Costruttori e distributori affiancano l’innovazione di prodotto a un servizio sempre più vicino allo stampista. Un valore aggiunto riconosciuto e apprezzato.
Gli utensili e le attrezzature che gli stampisti possono reperire sul mercato sono soddisfacenti rispetto alle esigenze del settore? Quali sono i possibili miglioramenti attuabili in termini di prestazioni? Sono integrati coi concetti di Industria 4.0? Quali invece gli eventuali margini migliorativi in termini di servizio? Aspetto, quest’ultimo (ma non solo), su cui tanto i costruttori e distributori stanno investendo. Sono questi i punti di riflessione che abbiamo sottoposto a due stampisti: Cropelli, costruttore di stampi iniezione plastica e pressofusione e Pantostamp, costruttore stampi a iniezione, il cui sales manager, Alessandro Scalici, ricopre anche il ruolo di Presidente di Ucisap.
Il valore aggiunto della formazione
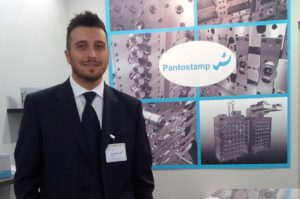
Dal suo osservatorio privilegiato come Presidente di Ucisap, Unione Costruttori Italiani Stampi & Attrezzature di Precisione, qual è il suo parere rispetto alla rispondenza dei requisiti richiesti dal settore per quanto riguarda utensili e attrezzature per la lavorazione di stampi? «È tutt’altro che semplice – spiega Scalici – riuscire a generalizzare se utensili e attrezzature possano soddisfare appieno quanto richiesto sul mercato. La segmentazione settoriale impone in questo senso molta cautela. Fermi restanti i positivi feedback emersi confrontandoci in associazione con alcuni colleghi, molto dipende infatti dal tipo di tipologia di prodotto che si costruisce e dunque dal tipo di utensile necessario. Senza dimenticare l’approccio per così dire in fresatura, anche in questo caso dettato da geometrie e dimensioni dello stampo». Sostanziali differenze che giustificano le diversificate ma, al tempo stesso, mirate scelte operative effettuate dal target di clienti di ogni stampista. «Nel nostro caso – rileva Scalici – in Pantostamp ci occupiamo per esempio prevalentemente di stampi multicavità destinati al comparto del packaging, per la produzione di componenti piuttosto piccoli. Particolari di geometrie contenute che impongono una selezione di utensili in una forbice abbastanza limitata. Anche gli acciai lavorati non differiscono di molto tra loro, con durezze comprese tra 50 e 56-58 Rockwell. Ben diverse sono invece le esigenze di chi produce stampi per deformazioni lamiera o trancia, dove non è raro dover fresare il metallo duro. In questo caso la ricerca dell’utensile più adatto si rileva molto più strategica e quasi scientifica per riuscire a ottenere le prestazioni volute». Nessun dubbio invece riguardo alla reperibilità sul mercato che, come conferma, lo stesso Scalici, rispetto a qualche anno fa, evita in alcuni casi la necessità di avere un nutrito magazzino interno a supporto dei processi. «Molti costruttori di utensili – osserva – sono in grado oggi di gestire praticamente in tempo reale l’ordine fatto dallo stampista, con spedizioni che raramente superano le 24 ore. Se non che, ci sono utensilieri che possono anche predisporre all’interno dell’officina del cliente piccoli armadi adibiti a magazzino compatto, costantemente riforniti in base all’utilizzo». Un grosso vantaggio per lo stampista, che ha la certezza di avere utensili sempre in ordine e pronti all’uso, in base al tipo di attività svolta e allo storico operativo. Tracciabilità e controllo totale e in tempo reale anche in termini di costi. «Opportunità questa – aggiunge Scalici – che si rileva molto utile in termini di Industria 4.0, di digitalizzazione. Tematica sempre più sentita e verso la quale gli stampisti prestano sempre più attenzione». Altro valore aggiunto richiamato da Scalici (e che alcuni utensilieri da qualche tempo propongono ai loro clienti) è l’aspetto formativo, in affiancamento alla fornitura e agli eventuali test di prova sul campo. «Mi riferisco a training personalizzati – precisa – attraverso un’istruzione dell’operatore con corsi di fresatura, strategie di lavorazione dettati dalla tipologia di prodotto che l’utensiliere stesso propone. In questo caso risultano senza dubbio più tangibili e concreti i miglioramenti in termini di performance di processo, in fresatura, in tornitura e così via». Una chiara possibilità, questa, per poter ampliare know-how e competenze. Utile anche a entrare in contatto con nuove tipologie di utensile, nuove tecnologie non sempre prese in considerazione con la dovuta attenzione per questioni di tempo e, forse, per timore di rallentare i cicli produttivi. «Non è semplice – conclude Scalici – modificare e/o cambiare certe metodologie operative consolidate e ben dominate. Ma innovare tuttavia significa anche questo, così come riuscire a ottimizzare i processi accettando di buon grado piccoli ma determinanti cambiamenti all’interno delle proprie officine».
