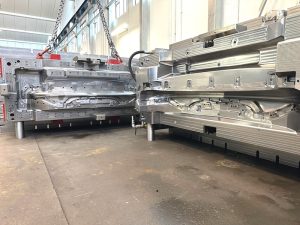
Home » Elettroerosione a tuffo
Condividi
L’Elettroerosione o EDM (dall’inglese Electrical Discharge Machining) è un processo di lavorazione non convenzionale, ovvero che non presenta contatto tra l’utensile e il pezzo durante l’asportazione di materiale, con cui è possibile ottenere feature tridimensionali complesse con elevato livello di dettaglio e rugosità superficiali basse. Rappresenta una delle tecniche di lavorazione più promettente nel campo delle lavorazioni di precisione per l’ottenimento di profili geometricamente complessi e con un rapporto di forma elevato poiché non genera bave e non risente delle caratteristiche meccaniche del materiale che si sta lavorando. Il processo, presenta il vincolo generico di poter lavorare solo materiali conduttori; limite che però si sta cercando di superare attraverso le attività di ricerca e sviluppo.
Il punto di forza delle lavorazioni non convenzionali e, in particolare dell’elettroerosione, è il meccanismo di rimozione svincolato dal contatto meccanico tra elettrodo-utensile e pezzo. In questo caso, il processo di asportazione avviene grazie alla formazione di rapide scariche elettriche all’interno dello sparking gap presente tra l’elettrodo-utensile e il pezzo in lavorazione. Lo sparking gap è, solitamente, impostato in modo tale da essere abbastanza piccolo per far sì che la tensione raggiunta risulti sufficientemente alta per permettere la ionizzazione del fluido dielettrico in cui sono immersi i due elementi. È proprio questa la caratteristica che consente di evitare tutti quei problemi legati allo stress fisico-meccanico, di eliminare la presenza di tensioni residue sul pezzo e sollecitazioni legate alla lavorazione che possono compromettere l’integrità del pezzo stesso. Il meccanismo primario di rimozione del materiale dal pezzo si basa sulla trasformazione dell’energia elettrica delle scariche in energia termica. Elettrodo-utensile e pezzo sono immersi in un liquido dielettrico, tradizionalmente rappresentato da cherosene oppure da acqua demineralizzata, per le loro caratteristiche di fluidi isolanti. In generale, il processo di asportazione del materiale può essere descritto individuando cinque diverse fasi:
Il processo EDM è influenzato da diversi parametri che vengono impostati dall’operatore in funzione della combinazione di materiali di pezzo da lavorare e elettrodo-utensile.
Le lavorazioni eseguite attraverso EDM possono essere caratterizzate e valutate attraverso indicatori delle performance di processo che ne valutano l’efficienza.