Una panoramica degli approcci di fabbricazione additiva che possono essere utilizzati per la costruzione di macchine elettriche ad elevate prestazioni
Grazie al crescente interesse verso il tema dell’elettrificazione e l’adozione sempre più diffusa di sistemi di propulsione e trasmissione ibridi o full electric in molte applicazioni, la progettazione delle macchine elettriche si trova ad affrontare sfide nuove, in particolare per soddisfare esigenze di prestazione importanti. Questo include, fra il resto, riduzione dei consumi, alleggerimento dei componenti e ridotti rapporti peso/potenza. Ebbene, queste premesse rappresentano una notevole motivazione per esplorare l’impatto dei materiali e delle tecniche di produzione avanzate sulle prestazioni delle macchine elettriche. Vedremo, a tal proposito, una panoramica degli approcci di fabbricazione additiva (additive manufacturing, AM) che possono essere utilizzati per la costruzione di macchine elettriche, con focus specifici sui componenti principali come il nucleo, gli avvolgimenti, i magneti permanenti e i sistemi di raffreddamento. Poiché finora ci sono stati pochi tentativi di applicare l’AM alle macchine elettriche (e ancora meno per quanto riguarda le macchine completamente fabbricate in modo additivo), le sfide e i vantaggi correlati non sono stati compresi in modo esaustivo. A conclusione di quanto vedremo, si capirà come sia certamente possibile realizzare macchine elettriche completamente fabbricate in modo additivo, ma anche saranno più chiari i potenziali miglioramenti delle loro proprietà meccaniche, elettromagnetiche e termiche.
La manifattura additiva di componenti metallici ha registrato un notevole sviluppo negli ultimi anni. Grazie ai vantaggi offerti dalla flessibilità delle geometrie e della riduzione degli scarti di materiale, questa tecnologia ha spianato la strada verso nuove soluzioni progettuali che non sarebbero possibili attraverso le tecniche di fabbricazione convenzionali. Fra le applicazioni più interessanti di questa tecnologia, sebbene non ancora molto diffuse, ci sono quelle relative ai sistemi a propulsione elettrica. È interessante conoscere le soluzioni costruttive già realizzate e testate, le quali riguardano diverse componenti metalliche dei motori elettrici. È anche utile identificare materiali, processi e tecnologie idonei a soddisfare le specifiche dei vari componenti, come proveremo a fare in questo articolo.
L’Industria 4.0 e 5.0 promuovono l’integrazione di tecnologie intelligenti e sistemi di produzione. Tra queste, l’AM svolge un ruolo essenziale nel soddisfare alcuni dei requisiti più importanti della prossima rivoluzione industriale. L’AM, inizialmente utilizzato come strumento personalizzato per la prototipazione rapida, ha vissuto un rapido avanzamento tecnologico e oggi copre una vasta gamma di processi e materiali. Dalle piccole applicazioni alle grandi industrie aerospaziali e della difesa, l’AM è chiaramente uno dei principali motori per le imminenti innovazioni. In questo contesto di sviluppo veloce, l’AM consente una maggiore convergenza tra progettazione e produzione e può aiutare efficacemente i produttori ad approcciare le innovazioni emergenti e gli ultimi sviluppi.
I benefici industriali dell’AM sono riassumibili in questi punti:
1. Produzione per volumi ridotti: l’AM è considerata uno strumento ideale ed economicamente vantaggioso per produrre volumi bassi e parti con geometrie complesse;
2. Ottimizzazione del design e riduzione del peso: benefici molto vantaggiosi anche per applicazioni aerospaziali e spaziali, poiché portano a notevoli risparmi di carburante e riduzione delle emissioni di anidride carbonica;
3. Scarti ridotti: a differenza della produzione sottrattiva, l’AM produce scarti di materiale vicini allo zero;
4. Accorpamento delle parti: è possibile integrare diversi componenti in una singola parte, semplificando e velocizzando le fasi di assemblaggio o riparazione.
