Sebbene l’elettroerosione possa rappresentare una valida alternativa a metodi di lavorazione tradizionale e sia, in talune circostanze, l’unica strada percorribile, è strategico valutare attentamente il suo impatto complessivo sull’ambiente e la sostenibilità in relazione alla gestione dell’energia, all’utilizzo dei fluidi dielettrici e alla minimizzazione degli sprechi. Diventa quindi fondamentale l’integrazione di pratiche e materiali green nell’ambito della lavorazione EDM, per contribuire a migliorare la carbon footprint di questo processo.
Recentemente si è osservato un notevole progresso nei materiali ingegneristici avanzati e, di conseguenza, nelle tecnologie di lavorazione a essi più appropriate. Le peculiarità di questi materiali innovativi richiedono approcci di progettazione e tecniche che tengano conto delle specifiche dei singoli processi e delle finalità dei prodotti finiti. I metodi di lavorazione tradizionali, infatti, oltre al provocare un’elevata usura degli utensili, possono danneggiare la superficie dei materiali più resistenti, causando cricche e punti di concentrazione degli sforzi, nonchè compromettendo la resistenza meccanica dei componenti. Una delle tecnologie di lavorazione più utilizzate per queste nuove categorie di materiali è l’elettroerosione (EDM). Questa tecnologia è particolarmente utile per la realizzazione di strutture complesse in 2D e 3D, come fori profondi, scanalature o sottosquadri, in materiali altamente resistenti all’usura.
L’elettroerosione è un processo prevalentemente termico che rimuove il materiale sfruttando la fusione e l’evaporazione del materiale in lavorazione, senza richiedere alcun contatto diretto tra l’utensile e il pezzo. Durante questa lavorazione, infatti, vengono generate in modo intermittente scariche elettriche tra l’elettrodo-utensile e il pezzo da lavorare, provocando l’erosione di quest’ultimo. Per consentire il passaggio della corrente tra l’elettrodo e il pezzo, nonostante questi non siano mai in contatto tra loro, viene assicurata la continuità elettrica immergendo l’intero assieme in un fluido dielettrico. Per avviare la lavorazione, infatti, l’elettrodo-utensile si avvicina gradualmente al pezzo finché, con l’aumento della tensione, viene generato un campo elettrico nella zona di minore resistenza, cioè dove la distanza tra utensile e pezzo è minore. Ciò porta alla formazione di un ponte di particelle a carica negativa che interrompe la funzione isolante del fluido dielettrico, consentendo il passaggio della corrente. Durante il processo, la corrente aumenta mentre la tensione diminuisce, producendo un canale di vapore che avvia l’ablazione del materiale per fusione o evaporazione del metallo colpito dalla scarica elettrica. Questo avviene a temperature comprese tra i 4000 e i 10000 °C, con una pressione del vapore che può raggiungere i 20 MPa. Quando la scarica elettrica e il calore raggiungono l’intensità massima, la bolla di vapore che si era generata all’interno del fluido dielettrico si espande, interrompendo il circuito elettrico e cessando la generazione di calore. Il metallo vaporizzato si solidifica rapidamente nel fluido dielettrico sotto forma di microsfere cave, mentre il metallo fuso si solidifica in microsfere piene. Queste particelle solidificate vengono espulse verso l’esterno del cratere eroso grazie all’implosione della bolla di vapore. Successivamente, il circuito viene nuovamente chiuso per avviare l’impulso seguente.
A causa della natura intrinseca del processo, la superficie risultante mostra una forma di cratere, derivante dalle singole scariche. L’accuratezza geometrica e la rugosità superficiale dipendono ampiamente dalle dimensioni e dalla conformazione di questi crateri, e quindi, dalla quantità di materiale rimosso ad ogni scarica. Pertanto, la riduzione dell’energia di scarica risulta essere fondamentale per garantire la precisione e le caratteristiche superficiali desiderate.
Il processo di EDM può essere utilizzato in due modalità distinte: a tuffo e a filo. Nella variante a tuffo, l’obiettivo della lavorazione è quello di modellare il pezzo in lavorazione in modo complementare alla forma dell’elettrodo-utensile. Questo è il processo comunemente utilizzato per la realizzazione di stampi e matrici con dettagli intricati. Nella modalità a filo, l’utensile è un filo teso che attraversa il pezzo in lavorazione, tagliandone o profilandone il materiale (Figura 2). Questa tecnologia trova oggigiorno ampio impego come supporto alla stampa 3D in metallo per separare i pezzi stampati dal piatto di accrescimento, anch’esso in materiale metallico per necessità pratiche (Figura 3).
Uno dei vantaggi principali dell’EDM risiede nella sua indipendenza rispetto a caratteristiche intrinseche del materiale come la microstruttura, la durezza o la resistenza alla rottura. Questo significa che tali proprietà non influenzano né la velocità di rimozione del materiale né la qualità finale ottenibile.
