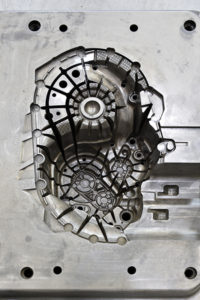
Non è un segreto: la legge del mercato guida l’evoluzione tecnologica e le scelte ad essa collegate. La varietà di componenti, prodotti secondo la logica one of kind o in lotti più o meno grandi, è sempre più ampia, sia in termini di geometria che tipologia di materiali utilizzati. Ad oggi, i processi produttivi più comuni sono lo stampaggio e la lavorazione per asportazione di truciolo, e, sempre più spesso, un mix dei due, con l’obiettivo di arrivare ad una produzione sempre più efficiente ed economica, riducendo i tempi di consegna e, al contempo, rispondendo alla necessità di una produzione sostenibile. Il materiale, sia del manufatto che dell’utensile, diventa strategico dovendo garantire le specifiche tecniche del prodotto ma anche le esigenze del processo produttivo.
Parlare di stampi significa parlare di una serie di utensili molto ampia, cui fanno riferimento numerosi processi manifatturieri, anche concettualmente diversi fra loro, ma non prevedono una asportazione di truciolo. Anche i materiali “stampati” sono estremamente vari, dalle leghe ferrose ai materiali polimerici, dalle leghe non ferrose ai materiali compositi, solo per citarne alcuni. E’ evidente come una tale varietà richieda stampi di materiali differenti, in grado di garantire la qualità del manufatto prodotto, per un numero di stampate tale da garantire l’economia del processo.
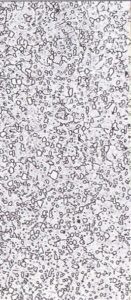
Un materiale storico: l’acciaio
Gli acciai per stampi rientrano nella famiglia degli acciai legati ed hanno i tutti in comune una elevata resistenza meccanica, tenacità all’impatto e resistenza all’usura, in un ampio intervallo di temperature. Gli acciai per stampi sono in genere divisi in tre macro-categorie: gli acciai a caldo, gli acciai a freddo e gli acciai rapidi.
Gli acciai a caldo, che fanno riferimento alla serie H, nascono per applicazioni ad alta temperatura, e sono caratterizzati da buona tenacità e resistenza all’usura e alla frattura, fondamentali in processi di stampaggio, estrusione e pressofusione. Negli acciai a caldo gli elementi in lega più utilizzati sono molibdeno, tungsteno, cromo e vanadio, proprio in virtù delle caratteristiche che conferiscono all’acciaio, che deve rispondere a specifiche esigenze, in funzione dell’uso. Questi acciai sono infatti utilizzati nella costruzione di stampi, per stampaggio in stampo aperto e pressofusione, e per le matrici di estrusione, tutti processi caratterizzati da sollecitazioni meccaniche e termiche, lavorando a temperature superiori a 200°C . E’ quindi fondamentale avere una elevata stabilità al rinvenimento e resistenza agli shock termici. Per contenere il rischio legato allo shock termico, gli acciai a caldo possono essere riscaldati, prima dell’inizio dell’impiego, a temperature fino a 300°C, anche se, a causa della ciclicità ripetuta di riscaldo-raffreddamento, possano nascere di tensioni interne in grado di compromettere la funzionalità. Naturalmente l’assenza di impurità e/o segregazioni permette di ridurre il rischio di tensioni interne.
Gli acciai a caldo possono essere distinti anche in funzione delle temperature di lavoro, distinguendo fra quelli che subiscono forti riscaldi, oltre 600°C, e quelli che lavorano a temperature più basse. Al primo gruppo si possono ricondurre gli stampi per pressofusione di materiali metallici non ferrosi, gli stampi per forgiatura di materiali ferrosi e le matrici di estrusione, mentre al secondo si riconducono gli stampi che lavorano a medie temperature, che richiedono maggiore tenacità eresistenza alle sollecitazioni dinamiche a caldo.
In generale, gli acciai a caldo devono possedere:
– Buona lavorabilità per asportazione di truciolo
– Bassa deformabilità dopo trattamento termico, con ridotta sensibilità alla formazione di micro intaglio e fessurazioni a seguito di cicli termici ripetuti
– Elevata tenacità
– Stabilità al rinvenimento
Si definiscono acciai a freddo quegli acciai che, in servizio, sono soggetti a riscaldamenti dovuti solo all’attrito, quindi tali da non compromettere la durezza iniziale. In generale, devono presentare una elevata resistenza alla usura, in particolare per abrasione, e alla frattura, elevata durezza e indeformabilità ai trattamenti termici dato che l’utilizzo è sempre a seguito di tempra, in olio o in aria. Al fine del conferimento delle caratteristiche richieste, è possibile agire sulla composizione chimica, ricordando come un elevato tenore di carbonio porti alla formazione di carburi, con miglioramento della resistenza alla usura, mentre l’aggiunta di opportuni elementi in lega portano alla formazione di diversi carburi complessi, in grado di migliorare la tenacità e l’indeformabilità.
