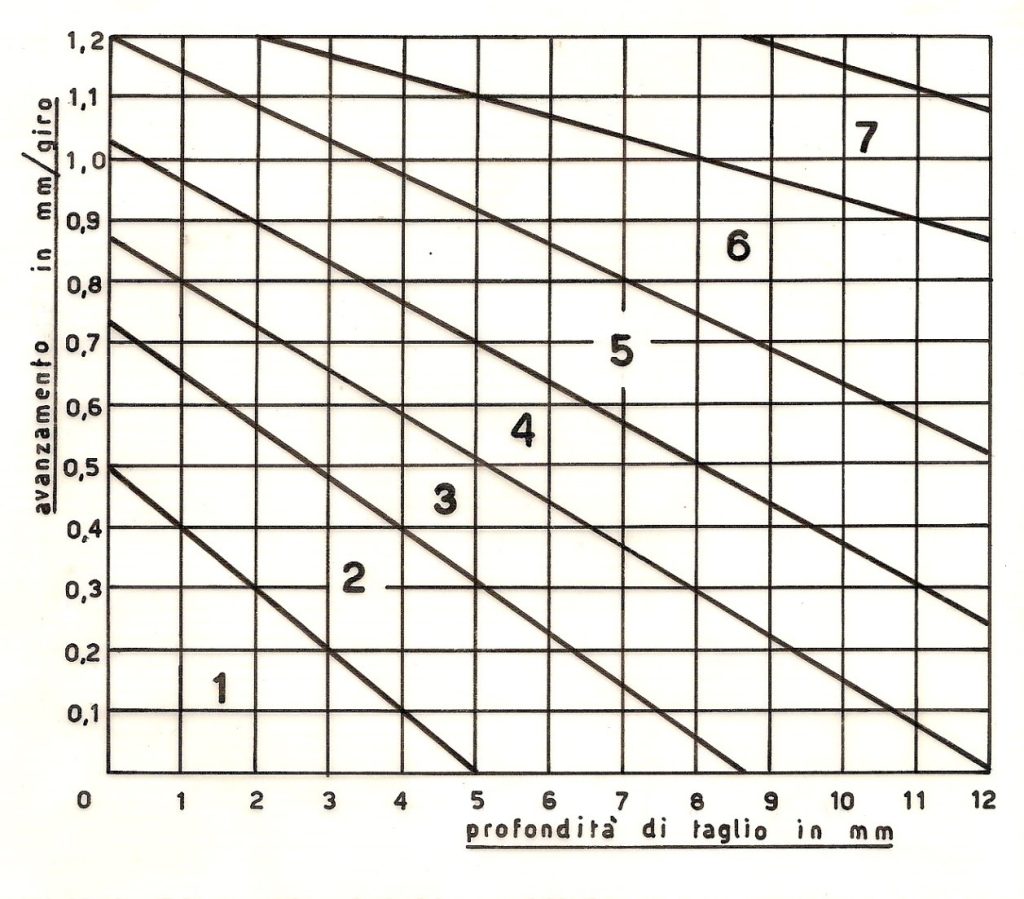
La larghezza e la profondità del rompitruciolo dipendono dalla profondità di taglio, dall’avanzamento e dal materiale lavorato. A tal riguardo, possono essere presi i valori ricavati dal diagramma di figura 4 e dalla tabella 1. In base alle caratteristiche di lavoro si determina sul diagramma il numero della zona; con questo numero e secondo la resistenza del materiale da lavorare si trova, nella tabella, la profondità e la larghezza del rompitruciolo.
Materiale | Numero della zona | |||||||
1 | 2 | 3 | 4 | 5 | 6 | 7 | ||
R fino a 700 N/mm2 | a | 1,0 – 1,5 | 1,5 – 2,2 | 2,2 – 2,8 | 2,8 – 3,5 | 3,5 – 4,5 | 4,5 – 5,5 | 5,5 – 6,0 |
p | 0,4 – 0,5 | 0,5 – 0,6 | 0,6 | 0,6 – 0,7 | 0,7 – 0,8 | 0,8 – 0,9 | 0,9 – 1,0 | |
R fino oltre 700 N/mm2 | a | 0,9 – 1,4 | 1,4 – 2,0 | 2,0 – 2,5 | 2,5 – 3,2 | 3,2 – 4,0 | 4,0 – 5,0 | 5,0 – 5,4 |
p | 0,3 – 0,4 | 0,4 – 0,5 | 0,5 | 0,5 – 0,6 | 0,6 – 0,7 | 0,7 – 0,8 | 0,8 |
L’esecuzione del rompitruciolo è un’operazione delicata che determina il più o meno elevato rendimento dell’utensile. Si impiegano mole diamantate a disco con legante resinoide o vetrificato.
