Una guida passo-passo, partendo dalla documentazione iniziale fino ai test finali per essere certi che la propria macchina sia effettivamente a norma.
La prima cosa che bisogna fare per affrontare le sfide dell’adeguamento della pressopiegatrice è quella di partire dalla documentazione che abbiamo a disposizione relativamente alla macchina in oggetto e creare un dossier iniziale che ne verifichi la completezza documentale.
Il manuale di istruzioni è un punto di partenza per identificare il macchinario: in esso possiamo trovare lo schema idraulico, lo schema elettrico e le eventuali soluzioni adottate dal costruttore per evitare gli infortuni.
Se tale manuale non fosse disponibile la targa sulla macchina potrà essere d’aiuto per individuare il costruttore a cui poterne richiedere una copia. Dalla targa si evince l’anno di costruzione dalla quale si potrà stabilire se la macchina è marcata CE oppure no, se invece la stessa è stata acquistata da un rivenditore che l’ha immessa nel mercato, sarà quest’ultimo che potrà dare le indicazioni in merito.
Ricordiamo che dal lontano 1955, con il DPR 547, di adempimenti ne sono stati imposti tanti, e di seguito faremo il punto per individuare le date salienti.
Nel 1955 nasce il DPR 547 che parla di dispositivi “scansamano” e di fotocellule monoraggio a infrarosso.
Di seguito, è riportato un estratto del DPR 547, dove si sono riportate le prescrizioni del 1955:
«Le presse, le trance e le macchine simili, debbono essere munite di ripari o di dispositivi atti ad evitare che le mani, o altre parti del corpo dei lavoratori, siano offese dal punzone o da altri organi mobili lavoratori.
Tali ripari o dispositivi, a seconda del tipo della macchina o delle esigenze della lavorazione, possono essere costituiti da:
a) schermi fissi che permettano il passaggio dei materiali nella zona di lavoro pericolosa, ma non quello delle mani del lavoratore;
b) schermi mobili di completa protezione della zona pericolosa, che non consentano il movimento del punzone se non quando sono nella posizione di chiusura;
c) apparecchi “scansamano” comandati automaticamente dagli organi mobili della macchina;
d) dispositivi che impediscano la discesa del punzone quando le mani o altre parti del corpo dei lavoratori si trovino in posizione di pericolo.
I dispositivi di sicurezza consistenti nel comando obbligato della macchina per mezzo di due organi da manovrarsi contemporaneamente con ambo le mani possono essere ritenuti sufficienti soltanto nel caso che alla macchina sia addetto un solo lavoratore.
I suddetti ripari e dispositivi di sicurezza possono essere omessi quando la macchina sia provvista di apparecchi automatici o semi-automatici di alimentazione».
Nel 1996 nasce la Direttiva Macchine che impone ai costruttori di pressopiegatrici di seguire le indicazioni relative alla sicurezza attraverso l’uso delle fotocellule monoraggio laser.
Nel 2000 nasce il Comitato Tecnico Europeo con le mansioni di legislatore; dalle direttive per la sicurezza delle pressopiegatrici prendono forma una serie di adempimenti che daranno poi luogo alla nascita del Pr En 12622 che prendono in considerazione le mutiraggio laser e le barriere da 800 mm, come soluzione ai pericoli di schiacciamento.
Nel 2002, l’organo Ispsel, attraverso un gruppo di ingegneri facenti parte delle maggiori case costruttrici italiane, sente il bisogno di fare chiarezza su come e cosa poter mettere in atto per adeguare in maniera sicura una pressopiegatrice. In questo contesto escono di scena le fotocellule monoraggio e prendono piede le barriere da 800 mm e le fotocellule multiraggio applicate sotto al punzone.
Nel 2004, la proposta di norma Pr En12622 diventa norma tecnica EN 12622, la quale impone come norma tecnica verticale di tipo c una serie di prescrizioni relative alla sicurezza delle pressopiegatrici e soluzioni pratiche circa i dispositivi di sicurezza che devono essere usati per garantirne la sicurezza; viene introdotto il concetto di pedale a tre posizioni, di ripari laterali e di fotocellule multiraggio installate sotto al punzone della pressopiegatrice congiuntamente a barriere da 800 mm poste sul fronte della macchina da adeguare.
