In questo articolo si valuta l’effetto di un innovativo trattamento termico in pressione sulle proprietà di componenti in lega AlSi10Mg ottenuti mediante pressocolata.
Come noto, i getti pressocolati in lega di alluminio ottenuti con processo standard non possono normalmente essere riscaldati ad alta temperatura né in esercizio né in fase di trattamento termico a causa dell’insorgere del fenomeno del blistering.
Questo è causato dalla presenza nel getto di porosità contenti gas intrappolato a seguito delle turbolenze che si creano in fase di riempimento dello stampo. Infatti, questo gas, se il componente è esposto ad un’elevata temperatura come accade durante il classico trattamento termico T6 (tempra di soluzione e invecchiamento), espande e, dal momento che a temperature elevate la resistenza del materiale è ridotta, è in grado di determinare un incremento delle dimensioni delle cavità e la formazione di vesciche superficiali (fenomeno del blistering).
Di conseguenza, non potendo essere sottoposta ad un adeguato trattamento termico al fine di ottimizzarne le prestazioni, tale tipologia di getti non può al momento essere impiegata in applicazioni strutturali.
Negli ultimi anni sono state proposte alcune soluzioni, quali la colata in semisolido o la colata sottovuoto, che consentono l’ottenimento di getti con un livello di porosità tale da consentire i trattamenti termici, a fronte però di un cambiamento del processo di colata o almeno di una revisione dei metodi di progettazione degli stampi e del know-how in termini di parametri di processo.
Al fine di risolvere tale problematica è stata indagata una soluzione alternativa che prevede l’applicazione a componenti in lega AlSi10Mg prodotti mediante pressocolata convenzionale di un innovativo trattamento termico T6 realizzato in pressione (HPT6), ovvero un trattamento che combina il tradizionale trattamento T6 con il processo di pressatura isostatica a caldo (HIP).
Lo scopo di tale trattamento innovativo è quello di ottenere in un unico step una effettiva densificazione del materiale insieme all’effetto di indurimento promosso dal tradizionale T6, rendendo possibile il trattamento termico di getti pressocolati standard senza andare incontro all’espansione delle porosità da gas e allo sviluppo del fenomeno del blistering, aprendo quindi la possibilità di una futura applicazione di tale tipologia di getti anche in applicazioni strutturali.
Introduzione
Le leghe Al-Si-Mg da fonderia, famiglia a cui appartiene la lega AlSi10Mg, sono ampiamente utilizzate per la produzione di componenti mediante pressocolata soprattutto per il settore automotive.
Il processo di pressocolata, o colata sotto pressione (high pressure die casting, HPDC), permette infatti di realizzare getti con geometrie complesse prossime alla loro forma finita e caratterizzati da microstruttura a grano fine, eccellente precisione dimensionale e ottima finitura superficiale.
Tuttavia, come noto, le elevate velocità con cui la lega fusa è iniettata all’interno della cavità dello stampo rendono il processo di pressocolata particolarmente soggetto alla formazione di difetti da riempimento.
La tipologia di difetto più comunemente presente nei componenti pressocolati è la formazione di porosità, che spesso non sono immediatamente rilevate al termine del processo (sono molto piccole, quindi non rilevabili mediante controlli non distruttivi standard come i raggi X), ma solo durante le successive operazioni di trattamento termico e/o lavorazione meccanica.
In particolare, tali porosità possono essere distinte in due categorie principali:
• Porosità da gas: sono cavità dovute all’intrappolamento di aria o gas (derivante dalla combustione del lubrorefrigerante) all’interno della vena liquida a causa del flusso turbolento determinato dalle elevate velocità di iniezione del metallo liquido nella cavità dello stampo.
• Porosità da ritiro: sono cavità che si formano a seguito di una mancata compensazione del ritiro volumetrico che accompagna il passaggio della lega dallo stato liquido allo stato solido a causa di un insufficiente apporto di metallo liquido nelle ultime regioni che solidificano.