L’AM metallico è divenuto recentemente un settore in rapida crescita nell’ambito dei processi additivi. Questo aspetto è misurabile con tre criteri principali di vantaggiosità rispetto alle produzioni metalliche tradizionali (sottrattive o fusione): prestazioni del prodotto, risparmio di tempo e costo di produzione. Quando è stata introdotta per la prima volta, la stampa 3D di metallo era più lenta e costosa rispetto alle tecniche tradizionali esistenti. Di conseguenza, il suo impiego era limitato ad applicazioni in cui il valore finale del prodotto superava gli extra costi di tempo e processo. Dopo anni di evoluzione, ormai la tecnologia di AM metallica può competere in velocità e costo per molti più prodotti che in passato. Per alcuni materiali, come le leghe di titanio e altri metalli duri, addirittura risulta più vantaggioso il processo additivo rispetto a quello sottrattivo per il minore scarto e il costo competitivo degli impianti.
AM in macchine elettriche
Venendo al settore delle macchine elettriche, l’utilizzo di tecnologie additive presenta vantaggi e sfide ancora aperte molto specifiche caso per caso. Ad esempio, per gli avvolgimenti, la sfida tecnologica aperta è di raggiungere una conduttività elettrica sempre più alta, insieme ad elevati fattori di riempimento. Per quanto riguarda il materiale magnetico del nucleo, si continua a ricercare una maggiore permeabilità e minori perdite da correnti parassite in ogni parte stampata. Con i vantaggi della prototipazione rapida e della complessità geometrica, l’AM sta aprendo la strada a diverse innovazioni nella costruzione di svariate parti di macchine elettriche, tra cui anche i sistemi di scambio termico e di raffreddamento, con superfici molto estese racchiuse in piccoli spazi. Inoltre, con il vantaggio della fabbricazione integrata, è possibile progettare motori elettrici interamente costruiti in modo additivo, includendo le restanti parti passive come alloggiamenti, coperchi, albero del rotore e telaio dell’avvolgimento.
Processo AM per macchine elettriche: sheet lamination
A parte i processi di AM più consolidati per i metalli, come quelli basati su letto di polvere (L-PBF, laser powder bed fusion) e deposizione (DED, direct energy deposition), il processo additivo basato sulla crescita per impilamento e incollaggio di lamine metalliche (sheet lamination 3D printing) è meno conosciuto, sebbene importante per la realizzazione di motori elettrici e per costruire nuclei in ferro laminato. Il metodo deriva direttamente dai primi processi di prototipazione rapida, che utilizzavano la carta in modo analogo. Ora è possibile utilizzare rame e acciaio in forma laminare per crescere oggetti 3D. La figura 1 mostra lo schema del processo, che include alcuni passaggi fondamentali:
1. Il materiale metallico, in forma di lamina, viene posizionato sul piano di taglio.
2. Il materiale viene incollato tramite applicazione di pressione e calore sul precedente strato, utilizzando un rivestimento adesivo termico, che può anche fornire isolamento funzionale tra i vari strati.