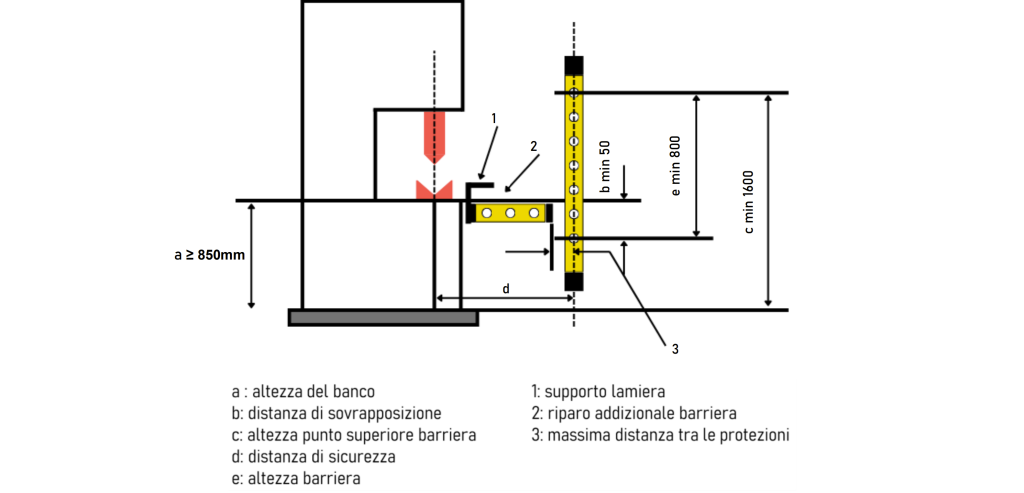
Nel 2010, la norma EN 12622 si evolve e fa chiarezza sull’uso di alcuni comandi che in precedenza non erano stati trattati correttamente; a questo punto va in disuso l’utilizzo del comando a due mani e viene chiarito il ciclo di piegatura relativo alla gestione del “mouting“.
Nel 2014, la norma EN 12622 si stabilizza all’ultima versione disponibile e vengono ulteriormente puntualizzate le tecniche di sicurezza da applicare sulle pressopiegatrici di ultima generazione; praticamente tutti i costruttori accettano la soluzione delle multiraggio laser applicate sotto a punzone e prende il via tale filosofia di sicurezza che invade il mercato attraverso 3 costruttori principali: uno italiano, uno tedesco e uno australiano.
Nel periodo compreso tra il 1955 e il 2014, si assiste all’evoluzione dei sistemi di sicurezza che le pressopiegatrici hanno subito nel tempo, passando da semplici fotocellule a infrarossi a complicati sistemi di sicurezza di ultima generazione in grado di controllare con precisione millimetrica la zona di lavoro; possiamo quindi affermare che se un’azienda si avvale di un dispositivo monoraggio come ausilio per la sicurezza, sta commettendo un grave e rischioso inadempimento alle normative per la sicurezza che potrebbe causare, oltre a gravi infortuni, non trascurabili strascichi legali, dal momento che tale dispositivo è considerato ormai da circa 25 anni, non più allo stato dell’arte.
Per quanto sopra detto, si ribadisce il concetto che, se sul proprio macchinario è presente questo tipo di fotocellula monoraggio, è fortemente consigliato di aggiornare la stessa con componenti idonei e in conformità alle normative vigenti.
La prima domanda da porsi è relativa al tipo di pezzi che devono essere prodotti con la propria macchina. Se, per esempio, si devono costruire pezzi piani di grosse dimensioni, la scelta potrebbe cadere sulle barriere multiraggio da 800 mm, opportunamente installate a una distanza da calcolare in genere tra i 200 e i 300 mm dal punzone; se invece i pezzi sono piccoli e possono essere anche scatolati, la scelta non ha alternative perché sicuramente necessita di una multiraggio laser applicata sul punzone che scende e, al punto di contatto con la lamiera, entra in mouting per permettere al punzone di penetrare nella lamiera e finire il ciclo di piegatura.
Suddetto ciclo è citato nella norma EN 12622, la quale descrive esattamente il funzionamento di tali dispositivi.