Dopo aver eseguito il rompitruciolo, lasciando il piccolo tratto piano o inclinato in senso negativo q, è utile eseguire due operazioni sussidiarie:
1. Arrotondare il filo tagliente con lima diamantata. Questo arrotondamento potrà accentuarsi verso il fondo del tagliente nella zona di deflusso dei trucioli; gli spigoli vivi del tagliente e la zona di evacuazione dei trucioli sono così notevolmente e razionalmente protetti. Sin tratta di un’operazione molto delicata, difficile soprattutto nel raccordo tra filo tagliente e raggio, la cui buona riuscita dipende esclusivamente dall’operatore e dove un controllo preciso è quasi impossibile.
2. Eseguire uno smusso sullo spigolo della parte frontale del bordo interno del rompitruciolo. Operazione da eseguirsi sempre. Questo smusso ripara enormemente un punto molto vulnerabile dell’utensile e lo preserva dalle rotture che i trucioli con molta facilità possono provocare (figura 5). Sullo stelo deve essere previsto uno scarico allo scopo di evitare che la mola diamantata vada ad intaccare l’acciaio.
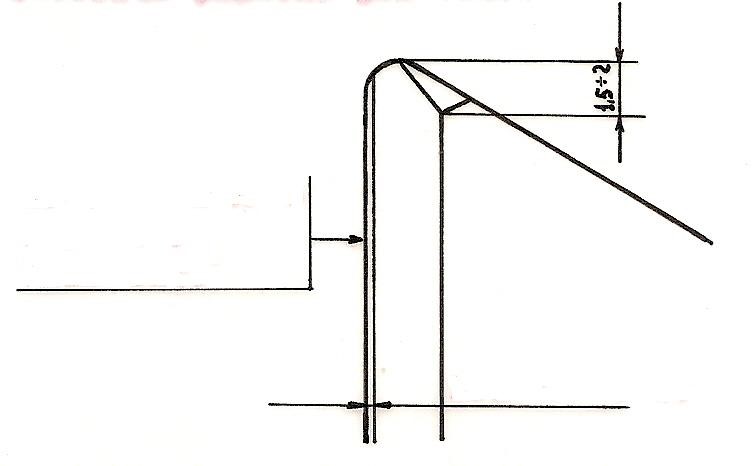
Convogliatore di trucioli (avvolgitruciolo)
È molto usato negli utensili in acciaio rapido (meno in quelli in metallo duro); ha la forma circolare. Alcuni lo chiamano impropriamente rompitruciolo scanalato.
Esso viene ottenuto con una mola a disco sagomata; dal raggio di sagomatura e dalla larghezza dipende la profondità e l’angolo di spoglia superiore.
Con riferimento alla figura 6 si può calcolare la profondità con:
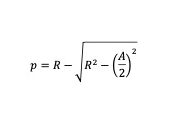
Con l’angolo α che si ottiene con: sin α = A / 2 ・R
Questo genere di avvolgitruciolo è usato nella lavorazione di materiali teneri quali acciaio dolce e leghe leggere dove è necessario ottenere una superficie ben finita. Il diagramma di figura 6 mette in relazione la larghezza, la profondità e l’angolo α.
