In questo studio, per stimare l’insorgere di bave durante il taglio, è stato scelto di sfruttare le reti neurali artificiali (“ANN”). Questa soluzione permette di creare un modello utilizzando “neuroni” artificiali collegati tra di loro. Essi sono in grado di apprendere, se opportunamente addestrati, a svolgere un compito.
Per il settore manifatturiero la qualità è un tema sempre più centrale. Negli ultimi decenni le richieste dei clienti sono sempre più esigenti, occorre quindi essere in grado di produrre componenti conformi agli ultimi standard qualitativi. Inoltre, è necessario assicurare un’elevata ripetibilità dei componenti prodotti, assicurando caratteristiche stabili indipendentemente dal lotto di produzione.
Non meno importante, per il moderno contesto produttivo, è la rapidità. Il tempo è denaro, occorre quindi ridurre il più possibile i tempi produttivi, pur assicurando le caratteristiche richieste. Questo binomio dato da tempi e qualità costringe tutti i produttori a trovare il giusto compromesso in grado di soddisfare le diverse esigenze.
Sia i produttori di macchinari che il mondo della ricerca, ben consci di queste esigenze, sono al lavoro per offrire soluzioni industriali sempre migliori grazie alla crescente integrazione tra fisico e digitale.
Il taglio laser
La tecnologia laser è ormai dominante per quanto riguarda il taglio di lamiere o tubi sottili. Questo perché vengono offerte, rispetto alle tecnologie alternative, un’ottima flessibilità e una buona produttività. La modalità di taglio laser più utilizzata negli ultimi anni è quella di fusione utilizzando l’azoto come gas di processo. Il motivo di questa diffusione è dovuto principalmente alla disponibilità di laser con potenze superiori.
Su sistemi di questo tipo è centrale la produttività, risulta quindi fondamentale riuscire ad ottimizzarla per riuscire ad ottenere macchinari sempre più competitivi. Ottimizzare la produttività significa trovare il giusto compromesso tra velocità produttiva e qualità di prodotto. Per determinare la qualità nel taglio laser vengono considerate diverse quantità come, ad esempio, la bava, l’eccessiva rugosità superficiale o la presenza di bruciature sugli angoli.
L’idea dei ricercatori del Politecnico di Milano è quella di riuscire a regolare, in tempo reale, la velocità di taglio per limitare la formazione di bave. Questa soluzione risulta particolarmente innovativa poiché i processi attuali, non in grado di valutare in tempo reale i difetti, sono tarati per lavorare a velocità inferiori rispetto all’ottimale.
Questo per limitare l’insorgenza di difetti ed assicurare un’elevata qualità. Tuttavia, lavorando a velocità ridotte si limita anche la produttività del macchinario, impiegando più tempo rispetto al necessario.
Stima delle bave
Per poter creare un prototipo di macchinario in grado di regolare in tempo reale la velocità del laser è stato utilizzato un macchinario di taglio industriale. Si tratta di sistema per taglio laser a fibra con una potenza massima di 6kW. La testa di taglio standard è stata modificata per permettere il monitoraggio dell’insorgenza del difetto di bava (Figura 1).
Il monitoraggio avviene tramite una camera CMOS coassiale ad alta velocità. Le immagini registrate dalla camera (mostrate in Figura 2a) sono state processate per estrarre parametri geometrici utilizzati poi in seguito per stimare l’insorgere di bave. Dalle immagini di monitoraggio sono state estratte la posizione e le dimensioni di larghezza e lunghezza della zona irradiata dal laser (chiamata anche “blob”). Per avere un riscontro reale sul componente tagliato sono anche state effettuate misure al microscopio in modo da definire dove fossero presenti bave sui provini fisici.
Queste misure sono infatti un fondamentale riscontro con la realtà per creare un algoritmo in grado di stimare in tempo reale la presenza di bave. Il riscontro sul fisico permette infatti di addestrare il modello e validarlo per questo scopo.
Rete neurale
In questo studio, per stimare l’insorgere di bave durante il taglio, è stato scelto di sfruttare le reti neurali artificiali (abbreviate come “ANN”). Questa soluzione permette di creare un modello utilizzando “neuroni” artificiali collegati tra di loro.
Essi sono in grado di apprendere, se opportunamente addestrati, a compiere un compito. Nel caso dello studio è stata strutturata una semplice rete neurale che, partendo dai parametri estratti dalle immagini derivanti dalla camera di monitoraggio, è in grado di stimare la presenza di bava sul componente. Il modello è stato addestrato ad eseguire questo compito confrontando i dati di monitoraggio con le misure effettuate sui corrispondenti componenti fisici.