Fra gli acciai a freddo particolarmente interessanti sono gli acciai ledeburitici, con tenore di cromo 12%, che presentano elevata resistenza all’usura e al taglio. In virtù delle loro caratteristiche, dovute anche alla presenza di altri elementi in lega, gli acciai ledeburitici al cromo sono impiegati con successo per matrici e punzoni, stampi da trancia per lamiere con spessori inferiori a 7mm, stampi per materie plastiche, anche altamente sollecitati. Gli acciai a freddo al wolframio cromo trovano impiego in applicazioni soggette ad urti violenti e ripetuti, come è il caso degli stampi coniatori.
Gli acciai rapidi, noti anche come HSS, sono i più datati, dato che il loro sviluppo nasce agli inizi del ‘900. Nonostante nel tempo siano stati messi a punto nuovi materiali, l’impiego degli acciai rapidi continua ad essere importante, in particolare nel caso degli stampi per lavorazioni a freddo. Fra l’altro, date le condizioni esasperate in cui oggi lavorano molti stampi, è particolarmente interessante l’ottima capacità di ancoraggio dei rivestimenti innovativi sul substrato degli HSS.
Tra gli acciai più altamente legati, i rapidi mantengono la loro durezza e resistenza all’usura anche a elevate temperature. Nonostante la famiglia degli acciai rapidi contenga un gran numero di tipologie di acciai, le principali sono due: la serie M e la serie T. La serie M contiene fino al 10% di molibdeno, con cromo, vanadio, tungsteno e cobalto come altri elementi in lega, mentre la serie T contiene 12÷18% di tungsteno, con cromo, vanadio e cobalto in lega; la serie T, rispetto alla M, ha maggior resistenza all’abrasione e minori distorsioni durante i trattamenti termici, oltre ad essere meno costosa.
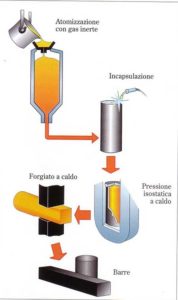
L’acciaio da polveri
Considerata in genere una categoria a parte è quella degli acciai da polvere. Si tratta di acciai rapidi, prodotti con la metallurgia delle polveri, che permette variare la composizione chimica arricchendo la matrice di elementi in lega, tipicamente carbonio e vanadio. La formazione di carburi, finemente dispersi nella matrice, conferisce una maggiore resistenza all’usura rispetto agli acciai rapidi convenzionali. Grazie all’arricchimento di elementi in lega, finemente dispersi, anche la tenacità e la resistenza a flessione possono essere migliorate. Quando si parla di metallurgia delle polveri, sono fondamentali le caratteristiche del grano, in particolare la sua dimensione e la distribuzione che deve essere omogenea. Nello stampaggio, in virtù delle caratteristiche ottenibili, gli acciai rapidi da polvere trovano largo impiego nelle lavorazioni a freddo, quali tranciatura fine ed estrusione, caratterizzate da sollecitazioni estreme dovute al tipo di lavorazione o al materiale lavorato, quale gli alto resistenziali.
Applicazioni interessanti riguardano lo stampaggio di materiali abrasivi, per esempio in presenza di fibre di vetro o di carbonio, a cui si può aggiungere l’azione corrosiva dovuta alla presenza di prodotti di scissione liberati alle alte temperature.
L’acciaio da polvere è utilizzato con successo anche in quelle lavorazioni a freddo caratterizzate da elevate pressioni da strisciamento che possono dar luogo, oltre all’usura abrasiva, anche a quella adesiva, più nota come incollaggio. In questo caso, acciai da polvere con caratteristiche tribologiche anti-incollaggio, come gli acciai da polvere azotati, permettono la costruzione di stampi per lavorazioni a freddo che non richiedono trattamenti o rivestimenti anti adesione, costosi oltre che dispendiosi in termini di tempo. La famiglia di acciai da polvere azotati presenta anche un’ulteriore caratteristica che riguarda la lavorazione all’utensile degli stampi: la lavorabilità di acciai altamente legati, prodotti secondo con metallurgia convenzionale, è sensibilmente più difficoltosa rispetto a quella di acciai da metallurgia delle polveri. Questo comporta inevitabilmente un incremento dei costi di produzione, a scapito dell’economicità tanto invocata dal mercato.