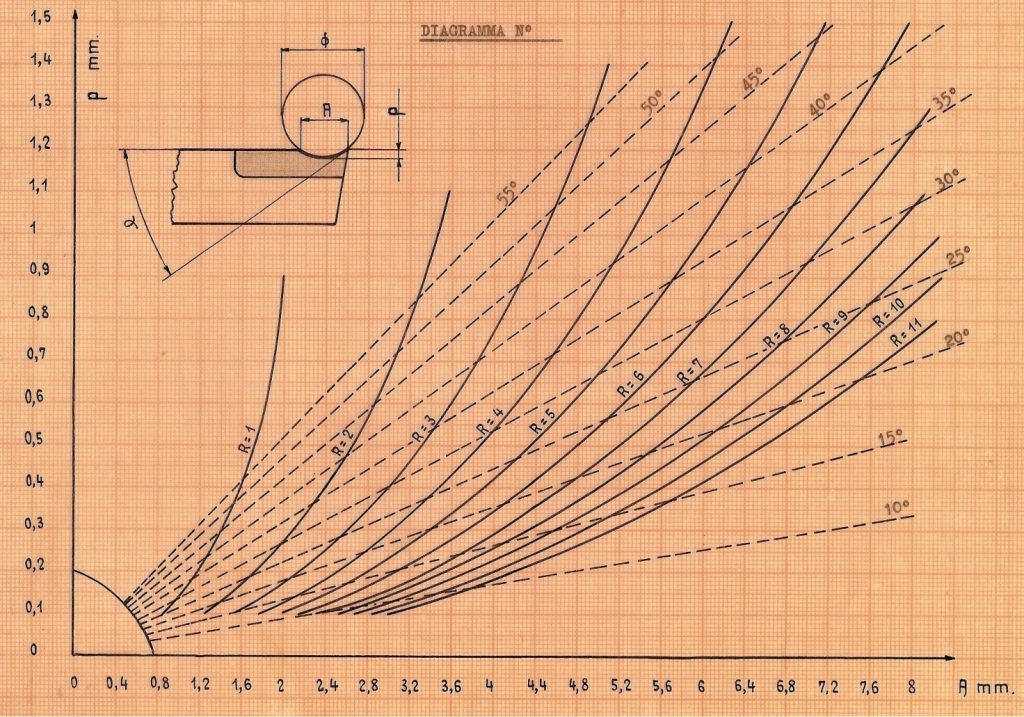
Si è detto più sopra che alcune lavorazioni producono un truciolo non continuo, cioè formato da frammenti più o meni grandi in relazione alle condizioni di lavoro, ma che comunque sono necessarie alcune azioni per rendere l’operazione efficiente.
Vediamo alcuni esempi.
Dentatura con creatore
Nelle moderne operazioni con creatore si è diffusa la dentatura a secco con velocità di taglio molto elevate, anche superiori a 150 m/min.
Con queste modalità i trucioli prodotti sono incandescenti e se non vengono allontanati velocemente dalla zona lavoro surriscaldano parti della macchina con gravi conseguenze.
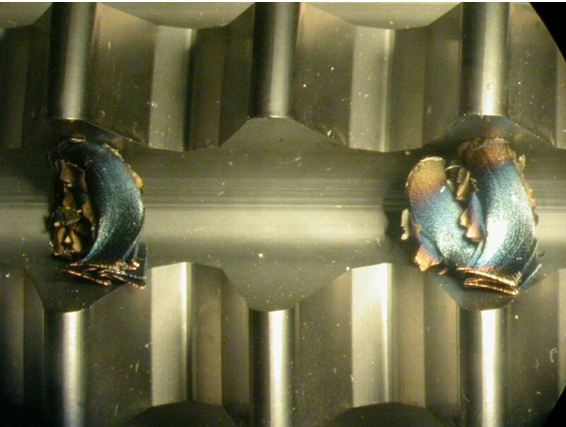
Per questo motivo le dentatrici che lavorano a secco sono strutturate in modo da permettere il deflusso dei trucioli per gravità fino a una canalina di raccolta che li allontanerà velocemente dalla macchina.
Un secondo problema in questo tipo di lavorazione è che, specie con forti avanzamenti per giro pezzo, il truciolo tende ad incastrarsi nel vano tra due denti del creatore, provocandone a volte la rottura. Un esempio è illustrato nella figura 7.
I creatori di questo tipo devono essere costruiti con scanalature di affilatura ampie e raccordate in modo accurato.