3. La forma richiesta per ciascuno strato viene tagliata dalla lamina, mediante un laser al biossido di carbonio.
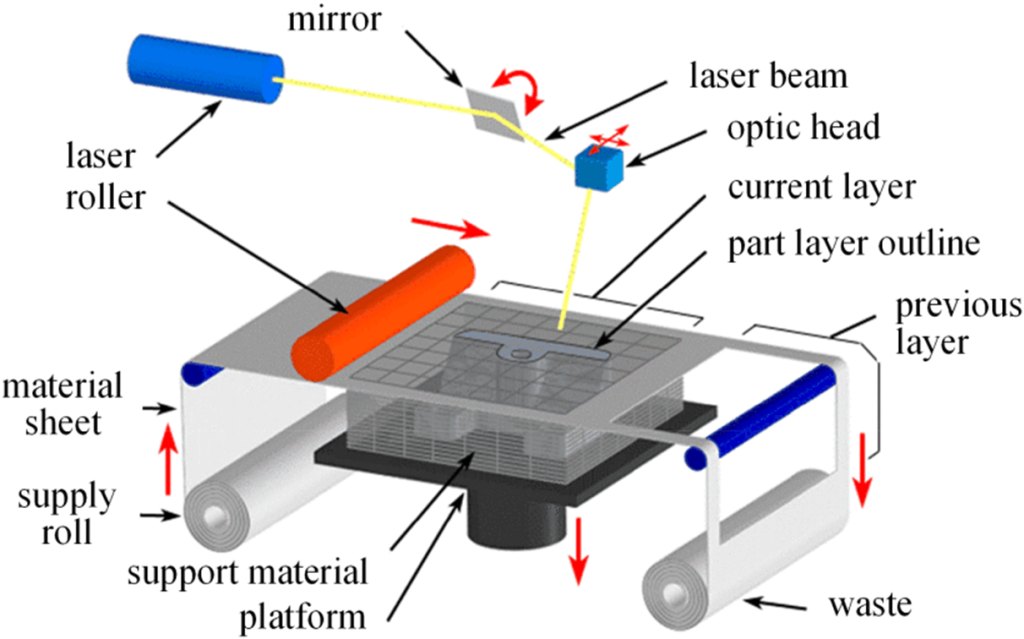
Realizzazione di parti di motori elettrici con processi additivi
Nucleo
La realizzazione del nucleo in ferro del motore elettrico può essere eseguita efficacemente con processi additivi. In particolare, se le perdite per correnti parassite sono basse, è possibile costruire un nucleo in ferro, strato per strato, mediante L-PBF. Questo processo tra l’altro consente una miscela di diversi tipi di polveri metalliche, come cobalto-ferro (Co-Fe, con alta magnetizzazione) e nichel-ferro (Ni-Fe). In questo modo, come per qualsiasi altra parte prodotta tramite AM, si ottengono caratteristiche interessanti come massa ridotta, geometria complessa, percorsi complessi del flusso magnetico. In questo caso è bene considerare che, poiché il legame coesivo tra gli strati si basa sulla ri-fusione degli strati precedenti, la lega metallica finale sarà asimmetrica a livello microscopico. Questa caratteristica potrebbe avere effetti sulla resistenza meccanica e sull’affidabilità del nucleo in ferro qualora venisse sottoposto a sforzi di taglio. Proprio per approfondire questi aspetti, legati alla non uniformità e alla natura eterogenea dei nuclei di rotore fabbricati in modo additivo, sono stati svolti studi mediante analisi agli elementi finiti. Sembrerebbe che, all’aumentare della velocità angolare del motore, le interfacce fra gli strati depositati in modo additivo danneggino più velocemente rispetto al nucleo laminato impilato. E’ comunque un settore che richiede ulteriori studi, specialmente per i rotori ad alta velocità.
Oltre alle proprietà meccaniche, le proprietà magnetiche dei materiali fabbricati in modo additivo possono essere potenzialmente migliorate rispetto ai materiali convenzionali. Alcuni studi mostrano che è possibile creare una texture cristallografica nell’acciaio inossidabile anisotropo mediante il processo L-PBF. La texture cristallografica può essere controllata deliberatamente dalla potenza e dal percorso del laser impiegato nel processo di microfusione delle polveri metalliche, con il quale viene cresciuto in 3D il nucleo stesso. È possibile produrre un nucleo in acciaio ad alto contenuto di silicio, con grani orientati nel modo desiderato, utilizzando il processo a letto di polvere L-PBF. La texture si allinea alla direzione di crescita del pezzo e può essere modificata variando l’energia del fascio laser. La microstruttura può essere inoltre modificata e migliorata con trattamenti termici sui pezzi prodotti. Come è ovvio, la progressiva comprensione di questi meccanismi di processo stanno portando verso una adozione sempre più ampia di nuclei in ferro da L-PBF.
