L’implementazione di un performante software di simulazione del processo di stampaggio della lamiera distribuito da Vision Forming Solutions ha permesso a Bora di ridurre al minimo le attività di prova stampo e relative messe a punto, migliorando in modo significativo tempi di attraversamento ed elevando ulteriormente la propria competitività.
Più di 45 milioni di pezzi stampati, per oltre 20.000 tonnellate di materia prima lavorata, con 350 codici articolo in produzione.
Sono questi alcuni numeri riferiti allo scorso anno di attività ma ben rappresentativi del potenziale di Bora, azienda specializzata nella progettazione, costruzione e manutenzione di stampi, oltre che di stampaggio a freddo di componenti in metallo per i settori dell’elettrodomestico e dell’automotive.
Componenti meccanici di varia tipologia accomunati dal fatto che negli ultimi anni (soprattutto nel mercato automotive) hanno dovuto garantire prestazioni sempre più elevate.
«Ciò – sottolinea Giuseppe Flocco, R&D Manager, responsabile per progettazione, costruzione e tuning di stampi in Bora – è dovuto essenzialmente al fatto che i progetti dei nostri clienti del comparto automotive da noi servito, ma non solo, si stanno sviluppando in un contesto di mercato di forte innovazione e continuo sviluppo».
Le ripercussioni di questo scenario si riflettono così in un aumento del numero e della complessità dei requisiti che i componenti stampati e assemblati devono garantire.
«A titolo puramente esemplificativo – rileva Flocco – posso citare tolleranze dimensionali e geometriche sempre più stringenti, requisiti che riguardano il livello di pulizia del componente, soprattutto per i particolari destinati ad applicazioni legate alla mobilità elettrica, requisiti di leakage e flussimetrie di valvole integrate nel componente stampato, requisiti dinamici degli assemblati.»
Altro effetto di questa aumentata competitività è la riduzione del lead time disponibile per lo sviluppo, il tuning, e l’industrializzazione della linea di produzione.
«In particolare – osserva Flocco – quest’ultimo punto è molto sfidante. Di fatto l’unica fase in cui ci sono margini nel ciclo di sviluppo è il tuning, ovvero la messa a punto degli stampi. Infatti, le altre fasi, e mi riferisco alla progettazione, alla costruzione e al montaggio, hanno tempi che, oltre un certo limite, diventano “incomprimibili”. Di conseguenza la sfida è quella di riuscire a sviluppare un concept di processo il più robusto possibile e validato in ambiente virtuale, in modo da ridurre al minimo le operazioni di fine tuning.»
Ed è proprio con il preciso l’obiettivo di sviluppare un concept di processo affidabile e in grado di ridurre al minimo le costose e lunghe operazioni di fine tuning dopo la realizzazione dello stampo e delle attrezzature, che Bora decide di puntare su adeguati e performanti strumenti.
«Circa 7 anni fa – conferma Flocco – abbiamo implementato all’interno del nostro processo di sviluppo anche la fase di simulazione solida del processo di stampaggio, effettuata tramite il software Stampack.»
Dalla simulazione semplice alla produzione efficace ed efficiente
Distribuito in Italia da VISION Forming Solutions, Stampack Xpress è un software di simulazione virtuale dei processi di stampaggio della lamiera per stampi di imbutitura, stampi a passo e transfer per componenti in svariati materiali.
Il software guida il progettista in una sequenza logica nel processo di simulazione in modo semplice ed efficace, a partire dallo spezzone, passando per la definizione del materiale, degli utensili e i parametri tecnologici di stampaggio simulando la pressa a video.
L’implementazione di questo ambiente di simulazione nel processo di definizione del metodo CAD, consente di validare un’idea progettuale prima ancora di aver completato la fase di definizione dello stampo, riducendo così al minimo le attività di prova stampo e relative messe a punto.
«Se in precedenza il risultato dei progetti più complessi – rileva Flocco – dipendeva principalmente dall’intuizione e dalla sensibilità del team di tool design, al contrario, validando sempre il metodo di stampaggio attraverso la simulazione FEM, riduciamo in maniera sostanziale il numero e l’impatto delle operazioni di messa a punto sugli stampi dopo il primo try-out.