In generale, la presenza di porosità (sia da ritiro che da gas) all’interno dei getti è sempre dannosa per le proprietà meccaniche del componente poiché determina una riduzione dell’area effettiva in grado di sostenere il carico applicato e favorisce l’innesco e la successiva propagazione della frattura facilitando il cedimento in esercizio.
Nel caso di componenti pressocolati però, oltre a tali problematiche, la formazione di porosità da gas comporta anche degli svantaggi aggiuntivi in quanto limita fortemente la saldabilità e soprattutto l’applicazione dei trattamenti termici sui getti pressocolati standard.
Alle temperature cui sono normalmente eseguiti i trattamenti termici, infatti, la resistenza del materiale è ridotta. Quindi, la pressione derivante dell’espansione del gas presente all’interno della porosità per effetto della temperatura è sufficiente per deformarlo plasticamente con conseguente incremento delle dimensioni delle cavità (si parla di porosità termicamente indotte) e, nel caso di porosità subsuperficiali, formazione di vesciche, dette blisters (tale fenomeno è infatti chiamato blistering), a seguito della deformazione plastica del sottile strato di metallo che le ricopre (fig. 1).
Pertanto, l’applicazione di getti pressocolati standard è al momento limitata a componenti non strutturali per i quali non è richiesta l’esecuzione di un trattamento termico per ottimizzarne le proprietà meccaniche, mentre per la produzione di getti pressocolati strutturali è necessario l’impiego del vuoto spinto, quindi di un macchinario specifico (non è possibile utilizzare le macchine da pressocolata tradizionali) e di sistemi di aspirazione ad elevata efficienza, con conseguente aumento dei costi di acquisto e gestione dell’impianto e dei costi di produzione.
HIP e trattamenti termici in pressione
Una tecnologia molto impiegata per rimuovere le porosità dai getti ottenuti tramite tecniche di fonderia è la pressatura isostatica a caldo (hot isostatic pressing, HIP).
Il processo di HIP prevede l’applicazione simultanea di elevate pressioni e temperature con l’obiettivo di rimuovere porosità da un oggetto o, più in generale, di eliminare i volumi non occupati da materiale solido.
La pressione applicata è isostatica (uguale in tutte le direzioni) ed è ottenuta tramite la pressurizzazione di un gas inerte (tipicamente Ar o He) all’interno di un apposito forno contenuto in una camera a pressione.
In particolare, l’esposizione ad elevata temperatura ed elevata pressione isostatica permette di agire sulle porosità presenti all’interno dei getti, che vengono progressivamente chiuse e sigillate, o quanto meno ridotte, sia che si tratti di porosità da ritiro che di porosità da gas.
Questo garantisce un incremento della densità del componente e migliori prestazioni in termini di duttilità, tenacità a frattura, resistenza a trazione e soprattutto resistenza a fatica.
Il processo di HIP è spesso seguito da opportuni trattamenti termici per modificare e ottimizzare ulteriormente la microstruttura e, di conseguenza, incrementare le proprietà meccaniche del materiale.
Queste ultime, infatti, dipendono principalmente dalla microstruttura del materiale, più che dai difetti presenti, e il processo di HIP, sebbene permetta di ridurre la difettosità dei componenti, non è in grado di determinare le trasformazioni microstrutturali necessarie all’ottimizzazione della microstruttura, rendendo quindi necessaria l’esecuzione di successivi trattamenti termici.
Tuttavia, l’esposizione ad elevate temperature dopo HIP può portare alla riapertura delle porosità da gas, nel caso queste non siano state del tutto rimosse. Per effetto dell’alta temperatura, infatti, il gas ancora presente all’interno delle porosità espande determinando nuovamente un incremento delle dimensioni delle porosità, con conseguente annullamento dei benefici ottenuti tramite HIP.
Di conseguenza, l’esecuzione dei trattamenti termici tradizionali (eseguiti a pressione atmosferica) a seguito del processo di HIP può rappresentare un problema, soprattutto nel caso di produzione di componenti strutturali.
