In questo articolo verrà fornita una breve panoramica riguardante le ultime novità nel mondo dello stampaggio plastico, con un focus incentrato sul sistema di iniezione a canale caldo. Si tratterà, inoltre, di alcune tecniche di stampaggio già diffuse ma relativamente recenti, che permettono di esaltare due caratteristiche tipicamente ricercate nei prodotti plastici: resistenza e leggerezza.
L’industria dello stampaggio plastico è in continua crescita, basti pensare che il 50% di tutta la materia plastica mondiale è stata prodotta a partire dall’anno 2000 e le previsioni indicano un potenziale raddoppio della produzione entro il 2050 [1], grazie soprattutto al continuo miglioramento delle tecniche di produzione.
Ecco tre novità interessanti nello stampaggio plastico a iniezione che riguardano la modifica dei sistemi a canale caldo ed alcune tecniche produttive e curiosità più recenti.
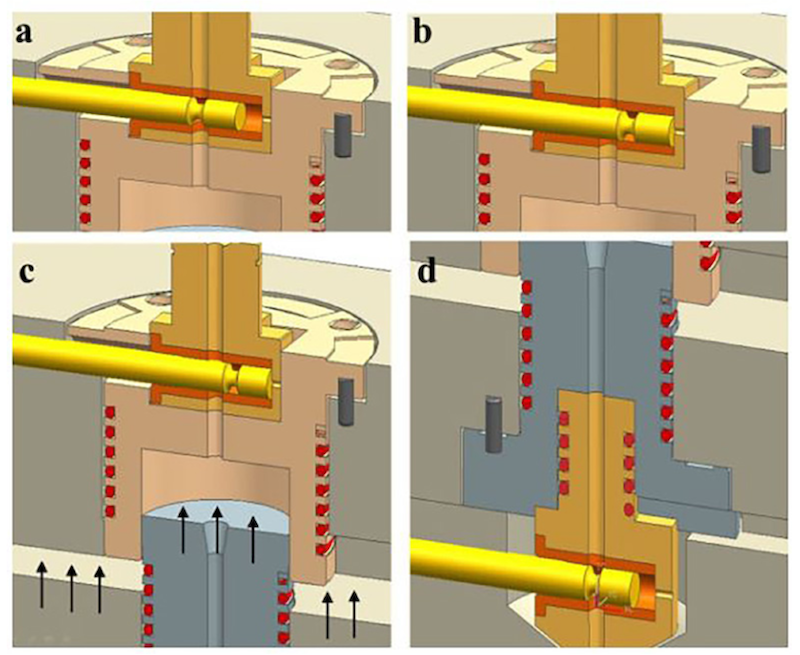
Miglioramento della regolazione del sistema di iniezione a canale caldo
In un articolo del 2022 pubblicato da De Gruyter, alcuni ricercatori hanno modificato un sistema di iniezione a canale caldo per gestire eventuali sovrappressioni e variazione di temperatura durante l’iniezione del polimero e nella fase di pressurizzazione dello stampo.
L’avanzamento del pistone nel sistema a canale caldo viene gestito solitamente in modalità “aperto” o “chiuso”. In questo caso, invece, modulando la corsa in modo controllato e sfruttando la conicità del componente, è stata modificata la sezione di passaggio al fine di abbassare la pressione applicata al polimero in raffreddamento. La capacità del sistema di gestire i disturbi introdotti volontariamente si è dimostrata ottima ed è stata valutata in base alla variazione in peso degli stampati rispetto ad alcuni campioni ottenuti in condizioni ottimali. In particolare, il sistema si è dimostrato particolarmente efficiente nel gestire le sovrappressioni mentre, nel caso la pressione interna allo stampo inferiore a quella ideale, è riuscito ad adattarsi alle condizioni ottimali solo parzialmente.
Il controllo graduale dell’avanzamento del pistone è stato testato anche durante l’iniezione di materiale a temperatura maggiore rispetto a quella ideale, riuscendo, in parte, a migliorare la qualità del prodotto finito variando la pressione. Questo sistema è ancora in fase di studio, ma le ricerche future verranno sicuramente focalizzare verso la riduzione della corsa del pistone, per renderlo ancora più reattivo, e verso una maggiore comprensione dell’influenza della conicità del componente e della compensazione della pressione [2].