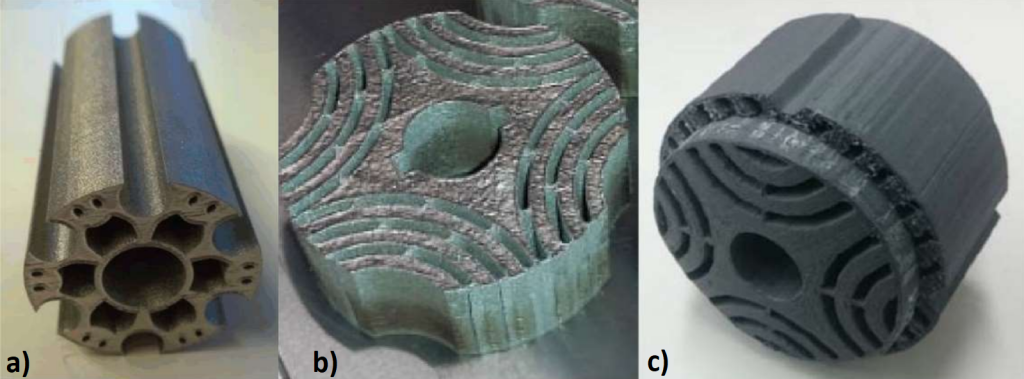
Un attuale limite del processo additivo riguarda la risoluzione dimensionale, non sufficiente per realizzare nuclei di alta precisione. Nei processi L-PBF, tipicamente, lo spessore del layer è intorno a 0.02 mm, mentre la risoluzione nel piano è di 0.3-0.4 mm. Di contro, la risoluzione di un taglio laser tradizionale può essere di 0.025 mm o anche inferiore, con una tipica finitura superficiale di 0.003-0.006 mm.
Per il nucleo dei motori elettrici, di solito si impiegano materiali magnetici morbidi con alta permeabilità magnetica. Il materiale magnetico più comune utilizzato a questo scopo è costituito da lamine impilate di sottili fogli (spessi 0.1-0.5 mm) di leghe ferro-silicio (Fe-Si), che possono fornire un mezzo efficace per il trasferimento di energia. Nelle applicazioni ad alta potenza, queste lamine devono fornire lo stesso flusso magnetico ma con meno materiale nel rotore e nello statore e l’AM può rispondere ad alcune di queste esigenze. Oltre ai già citati punti di forza, l’AM metallico può fornire i seguenti benefici aggiuntivi per la fabbricazione del nucleo dei motori elettrici:
– è possibile unire piuttosto agevolmente materiali diversi sotto forma di polvere metallica per controllare le proprietà magnetiche finali (magnetizzazione ad alta saturazione, perdite di flusso, etc.) Esempi di tali miscele sono leghe ferro-cobalto e nichel-ferro;
– l’AM metallico consente la costruzione di un percorso di flusso complesso, grazie ai minori vincoli sulle dimensioni e geometrie rispetto alle tradizionali lamine;
– l’integrazione dei canali di raffreddamento con il nucleo della macchina è più facile;
– l’AM metallico può anche risolvere alcune delle problematiche meccaniche delle parti mobili della macchina elettrica, controllando la microstruttura del materiale, pesi, resistenze strutturali, etc.
La figura 2a mostra un rotore per motore elettrico con 6 slot ad alta saturazione di flusso realizzato con polvere Fe-Co mediante processo additivo a letto di polvere (L-PBF). La densità di flusso magnetico in questo prototipo ha raggiunto un livello di 2.3 T. Nella figura 2b, è mostrato invece un prototipo di nucleo a barriera di flusso, che affronta congiuntamente gli aspetti meccanici ed elettromagnetici; si vedono presenti nello stesso componente anche “ponti” non magnetici collegati alle altre parti magnetiche. In figura 2c si mostra infine una soluzione basata su AM per la costruzione sia di statore che di rotore in una macchina a riluttanza sincrona per avviamento in linea.
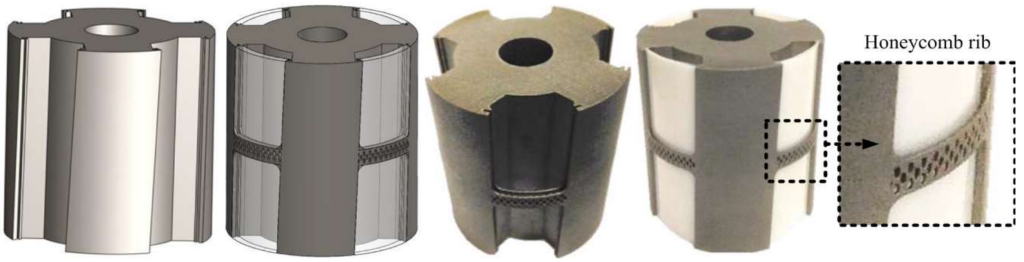
Nella soluzione mostrata in figura 3 (Tseng et al., 2016) si vede un rotore inclinato con struttura a nido d’ape, molto difficile da realizzare con metodi convenzionali, che consente una riduzione del 45% del momento torcente agente sul componente. La fabbricazione additiva consente anche l’adozione di strutture a “nido d’ape” che alleggeriscono il rotore.