Inoltre, i trattamenti termici vengono solitamente eseguiti in appositi forni e non all’interno della camera di HIP, in quanto le unità per HIP tradizionali non sono in grado di garantire velocità di raffreddamento elevate che sono fondamentali per l’efficacia di numerosi trattamenti termici, con conseguente incremento degli step di post-trattamento e quindi dei tempi e dei costi complessivi.
Allo scopo di risolvere tali problematiche sono state sviluppate unità per HIP in grado di garantire anche un raffreddamento rapido sotto pressione in condizioni controllate.
Mediante l’impiego di tali unità, infatti, è possibile garantire velocità di raffreddamento molto elevate al termine della fase di densificazione, permettendo l’esecuzione dei trattamenti termici all’interno della stessa camera impiegata per il processo di HIP, senza la necessità di dover ricorrere ad ulteriori forni e attrezzature.
In questo modo è quindi possibile combinare il processo di HIP con altri trattamenti termici permettendo di mantenere anche in fase di trattamento termico la stessa pressione applicata durante HIP, con possibilità di realizzare dei trattamenti termici in pressione, ovvero dei trattamenti termici innovativi che permettono di rimuovere le porosità e allo stesso tempo di migliorare le caratteristiche microstrutturali e di conseguenza le proprietà meccaniche.
In particolare, nel presente lavoro l’attenzione è stata rivolta allo studio dell’effetto del trattamento termico innovativo HPT6 (High Pressure T6), che combina il processo di HIP con il tradizionale trattamento termico T6, costituito da tempra di soluzione (solubilizzazione + tempra) e invecchiamento artificiale, tipico per le leghe di alluminio. Il trattamento è stato realizzato da Quintus Technologies AB mediante l’impiego dell’unità Uniform Rapid Quenching (URQ®).
In figura 2 è mostrato un confronto tra il ciclo di post-trattamento convenzionale (a sinistra) e quello innovativo (a destra).
Il principio alla base del funzionamento delle unità per HIP impiegate per l’esecuzione dei trattamenti termici in pressione si basa su un meccanismo di raffreddamento per convezione forzata che consiste nell’impiego di un gas a bassa temperatura che è immagazzinato all’esterno del forno, ma all’interno della camera a pressione (è separata dal forno da barriere isolanti che la proteggono dalle elevate temperature raggiunte all’interno del forno durante il processo di HIP).
Durante la fase di raffreddamento il gas freddo presente all’esterno del forno viene spinto attraverso appositi ventilatori all’interno in modo da raffreddare i componenti trattati e le pareti del forno, mentre il gas caldo presente nel forno è fatto circolare all’esterno dove si raffredda a seguito della miscelazione con il gas freddo e tramite il contatto con le pareti raffreddate ad acqua della camera a pressione che agisce quindi come uno scambiatore di calore.
Le elevate velocità di raffreddamento raggiungibili mediante tali unità sono garantite dal fatto che il gas raffreddante, trovandosi ad alta pressione, è caratterizzato da una densità elevata e, quindi, da una elevata conducibilità termica.
Questo permette di ottimizzare lo scambio termico e l’asportazione di calore dal componente, e quindi di ottenere raffreddamenti molto rapidi.
Oltre a vantaggi di natura economica e logistica derivanti da una riduzione del numero di step di post-trattamento e quindi del tempo totale di ciclo, la possibilità di unificare le fasi di HIP e di trattamento termico permette anche di ridurre la storia termica del componente con conseguente risvolto positivo sia in termini di impatto ambientale del processo produttivo che sulle proprietà del materiale, il quale permane ad alta temperatura per tempi inferiori.
Inoltre, la possibilità di temprare il materiale mediante l’impiego di un gas raffreddante direttamente nella camera di HIP permette di ridurre sensibilmente gli shock termici a cui va incontro il materiale con conseguente diminuzione degli stress termici e, quindi, del rischio di distorsione e criccatura (si parla infatti di soft quenching).
