Per microlavorazioni si intendono quei processi di realizzazione di componenti con dimensioni nell’ordine dei micron, più precisamente quando le tolleranze ottenute da queste sono inferiori ai 10 micron
Il grande interesse scientifico e industriale che recentemente si è sviluppato, parte da esigenze di mercato provenienti dal mondo microelettronico, dal mondo dei dispositivi medici, fino al mondo aerospaziale e dell’ottica per le produzioni di lenti e specchi con finiture superficiale di altissima qualità, per la creazione, ad esempio, dei cosiddetti MEMS (microelectromechanical systems) e circuiti integrati.
Ad esempio, una delle applicazioni in cui le microlavorazioni trovano impiego è nel campo della ricerca biologica, dove sono necessari per la manipolazione delle cellule a livello micro e nano, dei dispositivi in grado di interagire con le strutture in quell’ordine di grandezza. Per esempio, i dispositivi a microfluidi che sono dei canali e camere minuscoli incisi su un substrato, vengono utilizzati per studiare il comportamento a livello cellulare e per eseguire reazioni chimiche mirate, rendendo possibile lo studio e la capacità di analisi a livello di dettaglio impossibile per i metodi tradizioni (ad esempio nell’analisi dei geni).
È possibile poi suddividere ulteriormente a seconda se il processo di asportazione del truciolo sia strettamente utilizzato nel mondo micro, come ad esempio le tecnologie utilizzate per l’industria elettronica come la fotoincisione e placcatura elettrica dei wafer di silicio, oppure siano dei processi provenienti dal mondo macro (come la microfresatura).
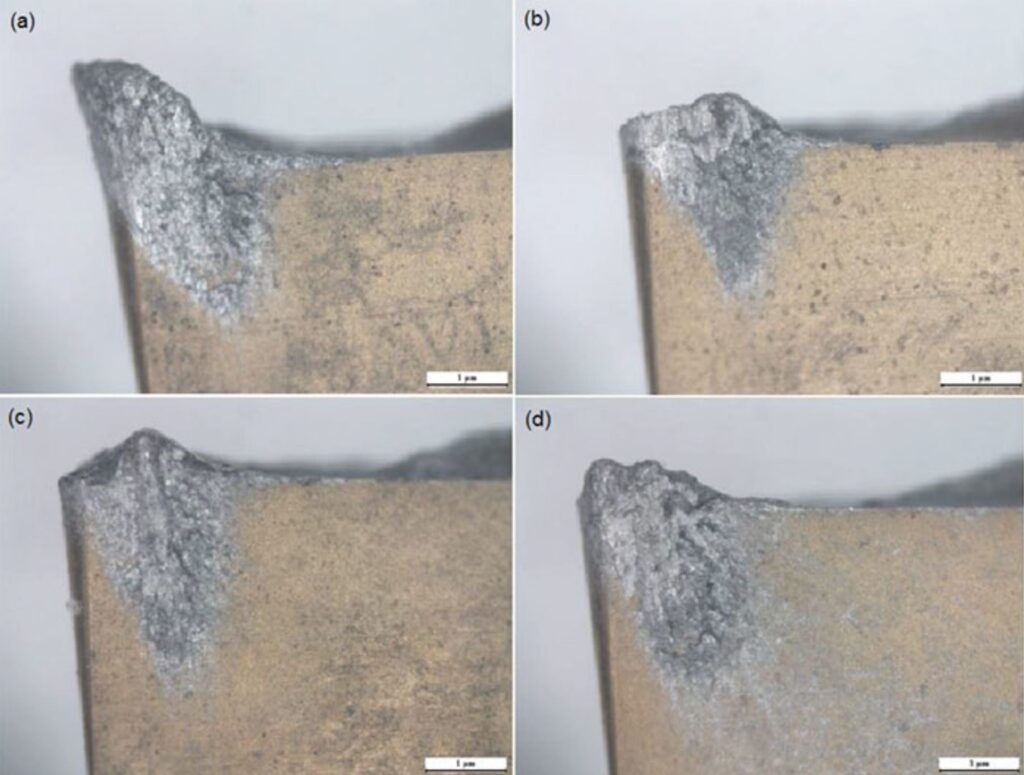
Le problematiche da affrontare nelle microlavorazioni
Nei processi di asportazioni di truciolo, il ridimensionamento in generale della scala di lavorazione non comporta un cambiamento della caratteristiche principali della stessa, ma quando il rapporto tra le dimensioni dell’utensile utilizzato e le dimensioni medie dei grani del materiale è prossimo a uno, viene meno un’assunzione spesso fatta per le lavorazioni macro; ovvero, che il materiale sia omogeneo e isotropo (vale a dire che le caratteristiche del materiale sono indipendenti dalla posizione e dalla direzione di lavorazione) dando luogo a fenomeni poco o per nulla presenti nel macro.