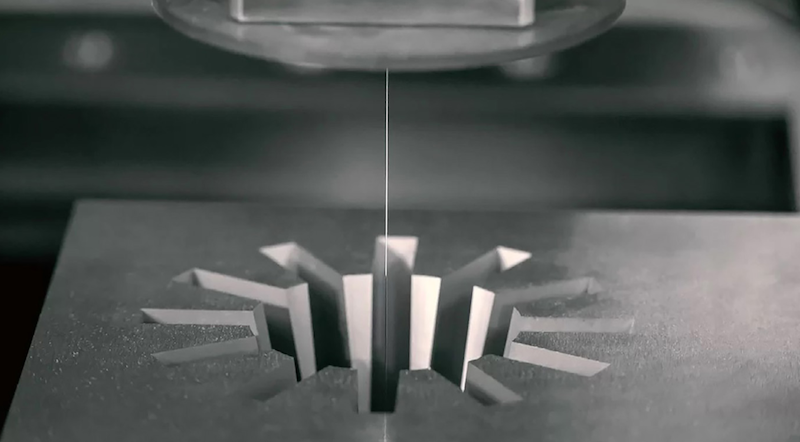
I problemi ambientali
Nonostante i diversi vantaggi che la tecnologia EDM offre in termini di precisione e capacità di lavorare materiali duri e complessi, la sua relazione con la sostenibilità è complessa e dipende da vari fattori. Relativamente a questo tema, sono stati pubblicati molti studi che mirano a minimizzare l’impatto ambientale dell’EDM.
I problemi ambientali associati alla tecnologia EDM sono legati a diversi fattori, tra cui l’alto consumo energetico specifico, la natura del dielettrico, il basso tasso di rimozione del materiale, l’elevata erosione dell’elettrodo, e la possibilità di emissioni pericolose vicino alla zona di lavoro dell’operatore, con il rischio di incendi ed esplosioni.
Dal punto di vista energetico, la lavorazione EDM può richiedere considerevoli quantità di energia elettrica per generare le scariche elettriche necessarie per rimuovere il materiale. Questo può contribuire a un maggiore consumo di risorse energetiche e all’aumento delle emissioni di gas serra, soprattutto nel caso in cui l’energia utilizzata non è proveniente da fonti rinnovabili. Tuttavia, a causa della sua capacità di lavorare materiali difficili e di ridurre l’usura degli utensili, può talvolta essere comunque più efficiente rispetto a metodi di lavorazione convenzionali, soprattutto quando si tratta di materiali ad alta durezza che richiedono una grande quantità di energia per essere lavorati tramite tecniche tradizionali.
Per valutare l’efficienza energetica del processo, sono stati identificati i componenti della macchina che influiscono maggiormente sul consumo totale. È stato scoperto che la maggior parte dell’energia, fino all’80%, viene impiegata dalle unità ausiliarie, quali compressore d’aria, filtri, unità di raffreddamento… mentre solo l’1% è richiesto per il vero e proprio processo di EDM.
Anche il tipo di dielettrico in cui sono immersi l’utensile e il pezzo in lavorazione ha un impatto significativo sulla sostenibilità del processo EDM. Solitamente, infatti, i dielettrici comunemente impiegati nel mondo industriale sono oli idrocarburi o soluzioni a base acquosa, che però presentano problemi legati, rispettivamente, al loro smaltimento, in quanto tossici, o alla corrosione del pezzo in lavorazione. Inoltre, il kerosene, uno tra gli idrocarburi più utilizzati, aumenta il rischio per gli operatori, con possibilità di incendi ed esplosioni e formazione di sostanze nocive nell’ambiente di lavoro. Per proporre una soluzione a queste problematiche, sono stati esaminati dielettrici alternativi come gli oli vegetali esausti, che consentono di migliorare l’ecocompatibilità del processo, garantendo maggiore sicurezza operativa e tutelando la salute del personale. Un’altra strategia attualmente impiegata è quella di utilizzare un dielettrico gassoso, come ossigeno, azoto, argon o aria compressa, distribuito nell’area di lavorazione tramite sistemi di tubazioni e di controllo della pressione. Questo gas mantiene l’area di lavoro pulita dalle particelle di materiale fuso o evaporato, previene l’accumulo di detriti sull’elettrodo e ripristina la resistenza dielettrica dopo la formazione del canale del plasma. Questa variante di EDM prende il nome di EDM a secco e comporta minori costi di produzione, ridotti costi di materiale dielettrico e minor inquinamento rispetto all’utilizzo di dielettrici liquidi. Tuttavia, entrambe queste varianti sostenibili del processo di EDM presentano svantaggi come una finitura superficiale scarsa a causa dell’accumulo di detriti, un basso tasso di rimozione del materiale, un cattivo odore di bruciato e un raffreddamento più lento dell’area di lavoro. Nonostante ciò, il tasso di usura degli utensili è inferiore, grazie all’effetto di schermatura causato dall’accumulo indesiderato di detriti sul pezzo lavorato. Per mitigare tali inconvenienti, sono state esplorate delle soluzioni intermedie, chiamate semi dry, mediante l’utilizzo, come dielettrico, di una miscela di liquido e gas.