Altre soluzioni costruttive basate su AM, mostrano rotori di forme elaborate per ottimizzare il funzionamento del motore. Alcune soluzioni presentano rotori cavi per ridurre peso e inerzia del rotore, oppure l’utilizzo di zone di transizione coniche tra la parte attiva e i cuscinetti. Con questi accorgimenti si documentano riduzione del peso del rotore del 50%, un’accelerazioni maggiori del 10% da fermo alla velocità nominale. Il momento torcente medio del motore aumenta (5% circa) e la coppia di spunto si riduce notevolmente (90%).
Sono state inoltre sviluppati nuovi concetti per soluzioni innovative e nuove classi di motori elettrici, come quello mostrato in figura 4 (Hosek et al., 2016). A differenza degli approcci convenzionali a flusso radiale o flusso assiale, questa macchina ha un percorso di flusso magnetico tridimensionale. Utilizzando l’AM, questa macchina è stata costruita utilizzando materiale magnetico morbido, che consente di ottenere motori più piccoli e leggeri, con una potenza di uscita superiore e una migliore efficienza energetica (densità di potenza del 40% superiore e perdite inferiori del 15%).

Compositi magnetici
I compositi magnetici (soft magnetic composites, SMC) costituiti da piccole particelle di ferro isolate, e i relativi processi di lavorazione della polvere metallica (compattazione, indurimento, ecc.) sono stati proposti per la costruzione dei nuclei in ferro delle macchine elettriche dotati di struttura complessa e percorsi di flusso magnetico tridimensionali. Rispetto alle tradizionali lamiere di acciaio al silicio e ai relativi processi, come la punzonatura, l’impilamento, la rivettatura e la saldatura, le caratteristiche interessanti del nucleo in ferro basato su SMC includono queste interessanti proprietà:
1. Riduzione delle perdite per correnti parassite nelle direzioni di magnetizzazione tridimensionale grazie ad alcune sue proprietà (isotropia magnetica) molto positiva per diverse tipologie di macchine, come macchine a flusso trasversale e a flusso assiale.
2. Bassa perdita specifica del nucleo a frequenze elettriche superiori a 500 Hz grazie all’elevata resistività elettrica specifica.
3. Con tecniche di lavorazione della polvere metallica ben consolidate, è possibile realizzare componenti a basso costo e di forma netta, anche con struttura complessa.
4. Utilizzando tecniche di compattazione e l’indurimento, non vi sono deterioramenti delle proprietà magnetiche/meccaniche dovute al processo di fabbricazione.
