Fra i metodi di ripristino e riparazione di componenti metallici, il processo additivo denominato “laser direct metal deposition” (LDMD) sta riscontrando un discreto successo
La vita utile dei singoli componenti di un sistema meccanico influisce significativamente sull’affidabilità e la durata del sistema stesso. Nel caso delle trasmissioni, molti di questi componenti sono soggetti a condizioni operative critiche come, ad esempio, le ruote dentate, frequentemente esposte a carichi elevati, variazioni di temperatura e usura.
Condizioni di lavoro particolarmente ostili, o in certi casi estreme, possono danneggiare prematuramente un componente originando fenomeni di degrado di varia natura. Nel caso di componenti metallici ad alte prestazioni la situazione viene complicata dal fatto che sono utilizzati materiali speciali alto-resistenziali, come leghe di titanio o nichel, i quali richiedono processi produttivi complessi e onerosi. In questi casi, la rottura di un componente e la sua completa sostituzione ha impatti negativi rilevanti anche sui costi. Per questi motivi, la riparazione e la ripresa in servizio del componente, quando possibile, è particolarmente interessante e spesso anche economicamente vantaggiosa. Oltre al risparmio, la riparazione di componenti danneggiati può produrre altri benefici, come un prolungamento rilevante della loro vita utile, maggiore sostenibilità e riduzione dei tempi associati al fermo impianto.
Fra i metodi di ripristino e riparazione di componenti metallici, ci concentriamo in questo articolo sul processo additivo denominato “laser direct metal deposition” (LDMD), che sta riscontrando un discreto successo. Questo processo utilizza un ridotto riscaldamento termico che contiene al minimo la distorsione del componente da riparare, caratteristica molto vantaggiosa per elementi snelli, sottili e strutturalmente delicati. Inoltre, con la LDMD si possono ottenere riparazioni a densità molto elevata con ottima resistenza. Il processo utilizza un laser concentrato ad elevata energia per creare un piccolo volume di fusione sulla zona danneggiata. Nel frattempo, polveri metalliche vergini vengono introdotte nella pozza di fusione, partecipando alla successiva solidificazione. Il materiale di base del componente viene quindi fuso insieme alla polvere di apporto, fornendo un eccellente adesione fra le superfici.
La corretta definizione del percorso del laser è essenziale per la riparazione del componente danneggiato, poiché consente di replicare la precisa geometria da riprodurre sulla regione danneggiata. In alcuni casi, sono stati documentati processi LDMD per la riparazione dei componenti utilizzando un percorso utensile controllato manualmente. Sebbene, da un lato, i processi LDMD si sposino bene con diversi materiali per la rigenerazione dei volumi mancanti, come ad esempio il Ti6Al4V e l’acciaio inossidabile, dall’altro, la definizione manuale del percorso utensile risulta praticabile solo nel caso in cui i componenti da riparare siano semplici e presentino geometrie regolari, poiché solo in tali casi i volumi di riparazione risultano facilmente prevedibili. In realtà, nella pratica il volume di riparazione è spesso complesso e la definizione manuale del percorso utensile richiederebbe un notevole dispendio di tempo. A questo si aggiunge la soggettività dell’operatore nella ricostruzione del danno basata sulla propria esperienza, che non garantisce elevata ripetibilità nell’intervento. Visto che queste problematiche potrebbero ridurre l’affidabilità della riparazione, si ricorre spesso ad una strategia di ricostruzione automatizzata, la quale fornisce un intervento più rapido e prevedibile. Per la riparazione di componenti dalle geometrie complesse, come nel caso di fratture nei denti di ruote dentate, occorrono, algoritmi avanzati di rilevamento e ricostruzione automatizzata dei danni mediante un numero elevato di punti di scansione.