Ciò deriva dal fatto che, a differenza che nel processo di tempra tradizionale in acqua o in olio in cui il componente è immerso in un mezzo raffreddante a temperatura molto più bassa, in questo caso il mezzo raffreddante è costituito dallo stesso gas impiegato per la fase di densificazione, il quale quindi all’inizio del raffreddamento si trova alla stessa temperatura del componente.
Successivamente, tale gas è progressivamente raffreddato mediante il meccanismo di convenzione forzata descritto in precedenza determinando il raffreddamento del componente.
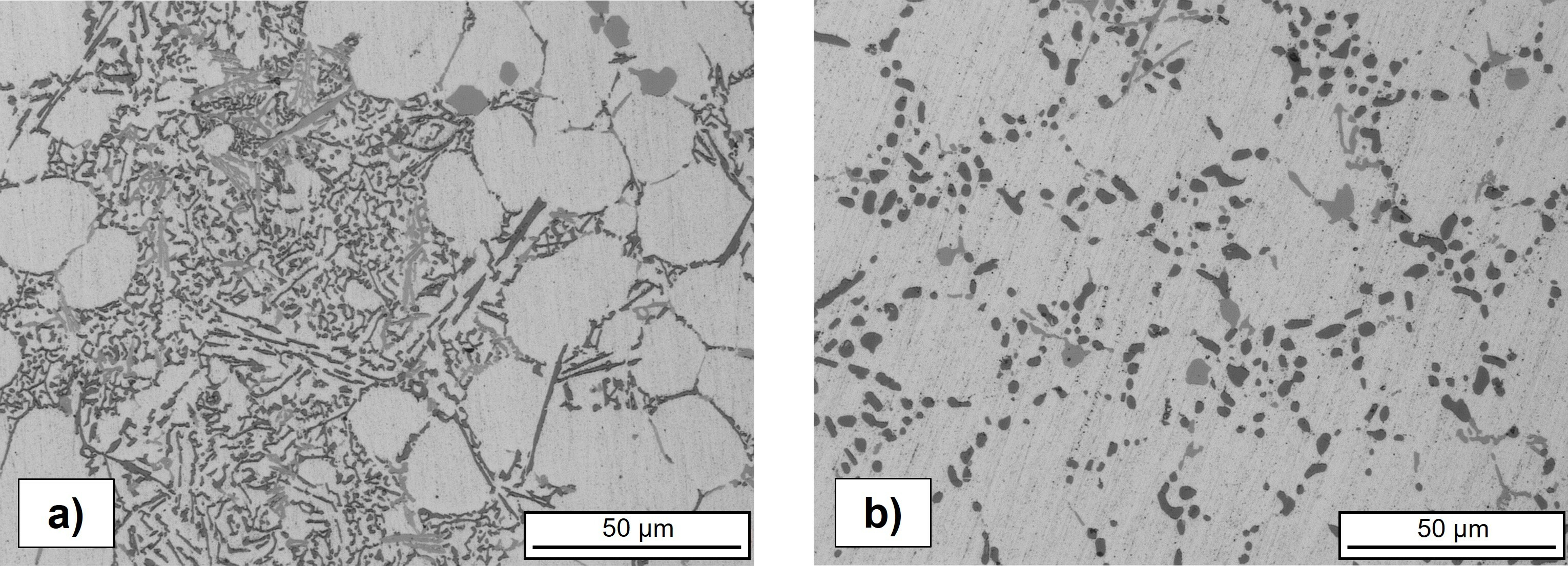
Infine, l’esecuzione del trattamento termico in pressione permette anche di contrastare in modo efficace l’espansione delle porosità da gas in fase di trattamento termico e lo sviluppo del fenomeno del blistering.
Questo è un punto molto importante in quanto l’impiego della pressione in fase di trattamento termico potrebbe consentire l’esecuzione di trattamenti termici normalmente non possibili per i getti pressocolati standard in lega di alluminio (come il trattamento T6), rappresentando il punto di partenza per un futuro impiego di questa tipologia di getti anche in applicazioni strutturali nelle quali al momento non possono essere utilizzati.