Ad esempio, quando il raggio del tagliente dell’utensile ha dimensioni comparabili con quelle dello spessore di truciolo da asportare, l’angolo di spoglia diventa negativo; ciò fa sì che il truciolo subisca una forte compressione e non più di taglio che comporta un innalzamento dell’energia specifica di lavorazione ed è causa del fenomeno del tagliente di riporto stabile e aderente all’utensile. Inoltre, vengono generate delle vibrazioni che unitamente al ritorno elastico del materiale sul fianco dell’utensile portano a una scarsa finitura superficiale e rapida usura dell’utensile.
Un altro effetto da tenere in considerazione è l’effetto del minimo spessore di truciolo che si verifica quando lo spessore del materiale asportato è minore di quello minimo teorico, comportando il cosiddetto profilo a “dente di sega”: il pezzo in lavorazione viene solamente ricalcato e/o deformato elasticamente, facendo sì che rimanga sulle superficie un sovrametallo indesiderato che viene poi lavorato dal tagliente successivo. Questo fenomeno, unitamente alla bassa rigidità dei microutensili utilizzati, produce quindi un taglio intermittente: la fresa si inflette nel verso opposto rispetto a quello della velocità di avanzamento fino a quando lo spessore del sovrametallo non raggiunge quello minimo.
A causa di quanto detto è importante specificare che non tutti i materiali sono quindi adatti per essere lavorati in ordini microscopico, infatti, caratteristiche quali durezza superficiale e conducibilità termica influiscono sulla capacità di lavorare il materiale. Ad esempio, materiali fragili e con bassa resilienza, come le ceramiche, sono soggetti a rotture e cricche durante il processo di lavorazione; d’altro canto, materiali molto plastici, tendono a deformarsi e a produrre finiture superficiali non di qualità.
Un altro esempio può essere fatto prendendo in considerazione materiali che hanno elevate conducibilità termica, che quindi hanno la capacità di raggiungere temperature estremamente elevate quando vengono lavorati, causando un aumento significativo della velocità di usura dell’utensile e qualità superficiale scadente. Pertanto, quando si sceglie un materiale per le microlavorazioni, è importante considerare le proprietà dello stesso in relazione alla tipologia di lavorazione e al risultato che si vuole ottenere.
Il microlaser e le lavorazioni a ultrasuoni
Oltre i processi “tradizionali” di microfresatura, microforatura e microtornitura, per asportare il truciolo da alcuni materiali particolari, con le caratteristiche evidenziate sopra, sono necessari dei processi particolari.
Il processo di microlavorazione a ultrasuoni è uno di questi: utilizzando vibrazioni ad alta frequenza (nel campo degli ultrasuoni ovvero oltre i 20.000 Hz) riesce a rimuovere materiale, con altissima precisione. La tecnica coinvolge l’utilizzo di un materiale estremamente duro (come il diamante) che riveste la punta dell’utensile in metallo. Questa punta è unita a un trasduttore, responsabile della generazione delle vibrazioni che vengono modulate dalla struttura geometrica dell’utensile definita corno, che è fatto da un materiale piezoelettrico (come il PZT) che consente la trasformazione da energia elettrica a meccanica, cambiando di forma quando è esposto a un campo elettrico.
Quindi, da una sorgente elettrica ad alta frequenza si genera una differenza di potenziale alternata che viene applicata al trasduttore: cambiando di forma a frequenze elevate, si generano quindi le vibrazioni che consentono alla punta dell’utensile di entrare in contatto con il pezzo da lavorare e rimuovere materiale attraverso un processo sia meccanico sia di cavitazione. È importante notare che le particelle abrasive sulla punta dell’utensile vengono costantemente rifornite grazie a una soluzione che viene iniettata costantemente sull’interfaccia utensile/workpiece.
Il vantaggio di questa tecnologia è la capacità di poter esser utilizzata su una vasta gamma di materiali, in particolare quelli fragili come le ceramiche, il vetro e certi tipi di materiali compositi oltre che su quei materiali sensibili alle alte temperature grazie alla caratteristica di generare poco calore nel processo. La precisione e la qualità dei pezzi finiti è tale da non dover utilizzare successivamente ulteriori processi per la finitura superficiale.
Per micro-laser si intende una particolare tipologia di laser in grado di concentrare il fascio di energia in un piccolo raggio nella scala dei micron. Questa tipologia di laser è molto utilizzata per una vasta gamma di applicazioni, dal manufacturing fino a procedure di tipologia medica. Questa particolare lavorazione consente, oltre a una precisione di taglio eccellente, anche di ottenere minimi danni sul pezzo finito e di poter operare su una vasta gamma di materiali: da quelli biologici ai polimeri. Rispetto alla microfresatura ha però degli svantaggi:
- Non raggiunge la precisione di quest’ultima, rendendo necessario talvolta un’ulteriore lavorazione di rifinitura superficiale;
- Il processo diventa lento per alti volumi di materiale da asportare.
