Kapp Niles, noto gruppo aziendale attivo a livello internazionale nel campo della lavorazione di precisione di ingranaggi e profili, ha posto una “pietra miliare” con la nuova serie KNG 350.
Una storia di successo è stata già scritta con il centro di rettificatura per ingranaggi KX 300 P. Le oltre 500 macchine vendute confermano il successo del concetto che combina alta flessibilità e produttività.
La nuova serie KNG 350 si basa su questo risultato. Nello sviluppo di questa nuova tecnologia, l’azienda ha fatto tesoro dell’esperienza passata, ha adottato e ottimizzato ulteriormente soluzioni collaudate e ha eliminato completamente le lacune esistenti.
Il risultato è un ingegnoso sistema modulare che consente di realizzare diversi concetti macchina su un unico basamento. Grazie a tre diverse configurazioni degli azionamenti degli utensili e del pezzo, le esigenze dei clienti possono essere soddisfatte in modo ottimale.
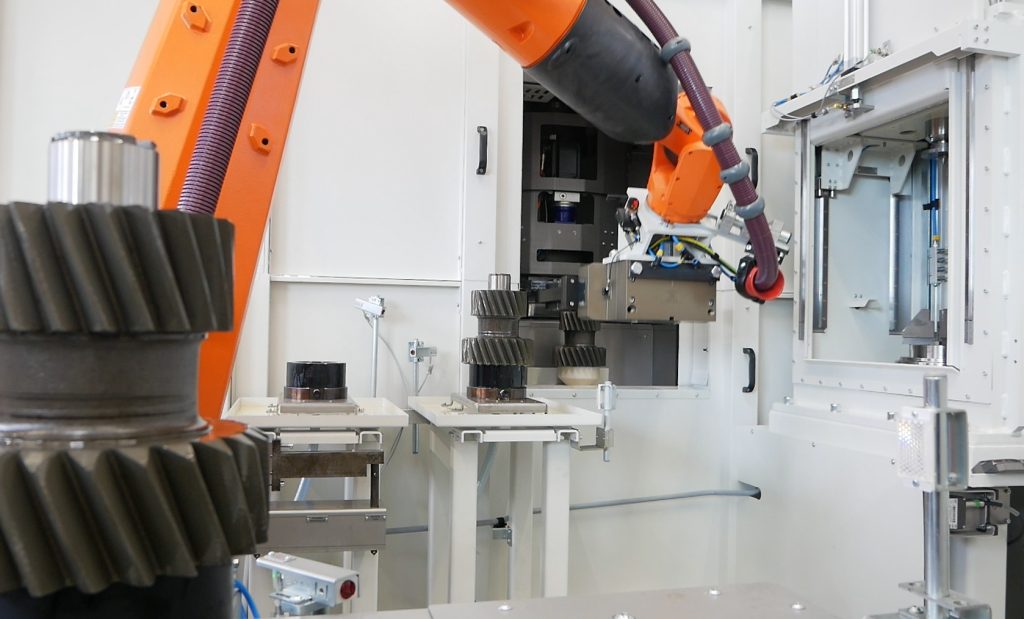
Il concetto macchina
La serie KNG 350 conta su un concetto macchina compatto e ottimizzato per la produzione in piccola e grande serie per pezzi fino a 400 mm di diametro. Il caricatore ad anello integrato garantisce tempi non produttivi estremamente ridotti, fino a 5 sec. e può gestire sia ruote che alberi fino a 600 mm di lunghezza.
Dal caricamento manuale, passando per semplici nastri trasportatori a pallet fino ad arrivare a complesse soluzioni robotizzate, il concetto offre una flessibilità totale nel caricamento dei pezzi da lavorare. Il design funzionale ed ergonomico della macchina, abbinato all’interfaccia utente KN grind, di facile utilizzo, supporta l’impostazione e l’ottimizzazione dei progetti di rettifica.
È stata posta grande attenzione anche sulla riduzione dei tempi non produttivi. Questa serie è caratterizzata da tempi di attrezzaggio ridotti, ottenuti tra l’altro grazie a componenti intelligenti (smart tooling).
Il monitoraggio del processo, la tracciabilità dei pezzi e la garanzia di qualità in linea sono disponibili come parti integranti di un centro di lavoro in grado di operare nel contesto dell’Industria 4.0.
Questa macchina convince non solo per il suo eccellente design (iF Design Award), ma anche per il suo continuo sviluppo nell’ottica dell’efficienza energetica. Le funzioni idrauliche, ridotte al minimo, sono garantite da un’unità di pompaggio controllata, mentre le funzioni pneumatiche sono in gran parte sostituite da azionamenti elettrici. Analizzando il ciclo di vita completo della macchina è emerso che l’intero equivalente di CO2 viene ridotto sostituendo il basamento della macchina in ghisa con un basamento in calcestruzzo polimerico. Si tratta di aspetti che stanno diventando sempre più importanti, soprattutto per gli OEM.