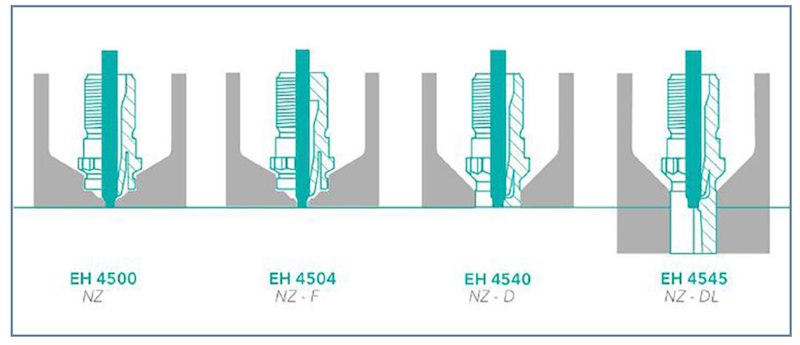
Modifica del sistema di iniezione a canale caldo per la realizzazione di stampati a parete sottile
In un altro studio recente, alcuni ricercatori sudcoreani hanno testato un sistema che sfrutta la forza di serraggio sugli stampi per incrementare la pressione del polimero fuso in ingresso allo stampo. L’architettura dello stampo, in questo caso, è costituita da tre piastre, una di serraggio, una di compressione e quella di stampaggio (Figura 1). Nella piastra di serraggio è ricavato un cilindro che viene alimentato col materiale fuso, il quale viene compresso da un pistone solidale alla piastra di compressione. Il movimento relativo tra queste due piastre, infatti, cambia il volume all’interno del cilindro, incrementando la pressione. Il pistone è solidale all’ugello di iniezione e i processi di alimentazione, pressurizzazione e iniezione vengono controllati da due valvole a perno che si aprono e si chiudono in modo alternato, consentendo al materiale fuso di raggiungere pressioni fino a 120 MPa.
Benché il sistema necessiti di ulteriori studi e miglioramenti, i ricercatori dell’Università della Scienza e Tecnologia di Seoul hanno notato un elevato potenziale nell’applicazione di questo sistema al micro-stampaggio o alla realizzazione di oggetti plastici con pareti sottili [3].
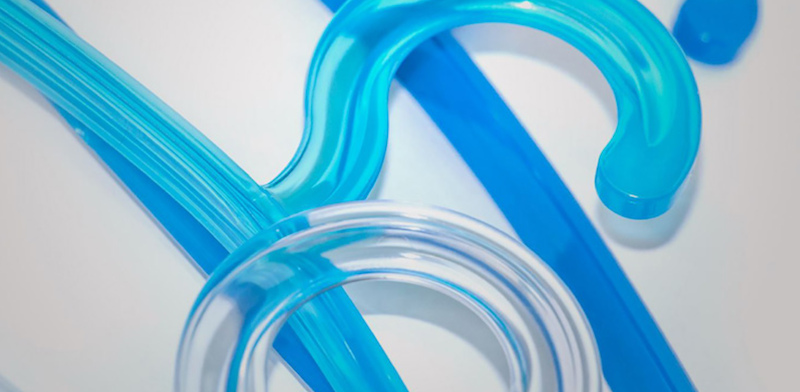
assistito a gas (cortesia DEK).
Nuovi ugelli a canale caldo Meusburger
È recente l’incontro organizzato da Fanuc e Meusburger presso la sede italiana del gruppo giapponese, per discutere delle ultime novità nel campo dello stampaggio delle materie plastiche con Ucisap – Unione Costruttori Italiani Stampi e Attrezzature di Precisione. In quest’occasione Meusburger ha presentato dei nuovi ugelli a canale caldo basati sulla tecnologia smartFILL. Questi ugelli danno la possibilità di stampare grammature da 0,5 a 2.5 e si distinguono per la loro versatilità nel poter stampare un’ampia gamma di materiali con un solo sistema.
