Gli autori di questo studio propongono un complesso approccio teorico per la stima del coefficiente d’attrito di componenti assialsimmetrici. Questo modello non lineare tiene conto dei diversi parametri geometrici e delle forze in gioco durante il processo, per meglio descrivere il fenomeno. Per valutare l’efficacia di questo modello è stato deciso di misurare il coefficiente d’attrito in diverse condizioni, così da poter confrontare i risultati fisici con la teoria.
I processi di trasformazione della lamiera devono la loro notevole diffusione in ambito industriale alla relativa semplicità, alla ridotta necessità di materiali consumabili e all’elevata produttività, pur assicurando costi concorrenziali. In questo modo è infatti possibile ottenere prodotti leggeri e con buone caratteristiche tecniche. Per queste ragioni le lamiere vengono utilizzate in numerosi settori: dall’automotive, fino all’aerospaziale, passando per gli elettrodomestici e il medicale.
L’industria relativa alla trasformazione è quindi un supporto fondamentale alla manifattura locale, giocando un ruolo centrale nell’economia nazionale. Soprattutto in periodi complessi determinati dall’elevata concorrenza, dalla volatilità della domanda e da produzioni disagevoli, diventa fondamentale puntare su qualità ed efficienza.
È un imperativo ridurre quanto più possibile gli sprechi di materiale ed energia, pur mantenendo un adeguato livello qualitativo per i prodotti. In questo difficile scenario la ricerca può proporre interessanti spunti per efficientare la produzione, offrendo nuove possibilità.
Il coefficiente d’attrito
I processi di stampaggio della lamiera sono influenzati da diversi parametri come, ad esempio, le proprietà del materiale, la forza del premilamiera e l’attrito. Quest’ultimo fattore influenza pesantemente il risultato sul prodotto finale, perciò risulta fondamentale una comprensione del fenomeno per minimizzarne gli effetti negativi.
Spesso viene semplificato il problema del coefficiente d’attrito, considerandolo costante come previsto dalla legge di Coulomb. Questa tradizionale legge meccanica prevede una proporzionalità diretta, regolata dal coefficiente d’attrito, tra la forza d’attrito e la forza normale agente sulle due superfici a contatto.
Tale legge, seppure sia universalmente accettata, rappresenta un semplice modello di descrizione del fenomeno di sfregamento. In realtà le condizioni di attrito fluttuano notevolmente e frequentemente durante il processo di formatura della lamiera. Negli ultimi anni, nonostante la complessità di questo tema e le numerose variabili che entrano in gioco, sono stati effettuati alcuni progressi. È stato dimostrato, ad esempio, che la velocità relativa tra i due materiali influenza il coefficiente d’attrito e ovviamente anche le condizioni di lubrificazione sono fondamentali. Gli autori di questo studio si pongono l’obiettivo di progredire in questo campo, analizzando il coefficiente d’attrito su un’imbutitura assialsimmetrica.
Modello di studio
Frequentemente l’imbutitura viene utilizzata per formare componenti cilindrici. Il processo necessita di un punzone, di una matrice e di un premilamiera (come mostrato in Figura 1). La lamiera, vincolata all’interno della pressa, viene deformata per ottenere la geometria desiderata. Il componente subisce differenti deformazioni a seconda della zona in cui si trova.
Solitamente l’attrito da contatto avviene principalmente nella zona di contatto tra premilamiera, lamiera e matrice (zone colorate in rosa e giallo in Figura 1). In questo caso si tiene conto della pressione applicata dal premilamiera nella flangia e nello smusso della matrice. Gli autori dello studio propongono un complesso approccio teorico per la stima del coefficiente d’attrito di componenti assialsimmetrici. Questo modello non lineare tiene conto dei diversi parametri geometrici e delle forze in gioco durante il processo, per meglio descrivere il fenomeno. Per valutare l’efficacia di questo modello è stato deciso di misurare il coefficiente d’attrito in diverse condizioni, così da poter confrontare i risultati fisici con la teoria.