Caso di studio: trattamento termico HPT6
I campioni oggetto del presente studio sono stati prelevati dai canali di colata di un componente industriale in lega AlSi10Mg prodotto per pressocolata da Ghial Spa.
In particolare, sono stati ricavati 5 campioni prismatici per le prove di durezza e le caratterizzazioni microstrutturali e 20 provini di trazione, aventi dimensioni e geometria in accordo con la normativa UNI EN ISO 6892-1.
I campioni sono stati testati nella condizione as-cast e in quattro diverse condizioni di trattamento termico indicate rispettivamente con le sigle T6, HIP+T6, HPT6-520 e HPT6-540.
In particolare, per quanto riguarda il trattamento HPT6 sono state valutate due possibili alternative (HPT6-520 e HPT6-540) che si distinguono unicamente per la temperatura della fase di solubilizzazione in modo da poter effettuare un confronto diretto con le tradizionali condizioni HIP+T6 e T6.
Una rappresentazione schematica dei cicli termici e di pressione impiegati è mostrata in figura 3.
Al termine del trattamento termico i campioni sono stati sottoposti sia ad attività di caratterizzazione microstrutturale sia a prove di densità, di trazione uniassiale e di durezza per valutare gli effetti del trattamento termico innovativo HPT6.
Le analisi sono state svolte presso i laboratori di Metallurgia del Dipartimento di Ingegneria Meccanica e Industriale dell’Università degli Studi di Brescia.
Al fine di valutare l’efficacia del trattamento HPT6 in termini di densificazione del materiale sono state inizialmente eseguite delle prove di densità. Dai risultati ottenuti (fig. 4) si osserva che, rispetto alle condizioni T6 e HIP+T6, in cui si ha una riduzione della densità rispetto alla condizione as-cast per effetto dell’espansione del gas contenuto all’interno delle porosità da gas in fase di trattamento termico (il livello di porosità infatti aumenta), il trattamento termico HPT6 porta all’ottenimento di una densità comparabile con quella nella condizione as-cast in quanto il mantenimento della pressione in fase di trattamento termico permette di contrastare in modo efficace la pressione esercitata dal gas contenuto all’interno delle porosità impedendone l’espansione (il livello di porosità è infatti ridotto sia nella condizione HPT6-520 che nella condizione HPT6-540).
La densità nella condizione HPT6-520 è leggermente superiore rispetto a quella nella condizione HPT6-540 per effetto della temperatura di solubilizzazione più bassa.
All’aumentare della temperatura di solubilizzazione, infatti, aumenta la quantità di energia che viene fornita al gas presente nelle porosità che, favorito dalla riduzione della resistenza del materiale con la temperatura, è quindi in grado di espandere maggiormente.
Una volta verificata l’efficacia del trattamento HPT6 in termini di densificazione del materiale la microstruttura dei campioni pressocolati è stata osservata al microscopio ottico metallografico LEICA DMI 5000 M.
In figura 5 a-b è riportata la microstruttura dei campioni pressocolati rispettivamente nella condizione as-cast e nella condizione HPT6-540 (è stata scelta come condizione rappresentativa delle diverse condizioni di trattamento termico studiate).