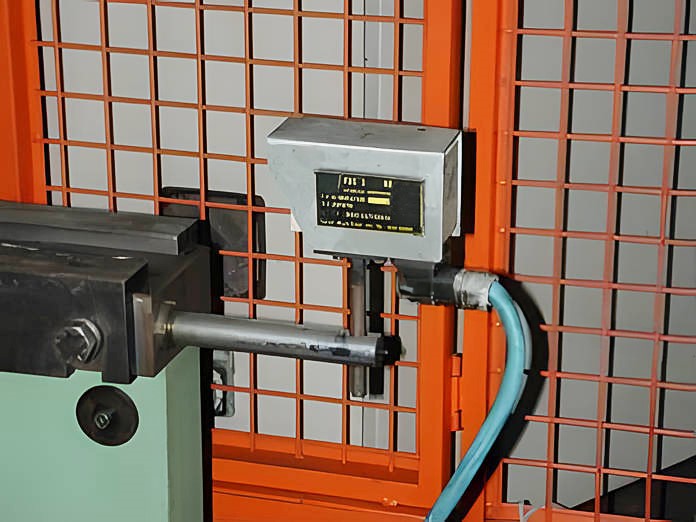
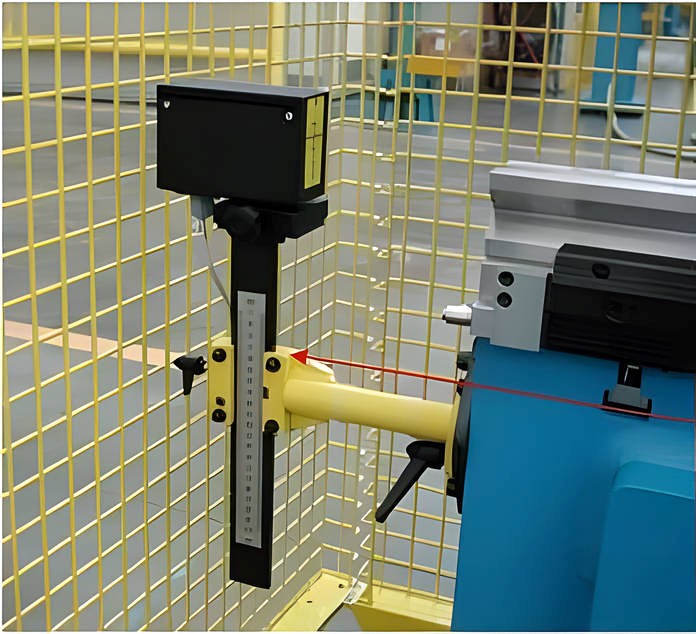
Il funzionamento è ben descritto, e ovviamente un bravo installatore eseguendo collegamenti opportuni, rispetterà tali requisiti; pertanto alla fine di ogni adeguamento sarà necessario farsi rilasciare:
- una dichiarazione di corretta installazione con i relativi schemi elettrici di collegamento;
- un manuale d’uso e manutenzione del dispositivo installato che riporti il corretto posizionamento dei raggi sotto al punzone;
- un documento che riporti i nomi delle persone con le relative firme della formazione avvenuta dopo l’installazione che permette al datore di lavoro di accertarsi che i lavoratori abbiano preso visione di come regolarlo.
I dispositivi AOPD laser sono regolati sotto al punzone attraverso una dima tenendo conto dello spazio di arresto della macchina coinvolta nell’adeguamento delle sicurezze; per questo, un errato posizionamento sotto al punzone può rendere il sistema non sicuro.
Per accertarsi che tale regolazione sia stata messa in atto correttamente, si devono eseguire alcune prove di seguito descritte.
Prova 1
Capacità di rilevamento: controllare la capacità di rilevamento tra la punta del punzone e il fascio laser (più vicino al punzone). La distanza deve essere ≤14 mm lungo l’intera area del punzone.
La prova deve essere eseguita con l’impugnatura (parte cilindrica) del provino.
Prova 2
Un provino di 10 mm di spessore composto da materiale flessibile, per esempio plastica, giacente sullo stampo, non deve essere toccato durante la corsa verso il basso del punzone. Inoltre, un provino di 15 mm di spessore deve passare tra gli utensili.
Prova 3
Un provino di 35 mm di spessore giacente sullo stampo non deve essere toccato durante la corsa verso il basso ad alta velocità della traversa.
Superate queste 3 prove il dispositivo AOPD sarà ritenuto idoneo a elevare la sicurezza sulla macchina testata. Va da sé che tale test deve essere eseguito a ogni cambio utensile.