La sperimentazione
È stata effettuata una sperimentazione per valutare il modello teorico confrontandolo con le misure effettuate durante il processo (Figura 2). Per la sperimentazione sono stati impiegati due materiali, entrambi nello spessore di 1 mm: una lega alluminio-magnesio Al-5754 e un acciaio laminato a freddo SPCC. Gli autori hanno effettuato le misure tramite un sistema auto sviluppato in grado di registrare i dati durante il processo grazie ad un programma MATLAB per elaborare le informazioni.
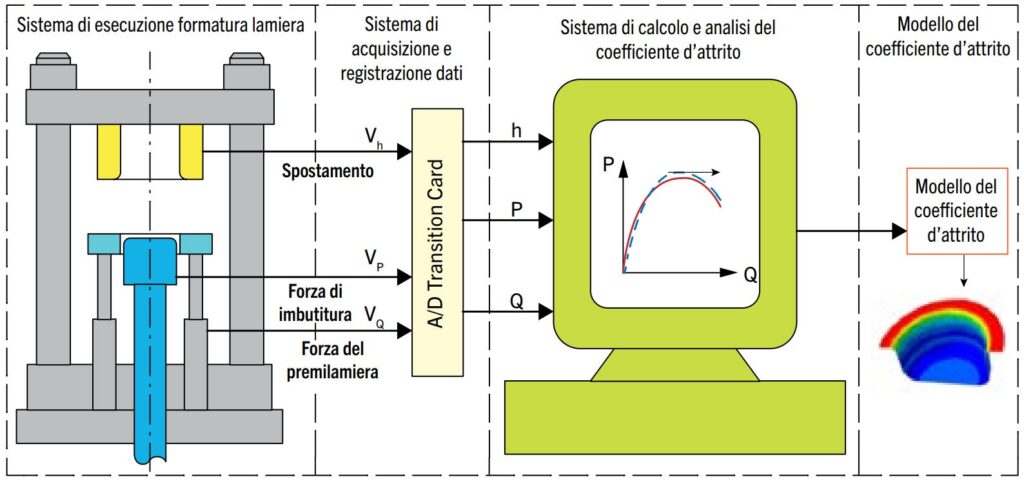
Conoscendo la corsa del punzone e le due forze in gioco (punzone e premilamiera) è possibile tracciare i grafici ed effettuare una misura del coefficiente d’attrito. Tre esperimenti per ogni gruppo sono stati svolti, così da poter calcolare una media e confrontare il modello teorico con il misurato.
I risultati
Le curve ottenute sperimentalmente offrono una buona concordanza con quelle ottenute dal modello teorico. Tuttavia è possibile notare che il modello teorico risulta essere più adeguato alle fasi finali del processo di imbutitura, poiché inizialmente è possibile notare un’adesione tra le superfici prima di entrare in regime di attrito dinamico. Il confronto tra modelli risulta qualitativamente simile su entrambi i materiali analizzati, sottolineando la validità dell’approccio utilizzato.
Inoltre, l’attrito durante il processo di imbutitura è stato simulato anche utilizzando un software di simulazione ad elementi finiti: ABAQUS. Questa tecnica permette di dividere il componente in diversi elementi e simularne le interazioni durante il processo. In questo modo è possibile ottenere una previsione del risultato finale del processo, senza dover investire in tempo macchina, materiale e misure. Per effettuare la simulazione sono stati impostati tutti i parametri geometrici dello strumento e del materiale.
Come modelli per l’evoluzione dell’attrito è stato effettuato un paragone tra coefficiente costante e modello a coefficiente variabile.
In Figura 3 è possibile apprezzare questa analisi dove sono confrontati coefficiente fisso, variabile e modello reale. È possibile notare come il modello più complesso a coefficiente d’attrito variabile permetta di offrire una miglior accuratezza della simulazione, offrendo agli utilizzatori dei software ad elementi finiti maggiore accuratezza.