La tipologia di laser più utilizzata per le microlavorazioni è quella ai femtosecondi ovvero laser che generano impulsi di durata brevissima (nell’ordine dei 10-15 secondi) per evitare il surriscaldamento del materiale che causa deformazioni e imperfezioni. È inoltre adatto per quei materiali, come i tessuti biologici, sensibili alle radiazioni elettromagnetiche. Si tratta di una tecnologia molto costosa e avanzata rispetto alle sorgenti laser “tradizionali”: infatti il fascio è generato da una sorgente che utilizza un cristallo o un materiale non lineare (cioè materiali in cui l’interazione tra polarizzazione e campo elettrico non è lineare). La sorgente emette un fascio a lunghezza d’onda ben definita grazie all’interazione tra luce e materiale e un sistema ottico che permette di “filtrare” e concentrare la luce. Spesso sono associati a sistemi di controllo ed elaborazione dei dati per la regolazione sia della potenza sia della durata. La durata molto breve degli impulsi è necessaria per eccitare solamente gli elettroni sulla superficie del materiale, che vengono qui “strappati” dai lori atomi: questo fa sì che gli atomi ionizzati creino delle interazioni Coulombiane (cioè di tipo elettrico) che causano l’asportazione di materiale.
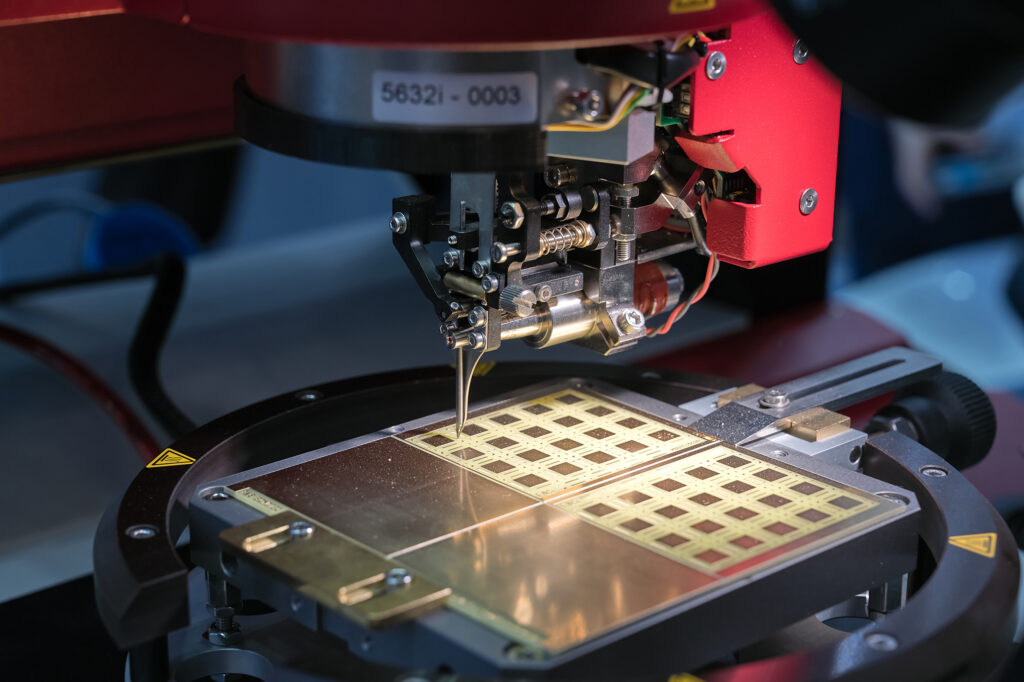
Aspettative e sviluppi futuri
Il mondo accademico e delle ricerca, spinto da esigenze industriali sempre più personalizzate, è impegnato nello sviluppo e nel miglioramento delle tecnologie in questo campo, consentendo al contempo la realizzazione di geometrie e finiture superficiali sempre migliori. Gli obiettivi posti sono:
- un miglioramento sulla precisione e il controllo, in particolare per quanto riguarda i laser;
- lo sviluppo di nuovi materiali avanzati attraverso le microlavorazioni;
- la definizione di nuove tecniche in grado di innovare e ampliare le possibilità di lavorare determinati materiali.
In particolare, il focus si sta concentrando sul campo elettronico per migliorare e implementare le tecnologie esistenti con metodi capaci di produrre circuiti integrati e dispositivi elettronici che richiedono una sempre più elevate precisione di produzione. Ultimo, ma non per importanza, il mondo medico richiede strumentazioni di precisione che richiedono l’utilizzo della massima precisione e finitura.