Riparazione di ruote dentate mediante LDMD: lo stato dell’arte
Il metodo più comune per trattare componenti danneggiati è quello di rimuovere l’area danneggiata, insieme ad una porzione aggiuntiva di materiale integro, e successivamente ripristinarla depositando il nuovo materiale. Negli ultimi decenni sono state rese disponibili diverse tecniche di deposizione. Importante è scegliere quella che più si avvicina allo scopo specifico della riparazione. Tradizionalmente, la riparazione di ruote dentate veniva eseguita mediante processi di saldatura per fusione, come la saldatura ad arco o al plasma. Tuttavia, con tali procedure si è visto, in generale, che l’abbondante apporto di calore comportava fragilità nei denti delle ruote dentate ed un indebolimento del materiale circostante. Con l’avvento delle tecniche additive, in particolare del processo LDMD, sono emerse nuove possibilità.
Grazie all’uso di bracci guidati e alla produzione computerizzata, il processo, e in particolare l’apporto di calore, è altamente controllabile. Come noto, la storia termica gioca un ruolo dominante nella qualità delle strutture additive. Nei metodi convenzionali, come la saldatura, l’eccesso di calore è spesso accompagnato da effetti dannosi (indebolimento del substrato, sollecitazioni termiche estreme nel materiale depositato, etc.). Con il processo LDMD, la ridotta esposizione al calore e la profondità del laser garantiscono una distorsione termica minima nel materiale circostante. Inoltre, è possibile creare un legame metallurgico qualitativamente superiore tra il substrato e lo strato aggiunto grazie ad una diluizione controllabile e tipicamente ridotta. Una diluizione ridotta può essere un vantaggio nei casi in cui sono richieste transizioni nette nelle proprietà del materiale o quando la miscelazione del materiale del substrato è nociva per il materiale depositato. Un altro grande vantaggio della LDMD è la riduzione della porosità grazie ad un ambiente controllato. Le prestazioni complessive delle deposizioni sono eccellenti e l’incollaggio è solitamente più resistente. Tutte le proprietà tipiche del processo LDMD si traducono in microstrutture più omogenee.
Il progresso tecnologico sta oggi favorendo l’impiego della tecnologia LDMD per la riparazione di componenti. Attualmente sono disponibili numerose tecniche convalidate e sono in corso ulteriori ricerche per la realizzazione di strutture 3D. Materiali classificati funzionalmente possono risultare ottimali in determinate circostanze, come ad esempio il nucleo duttile combinato con la superficie esterna dura e resistente all’usura di un dente di una ruota dentata. È stato dimostrato che tali strutture possono essere create anche in caso di processi produttivi complessi. Un altro vantaggio è poi l’aumento dell’efficienza: determinare la geometria di un vecchio componente richiede molto tempo e talvolta i disegni non sono disponibili. Combinando sensori e tecnologie ICT, i ricercatori sono oggi in grado di applicare il reverse engineering per il ripristino di parti usurate o danneggiate, con una radicale riduzione dei tempi e risultati più accurati. In sintesi, si può affermare che, grazie all’estrema flessibilità del processo LDMD, non è una questione di “se” ma di “come” lo si può utilizzare per riparare una ruota dentata danneggiata.
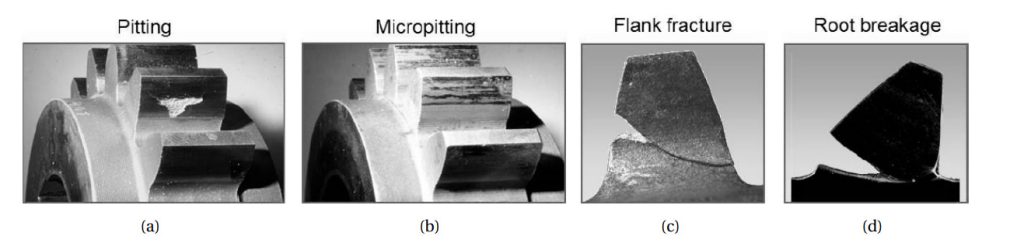
Caratteristiche delle ruote rilevanti per la loro riparazione
Il design delle ruote dentate: geometrie e materiali
Come noto, a seconda dell’applicazione prevista, sono disponibili molte varianti di ruote dentate. Le principali specifiche per la progettazione di questi componenti per uso industriale sono la coppia trasmessa, la geometria e la massa, la resistenza al carico dinamico e la durata. Sono anche numerose le tipologie di materiali impiegati; ad esempio, i polimeri e le leghe non ferrose sono utilizzate per applicazioni di bassa potenza, mentre leghe in acciaio sono la soluzione migliore laddove è richiesta una potenza elevata. La selezione del materiale dipende quindi sia da specifiche generali di progettazione, ma anche da fattori tecnologici di processo come (lavorabilità, temprabilità, etc.) e da caratteristiche prestazionali. Fra queste ultime in particolare sono importanti le seguenti:
- Resistenza alla flessione del dente: capacità di resistere ai carichi locali di ingranamento agenti sul singolo dente prima della deformazione plastica.