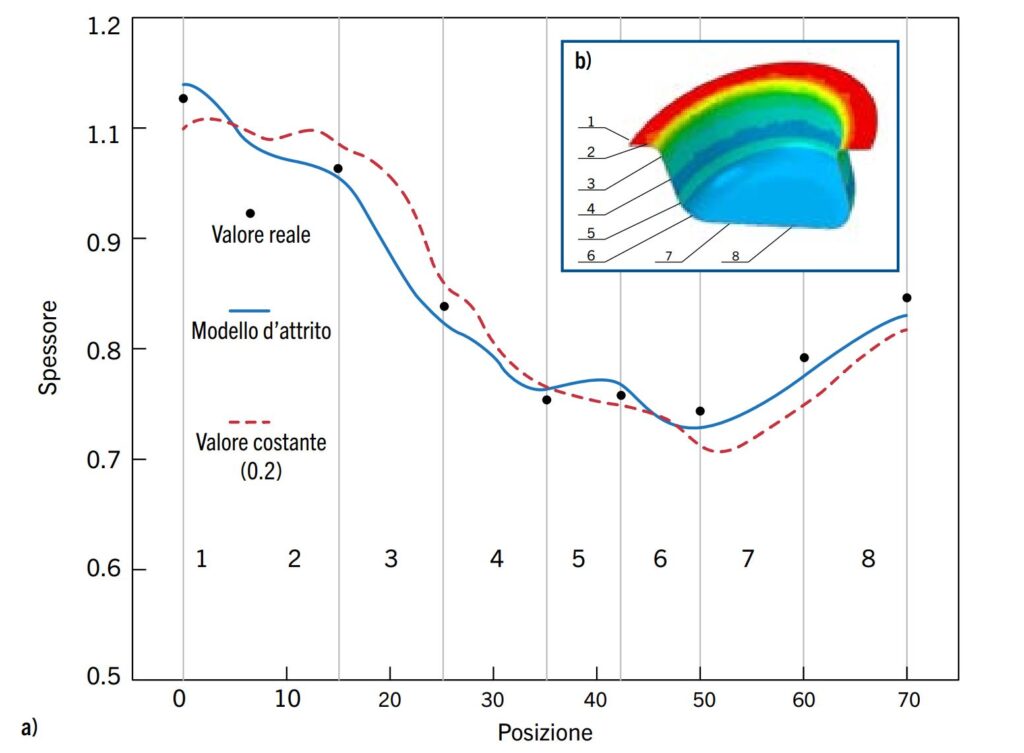
Se fino a pochi anni fa l’applicazione di simulazioni a elementi finiti e modelli complessi erano limitati a grandi aziende e centri di ricerca ora non è più così.
L’aumento delle potenze di calcolo disponibili su PC e workstation permettono un’ampia diffusione di queste tecnologie. Le soluzioni commerciali di simulazione diventano sempre più diffuse nel mondo industriale e oggi è relativamente semplice approcciarsi a questo mondo. Anche piccole aziende possono ormai effettuare complesse simulazioni di processo ottenendo stime sul risultato dei componenti finali.
Il vantaggio diventa significativo poiché è possibile anticipare rotture o non conformità, senza dover fermare macchinari di produzione per effettuare prove onerose dal punto di vista di tempi e costi. In questo contesto in rapida evoluzione risultano particolarmente preziose ricerche in grado di incrementare l’accuratezza e l’affidabilità di questi sistemi di simulazione, per supportare sempre le richieste del mondo industriale.
A cura di Stefano Grulli
Fonte: Xia, J., Zhao, J., Dou, S., & Shen, X. (2022). A novel method for friction coefficient calculation in metal sheet forming of axis-symmetric deep drawing parts. Symmetry, 14(2), 414. https://doi.org/10.3390/sym14020414