Nata dall’unione e dalla sinergia di aziende specializzate in settori diversificati, Ims Deltamatic Group è oggi un punto di riferimento internazionale nell’engineering e nella produzione di impianti speciali nei settori converting, automotive e stampi per fusioni di alluminio. Competenze, esperienza e know-how che trovano applicazione in vari settori merceologici grazie a un trasferimento tecnologico in cui qualità e attenzione al processo rivestono un ruolo fondamentale e strategico.
In questo contesto Delta Moulds, divisione Specials del Gruppo, si occupa della progettazione e della produzione di stampi per fusioni di alluminio (conchiglie in gravità, stampi in bassa pressione e pressocolata, casse anima e prototipi).
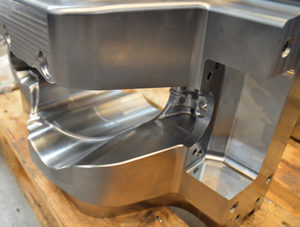
Attività svolta conto terzi grazie al contributo di un qualificato team composto da una quindicina di persone. «Servizio e flessibilità – sostiene Daniele Maino, product & sales manager in Delta Moulds di Presezzo (BG) – rappresentano i nostri punti di forza sui quali quotidianamente impostiamo la nostra crescita. Servizio al cliente inteso come attenzione alle sue richieste e al suo completo soddisfacimento. Per agevolare questo approccio è risorsa fondamentale il nostro ufficio tecnico di progettazione interna che, interfacciandosi con il cliente stesso, riesce a gestire con elevato dinamismo le commesse, nel rispetto di standard qualitativi sempre più elevati e tempistiche oggi sempre più stringenti».
Proprio con l’obiettivo di minimizzare i tempi di risposta, l’azienda punta all’aggiornamento tecnologico, non solo introducendo nuove macchine di altissimo livello, ma anche interessandosi dei migliori utensili sul mercato e di adeguate attrezzature. Ambito, quest’ultimo, nel quale MMC-Hitachi Tool ha saputo fornire il proprio prezioso apporto con un mirato supporto tecnico finalizzato alla fornitura di una vasta gamma di frese destinate a diverse lavorazioni.
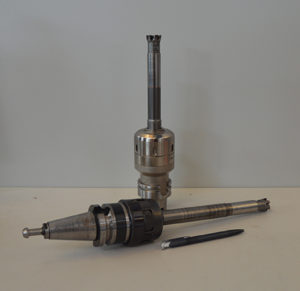
Produttività e qualità senza compromessi
«Ottimizzare tempi e metodi – continua Maino – presuppone un aggiornamento tecnologico che non si può limitare all’acquisizione di nuove e più performanti macchine, di nuovi utensili e di attrezzature collegate. Si rende infatti necessario rivedere i processi riadattandoli al meglio per poter soddisfare un mercato sempre più esigente e costantemente in cerca di innovazione».
Aggiornare processi significa rivedere le tecnologie adottate, le strategie di lavorazione nel tempo consolidate, gli utensili impiegati. In questo processo di rinnovamento MMC-Hitachi Tool ha saputo affiancarsi a Delta Molds non solo come semplice fornitore, bensì come partner nel trovare strategie più performanti e adeguate alle specifiche esigenze. «Il supporto e l’affiancamento tecnico – aggiunge lo stesso Maino – sono stati determinanti per la ricerca mirata che, nel tempo, ha permesso progressivamente di sostituire le frese impiegate nelle nostre lavorazioni».
Una scelta degli utensili condivisa congiuntamente dai tecnici MMC-Hitachi Tool, coordinati dal tecnico commerciale responsabile sig. Filippo Ambrosi, e dalla squadra operativa in Delta Moulds, che ha portato all’ottenimento dei risultati ambiti in termini di efficienza ed efficacia operativa.