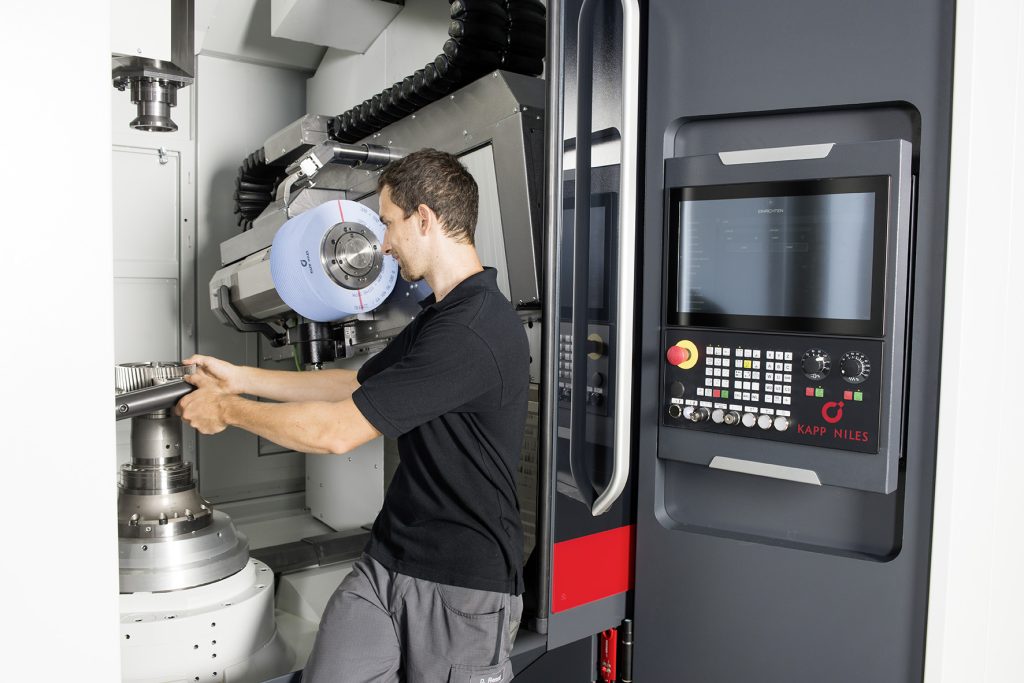
A dimostrazione del gradimento ottenuto merita di essere citata l’opinione di un partner di lunga data, Scania di Södertälije/SE. Anders Urefors, ingegnere responsabile della manutenzione, ha seguito l’evoluzione tecnica a partire dalla KX 300 P. Durante il test tecnico di accettazione della macchina, prima familiarizzazione con la KNG 350, ha mostrato un’espressione soddisfatta. Quello che in passato era customizzato, come il pannello di controllo regolabile in altezza, ora è diventato standard. Anche aprendo la porta lato operatore, oggi si è molto più vicini al pezzo e all’asse porta utensile. Insieme ai sistemi di cambio rapido per attrezzatura dedicata al pezzo, è stato definito un nuovo standard per l’attrezzaggio della macchina. Segno tangibile che l’ergonomia e la praticità d’uso sono state una priorità assoluta nelle scelte per lo sviluppo di questa macchina. «Lesson learned», è stato il commento dello svedese, di norma piuttosto riservato, accompagnato da un sorriso compiaciuto. Miglior verdetto non poteva esser pronunciato: per tutti fu chiaro che l’approvazione di Anders era o meglio è la soddisfazione di Scania.
KNG 350 expert
La nuova serie è stata lanciata con la macchina KNG 350 expert, focalizzata esclusivamente sulla rettifica a generazione di ingranaggi. Il concetto del mandrino di rettifica senza contro-supporto ha già dato prova di sé sulle macchine DYNAMIC. L’interfaccia automatica HSK consente un cambio utensile semiautomatico, che viene implementato anche nelle altre varianti di questa serie. La macchina è dotata di notevoli opzioni tecnologiche, ad esempio per rettificare ingranaggi senza svergolamento (Twist/Bias) o per soddisfare requisiti di rugosità più elevati utilizzando mole a vite combinate. Grazie ai processi di ravvivatura selezionabili, è possibile soddisfare tutte le esigenze, dalla produzione di singoli pezzi (ravvivatura topologica) alla produzione di grandi quantità (ravvivatura multi-ring). Per tutte le macchine di questa famiglia è disponibile il dispositivo di misura integrato, che consente la misurazione completa degli ingranaggi in macchina e viene utilizzato anche per la misurazione ciclica di aspetti definibili della dentatura.
KNG 350 flex HS
La mobilità elettrica ha portato nuove sfide per la produzione di ingranaggi. L’elevata intensità delle prestazioni in uno spazio compatto nel settore automobilistico e la miniaturizzazione per i sofisticati azionamenti delle biciclette, spesso, comportano geometrie dei pezzi non esattamente favorevoli per la produzione.
