Uno studio proposto dai ricercatori cinesi mostra un’interessante soluzione di monitoraggio di processo: tramite misure non distruttive e relativamente semplici è infatti possibile approfondire quanto sta avvenendo durante una tradizionale operazione di tranciatura.
La qualità produttiva, da sempre, è motivo di orgoglio e vanto per la manifattura italiana. Questa caratteristica del componente finale diventa sempre più importante. Oggi moltissimi settori richiedono prodotti in grado di soddisfare gli ultimi standard qualitativi o anche requisiti superiori.
Il prezzo dei componenti non è sicuramente l’unico fattore da considerare quando ci si trova a valutare un fornitore. Importante è anche assicurare ai clienti prodotti di qualità e in grado di evitare costose riparazioni o fermi.
Queste richieste, unite alle potenzialità offerte dalla rivoluzione di Industria 4.0, stanno spingendo verso la possibilità di offrire prodotti di qualità sempre superiore. I controlli sui componenti diventano sempre più frequenti e permettono sia di migliorare la vita dei componenti che di offrire prestazioni superiori. Tradizionalmente, i controlli qualitativi venivano effettuati tramite test distruttivi di componenti scelti a campione. Una nuova alternativa ora possibile è quella del monitoraggio in tempo reale durante la produzione. Misure effettuate durante le lavorazioni permettono di ottenere misure quantitative, così da poter anticipare la presenza di potenziali danni o criticità.
Tranciatura
La tranciatura è un processo di lavorazione a freddo delle lamiere che permette di ottenere componenti per taglio. Questa lavorazione è caratterizzata dai tempi ridotti e dai costi contenuti, infatti è particolarmente diffusa in ambito industriale. Il processo si basa semplicemente su un punzone e su una matrice adeguatamente progettati per ottenere la separazione di una porzione della lamiera (Figura 1).
È possibile individuare principalmente cinque fasi distinte in questa lavorazione: inizialmente si ha l’avvicinamento del punzone alla lamiera, successivamente inizia la fase di deformazione elastica, il terzo passo è quello di deformazione plastica e inizio delle fratture, in seguito si ha la vera e propria propagazione della frattura, fino ad arrivare alla separazione della lamiera tranciata. In questo processo la qualità è influenzata da diversi fattori che possono condizionare il risultato finale della lavorazione.
Il primo fattore è dato dal materiale da lavorare e dalle sue caratteristiche, successivamente bisogna considerare i parametri di processo. I principali parametri da analizzare durante la tranciatura sono il gioco tra punzone e matrice e l’angolo di taglio. Per ottenere un prodotto di valore bisogna considerare la qualità della superficie di taglio e l’accuratezza della lavorazione. Inoltre, soprattutto per alcuni settori critici come l’aerospazio, risulta importante effettuare misure quantitative durante il processo al fine di assicurare ai componenti così prodotti una lunga vita di utilizzo in sicurezza.
Monitoraggio
Per effettuare i controlli di qualità sulla produzione fino a qualche anno fa l’opzione più diffusa era quella di effettuare test distruttivi a campione. In questo modo è possibile analizzare la microstruttura o l’evoluzione di danni, ma solo su alcuni provini. Un’interessante metodologia che sta rapidamente prendendo piede è quella di monitorare il processo produttivo tramite tecniche di misura indiretta. Nel caso specifico della tranciatura risulta particolarmente interessante ricorrere alle emissioni acustiche (abbreviate come “AE”) per monitorare le varie fasi del processo. Questa tecnologia, come confermano diversi studi, è in grado di quantificare i cambi di microstruttura nel materiale durante la lavorazione. Un’altra interessante tecnica di monitoraggio è quella di correlazione di immagini digitali (Digital Image Correlation o “DIC”). Questa metodologia si basa su immagini ad alta risoluzione per misurare gli spostamenti. Secondo gli autori della ricerca, la singola tecnica di misurazione presenta limitazioni, ma unendo le due metodologie è possibile offrire un’accurata descrizione delle diverse fasi del processo di tranciatura, così da poter valutare anche la qualità della lavorazione.
Sperimentazione
I ricercatori dell’università cinese, per approfondire la questione hanno riprodotto un setup sperimentale (mostrato in Figura 2).
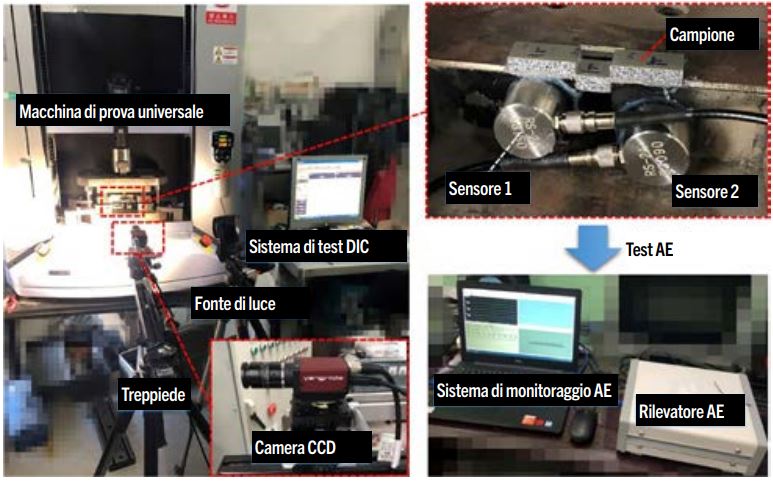
Il materiale lavorato è alluminio 6082-T6, utilizzato per strutture e nel settore dei trasporti grazie all’elevata resistenza alla corrosione, alta resistenza e buona saldabilità. La tranciatura è stata effettuata tramite un macchinario universale con un carico massimo di 50 kN sensorizzato dagli autori. Le immagini sono state registrate da una camera CCD per tracciare l’intero processo.