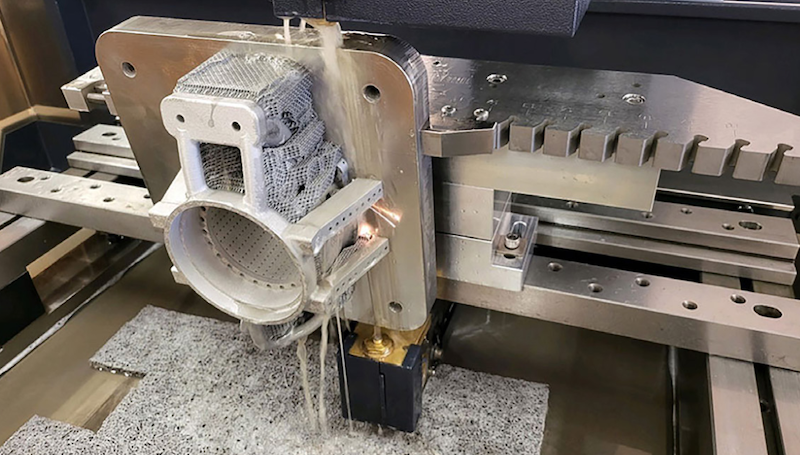
Il consumo di elettrodi
Un altro problema impattante sulla sostenibilità del processo di EDM è il consumo degli elettrodi utilizzati per generare le scariche elettriche. Questo comporta la necessità di sostituirli periodicamente, generando rifiuti e aumentando i costi associati al processo. Inoltre, durante il processo di EDM, possono essere prodotte emissioni di gas e polveri, con un conseguente impatto negativo sia sull’ambiente che sulla salute degli operatori, specialmente se queste emissioni non sono gestite correttamente.
Per valutare quantitativamente il grado di sostenibilità della lavorazione, è stato deciso di correlare il valore economico delle risorse utilizzate all’impatto ambientale generato. Secondo questa premessa, un aumento delle risorse impiegate durante il processo peggiora la sua sostenibilità, indicando che un processo è considerato sostenibile se richiede un basso consumo di risorse. Il consumo energetico viene, quindi, valutato misurando l’energia assorbita durante la lavorazione e stabilendo il costo unitario dell’elettricità. Per quanto riguarda il consumo di elettrodi, la quantità di utensili consumati viene stimata confrontando le lunghezze iniziali e finali dell’elettrodo, permettendo di valutarne il suo valore economico. Il consumo di dielettrico considera i costi unitari di acquisto del liquido dielettrico e dei filtri, considerando anche i costi di smaltimento alla fine della loro vita utile. Assegnando un valore economico a ciascun elemento, è possibile valutare la sostenibilità del processo di elettroerosione. L’indice proposto è semplice da implementare nei casi reali e può essere ulteriormente implementato con una stima delle emissioni di anidride carbonica prodotta considerando tutti gli aspetti sopra citati [4].
In conclusione, per migliorare la sostenibilità dell’EDM, è possibile adottare diverse strategie: l’efficienza energetica delle macchine EDM può essere migliorata attraverso l’adozione di tecnologie di ultima generazione e l’ottimizzazione dei parametri di lavorazione, che potrebbero avere un forte impatto anche sulla riduzione del consumo eccessivo degli elettrodi. Per la cattura e il trattamento dei gas e delle polveri generate durante il processo di EDM si può far riferimento all’implementazione di moderno sistemi di filtraggio e depurazione, con i quali è possibile ridurre l’impatto ambientale dell’EDM e rendere il processo più sostenibile nel lungo termine.
Bibliografia e riferimenti immagini
[1] https://mwi-inc.com/blog-post/what-are-the-advantages-of-using-wire-edm-machining/[2] https://www.meccanicanews.com/elettroerosione-a-tuffo/
[3] https://www.protolabs.com/resources/blog/leveraging-edm-to-rapidly-scale-metal-additive-manufacturing/
[4] Ravasio C., Maccarini G. e Pellegrini G. Micro-EDM Process Sustainability Aspects, ICMEM 2021, LNME, pp. 23–37, 2021. https://doi.org/10.1007/978-3-030-71956-2_3
Sara Bocchi