- Resistenza agli urti: proprietà correlata alla tenacità del materiale, con la quale esso consente di assorbire elevati picchi di carico senza generazione di danneggiamenti locali (cricche) e riduzione della vita utile.
- Resistenza alla fatica del dente: capacità di resistere ai carichi ciclici di ingranamento senza innescare deterioramento irreversibile del materiale, specie alla radice del dente.
- Resistenza all’usura: capacità di ridurre gli effetti di alterazioni superficiali legate alle forze di contatto. Spesso legata alla efficienza della lubrificazione, questa caratteristica consente di contenere micro-danneggiamenti superficiali e sub-superficiali legati al distacco di piccole parti dal fianco del dente (ad esempio il fenomeno del pitting).
La maggior parte delle ruote dentate industriali di medie e grandi dimensioni sono realizzate con acciai basso legati. Oltre al carbonio, l’acciaio basso legato contiene tipicamente particelle di cromo, nichel e/o molibdeno, che contribuiscono a migliorarne le prestazioni. Il nichel, ad esempio, aumenta la resistenza alla trazione, la temprabilità, la resistenza alla fatica e abbassa le temperature critiche per il trattamento termico, ciò significa che è possibile applicare temperature e velocità di raffreddamento inferiori in tale fase. Il cromo indurisce il materiale, migliorando la temprabilità e la resistenza all’usura. Il molibdeno, in combinazione con il cromo, contribuisce non solo alla temprabilità, ma aumenta anche la tenacità del materiale. È possibile produrre diverse composizioni di acciaio. La scelta finale, tuttavia, dipende soprattutto dalla loro disponibilità. Attualmente, gli acciai per ruote dentate più utilizzati sono il 20MnCr5 e il 18CrNiMo7-6.
L’influenza del processo di produzione sulla riparazione di una ruota dentata
Per determinare la tecnica ottimale di riparazione di una ruota dentata al fine di ripristinare le condizioni di origine, è fondamentale comprendere a fondo il processo di produzione della ruota stessa. La produzione di ruote dentate può avvenire attraverso una grande varietà di processi, talvolta anche assai complessi, a seconda dei requisiti e delle applicazioni previste.
Un generale un processo di produzione di ruote dentate include:
- Realizzazione del cilindro di base.
- Generazione dei denti tramite sagomatura, brocciatura o fresatura.
- Affinamento dei denti: finitura dei denti mediante operazioni come di rettifica, lappatura, etc.
- Trattamento termico. Per migliorare le proprietà del materiale costitutivo della ruota dentata si eseguono diversi trattamenti termici. L’obiettivo principale è aumentare la resistenza all’usura e la durata a fatica. Al contempo, il processo garantisce che il nucleo del materiale mantenga la sua duttilità e tenacità iniziale, poiché il trattamento termico agisce solo sullo strato esterno della ruota dentata.
- Finitura finale per eliminare imprecisioni del passo o del profilo. In tal modo usura, rumore e altri inconvenienti sono minimizzati o eliminati.