Brocciatura
Nella brocciatura di fori cilindrici devono essere eseguiti, sul diametro esterno dei denti, dei rompitruciolo in modo da rompere il truciolo circolare che si formerebbe in loro assenza (figura 8).
La forma e le dimensioni di questi rompitruciolo dipendono dal diametro e della broccia e dalle condizioni di lavoro con cui opera.
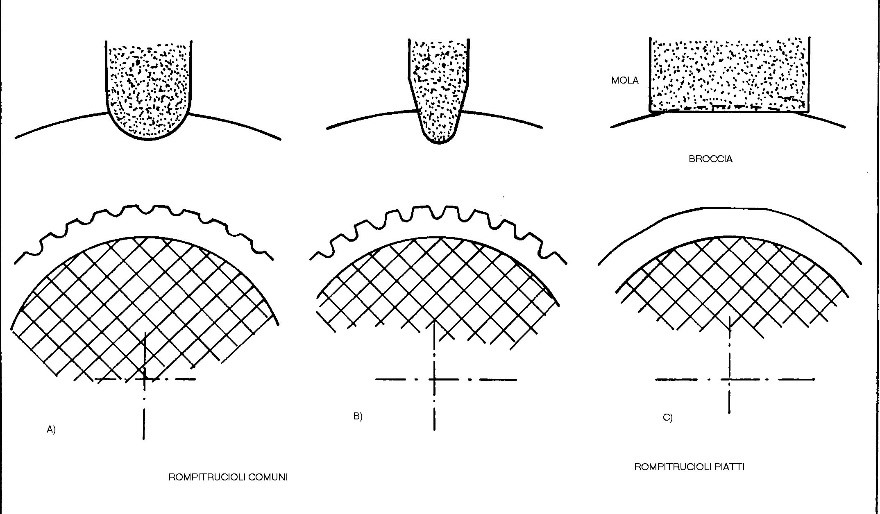
Foratura e maschiatura
In queste due operazioni, se si lavorano materiali molto duttili e con fori profondi, si formano spesso dei trucioli fluenti che si aggrovigliano sull’utensile impedendo in primo luogo al lubrorefrigerante di raggiungere la zona in cui si forma il truciolo, e quindi si ha un aumento della temperatura e la forte possibilità di grippaggio tra utensile e pezzo con conseguente rottura di punte elicoidali e maschi (figure 9 e 10).
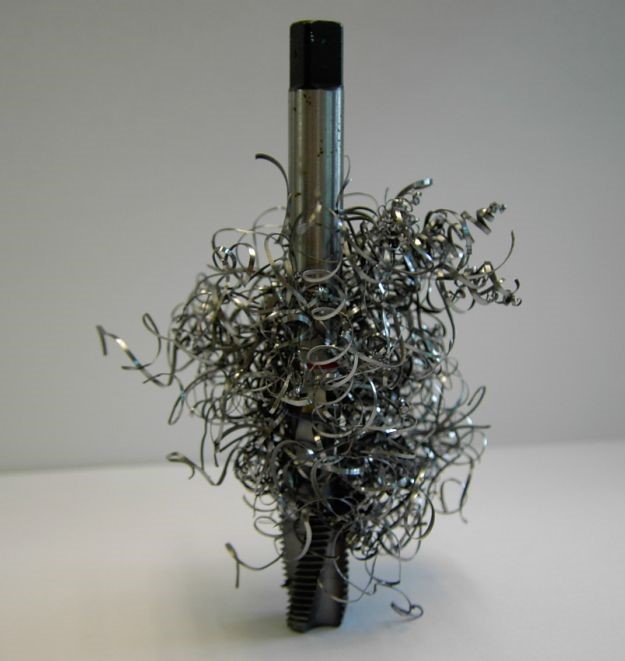
Le soluzioni possono consistere nell’eseguire delle modifiche nel cono di affilatura che fungono da rompitruciolo. Oppure, nel caso di foratura profonda, si interrompe l’avanzamento estraendo la punta elicoidale dal foro parzialmente lavorato in modo da scaricare i trucioli prodotti.