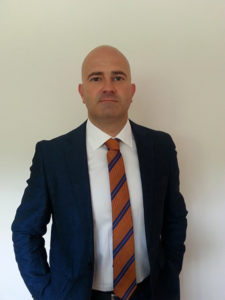
Risultati alla cui base risiede un concetto di produttività noto da tempo in MMC-Hitachi Tool e definito “Production50”. Questo concetto, applicabile in particolare per il settore stampi e matrici, consente la possibilità di tagliare i costi di produzione complessivi sino al 50%. Per il citato settore si può infatti stimare in un 5% il costo degli utensili di taglio, attribuire al 25% una quota di costi generali, mentre la restante parte (70%) rappresenta il reale costo di processo. Ed è proprio in quest’ultima che si concentrano i margini di miglioramento. Infatti, adottando sistemi di lavorazione, utensili e strategie di taglio innovativi è possibile ottimizzare sensibilmente i tempi ciclo, aumentando al tempo stesso produttività.
«Un percorso di rinnovamento di certo non semplice ed immediato – rileva Maino – ma, il forte orientamento alla continua innovazione, la presenza di coraggiosi obiettivi comuni e l’intenso lavoro di squadra, hanno concretizzato il raggiungimento di risultati tangibili e replicabili».
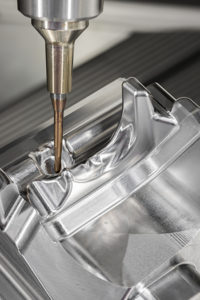
Affidabilità di prodotto e stabilità di processo
Un progetto di sviluppo comune nel quale anche l’aspetto di training formativo ha avuto un peso determinante nel rapporto di collaborazione.
«È innegabile infatti – continua Maino – quanto sia importante saper sfruttare al meglio le nuove soluzioni adottate in alternativa a quelle consolidate nel tempo, ma ormai obsolete. Indispensabile il continuo percorso formativo dei nostri operatori affiancati da MMC-Hitachi Tool che porta di fatto a questo risultato».
Una fornitura di soluzioni e di supporto tecnico che ha portato non solo maggiore qualità di lavorazione, tempistiche ridotte ed elevata affidabilità di processo, ma anche l’opportunità per Delta Moulds di aumentare la propria capacità produttiva e, di riflesso, di ampliare il proprio portafoglio clienti.
«Come diretta conseguenza – sottolinea Maino – ora riusciamo a liberare “risorse uomo-macchina” per ricollocarle e riuscire ad acquisire un più ampio numero di commesse. Importante è anche l’affidabilità di prodotto che permette una maggiore stabilità di processo, un importante aumento delle lavorazioni non presidiate e una maggiore certezza nella pianificazione dei carichi macchina, con indiscutibile positivo impatto sulla pianificazione delle consegne».
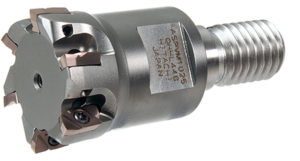
Risultati che trovano riscontro concreto anche in uno degli stampi realizzati da Delta Moulds, ovvero uno stampo di particolari automotive con tasche profonde e sporgenze importanti, in precedenza effettuate anche avvalendosi dell’elettroerosione a filo.
«Un esempio evidente – prosegue Maino – di come l’affiancamento ed il supporto tecnico del fornitore (MMC-Hitachi Tool ndr) abbiano reso possibile la rivisitazione di un processo che, se pur consolidato, si sia rivelato migliorabile grazie all’utilizzo di un prodotto adeguato e strategicamente più avanzato. Sperimentando e introducendo questa lavorazione, siamo riusciti ad eliminare la fase di elettroerosione, riducendo sensibilmente tempi e costi».

Un esempio concreto: dalle criticità alle soluzioni adottate
Una volta analizzate le criticità e i target da raggiungere per le posizioni chiave di sgrossatura, finitura sede verticale e finitura chiusure dello stampo, i tecnici MMC-Hitachi Tool e Delta Moulds hanno condiviso e messo in atto le seguenti soluzioni tecniche. La fase di sgrossatura è stata eseguita con una Pico d32, fresa per sgrossatura semi-finitura appartenente alla famiglia “alto avanzamento”, tipicamente da impiegarsi come scelta prioritaria su macchine ISO40/HSK63, efficienti con elevata dinamica.