Dopo l’introduzione dell’utilizzo della piattaforma Stampack e di questa tecnologia di simulazione abbiamo constatato come il metodo di stampaggio sia stato sempre validato e non sia stato mai più necessario aggiungere alcuni passaggi, oppure modificare in modo sostanziale il processo ipotizzato. Con effetti positivi in termini di tempi di attraversamento, a favore di maggiore efficienza ed efficacia produttiva, nonché competitività».
In che modo il software fornito da VISION Forming Solutions è diventato negli anni di grande supporto in Bora e in che termini?
«Oltre che durante la fase di tool design – commenta Flocco – non è raro modellare e validare il processo anche nella fase di offerta iniziale. In questa fase i risultati delle simulazioni effettuate con Stampack Xpress vengono impiegati per confermare le richieste di tolleranze fatte dai nostri clienti, per operazioni di co-design durante lo sviluppo di particolari innovativi. E, non meno importante, per verificare che il tonnellaggio delle presse ipotizzate in fase di offerta sia sufficiente a eseguire correttamente il ciclo di stampaggio.»
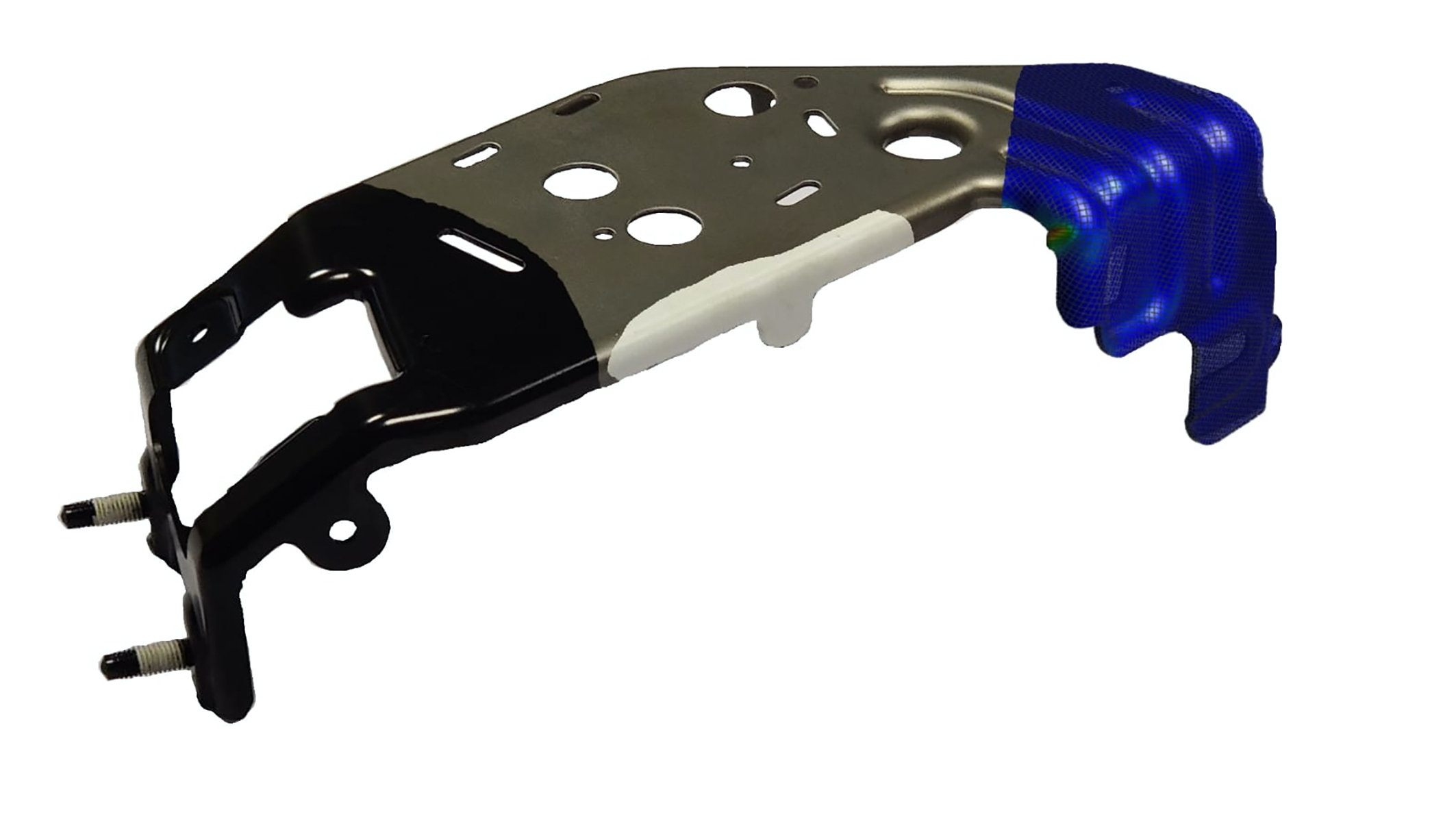
Deformazioni sotto controllo anche nelle condizioni più critiche
Nei propri reparti di produzione stampi Bora è in grado di seguire tutte le fasi della lavorazione dei particolari e si occupa dell’assemblaggio e dell’aggiustaggio degli stampi.