Le serie lanciate dall’azienda austriaca sono tre: ugelli ad otturazione avvitati, ugelli appoggiati per sistema a canale caldo e mono-ugelli ad otturazione con sistema di montaggio facilitato. In linea generale, quello che accumuna le tre famiglie di componenti è:
• riduzione delle perdite di temperatura e maggiori possibilità di applicazione: la geometria del canale di fusione, unita all’innovativa tecnologia di riscaldamento, permette di lavorare praticamente tutti i tipi di materiale termoplastico. I nuovi ugelli si adattano facilmente all’impiego nella stampa dei tecnopolimeri con temperature di lavorazione estremamente elevate;
• ghiere ugello variabili: le diverse ghiere ugello a disposizione danno la possibilità di scegliere quella più adatta alle esigenze specifiche del pezzo stampato e del tipo di stampo. Il punto di rottura rimane fisso, rendendo semplice il passaggio da una versione all’altra, quando necessario (Figura 2);
• miglior compattezza e montaggio sullo stampo facilitato: la progettazione di questi nuovi sistemi a canale caldo ha messo in primo piano la compattezza, cercando di ridurre il più possibile lavorazioni complesse sugli stampi per il montaggio di questi ugelli. Inoltre, Meusburger ha anche messo in evidenza come la facilità di manutenzione sia stata una priorità durante la progettazione di questa nuova serie di componenti [4][5].
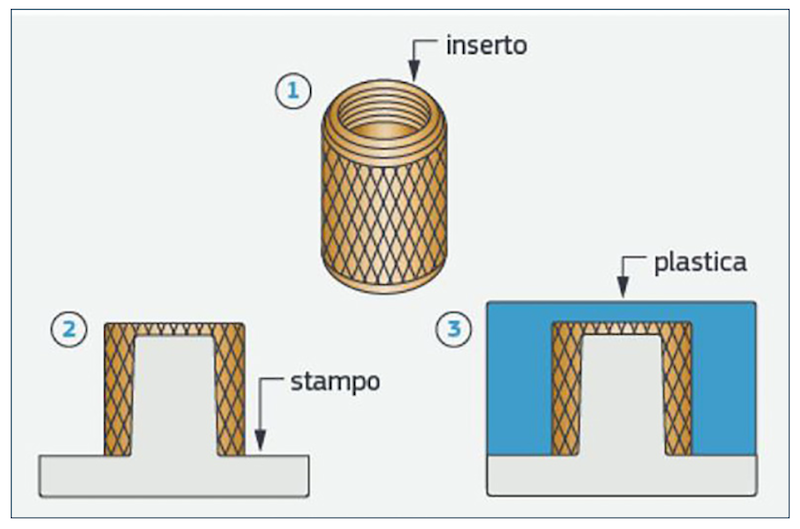
Leggero e resistente è possibile? Lo stampaggio a iniezione assistito a gas e lo stampaggio ad iniezione di schiuma
Questi due processi consentono entrambi di ottenere prodotti estremamente leggeri e funzionali coadiuvando l’utilizzo di un gas inerte alla lavorazione, ma sfruttandolo in maniera diversa.
Nel caso dello stampaggio a iniezione assistito a gas, questa lavorazione consente di ottenere forme cave nello stampaggio di materie plastiche aggiungendo al pompaggio del polimero anche l’iniezione di un gas inerte, tipicamente azoto, che ha lo scopo di svuotare internamente il prodotto.
L’azoto iniettato mantiene la pressione di stampaggio e consente al materiale plastico di distribuirsi uniformemente sulle pareti, generando prodotti leggeri e resistenti. Gli stampi per questa applicazione richiedono solitamente tempi di raffreddamento superiori, ma sono soggetti a minor usura e risultano più semplici da realizzare rispetto ad uno stampo classico [6].
Lo stampaggio ad iniezione di schiuma, invece, è una variante interessante del tradizionale stampaggio a iniezione e integra un agente espandente nel polimero, creando una struttura in schiuma cellulare all’interno dei componenti stampati. Questo processo produce parti leggere ma robuste, con un risparmio nel consumo di materiale che si attesta mediamente attorno al 20%. Inoltre, offre una maggiore flessibilità di progettazione, consentendo la realizzazione efficiente di forme complesse e parti di grandi dimensioni.