«Impiegata con una sporgenza di 150 mm – spiega Maino – è stata in grado di lavorare con picchi di avanzamento fino a 10.000 mm/min con 0,5 mm di asportazione assiale su un acciaio 1.2343 a 42-44 HRC, mantenendo sempre un ottimo volume truciolo. Questa integrazione ha reso il processo sicuro, automatico e ha permesso di ridurre sensibilmente i tempi di esecuzione».
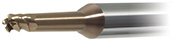
La finitura della sede di scorrimento, che doveva essere assolutamente precisa sia a livello dimensionale che geometrico (perpendicolarità delle pareti senza effetto botte) è stata invece eseguita impiegando una Aspv mini d25. La particolarità di questo utensile è di abbinare a un’elevata precisione a livello costruttivo del corpo (run out estremamente preciso), all’utilizzo di inserti in classe “H”, in metallo duro integrale. Ciò comporta la possibilità di lavorare con elevate velocità di taglio senza un tangibile consumo dei taglienti. Lo stampo presentava una sporgenza di 250 mm, rendendo così necessario il montaggio dell’utensile su prolunga in metallo duro fornita sempre da MMC-Hitachi Tool e un mandrino a forte serraggio. La finitura delle chiusure è stata invece affidata a una fresa sferica in metallo duro integrale, serie EPBT 2080, prodotta con tecnologia HIP (processo di sinterizzazione di polveri dalla granulometria bassissima), e rivestimento TH, multi strato, nano depositato. Questo ha permesso di garantire un elevato avanzamento in finitura a fronte di vita utensile molto elevata.
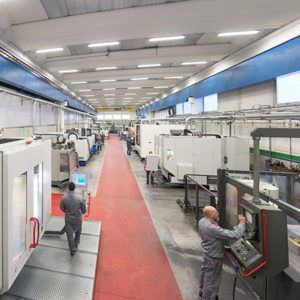
«Con un parco macchine ampio, diversificato e costantemente aggiornato come il nostro – conclude Maino – assume ancora più valore il processo di rinnovamento tecnologico in corso presso il nostro stabilimento. In quest’ottica lo sforzo congiunto è anche quello di riuscire a unificare il magazzino utensili con frese che supportino le dinamiche macchina sempre più spinte e che garantiscano, quindi, il massimo rendimento ottenibile. Dalla sgrossatura alla superfinitura: la collaborazione con MMC-Hitachi Tool è in questo senso è mirata ed efficace, in linea con le aspettative e le ambizioni di continua crescita e miglioramento del nostro Gruppo».
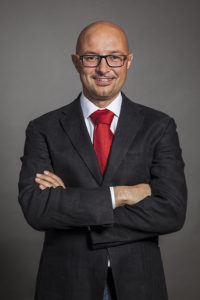
Group di Calcinate (BG).