Fino ad oggi, la rettificatura di precisione di ruote dentate con piani di spallamento è stata realizzata principalmente mediante rettifica a profilo discontinua o honing.
Il motivo è semplice: le mole a vite a più principi, con un diametro di 300 mm, sono troppo grandi per questi componenti.
Rispetto alla rettifica a generazione in continuo, tuttavia, entrambi i processi presentano svantaggi in termini di produttività, economicità e costanza della qualità. L’unico modo per usare mole a vite di rettifica più piccole, tuttavia, è quello di aumentare il numero di giri per ottenere velocità di taglio elevate con diametri utensili più piccoli. I concetti macchina precedenti non erano progettati per soddisfare gli elevati requisiti dinamici degli azionamenti degli utensili e dei pezzi.
La KNG 350 flex HS è caratterizzata dalla massima qualità di rettifica e produttività, anche quando si utilizzano utensili così piccoli. Grazie a un mandrino di rettifica ad alta velocità (HS) con 25.000 giri/min, è possibile rettificare anche ingranaggi con piani di spallamento con utensili di Ø 55 mm (rettifica a generazione) o 20 mm (rettifica a profilo).
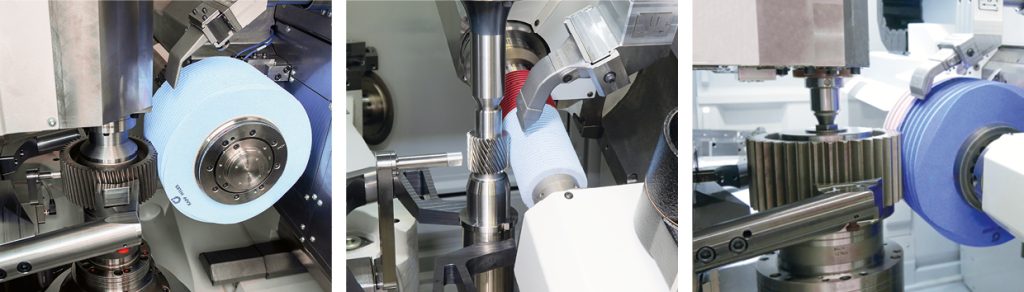
KNG 350 flex
Dato che la gamma di diametri degli ingranaggi tende verso l’alto, in particolare nei veicoli commerciali a trazione elettrica, mentre le classiche ruote dentate per TIR arrivavano a circa 300 mm, i componenti di oggi possono raggiungere i 350 mm, e in alcuni casi anche i 400 mm. La macchina KNG 350 flex copre anche questa grandezza grazie alla possibilità (opzionale) di estendere il diametro.
Il mandrino di rettifica ottimizzato è stato progettato per l’utilizzo di mole a vite di grandi dimensioni con larghezza fino a 200 mm e consente velocità di taglio fino a 100 m/s. Ciò favorisce la lavorazione efficiente di componenti di grandi dimensioni e l’uso di mole a vite combinati per applicazioni di rettifica di finitura o polishing.
Con un utensile standard è possibile ottenere superfici con una rugosità media Rz = 2,5 – 3 µm mediante la rettifica a generazione in continuo. Per requisiti più elevati, si utilizzano utensili combinati con due aree diverse: una con grana standard e un’altra per la rettifica di finitura o polishing, a seconda dei requisiti della rugosità. Sono quindi possibili anche valori di rugosità Rz < 1 µm. L’aumento significativo del rapporto di contatto dei fianchi dei denti aumenta la capacità di carico massima dell’ingranaggio.
Un altro vantaggio di questo processo è che può essere integrato in un processo in sequenza automatizzato con “One-piece-flow”, cosa che non si potrebbe realizzare con il processo a scorrimento usato spesso finora. Punto di forza Kapp Niles è la possibilità di offrire anche il polishing come singola tecnologia, ad esempio per lucidare gli ingranaggi dopo la pallinatura.
Altre due caratteristiche sottolineano la flessibilità di questa macchina.
L’uso di mandrini frontali consente l’utilizzo di mole a profilo molto piccole per un dia. di piede minimo dell’ingranaggio da rettificare. Lo stadio di trasmissione integrato consente una velocità di taglio fino a 50 m/s anche con un diametro mola di 30 mm. Con il dispositivo per la rettifica di interni è possibile lavorare ingranaggi interni ad evolvente e profili speciali. I mandrini frontali e i bracci per interni possono essere montati rapidamente direttamente sul mandrino porta utensile grazie alla nuova interfaccia a cambio rapido.
La rettifica di ingranaggi esterni e interni di pezzi piccoli e grandi può essere realizzata sia mediante rettifica a generazione che rettifica a profilo con utensili ravvivabili e non, a seconda dell’applicazione.
Questo tipo di macchina merita giustamente il nome “flex” e non lascia nulla di incompiuto quando si tratta di rettifica di ingranaggi.