La questione alta velocità
Un tema molto dibattuto ed oggetto di ricerca, riguarda la possibile influenza delle lavorazioni per asportazione ad alta sulla superficie del materiale lavorato. Questo tema risulta essere particolarmente interessante nel caso degli stampi: da un lato è fondamentale l’efficienza dell’operazione di stampaggio, fortemente influenzata dalla qualità della superficie, dall’altro i tempi di consegna sempre più stretti richiedono lavorazioni high performance e, fra queste, l’alta velocità è certamente la più interessante.
Nonostante l’argomento continui ad essere studiato, ciò che ad oggi è emerso indica che la lavorazione ad alta velocità può causare dei danni alla superficie lavorata, se non eseguita secondo condizioni identificate come “ottimali”. In generale, ciò significa lavorare con utensili che non abbiano taglienti usurati, inclinati rispetto al materiale, evitando possibilmente la fresatura in discordanza. In particolare, nelle lavorazioni ad alta velocità di finitura, o superfinitura, post trattamento termico, è bene che il percorso dell’utensile sia sempre inclinato, fresando in concordanza eventualmente con cambi utensile anticipati in modo da scongiurare il rischio “tagliente usurato”. Anche un trattamento di distensione prima della prova di stampaggio è consigliabile. Una lavorazione ad alta velocità eseguita secondo parametri non ottimali potrebbe compromettere la durata dello stampo, principalmente a causa della possibile formazione di microcricche e coltre bianca martensitica, oltre a durezze anomale causate dalla deformazione plastica del materiale in lavorazione.
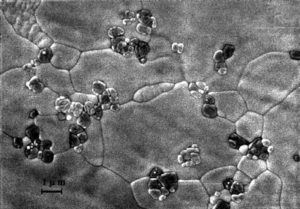
A proposito di compositi…
I Cermet, detti anche Ceramici neri, sono una combinazione di ceramici legati con una fase metallica, introdotti sul mercato verso la metà degli anni ’60. Proprio grazie alla loro composizione, i Cermet combinano la resistenza all’ossidazione alle alte temperature (ceramici) alla tenacità, resistenza agli shock termici e duttilità, tipiche dei metalli. I Cermet vengono classificati come materiali compositi ed impiegati con combinazioni variabili di ceramici e metalli, legati secondo la metallurgia delle polveri.
Lo stampaggio di materiali compositi può sostituirsi alla produzione di manufatti tradizionalmente prodotti con tecniche di laminazione: in questo caso si parla di infusione. Gli stampi, sia maschi che femmine, possono essere in vetroresina, ma non solo, l’importante è che sia garantito un adeguato grado di robustezza dato che, durante il processo di infusione, la resina viene richiamata nello stampo per depressione, che va a creare una forte sollecitazione sullo stampo che può deformarsi e rompersi, con conseguenti gravi conseguenze. E’ quindi fondamentale che gli stampi siano adeguatamente strutturati e, per questo, sono generalmente realizzati in vetroresina rinforzata mediante “strutture di rinforzo” esterne che possono essere aumentate in modo da contrastare la sollecitazione dovuta alla depressione. Qualora vengano utilizzati materiali diversi dalla vetroresina rinforzata, questi devono essere compatti: è infatti fondamentale la verifica della porosità, per evitare il passaggio dell’aria all’esterno. Gli stampi in materiale composito, indipendentemente da quale sia il materiale stampato, presentano diversi vantaggi, fra cui spicca la morfologia del manufatto che può avere geometrie e forme complesse, prodotte comunque con estrema precisione.
Acciaio per stampare la plastica
Per stampare le materie plastiche possono essere impiegati diversi tipi di acciaio, da quelli studiati ad hoc, fino ad alcuni tipi di acciai da costruzione e inossidabili. Anche nel caso degli stampi per materie plastiche vengono ampiamente utilizzati gli acciai da polveri, data la possibilità di controllare l’omogeneità e il grado di finezza, cui corrispondono caratteristiche meccaniche elevate.
La scelta viene fatta sulla base sia delle differenti caratteristiche delle materie plastiche da stampare, in particolare considerando le cariche e gli additivi utilizzati, che del sistema di lavorazione. La lavorazione determina lo stato di sollecitazione cui l’acciaio è sottoposto, a cui deve rispondere. In realtà, sono tre i punti di vista da considerare nella scelta del materiale: quello del materiale stesso, cioè lo stato di sollecitazione cui sarà sottoposto, quello dello stampista, in termini di rendimento desiderato, e quello del costruttore, cioè le dimensioni, la lavorabilità e la stabilità ai trattamenti termici. Generalizzando, ad oggi vengono ampiamente utilizzati acciai da bonifica, acciai pretrattati e acciai da tempra.