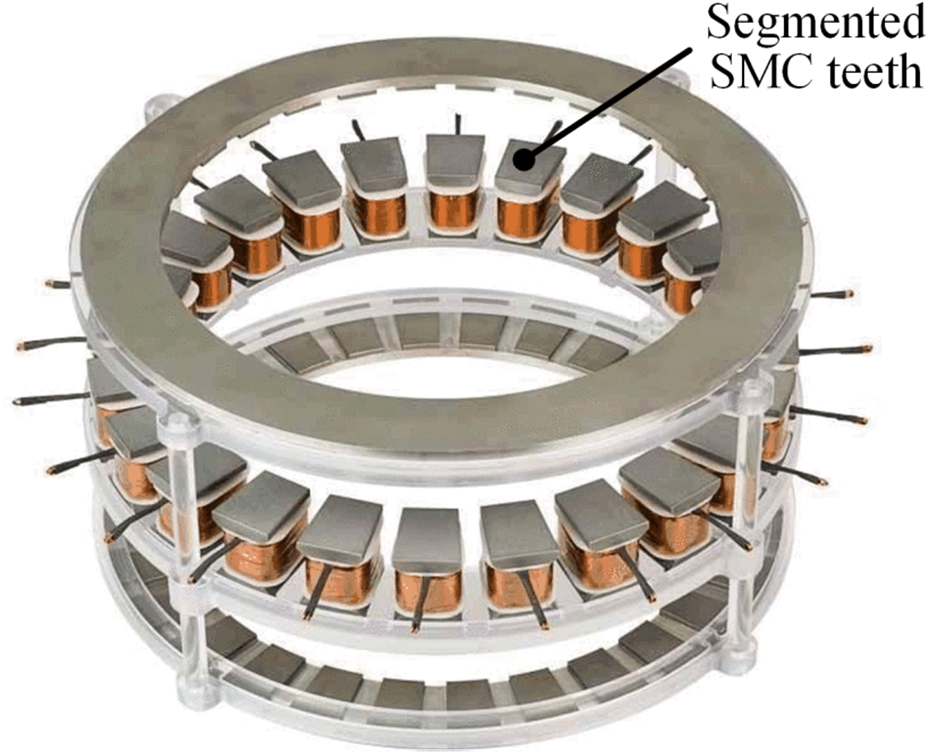
Anche se la resistenza meccanica e la permeabilità di SMC sono inferiori rispetto alle lamine di acciaio al silicio impilate, negli anni la loro produzione e applicazione sono cresciute in modo significativo. Per esempio, Hoganas ha sviluppato una serie di materiali SMC per applicazioni elettromagnetiche in cui si applicano pressioni di compattazione di 600-800 MPa e trattamenti termici a 650 °C. La figura 5 mostra un esempio di macchina a flusso assiale con nuclei in ferro SMC.
Avvolgimenti
L’implementazione dell’AM metallico per gli avvolgimenti dei motori elettrici è ancora nelle sue fasi iniziali. Tuttavia questi processi possono offrire soluzioni progettuali innovative specialmente per i motivi qui riportati:
– grazie alla flessibilità geometrica dell’AM, l’area della sezione trasversale della bobina può essere progettata con un fattore di riempimento dello slot più elevato e un miglior comportamento termico;
– le estremità dell’avvolgimento possono essere personalizzate fino al 50% della loro lunghezza, accorgimento che consente una notevole riduzione del peso e del volume della macchina;
– alcune tecniche di fabbricazione consentono la stampa dell’avvolgimento e dell’isolamento contemporaneamente;
– è possibile raggiungere temperature di funzionamento più elevate utilizzando materiali resistenti alle alte temperature sotto forma di polvere ceramica anziché utilizzare rivestimenti successivi come smalto, resina e polimeri. Il trattamento di materiali come la ceramica utilizzando metodi convenzionali è difficile a causa del punto di fusione elevato;
– è possibile controllare le proprietà elettriche degli avvolgimenti, come la conducibilità, adattando la microstruttura del materiale o mescolando materiali diversi.
Osservando alcuni esempi costruttivi di avanguardia, si può ad esempio citare la soluzione di Additive Drives, che ha sviluppato un avvolgimento a bobina singola stampato in 3D ad alte prestazioni per un motore da competizione (figura 6a). Con un perfetto adattamento geometrico, le bobine hanno un fattore di riempimento massimo del rame e il design consente il trasferimento forzato del calore dall’avvolgimento al nucleo laminato, prevenendo la formazione di punti caldi. Di conseguenza, la densità di potenza dichiarata aumenta del 45%. L’isolamento delle spire viene realizzato in una fase di post-processo separata. Un’altra soluzione analoga (Travitzky et al., 2014) mostra bobine distribuite a forcina e stampate in 3D per motori automobilistici a “E-traction” (figura 6b). In questo motore, i tradizionali fili di rame avvolti sono sostituiti da barre rettangolari di rame con sovrapposizione delle spire solo su metà altezza della testa. Con questa soluzione viene dichiarato un aumento della coppia del 30% a parità di volume occupato.