Invece, le emissioni acustiche sono state misurate da due sensori tra i 50 e i 400 kHz, sono state filtrate e amplificate. I test relativi alle misure acustiche hanno evidenziato l’importanza di processare questo segnale eliminando il rumore di fondo ed estraendo dalla registrazione indicatori da utilizzare in fase di analisi. Sono inoltre state effettuate delle ispezioni metallografiche tramite microscopio elettronico a scansione (SEM) per approfondire quando suggerito dai sensori di monitoraggio durante le diverse fasi del processo.
Risultati
Analizzando i segnali registrati durante la tranciatura è possibile ottenere una descrizione completa di quanto avviene durante la lavorazione. La misura a immagini (Figura 3b) permette di identificare, quantificare e soprattutto localizzare la zona di inizio e propagazione della crepa, identificando le zone più sollecitate. Le emissioni acustiche invece (Figura 3a) possono essere utili a identificare la transizione tra le fasi del processo. In questo modo è possibile misurare la durata di ogni singola fase da utilizzare come indice di qualità e stabilità del processo.
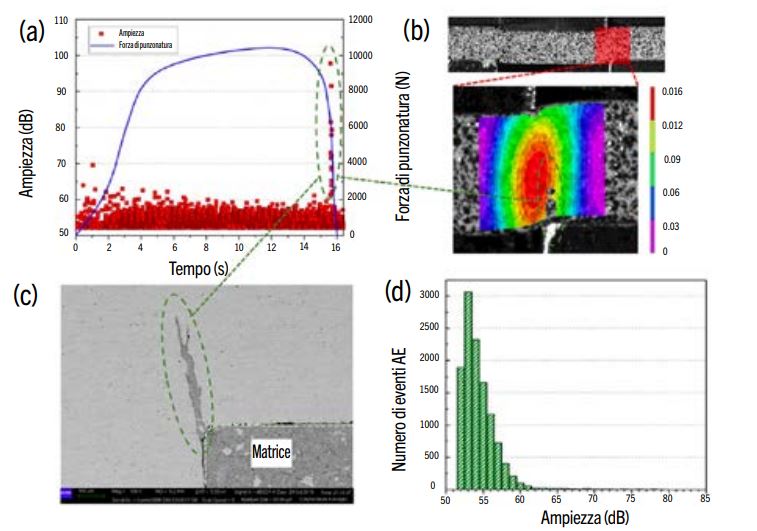
Dal punto di vista di emissioni acustiche la fase di frattura risulta particolarmente densa di eventi ad alta frequenza ed energia. Questo poiché viene rilasciata istantaneamente una grande energia nel momento di formazione della crepa generata dal punzone. Accoppiando le due misure in tempo reale è infatti possibile descrivere accuratamente il processo di tranciatura. Queste misure si sono dimostrate interessanti indicatori di ciò che avviene all’interno del materiale durante la trasformazione, così da poterne misurare e tracciare, seppur indirettamente, l’evoluzione.
Lo studio proposto dai ricercatori cinesi mostra un’interessante soluzione di monitoraggio di processo. Tramite misure non distruttive e relativamente semplici è possibile approfondire quanto sta avvenendo durante una tradizionale tranciatura. In questo modo viene ridotta la necessità di effettuare numerose misure su componenti finiti sprecando tempo e denaro. La sensorizzazione di macchinari apre nuovi scenari per la manifattura.
Queste misure effettuate direttamente durante la lavorazione permettono di identificare anomalie durante il processo di trasformazione dovute, ad esempio, a materiali non conformi o a guasti del macchinario. Così da evitare di consegnare componenti difettosi che potrebbero poi essere scartati dal cliente o, ancora peggio, causare guasti.
Non meno importante è la possibilità di tenere traccia e documentazione delle lavorazioni, assicurando al cliente stabilità e affidabilità dei processi. Il ventaglio di possibilità offerto da queste nuove tecnologie è veramente ampio e permette di sfruttare interessanti opportunità anche a livello aziendale.
A cura di Stefano Grulli
Fonte: Zhao, P., Jiao, J., Tang, Y., & Fang, G. (2021). Investigation on damage evolution and acoustic emission behavior of aluminum alloy sheet during blanking process. The International Journal of Advanced Manufacturing Technology, 117(1-2), 675–688. https://doi.org/10.1007/s00170-021-07770-4