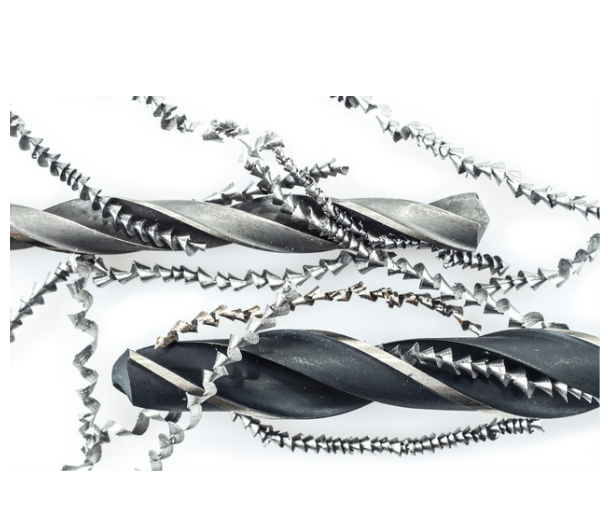
Nella maschiatura invece si eseguono nell’imbocco modifica dell’angolo dell’elica che facilitano la rottura del truciolo o il loro deflusso più ordinato.
Foratura profonda
L’esecuzione dei fori profondi, cioè quelli con lunghezza superiore a 5 volte il diametro, presenta delle difficoltà che non permettono l’uso delle normali punte.
Negli ultimi decenni si sono compiuti enormi progressi nel campo della foratura profonda, soprattutto per quanto riguarda il materiale usato per la costruzione degli utensili e per la tecnica della loro progettazione e realizzazione.
In primo luogo c’è da dire che l’adozione dei carburi sinterizzati (carbide) ha permesso di aumentare in maniera esponenziale la velocità di foratura, ma anche lo studio sistematico della formazione del truciolo, la sua evacuazione e la razionale lubro-refrigerazione, ha consentito un enorme miglioramento dell’efficienza dell’operazione di foratura profonda.
A questo si aggiunge la pratica estesa quasi al 100% delle applicazioni della ricopertura con TiN, TiAlN, TiCN o altri più sofisticati layer.
La vecchia punta elicoidale in acciaio ritorto, con fori di lubrificazione, esiste ancora, ma viene sempre più sostituita con punte in metalli duro, con punte che hanno la placchetta in metallo duro staffata meccanicamente, con punte aventi quattro taglienti e affilature molto elaborate, e che hanno i fori di lubrificazione interni ma con getti indirizzati in direzioni predefinite per facilitare al massimo l’evacuazione dei trucioli (figura 11).
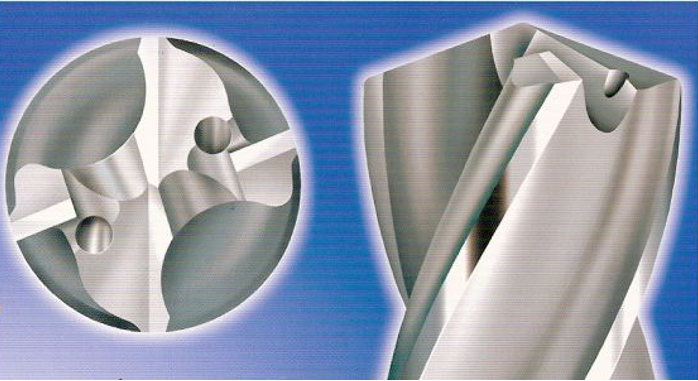
Il liquido refrigerante viene immesso con alta pressione (anche da 40 o 60 bar) per cui oltre a un effetto refrigerante, si determina un flusso di ritorno che facilità l’evacuazione dei trucioli.
Sono disponibili sul mercato i compattatori di trucioli che sono, in sostanza dei tipi di presse che riducono anche del 90% il volume dei trucioli riducendoli in blocchi compatti di piccole dimensioni denominati bricchetti.
I vantaggi ottenuti con questi compattatori sono notevoli: recupero anche del 90% dell’olio che li impregna trasformando il truciolo da rifiuto speciale a rifiuto normale, riduzione dello spazio e maggior facilità di trasporto, possibilità di vendita del metallo recuperato, riduzione del pericolo di infortuni, maggior pulizia e ordine nell’officina.