Quando l’innovazione si ottiene con dinamismo, passione e qualità
Con sede principale a Calcinate (BG), Ims Deltamatic progetta, sviluppa e commercializza impianti industriali automatici e stampi ad alta tecnologia, realizzati su specifica commessa per una clientela mondiale. Una realtà in continua crescita che si sviluppa su 4 stabilimenti, di cui 2 in Italia (Calcinate e Presezzo, in provincia di Bergamo), uno negli Stati Uniti, e uno in Germania, oltre ad un ufficio Service in Cina, per un complessivo di 330 persone impiegate. «Ci riteniamo una struttura fortemente dinamica – spiega l’ing. Daniele Vaglietti, amministratore delegato – operante in tre settori prevalenti, ovvero: quello del converting, nostro business principale, il settore automotive e quello definito “specials”. Al loro interno si ritrovano poi diversi brand frutto di acquisizioni fatte nel tempo e che ci permettono oggi di proporci e affermarci con un consolidato know-how nei diversi ambiti di competenza». La divisione Converting propone una vasta gamma di macchine e impianti realizzati ad hoc per la trasformazione da bobina a bobina di alluminio, carte speciali e non, materiali per imballaggio flessibile e film plastici.«Un ulteriore sviluppo di questa divisione – aggiunge l’ing. Vaglietti – è stato rivolto anche all’automazione delle fasi di lavorazione mediante l’impiego di sofisticati ed evoluti processi robotizzati». La divisione Automotive è invece specializzata nella progettazione e costruzione di impianti automatici per la produzione di interni automobilistici in materiali accoppiati, trovando applicazioni nei rivestimenti interni dei bagagliai, piani vettura, cielo dell’abitacolo, passo ruota ecc. All’interno della divisione Specials, sono presenti Delta Moulds (acquisita nel 2009) la cui attività di progettazione e realizzazione di stampi è iniziata negli anni novanta da personale con decennale esperienza e Turra, azienda specializzata in presse verticali a iniezione ad alto contenuto tecnologico. «Come le altre aziende del Gruppo – sottolinea l’ing. Vaglietti – anche Delta Moulds, oltre a essere un riconosciuto brand, vanta un trascorso storico, sancendo al meglio uno dei nostri punti distintivi dei quali siamo molto fieri, ovvero: “the luxury of having a history”». Quali dunque le strategie per il futuro e con quale vision di mercato? «Consolidare – conclude l’ing. Vaglietti – prima di tutto la nostra presenza nei mercati in cui abbiamo investito in questi ultimi anni. Guardiamo al futuro con attenzione, considerando non solo l’opportunità di nuove acquisizioni, ma anche intensificando la nostra presenza in mercati ritenuti chiave, come quello asiatico e quello americano nel quale il nostro Gruppo crede molto».
Frese in metallo duro integrale
La famiglia di linee Etm ed Etmp di MMC-Hitachi Tool nasce come soluzione di riferimento nel mondo del metallo duro ad altissime prestazioni, come scelta prioritaria in fase di sgrossatura dal pieno, ripresa e fresatura diretta. Mantenere un elevato volume di truciolo è fondamentale nelle fasi di ripresa e nervatura sia su materiali bonificati che temprati fino a 60 HRC, rappresentando mediamente oltre il 50% delle operazioni di fresatura di uno stampo. Questo è l’obiettivo delle frese citate, assicurato da una particolare affilatura ovale antivibrante, dal metallo duro micrograna e dal rivestimento TH (multistrato nano depositato). Disponibili in diametri da 1 a 12, diritte o sformate a 0,9° oppure 1°, dette frese coprono in maniera ottimale le varie tipologie di applicazioni affrontate dagli utilizzatori finali.
Al servizio degli stampi e di chi li produce
Multinazionale giapponese operante nel settore della produzione di utensili, MMC-Hitachi Tool si rivolge ad aziende che svolgono lavorazioni meccaniche e, soprattutto, a realtà produttrici di stampi per offrire una gamma di utensili in grado di coprire tutte le fasi del processo produttivo. Presente in Italia sin dal 2004 con una propria filiale diretta a Iseo (BS) dove operano circa una ventina di persone (di cui una quindicina sono figure tecnico-commerciali), mette a disposizione un’ampia scelta di soluzioni in grado di soddisfare le più diverse esigenze. Nel proprio settore, grazie al know-how e all’esperienza sviluppata nel tempo, l’azienda è riuscita a determinare gli standard, sia per l’ampiezza e la profondità del suo assortimento che per la capacità di fornitura. La qualità dei prodotti abbinata a una specifica attività di consulenza e supporto applicativo, come nel caso di Delta Moulds, Gruppo Ims Deltamatic, ne fanno un affidabile partner sul quale poter contare in tutte le fasi di fresatura degli stampi.