Utensili e attrezzature sempre più 4.0
«Senza dubbio sono oggi reperibili molte più frese rispetto solo a 5 anni fa. Utensili il cui grado di finitura e il ciclo di vita sono notevolmente migliorati. Attualmente ci sono oltretutto molte più soluzioni standard che prima erano considerate “speciali”, fuori magazzino. E il cui reperimento richiedeva talvolta lunghi tempi d’attesa». Commenta così Elena Cropelli, alla guida della Cropelli Srl Unipersonale di Palazzolo sull’Oglio (BS), azienda che conta una trentina di dipendenti, un fatturato di circa 5 milioni di euro e la precisa volontà di ricoprire un ruolo da protagonista in un mercato sempre più competitivo. Una vocazione da sempre orientata all’innovazione tecnologica, alla ricerca della qualità di prodotto e di processo, oltre che all’attenzione al cliente. Approccio che significa essere in grado di assicurare lavorazione stampi di elevata qualità per clienti nazionali e internazionali, operanti principalmente nei settori dell’automotive e dell’elettrodomestico.
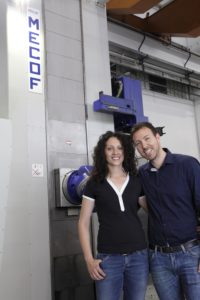
«In sintesi – aggiunge – gestire e coordinare sempre più l’attività secondo i dettami di Industria 4.0. Orientamento, devo riconoscere, a cui guardano con grande interesse anche alcuni costruttori di utensili e attrezzature per noi stampisti. E lo confermano alcune soluzioni che, per esempio, riconoscono in autonomia l’utensile inserito».
Quali i margini e i miglioramenti attuabili e ancora ottenibili?
«Dal nostro punto di vista – prosegue Cropelli – margini e i miglioramenti potrebbe essere apportati sulla base di sicurezza e delle tempistiche. Maggiore sicurezza per utensili che hanno una “vita prestabilita”. Quindi anche l’operatore sa sprecare meno e il non presidiato rende ancora di più. In merito alle tempistiche mi riferisco al fatto che l’utensile riesca a rispettare il ciclo di vita proposto e indicato dal fornitore. In tal caso la pianificazione viene rispettata e il cerchio 4.0 prende consistenza».
Rispetto a eventuali miglioramenti al servizio, la stessa Cropelli auspica che gli utensili possano costantemente offrire prestazioni più elevate per poter garantire massima competitività.
«Tempi più stretti – sottolinea – per le stesse lavorazioni di paraurti che venivano fatti solo 5 anni fa, oggi si pretendono con meno tempo di attraversamento e più qualità. Oggi ci stiamo differenziando e cerchiamo di migliorare il nostro servizio per comunicazione, reportistica, planning, flessibilità, tempistica e precisione. Essendo conto terzisti, lavoriamo più materiali quindi le prove e le ricerche su utensili e attrezzature non devono incidere sulla pianificazione. Il tempo che viene impiegato deve essere recuperato con utensili performanti e abilità dell’officina».
Concetto espresso anche con due esempi concreti molto importanti.
«Le nervature – conclude Cropelli – 20 anni fa venivano eseguite di erosione. Oggi quasi il 99% della figura viene fresato grazie agli utensili disponibili sul mercato. Altro passo molto importante riguarda le punte in HSS che, una volta, riempivano gli scaffali delle officine mentre, oggi, stanno lasciando il posto a punte forate internamente in metallo duro. In questo caso il risparmio che abbiamo testato presso la nostra unità produttiva si attesta a circa il 60% del tempo in meno. Un’altra nota va spesa per le macchine utensili, oggi permettono di lavorare figure complesse e profonde con teste di alta precisione e struttura minimale».