L’azienda dispone di un parco macchine utensili di varie dimensioni e caratteristiche, comprendente tra le altre, numerose fresatrici a CNC, elettroerosioni (a filo e a tuffo), rettifiche e sistemi di taglio.
Sono invece oltre una trentina le presse complessivamente disponibili, presenti tra la sede italiana e quella polacca, con tonnellaggio variabile da 25 a 2500 ton.
«Sulle due presse più grandi – interviene Flocco – quelle da 2500 ton, processiamo lamiere fino a 8 mm di spessore. I componenti che realizziamo sono caratterizzati spesso da alto spessore in relazione ai raggi minimi di imbutitura. Per questo motivo, per analizzare tutte le criticità del processo di stampaggio abbiamo necessità di simulare il comportamento del materiale all’interno dello spessore e non solo superficialmente. Tutto questo è possibile solo utilizzando un modello “solido” a elementi esaedrici invece che “shell” a elementi triangolari. Con questo tipo di simulazione riusciamo a verificare le caratteristiche del materiale del componente stampato in maniera “puntuale” oltre che “integrale”. Inoltre riusciamo a tenere in considerazione tutti gli effetti inerziali durante la deformazione del materiale grazie al solver integrato in Stampack Xpress.»
La simulazione solida, che rappresenta in modo volumetrico il pezzo da stampare (e non solo una pelle), fornisce un importante valore aggiunto per la simulazione su componenti con spessori importanti o per imbutiture profonde.
La simulazione solida fornita da Stampack Xpress permette infatti di simulare deformazioni derivanti da schiacciature, coniature, evidenziare problemi superficiali di estetica del componente stampato, oltre a evidenziare zone di rottura o strappo del materiale.
Comportamento reale anche su geometrie complesse e nuovi materiali
Come già sottolineato, gli ultimi anni sono stati per Bora molto sfidanti dal punto di vista di sviluppo di prodotto, quest’ultimo caratterizzato da design sempre più difficili da realizzare.
Un esempio in particolare ha riguardato la realizzazione di componenti in alluminio legati al mercato della mobilità elettrica.
«Stiamo parlando di componenti stampati – chiarisce Flocco – che si vanno a interfacciare con le varie centraline di gestione e controllo elettroniche. La peculiarità di design più critica è l’estrusione di rivetti, integrati nel componente, che serviranno al montaggio della centralina stessa. Inoltre questi componenti devono essere totalmente esenti da cricche per garantire la corretta funzionalità dell’assieme.»
Per lo sviluppo del processo di produzione che fosse stabile e controllabile, è stato necessario per il team Bora modellare e ottimizzare attraverso svariati cicli di correzione virtuale lo stampaggio.