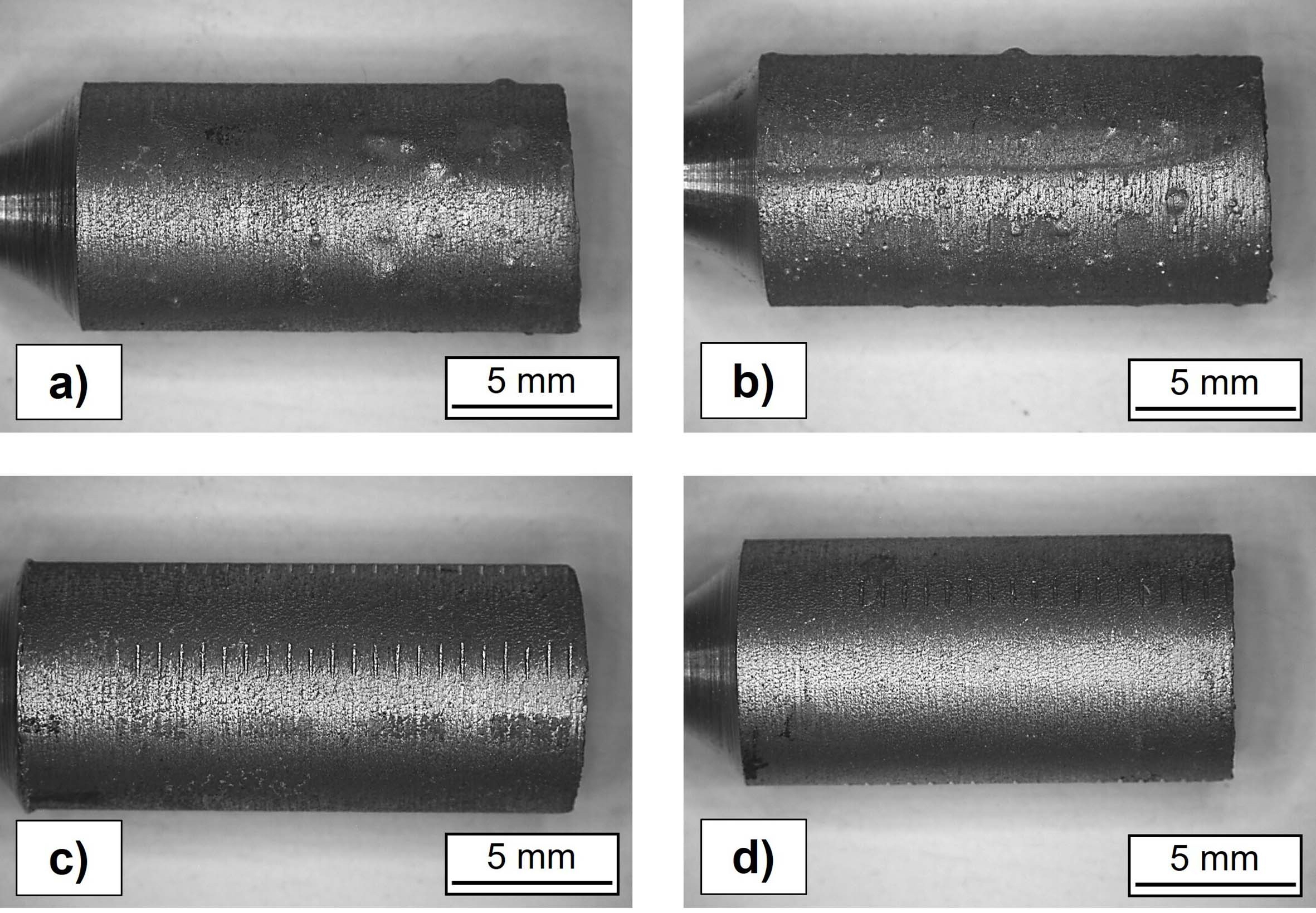
Nella condizione as-cast si riconosce una microstruttura dendritica composta da dendriti di fase α-Al primaria circondate da eutettico Al-Si con una struttura lamellare, mentre a seguito del trattamento termico si osserva una omogeneizzazione della lega e una variazione della morfologia del Si eutettico che da lamellare diventa globulare.
Osservando la microstruttura ad ingrandimenti più bassi è stato possibile eseguire un confronto qualitativo tra i livelli di porosità nelle diverse condizioni testate (fig. 6) che conferma i risultati ottenuti dalle prove di densità.
Nelle condizioni HPT6 non si osserva infatti la presenza di porosità da gas di dimensioni significative, che sono invece chiaramente visibili nelle condizioni T6 e HIP+T6, a conferma dell’effetto benefico dell’applicazione della pressione in fase di trattamento termico. Infine, sono state condotte attività di caratterizzazione meccanica tramite l’esecuzione di prove di durezza Brinell e prove di trazione mediante la macchina di prova Instron 3369 dotata di una cella di carico di 50 kN.