Questa soluzione si dimostra particolarmente rapida data la sua semplice struttura e permette di ottenere interessanti prestazioni. Dal confronto (Figura 3) si può notare uno scarto limitato tra la stima e la misura reale della bava durante il processo di taglio di una lamiera spessa 5 mm di acciaio inossidabile X5CrNi18-10.
Adattamento in tempo reale
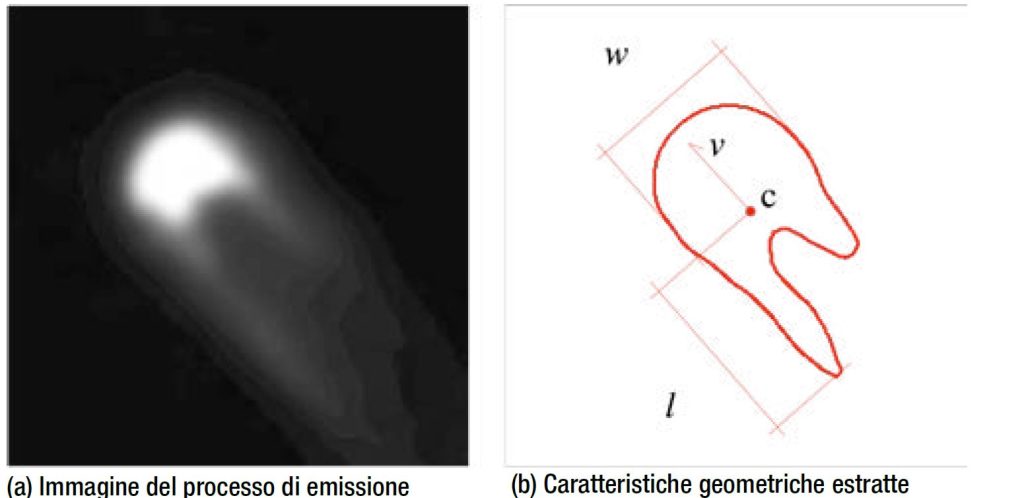
Dopo essere riusciti a monitorare in tempo reale l’insorgenza di difetti di bava nel processo di taglio i ricercatori italiani hanno compiuto un ulteriore passo in avanti. L’obiettivo è infatti quello di creare un processo ad anello chiuso, in grado di regolare la velocità di taglio secondo la stima di presenza di bava. Questo controllo risulta particolarmente interessante perché permette di massimizzare la velocità e quindi la produttività del processo garantendo un adeguato livello qualitativo.
Un controllo proporzionale è stato definito per permettere di adattare la velocità alla stima di bava ottenuta dal sistema di monitoraggio. Il sistema ad anello chiuso (mostrato in Figura 4), dopo un transitorio iniziale, è in grado di regolare la velocità di taglio per ottenere la qualità desiderata sul componente finale. Interessante il fatto che sia possibile definire un target qualitativo (in questo caso un livello di bava) che il sistema cerca di ottenere.
In questo modo, definendo la qualità richiesta per la lavorazione, il sistema agisce in autonomia per regolare la velocità massima tale da assicurare quella caratteristica. La soluzione risulta essere particolarmente interessante dal punto di vista industriale poiché permette di ottimizzare la produttività del sistema (massima velocità) per ottenere un componente della qualità richiesta.
In un contesto in rapida evoluzione e sempre più difficile è fondamentale riuscire a rispondere alle richieste dei clienti in tempi rapidi e in modo efficiente. Ogni aumento di produttività, anche piccolo, permette di risparmiare risorse e quindi di aumentare la competitività sul mercato.
Il tradizionale processo di taglio laser, senza adattamenti o retroazioni, limita inevitabilmente la produttività per garantire ripetibilità e una qualità adeguata. Inoltre possono presentarsi differenze, anche significative, tra la fase di ottimizzazione e la reale pratica quotidiana.
Ad esempio, è possibile avere un invecchiamento delle componenti ottiche sul macchinario o differenze legate al materiale da processare. In questi casi un processo autoadattante ad anello chiuso permette di ottenere notevoli vantaggi. Adeguando autonomamente la velocità di taglio per ottenere la qualità desiderata si è in grado di garantire una elevata ripetibilità indipendentemente dall’invecchiamento del macchinario o da variate condizioni operative.
La soluzione proposta dai ricercatori del Politecnico presenta chiari ed immediati vantaggi anche per il mondo industriale. La digitalizzazione dei macchinari produttivi permette infatti di portare concreti benefici per gli operatori del settore manifatturiero.
Fonte: Pacher, M., Strada, S., Tanelli, M., Previtali, B., & Savaresi, S. M. (2021). Real-time velocity regulation for productivity optimization in laser cutting. IFAC-PapersOnLine, 54(1), 1230–1235. https://doi.org/10.1016/j.ifacol.2021.08.146