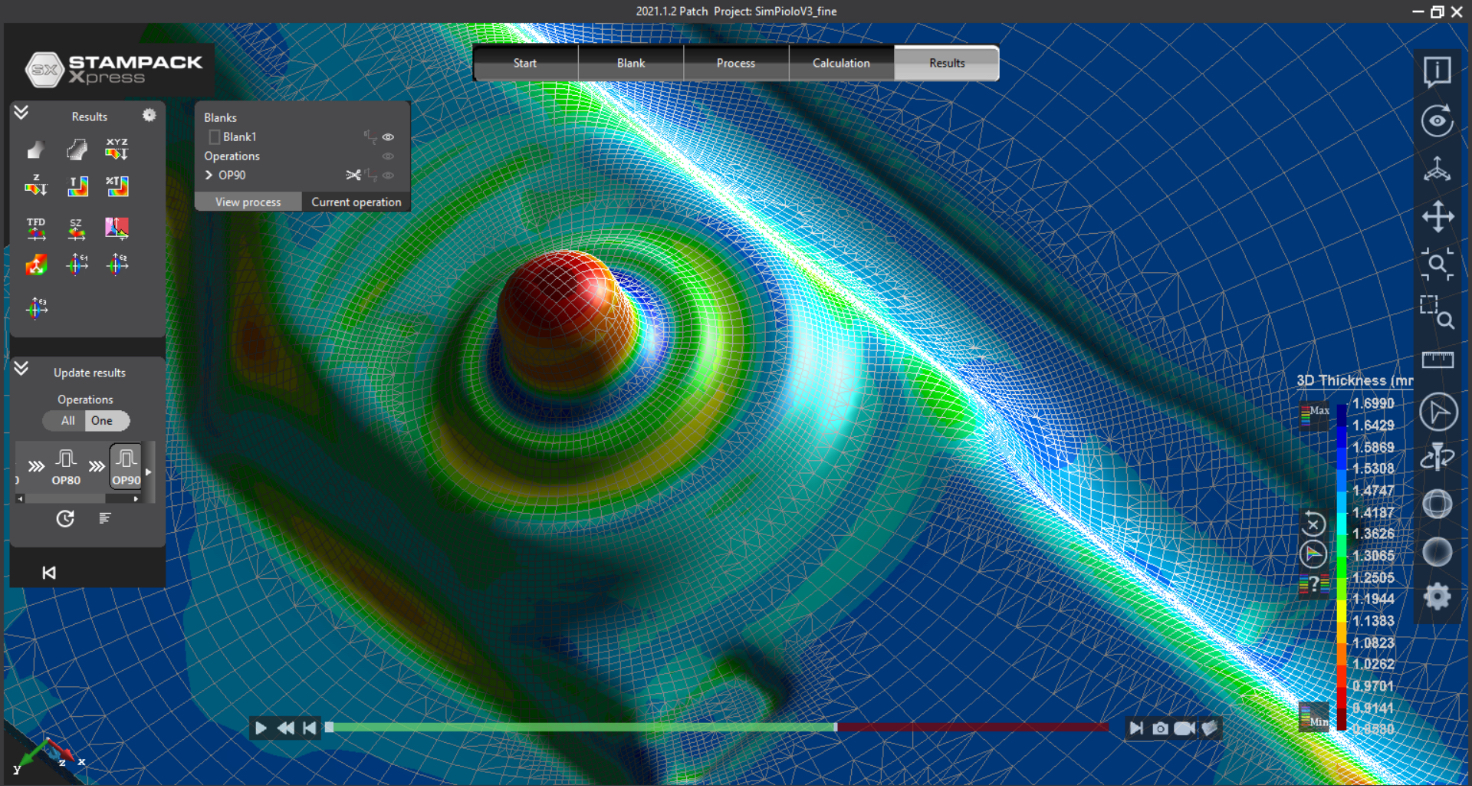
«Ritengo che l’utilizzo di tecniche di prototipazione virtuale – sottolinea Flocco – sia cruciale nello sviluppo di componenti nuovi e con geometrie complesse, cosa peraltro sempre più comune in un mercato dinamico come quello attuale. Per migliorare ulteriormente l’affidabilità dei risultati abbiamo in attivo svariati progetti di collaborazione con il dipartimento di ingegneria industriale e scienze matematiche dell’Università Politecnica delle Marche per la caratterizzazione di dettaglio del legame costitutivo dei materiali da stampaggio a freddo, per esempio alluminio, oppure acciai DX54, DD13 e S355. Questo ci permette di alimentare il software di simulazione con le curve di incrudimento e FLC (Curva Limite di Formabilità), reali e ottenute attraverso test su campioni fisici come possono essere test di trazione, test di rigonfiamento e così via.»
A questo proposito, oltre alla simulazione per componenti in lamiera, acciaio, alluminio, rame, titanio e leghe di metallo, il software Stampack Xpress consente anche una caratterizzazione del materiale da parte dell’utente.
Il sistema dispone infatti di un database di 300 materiali da fornitori differenti. Database che può ulteriormente essere arricchito e aggiornato grazie alle collaborazioni in essere di VISION Forming Solutions con università e laboratori qualificati, per la definizione delle proprietà di nuovi materiali (a uso esclusivo del richiedente), per fornire un servizio ad alto valore aggiunto di coloro che necessitano di sperimentarne o caratterizzarne altri per lo stampaggio.