Infatti, anche se la produttività risulta inferiore rispetto a quella di altri metodi di stampaggio, un altro vantaggio di questa tecnica risiede nella possibilità di stampare parti molto grandi senza dover utilizzare pressioni elevate e a temperatura inferiore di quelle usate nello stampaggio tradizionale. L’abbattimento dei costi risiede anche nella possibilità di poter usare stampi in alluminio, in quanto questo tipo di lavorazione genera uno stress minore sui componenti [7].
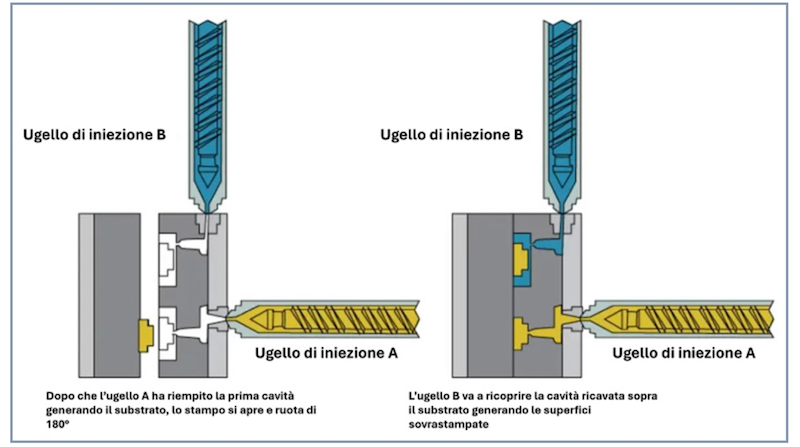
Adattare le superfici a diverse esigenze: il sovrastampaggio
Il sovrastampaggio è un insieme di tecniche di stampaggio a iniezione che consente di produrre un pezzo in due fasi successive utilizzando due materiali diversi, oppure in una sola lavorazione utilizzando presse bi-materiale, che hanno quindi due gruppi di iniezione distinti. Le lavorazioni che stanno sotto questa definizione sono tipicamente tre:
– Stampaggio con materiali multipli
– Stampaggio a inserto
– Stampaggio con tavola rotante e navetta
Lo stampaggio di più materiali, noto anche come “stampaggio a due colpi” o 2K, è un processo in cui le parti sovrastampate formano un legame col substrato per varie finalità, che possono comprendere la semplice protezione dall’ambiente o da urti, il miglioramento dell’ergonomia, l’ottimizzazione delle funzionalità di una superficie o per semplice aspetto estetico. Questo metodo utilizza due serie di cavità: la prima trattiene il substrato mentre la seconda modella il materiale di sovrastampaggio. I prodotti ottenuti con questa tecnica possono anche essere realizzati tramite stampaggio a inserti, offrendo vantaggi come alta qualità, costi ridotti e cicli di produzione brevi.
Le due opzioni disponibili per lo stampaggio di più materiali includono l’elastomero su substrato termoplastico o il sovrastampaggio termoplastico su base termoplastica. Le fasi principali del processo sono l’iniezione di materiale plastico fuso nello stampo dall’ugello A, il raffreddamento della materia fusa, la rotazione dello stampo per allinearsi con l’ugello di iniezione B, la chiusura dello stampo e l’iniezione del polimero scelto per il sovrastampaggio e, infine, il raffreddamento e l’espulsione della parte dallo stampo (Figura 4).
Lo stampaggio a inserti, invece, utilizza una pressa a iniezione a colpo singolo e richiede strumenti meno costosi rispetto allo stampaggio a due colpi. Nel processo di stampaggio a inserti, il supporto viene prima posizionato all’interno dello stampo a iniezione. Ad esempio, lo stelo di un cacciavite che necessita di impugnatura viene posto nello stampo senza manico. Successivamente, materiali come elastomeri o termoplastici vengono iniettati nello stampo per formare la presa dello strumento. Infine, la parte viene raffreddata e successivamente espulsa dallo stampo.
