Perché il test dello spazio di arresto è fondamentale per la taratura dei dispositivi AOPD Laser e deve essere sempre eseguito ad ogni cambio utensile.
Per comprendere questa regolazione introduco un concetto semplice, ma efficace che spiega, in poche parole, lo spazio di arresto. Immagina di viaggiare in autostrada alla velocità di 100 km/h; se improvvisamente avvistassi un ostacolo e azionassi il freno, la tua auto non si arresterebbe immediatamente, bensì proseguirebbe la sua corsa ancora per una certa distanza prima di fermarsi completamente. Questa distanza, percorsa dal momento in cui inizi a frenare fino a quando il veicolo si immobilizza, è ciò che definiamo “spazio di arresto”.
Analogamente, per una pressa piegatrice, il principio è lo stesso. Quando viene impartito il comando di arresto, la pressa piegatrice non si ferma istantaneamente poiché anch’essa necessita di tempo e di spazio per raggiungere la completa immobilità. Tale spazio è influenzato dalla velocità della pressa piegatrice e dall’efficacia del suo sistema di frenata e può prolungare lo spazio di arresto.
È fondamentale conoscere lo spazio di arresto per garantire la distanza di sicurezza attraverso la quale vengono regolati i raggi laser sotto al punzone, assicurando che vi sia un adeguato margine per permettere al macchinario di arrestarsi senza causare danni materiali o lesioni alle persone.
Il calcolo dello spazio di arresto è quindi un elemento fondamentale per garantire la sicurezza degli operatori addetti alla piegatura ed è regolato dalla norma EN 12622. Per calcolare tale spazio abbiamo due soluzioni.
Soluzione 1. Raccogliere dati specifici della macchina
- Velocità di operazione. Determinare la velocità massima con cui la pressa piegatrice si muove durante il suo ciclo di lavoro.
- Tipo di sistema di frenata. Verificare il sistema di frenata utilizzato dalla macchina, che potrebbe essere meccanico, idraulico, pneumatico o elettrico.
Formula di calcolo: la distanza di arresto può essere calcolata usando principi fisici base di moto con decelerazione costante.
Dove:
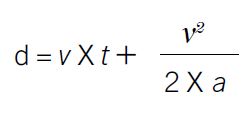
- d è lo spazio di arresto totale;
- v è la velocità iniziale del veicolo (in metri al secondo);
- t è il tempo di reazione del conducente (in secondi);
- a è l’accelerazione negativa, ovvero la decelerazione (in metri al secondo quadro).
Soluzione 2. Test pratici
Dopo aver eseguito i calcoli teorici, è consigliabile condurre dei test pratici per verificare la distanza di arresto in condizioni reali. Questi test possono aiutare ad affinare i calcoli e assicurare che la pressa piegatrice operi in sicurezza.
Diciamo che, come utilizzatori, il reverse engineering con la soluzione 2 è molto semplice e facilmente attuabile. La tecnica AOPD laser, ci mette a disposizione principalmente due metodi per estrapolare questo dato.
- Sistema a camma, il cui funzionamento si basa su un sensore di diametro 8, normalmente chiuso che, collegato alla centralina della fotocellula, legge in fase di test una camma opportunamente sagomata in grado di restituire il dato direttamente. Tale test è ripetuto ogni 24 ore di alimentazione continua dei dispositivi.
- Sistema elettronico, il cui funzionamento si basa su un dato di lettura digitale delle righe ottiche che viene restituito sul display del PLC di sicurezza.
Possiamo affermare che la lettura dello spazio di arresto è fondamentale per un funzionamento sicuro del sistema. Il dato deve essere disponibile in tempo rBeale sulla macchina in oggetto con tale dato si eseguirà la taratura reale del dispositivo di sicurezza AOPD laser attraverso la regolazione della staffatura di sostegno.
Seguendo la procedura sotto riportata, possiamo eseguirne la taratura fisicamente.
- Identificare lo spazio di arresto della pressopiegatrice attraverso il metodo del reverse engineering (Sistema 2).
- Per la prima installazione, è necessario allineare otticamente i dispositivi AOPD laser TX e RX all’utensile superiore della macchina e tra di loro. Allo scopo viene fornito con AOPD laser, uno strumento di test e posizionamento.
Il piano orizzontale di protezione deve essere posizionato dall’apice dell’utensile ad una distanza di sicurezza pari allo spazio di arresto massimo consentito da DSP LASER AP + 5 mm. I valori massimi consentiti, come in seguito descritto, sono tre: 14 mm, 18 mm e 24 mm. Per posizionare il sistema in una delle tre posizioni è necessario allineare il fascio laser nella zona 1 per uno SA massimo di 14 mm, nella zona 2 per uno SA massimo di 18 mm, nella zona 3 per uno SA massimo di 24 mm. Nella descrizione di seguito riportata è descritto il posizionamento nella zona 1; per posizionare nelle altre zone, il procedimento è lo stesso, cambia ovviamente solo la zona.
Rispettando tale procedura, possiamo poi eseguire i test periodici riportati nella norma al punto EN 12622 al punto 7.2.2.O.
Istruzioni per la manutenzione periodica
L’operatore deve controllare la corretta regolazione della macchina e dell’AOPD laser del dispositivo con l’utensile operativo superiore a intervalli regolari e almeno ad ogni cambio utensile, effettuando le prove di cui all’appendice G su entrambi i lati della traversa con il provino disteso sulla lamiera da piegare.
L’operatore deve controllare le prestazioni di arresto ad ogni accensione e ad ogni cambio utensile e almeno ogni tre mesi.
Di seguito vengono riportate le prove della appendice G relative alla EN 12622.
Prova 1. Capacità di rilevamento: controllare la capacità di rilevamento tra la punta del punzone e il fascio laser (più vicino al punzone). La distanza deve essere ≤14 mm lungo l’intera area del punzone. La prova deve essere eseguita con l’impugnatura (parte cilindrica) del provino (vedere figura 3).
Prova 2. Un provino di 10 mm di spessore (vedere figura 3) composto da materiale flessibile, per esempio plastica, giacente sullo stampo, non deve essere toccato durante la corsa verso il basso del punzone. Inoltre, un provino di 15 mm di spessore deve passare tra gli utensili.
Prova 3. Un provino di 35 mm di spessore giacente sullo stampo non deve essere toccato durante la corsa verso il basso ad alta velocità della traversa.
Conclusioni
Il test dello spazio di arresto è fondamentale per la taratura dei dispositivi AOPD laser e deve essere sempre eseguito ad ogni cambio utensile; conoscere questo dato permette un uso sicuro del dispositivo perché la zona di rispetto è molto piccola e l’operatore è spesso in tale zona, soprattutto con pezzi di piccole dimensioni.
Concludendo, possiamo affermare che conoscere lo spazio di arresto è fondamentale per regolare correttamente i dispositivi AOPD laser. Tale regolazione permette, in caso di necessità, una frenata sicura nei tempi stabiliti dalla norma tecnica al fine di evitare lo schiacciamento delle dita tra punzone e matrice.
Un modulo di verifica inserito in una formazione annuale potrebbe essere una prassi da adottare per una consapevole diminuzione degli infortuni nei luoghi di lavoro.