Purtroppo, a causa della presenza di un intenso fenomeno di blistering (fig. 7 a-b) che ha portato alla rottura dei provini di trazione in fase di lavorazione alle macchine utensili, è stato possibile testare solamente un provino nella condizione T6, mentre non è stato possibile testare i provini nella condizione HIP+T6. Tale problematica non è invece stata rilevata nel caso dei provini nella condizione HPT6-520 e HPT6-540, come evidente dalla figura 7 c-d.
Dai risultati delle prove meccaniche (fig. 8) è possibile affermare che il trattamento termico HPT6 è efficace anche in termini di incremento delle prestazioni del materiale sia in termini di durezza (che raggiunge un valore di circa 100 HB) che di proprietà a trazione.
In particolare, il carico unitario di snervamento dopo trattamento HPT6 è superiore ai 200 MPa, mentre il carico di rottura mediamente si avvicina ai 300 MPa. Oltre alla resistenza, anche l’allungamento percentuale beneficia di questa tipologia innovativa di trattamento termico, e questo è dovuto principalmente a due fattori.
Innanzitutto, la possibilità di eseguire l’intero ciclo di trattamento termico all’interno della stessa unità permette di massimizzare l’efficacia della tempra, e quindi del successivo invecchiamento, in quanto permette di annullare il quench delay time, ovvero l’intervallo di tempo necessario allo spostamento del componente dal forno di solubilizzazione alla vasca di tempra, che è uno dei principali parametri che influenza la quantità di atomi in soluzione solida disponibili per il successivo processo di invecchiamento.
In particolare, nel corso del quench delay time la lega si trova a temperatura ambiente e quindi va incontro ad un raffreddamento lento con conseguente formazione di precipitati grossolani non indurenti a bordo grano che non contribuiscono al rafforzamento della lega.
Realizzando l’intero ciclo di trattamento termico all’interno della stessa unità invece ciò non accade poiché il quench delay time è completamente azzerato, permettendo di massimizzare la quantità di atomi in soluzione solida e, quindi, l’efficacia del processo di invecchiamento artificiale.
L’effetto di indurimento è anche favorito dall’applicazione della pressione.
Per effetto della pressione, infatti, si osserva una riduzione della diffusività degli atomi di Si e di Mg, la quale permette di ritardare la sequenza di precipitazione e, quindi, la coalescenza dei precipitati Mg2Si rispetto al trattamento di invecchiamento eseguito a pressione atmosferica (più i precipitati sono finemente dispersi nella matrice, maggiore è la loro capacità di rafforzare la lega).
Inoltre, la riduzione del livello di porosità ad opera della pressione applicata favorisce ulteriormente l’incremento della durezza e delle proprietà a trazione.
La presenza di porosità, infatti, è dannosa in quanto riduce notevolmente la capacità di carico del materiale e favorisce l’innesco e la propagazione della frattura.
Quindi, una loro rimozione garantisce importanti vantaggi dal punto di vista delle prestazioni meccaniche.
Il trattamento termico HPT6 permette infatti di incrementare in modo significativo sia la resistenza (carico unitario di snervamento e carico unitario di rottura) che la duttilità (allungamento percentuale) rispetto alla lega nella condizione as-cast oltre che la durezza, come è evidente dalla figura 8.
È importante però sottolineare che tali risultati sono stati ottenuti a partire da provini ricavati dai canali di colata, quindi da materiale caratterizzato da una maggiore quantità di impurità rispetto al getto, la cui presenza influenza fortemente le proprietà meccaniche del materiale determinando anche dei problemi di ripetibilità della misura.
Pertanto, in figura 8b sono riportate le curve sforzo-deformazione rappresentative del comportamento del materiale nelle diverse condizioni.