«Un altro aspetto critico di questo processo – continua Flocco – è la necessità di rispettare dei requisiti di pulizia molto alti. Di conseguenza per ottimizzare il processo di lavaggio, eseguito internamente su tunnel di lavaggio dedicato, è stato necessario investigare la necessità e la tipologia di lubrificazione durante lo stampaggio».
Il valore aggiunto dell’integrazione digitale
Da anni Bora sfrutta dunque tutto il potenziale reso disponibile dal software Stampack Xpress distribuito da Vision Forming Solutions come strumento strategico nelle proprie attività di simulazione, avendolo individuato come idoneo e aderente alle proprie necessità.
«Nella fase iniziale di scelta del software – ricorda e conclude Flocco – un parametro importante che era stato preso in considerazione aveva riguardato senza dubbio la simulazione solida oltre all’elevata integrazione del sistema FEM con il CAD in uso. Questo avrebbe così permesso, come poi è realmente stato, di facilitare, di velocizzare e di ridurre, se non annullare, i possibili errori durante le frequenti operazioni di importazione ed esportazione di modelli tra software diversi. Nell’ultimo anno abbiamo implementato l’utilizzo di licenze flottanti in maniera da rendere ogni nostro progettista autonomo per la simulazione virtuale del processo di stampaggio. Questa scelta tende a far aumentare la consapevolezza delle criticità di ogni operazione a tutti i nostri progettisti.»
Dal co-design alla prototipazione, dalla simulazione allo stampaggio
Fondata nel 1975, Bora rappresenta un punto di riferimento nel mercato della progettazione e nella costruzione stampi e nello stampaggio a freddo della lamiera per i prevalenti settori dell’elettrodomestico e dell’automotive.
Nel primo periodo di attività l’azienda si occupa della progettazione e costruzione stampi per poi, negli anni 80, integrare il servizio al cliente introducendo anche lo stampaggio. Attività quest’ultima che si svilupperà negli anni successivi fino a diventare il core business principale con una presenza strategica sul mercato europeo.
«Possiamo vantare un’esperienza di oltre 45 anni – dichiara l’amministratore delegato e direttore commerciale, Cristiano Bora – alla quale si è aggiunta negli ultimi anni anche la profonda competenza maturata nell’ambito dell’analisi FEM e della simulazione del processo stesso di stampaggio. In tal modo possiamo offrire ai nostri clienti un servizio completo che contempli dunque anche la parte di co-design e quella di prototipazione, oltre che la saldatura e il supporto al cliente con eventuali piccoli assemblaggi.»
Le attività sono svolte in due importanti siti produttivi, uno in Italia, presso la sede principale a Maiolati Spontini (AN) e uno in Polonia, inaugurato nel 2006 nel distretto di Radomsko, entrambi certificati UNI EN ISO 9001:2015, IATF 16949:2016, UNI EN ISO 14001:2015 e UNI EN ISO 45001:2015, dove sono presenti linee di produzione automatiche transfer e progressive per soddisfare le più diverse esigenze.
«La nostra struttura operativa – precisa Bora – può contare su un ampio e articolato parco macchine, comprendente per la prevalente fase di stampaggio un complessivo di oltre una trentina di presse, con tonnellaggio compreso tra 25 e 2500 ton. A completamento del ciclo di sviluppo di prodotto si aggiungono poi linee di lavaggio di saldatura, linee di assemblaggio.»
A garantire i più elevati livelli di efficienza e competitività in Bora c’è oggi anche una logistica evoluta e tecnologicamente avanzata del sistema di gestione magazzino, che ha permesso all’azienda di rendere il flusso della propria supply chain ulteriormente ottimizzato.
«In un mercato sempre più competitivo – conclude Bora – è più che mai necessario prestare attenzione all’intero ciclo di sviluppo di prodotto, cercando di intervenire laddove vi siano opportunità per apportare miglioramenti operativi e per ottimizzare le varie fasi di processo. Ne sono un esempio l’integrazione del software Stampack Xpress per la parte di simulazione del processo stesso di stampaggio e la più recente rivisitazione della gestione della logistica interna.»
In entrambi i casi rappresentano la spiccata vocazione dell’azienda marchigiana verso una produzione e gestione dei processi sempre più digitalizzate.