Fenomeni di danneggiamento e prevenzione dei guasti nelle ruote dentate
In condizioni operative estreme, sia la macrostruttura che la microstruttura del materiale di una ruota dentata sono fortemente influenzate, con conseguente aumento del rischio di malfunzionamenti. Guasti alle ruote dentate sono spesso correlati ad errori o cambiamenti nelle condizioni di lavoro, come disallineamento o violenti impatti. I danni più frequenti si hanno solitamente in corrispondenza dei denti e, a seconda delle circostanze possono essere di vario tipo (figura 1).
L’usura superficiale o micro-pitting (figure 1a e 1b) si verifica a causa di un piccolo scorrimento dei denti in corrispondenza di piccole aree. Sebbene l’usura superficiale sia inevitabile, è necessario ridurla sempre al minimo, mediante, ad esempio un corretto allineamento e lubrificazione.
Altra tipologia di danno è il pitting, causato da microfratture in superficie o al di sotto di essa. Più difficile da notare e più pericoloso dell’usura abrasiva, nelle fasi iniziali, il pitting può essere riparato o confinato, ma se trascurato sviluppa macro-fessurazioni sino alla frattura del fianco (figura 1c).
Ultimo fenomeno di danneggiamento raffigurato è legato alla fatica del materiale alla radice. Numerosi cicli di carico indeboliscono il materiale, dando origine a microfratture. Spesso, un violento impatto, come un arresto improvviso, può causare la propagazione di queste cricche attraverso l’intera radice, provocando la frattura del dente di una ruota dentata (figura 1d).
Il processo LDMD
La produzione additiva sta attualmente rivoluzionando l’industria manifatturiera. In particolare, il processo LDMD (laser direct metal deposition) è una delle tecniche più recenti ed oltre ad essere applicabile ai processi di produzione di componenti, si sta dimostrando molto promettente anche per quanto concerne la riparazione di parti danneggiate e usurate.
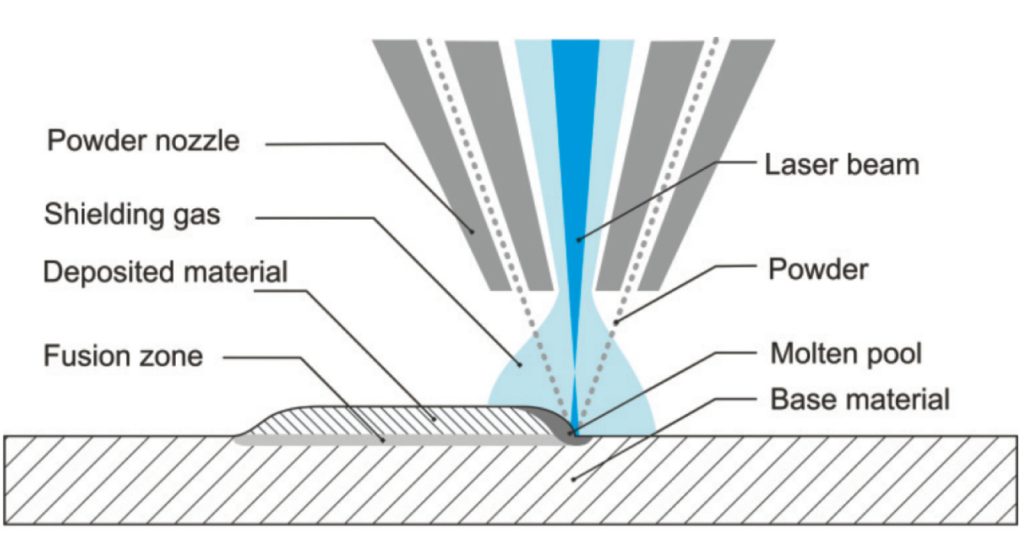
Grazie all’apporto termico relativamente ridotto e alla deposizione uniforme di materiale, risulta preferibile ai metodi di riparazione convenzionali, portando a una nuova era in cui anche le parti a fine vita possono essere riciclate.