La terza tipologia di lavorazione è lo stampaggio con tavola rotante e navetta, essa coinvolge la lavorazione di un substrato che viene posizionato o formato in un piattello rotante utilizzando un’unità di iniezione orizzontale o un robot. Successivamente, il tavolo ruota o si sposta alla stazione successiva, dove il secondo materiale scelto viene iniettato attraverso un’unità di iniezione a canale caldo verticale o orizzontale. Infine, la tavola ruota una terza volta verso la stazione di scarico, dove la parte bicomponente viene espulsa [8].
L’utilizzo di una tecnica piuttosto che un’altra dipende strettamente dal tipo di prodotto che si vuole realizzare, dai volumi di produzione e dal costo della manodopera. Pur richiedendo una progettazione, una lavorazione e una selezione di materiali più complesse rispetto allo stampaggio ad iniezione, il sovrastampaggio, consente di ottenere parti con un’eccellente adesione e solidità, evitando la necessità di montaggi manuali dei componenti e riducendo i relativi costi. [9].
Tra i materiali più apprezzati per realizzare le superfici sovrastampate si trovano generalmente gli elastomeri termoplastici (TPE); relativamente semplici da elaborare, uniscono una buona durabilità a morbidezza ed elasticità.
Anche il silicone viene utilizzato come materiale da sovrastampaggio ed è richiesto solitamente in campo medico in quanto biocompatibile e resistente alla sterilizzazione.
Altri materiali comunemente diffusi sono il poliuretano e il PVC, che tra le tante applicazioni trovano ampio spazio nella realizzazione di dispositivi elettrici e prodotti di elettronica ai fini di impermeabilizzazione e isolamento elettrico [10].
Mantenere le superfici funzionali, alleggerire il resto: il costampaggio
Il costampaggio entra in gioco quando è necessario produrre parti con forme complesse da realizzare in metallo o quando i costi di realizzazione del pezzo totalmente metallico non sono giustificati dalla funzionalità del componente che si vuole realizzare. In questo caso, si può pensare di mantenere le parti funzionali del prodotto invariate e sostituire il resto del corpo con del polimero.
A differenza del sovrastampaggio che utilizza due stampi distinti, questa tecnica impiega di solito una parte metallica preformata, che viene inserita in uno stampo e sovrastampata con materiale plastico. Questo processo rinforza i pezzi in materiale plastico incorporando inserti filettati e migliora la loro capacità di fissarsi tra loro, soprattutto per installazioni ripetute o per rendere possibili movimentazioni precise come rotazioni e scorrimenti. Inoltre, l’uso di boccole e manicotti rappresenta una soluzione efficace per aumentare la durabilità dei componenti in accoppiamento. Questa tecnica, spesso utilizzata anche nell’additive manufacturing, deve tenere in conto di vari fattori, tra cui la capacità di materiali plastici diversi di creare un legame chimico resistente, lo spessore delle pareti, i sottosquadri, gli angoli di spoglia e la finitura superficiale. Insomma, il tema è quello di considerare tutti gli accorgimenti solitamente necessari per la realizzazione dell’accoppiamento desiderato (Figura 5) [9].
Riferimenti
[1] Crescita del settore plastico nei prossimi anni: esg360.it[2] Regolazione sistema a canale caldo: C. Hopmann, M. Schöll, H. Dornebusch – “Development of a cavity pressure control for injection moulding by adjusting the cross-section in the hot runner”
[3] Modifica sistema canale caldo: J. H. Park, S. K. Kim – “Expansion Injection Molding Process Using Clamping Force for Melt Compression”.
[4] Nuovi ugelli smartFILL
[5] Sito Meusburger: meusburger.com
[6] Stampaggio assistito a gas: stamplastitalia.com
[7] Stampaggio a iniezione di schiuma: proleantech.com
[8] Sovrastampaggio e costampaggio: dekmake.com
[9] Sovrastampaggio e costampaggio: protolabs.com
[10] Sovrastampaggio e costampaggio: djmolding.com
Marco Zambelli