A tal proposito, visti i primi risultati incoraggianti, seguiranno in un prossimo futuro degli studi su getti reali al fine di confermare quanto osservato mediante il presente studio e valutare con maggiore precisione le prestazioni meccaniche raggiungibili mediante l’impiego del trattamento termico HPT6.
Conclusioni
Lo studio ha riguardato l’analisi dell’effetto di trattamenti termici innovativi sulle proprietà di componenti in lega AlSi10Mg realizzati mediante pressocolata.
In particolare, l’attenzione è stata rivolta all’applicazione di un innovativo trattamento termico T6 eseguito sotto pressione denominato HPT6 che combina il processo di pressatura isostatica a caldo (HIP) con il tradizionale trattamento T6 delle leghe di alluminio allo scopo di ottenere in un unico step una effettiva densificazione del materiale insieme all’effetto di indurimento promosso dal trattamento T6.
Dai risultati ottenuti il trattamento termico HPT6 si è dimostrato essere una soluzione efficace per trattare termicamente i getti pressocolati standard senza andare incontro alla formazione di porosità termicamente indotte e allo sviluppo del fenomeno del blistering, che sono le principali problematiche tradizionalmente associate al trattamento termico di tale tipologia di getti.
I campioni sottoposti al trattamento termico HPT6 presentano infatti densità comparabili con quella nella condizione as-cast e sensibilmente superiori rispetto a quella nelle condizioni T6 e HIP+T6, oltre che migliori proprietà sia in termini di resistenza che di duttilità.
Questo è un risultato molto importante in quanto rappresenta il punto di partenza per un futuro impiego dei getti pressocolati standard anche in applicazioni strutturali nelle quali al momento non possono essere utilizzati.
Inoltre, la possibilità di ottimizzare le proprietà meccaniche mediante trattamento termico permetterebbe anche di ampliare l’utilizzo di leghe secondarie in sostituzione a quelle primarie per la produzione di componenti strutturali, con conseguente impatto positivo sia in termini di sfruttamento delle materie prime che di impatto ambientale.
Ringraziamenti
Si ringrazia Ghial Spa per aver fornito i campioni e Quintus Technologies AB per l’esecuzione dei trattamenti termici in pressione.
Riferimenti
- H.X. Lu, Q. Zhu, S.P. Midson, W.Y. Qu, F. Zhang, D.Q. Li: Forming conditions of blisters during solution heat treatment of Al–Si alloy semi-solid die castings, Rare Metals, 1-8, 2018.
- P. Niu, B.H. Hu, I. Pinwill, H. Li: Vacuum assisted high pressure die casting of aluminium alloys, Journal of Materials Processing Technology, Vol. 105, 119-127, 2000.
- R.N. Lumley, R.G. Odonnell, D.R. Gunasegaram, M. Givord: Heat treatment of high-pressure die castings, Metallurgical and Materials Transactions A, Vol. 38A, 2007.
- H.V. Atkinson, S. Davies: Fundamental aspects of hot isostatic pressing: an overview, Metallurgical and Materials Transactions A, Vol. 31, No. 12, 2981-3000, 2000.
- S. Hafenstein, M. Brummer, M. Ahlfors, E. Werner: Combined hot isostatic pressing and heat treatment of aluminum A356 cast alloys, HTM Journal of Heat Treatment and Materials, Vol. 71, No. 3, 117-124, 2016.
- M. Tocci, A. Pola, M. Gelfi, G.M. La Vecchia: Effect of a new high-pressure heat treatment on additively manufactured AlSi10Mg alloy, Metallurgical and Materials Transactions A, Vol. 51, No. 9, 4799-4811, 2020.
- C. Beamer: The use of Modern HIP equipment for the investment castings industry, IVI Virtual Conference, 10/06/2020.
- A. Angré, M. Ahlfors, D. Chasoglou, L. Larsson, E. Claesson, O. Karlsson: Phase transformation under isostatic pressure in HIP, Powder Metallurgy, Vol. 60, No. 3, 167-174, 2017.
- https://quintustechnologies.com// (marzo 2022).