Il processo LDMD ha inizio con l’applicazione di un raggio laser su di un pezzo o di un substrato. L’accumulo di calore locale produce la fusione del materiale, creando una pozza di fusione. Attraverso un ugello coassiale e l’impiego di un gas inerte per evitarne l’ossidazione, la polvere viene introdotta nel metallo fuso. Contemporaneamente, la testa del laser si muove lungo la superficie del pezzo in lavorazione. Una sintesi del processo LDMD è mostrata in figura 2.
Il laser segue un percorso predeterminato e uno strato di materiale viene depositato sul pezzo in lavorazione. La ripetizione sequenziale di tale processo consente di ottenere una struttura tridimensionale multistrato. Dopo un breve periodo di raffreddamento, il pezzo viene quindi rimosso dalla macchina per essere ispezionato alla ricerca di eventuali cricche e visionato per rilevarne le tolleranze. Successivamente, viene lavorato secondo le dimensioni desiderate.
La sfida principale nel processo LDMD è di creare una traccia o uno strato con proprietà uniformi in tutto il materiale depositato. Le proprietà della deposizione sono determinate da una grande quantità di parametri e impostazioni della macchina, che devono essere opportunamente regolati per ottenere risultati ottimali. Tra i principali parametri del processo LDMD ci sono la velocità di deposizione, la velocità di scansione e la potenza del laser. La figura 3 mostra la sezione di una traccia depositata su un substrato. Occorre tenere presente che, quando si utilizzano materiali differenti, la miscelazione del materiale di deposito con il substrato può alterare le proprietà della struttura depositata. Tuttavia, si presume che questo effetto sia trascurabile per le deposizioni con più di tre strati.
A determinare le prestazioni meccaniche del materiale depositato concorrono anche poi anche altre proprietà come la densità, la porosità, la microstruttura e il legame metallurgico. Molti studi, a seguito di differenze nell’hardware e di configurazione, come ugelli e sistemi ottici, hanno mostrato risultati diversi per i set di parametri ottimali, pertanto, non è ancora disponibile un setup LDMD condiviso, ma esistono varie configurazioni, con elementi comuni distinguibili, a seconda dei diversi scopi della macchina.
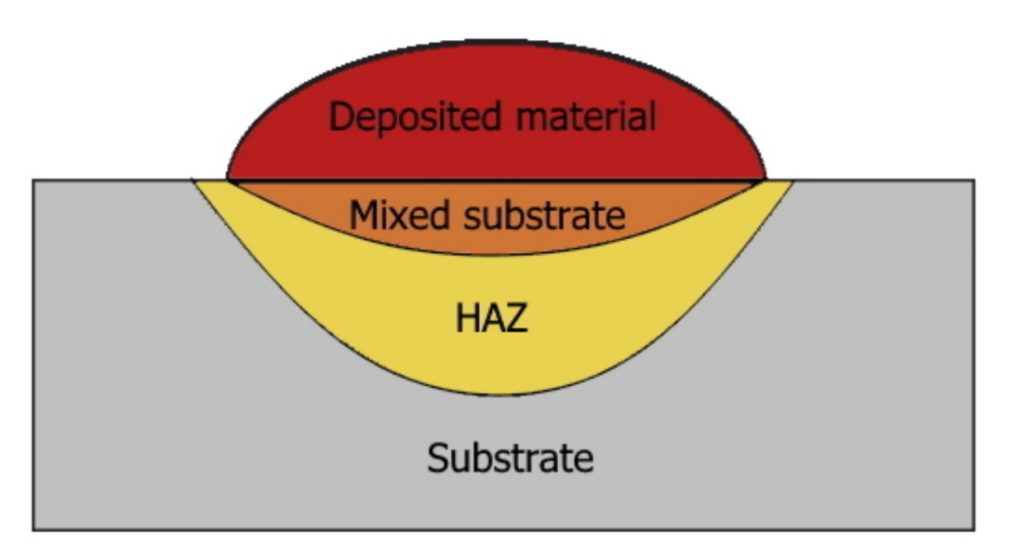
Analisi dei danti dopo la riparazione
In generale, è fondamentale comprendere il comportamento meccanico di un componente quando viene riparato. Anche nel caso delle ruote dentate, per assicurarsi che un dente riparato sia in grado di resistere in condizioni operative specifiche, è quindi necessaria una sua analisi approfondita. Durante l’intero ciclo di vita di una ruota dentata, i denti sono soggetti a diversi tipi di carico, che introducono sollecitazioni in diverse zone. Carichi ciclici comportano, come abbiamo già visto in precedenza, diversi tipi di fenomeni di danneggiamento. Le forze di contatto sono costituite sia da forze di rotolamento che da minime forze di scorrimento, mentre la radice del dente subisce sollecitazioni di trazione e compressione. In base alle diverse sollecitazioni durante un ciclo di carico, il dente può essere approssimativamente suddiviso in quattro aree di interesse (fianco, nucleo, radice e interfaccia – figura 4), che incidono sulle prestazioni della ruota dentata. Le proprietà di tali aree critiche sono estremamente diverse. Idealmente, le caratteristiche del processo LDMD dovrebbero rispondere ai requisiti di ciascuna regione senza influenzare le altre.