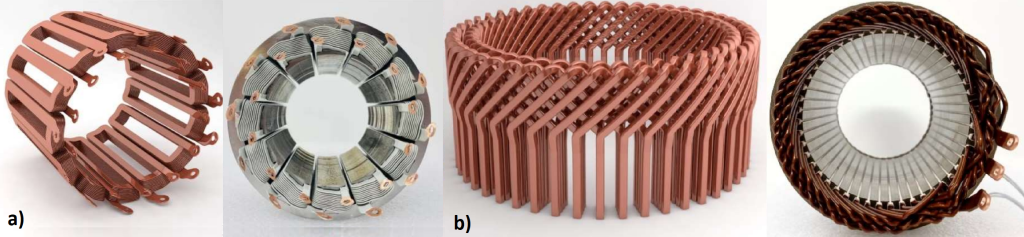
Scambiatori di calore
La diffusione dei veicoli elettrici sta promuovendo la produzione di motori elettrici ed elevata densità di potenza. Di conseguenza, i progettisti devono trovare soluzioni di raffreddamento molto performanti dal punto di vista dell’efficienza termica, dell’uniformità della temperatura, delle dimensioni, del peso e del costo. Ecco perché la libertà geometrica offerta dall’AM ha un ruolo importante nello sviluppo delle nuove soluzioni per il raffreddamento dei motori elettrici.
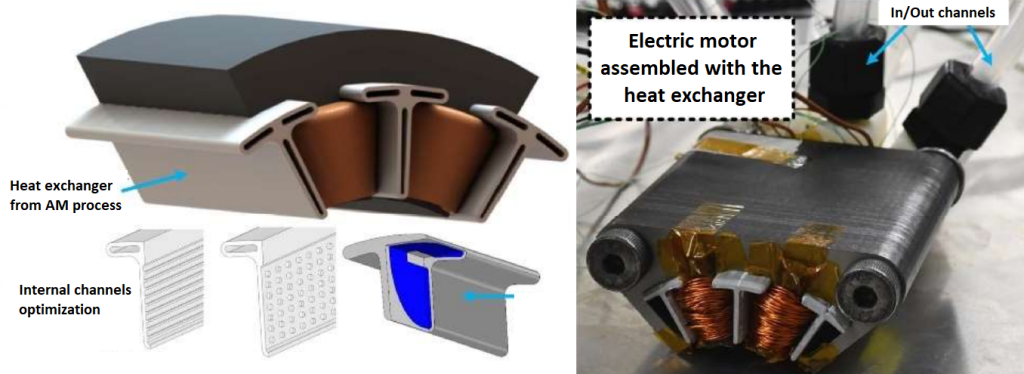
Alcuni design prevedono, ad esempio, di raffreddare gli avvolgimenti attraverso scambiatori di calore in ceramica stampati in 3D e collocati in modo da occupare lo spazio inutilizzato tra gli avvolgimenti stessi (Sixel et al., 2019). In questo modo, la densità di potenza del motore aumenta senza influenzare il design elettromagnetico. La geometria dei micro-canali interni è ottimizzata secondo diverse forme per un raffreddamento ottimizzato, supportato da modelli fluidodinamici. In questa soluzione, viene dichiarata una riduzione della temperatura dell’avvolgimento del 44% grazie allo scambiatore in AM, e una densità di corrente continua di 35.7 A/mm2 viene raggiunta mantenendo la temperatura massima dell’avvolgimento al di sotto dei 200 °C.
Conclusioni
La maggior parte degli esempi menzionati dimostra un alto livello di maturità avanzato, con un miglioramento delle prestazioni dei motori elettrici tradizionali. Alcune applicazioni possiedono effettivamente buoni riscontri termici uniti a riduzione di massa. Restano aperte alcune questioni di ricerca, che potranno condurre ad ulteriori miglioramenti nell’utilizzo dei processi additivi per la produzione di motori elettrici, come ad esempio la possibilità di fabbricare parti multi-materiale per motori ad elevate prestazioni elettromagnetiche (avvolgimento insieme all’isolamento o al nucleo), oppure l’impiego di nuovi materiali magnetici o leghe con elevata permeabilità magnetica.
Giorgio De Pasquale Dipartimento di Ingegneria Meccanica e Aerospaziale, Politecnico di Torino, Smart Structures and Systems Lab