Il fianco del dente è lo strato esterno, tipicamente cementato, e quindi più duro, tra i 50 e i 60 HRC, rispetto all’anima. La maggiore durezza rende i fianchi del dente più resistenti all’usura e alle forze di contatto hertziane. Alcuni studi dimostrano poi una maggiore resistenza all’usura con l’aggiunta di uno strato contenente carburi di tungsteno e superleghe di nichel. Altre prove si mostrano promettenti per quanto riguarda la riparazione dei fianchi delle ruote dentate. Fianchi usurati e poi sostituiti hanno superato con successo le prove di durezza. La sfida principale nella creazione di un fianco del dente resistente all’usura è la creazione di un deposito privo di cricche con durezza sufficiente.
Il nucleo del dente è la parte centrale, la quale ha la funzione di fornire resistenza strutturale rispetto alle forze che agiscono sul dente stesso per la trasmissione della coppia. In genere, il nucleo presenta valori di durezza compresi tra 30 e 40 HRC. La propagazione delle cricche è contrastata dalla sua duttilità. Considerando gli acciai, la flessibilità di un dente è scarsamente influenzata dalla scelta del materiale. Inoltre, l’anima deve essere priva di porosità e cricche. Qualsiasi deviazione nel nucleo può contribuire all’innesco di cricche e a cedimento prematuro.
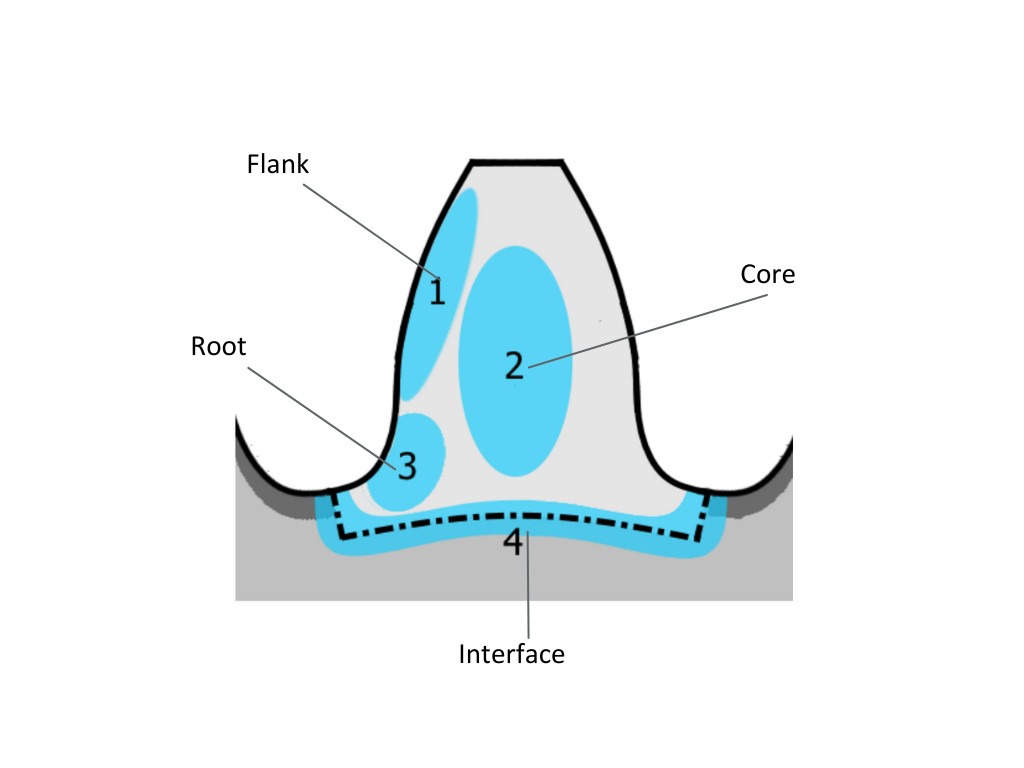
Tra tutte le aree del dente, quella che subisce le maggiori sollecitazioni è la radice, a causa della flessione a cui è sottoposto il dente stesso. Questa causa, alla radice, tensioni di compressione da un lato e di trazione dall’altro (classico andamento “a farfalla”). La rottura del dente in applicazioni industriali ha spesso origine in prossimità della radice, con la formazione di piccole cricche. L’innesco di tali cricche può avvenire in seguito ad un impatto, legato ad esempio a un arresto brusco del sistema o a causa della fragilità dello strato esterno della ruota dentata. Le cricche si sviluppano rapidamente e si propagano verso l’interno del dente, portando a cedimento. Tale fenomeno può essere contrastato scegliendo un materiale resistente in grado di ridurre la formazione e la propagazione delle cricche.
Una ulteriore modalità di guasto è la fatica, che si verifica nel momento in cui la radice è sottoposta a un carico ciclico. L’origine del fenomeno è spesso imputata a una progettazione errata o a un sovraccarico persistente. Concentrazioni di tensioni cicliche in corrispondenza della radice danno inizio a cricche, che finiscono per provocare la rottura della radice del dente. I valori tipici per i limiti di resistenza del materiale della radice sono compresi tra 700 e 1000 MPa. Il processo LDMD offre la possibilità di selezionare un materiale che migliori le prestazioni complessive della radice.
In figura 5 si mostra la distribuzione tipica della tensione equivalente di Von Mises all’interno di un dente prodotta da una forza normale che agisce sul punto più esterno dell’area di contatto (detto HPSTC, Highest Point of Single Tooth Contact). Le sollecitazioni più elevate si verificano in corrispondenza del punto di contatto e della radice del dente.
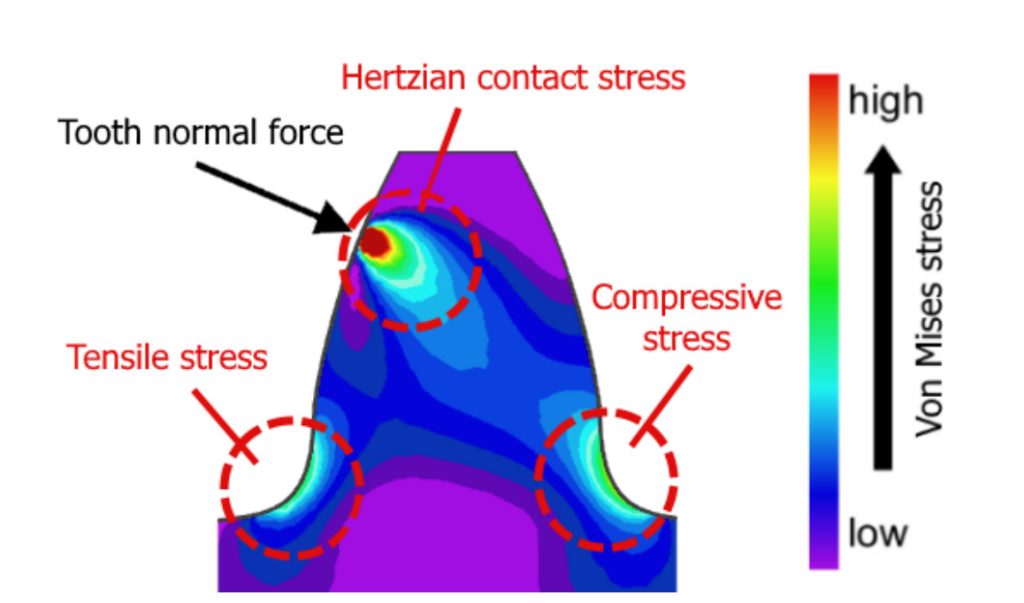
A livello di interfaccia, l’adeguata adesione tra il nuovo materiale quello pre-esistente è essenziale. Le maggiori criticità della riparazione si verificano nelle aree in cui il nuovo materiale viene depositato su regioni sottoposte a indurimento. Qui infatti la presenza di carbonio rende la zona di fusione suscettibile alla formazione di fasi intermetalliche altamente fragili. Queste fasi possono influire negativamente sulle prestazioni successive del dente, per il rischio di formazione di cricche. È particolarmente importante evitare spigoli vivi e porosità interne per massimizzare le prestazioni del materiale additivo.
È bene specificare che, a sua volta, il processo LDMD introduce nuove modalità di potenziale cedimento nelle aree riparate del dente. Un riepilogo è mostrato nella tabella 1.
Posizione | Causa | Effetto |
Fianco del dente | Bassa durezza Ridotta profondità Bonding insufficiente | Attrito abrasivo Pitting Distacco del fianco |
Nucleo | PorositàBasso modulo di YoungBassa tenacità | Innesco di criccheBassa rigidezza Propagazione di cricche |
Radice | Bassa resistenzaFaticaBassa resistenza a impatto | Cedimento prematuro Innesco di cricche |
Interfaccia | Fasi intermetalliche Bonding insufficiente | Innesco di criccheDistacco del dente |
Algoritmi avanzati per la ricostruzione di un danno al dente
Di seguito viene descritto un esempio di algoritmo per il rilevamento automatico e la ricostruzione automatizzata della geometria danneggiata di un dente.
In prima battuta, la geometria della ruota dentata danneggiata viene rilevata e confrontata con il modello nominale. Quindi il modello danneggiato viene allineato al modello nominale e, successivamente, entrambi i modelli vengono suddivisi in strati ed è estratto il volume di riparazione.
Sulla base del modello 3D ricostruito, è sviluppata una strategia di elaborazione per eseguire una deposizione di precisione sulla zona riparata e ripristinare la geometria della ruota dentata. Questo metodo consente una riparazione rapida e automatizzata anche in caso di geometrie complesse. Successivamente, le particelle di polvere metallica vengono depositate sulla regione danneggiata, precedentemente pulita, utilizzando il processo additivo LDMD.
L’elevata coincidenza dei punti di scansione tra il modello riparato e quello nominale conferma l’efficienza di un algoritmo. Esso è infatti in grado di garantire una ricostruzione coerente e ripetibile di danni complessi, riducendo drasticamente il rischio di guasti durante il servizio. In termini di tempo, tale strategia consente un significativo risparmio rispetto ai metodi convenzionali.
Per valutare la qualità del componente riparato sono state poi effettuate analisi della microstruttura e della durezza. Le micrografie sono state eseguite su tre diverse sezioni trasversali dei campioni riparati e hanno evidenziato una buona adesione senza difetti all’interfaccia, come delaminazione, pori o cricche. La misurazione della durezza è stata eseguita sulla sezione trasversale del campione riparato.
Infine, è stato sviluppato un modello 3D a elementi finiti basato sull’analisi termomeccanica per simulare e prevedere con precisione la deformazione e il comportamento delle sollecitazioni del processo di riparazione. È stato osservato che le tensioni residue sono maggiori lungo la direzione di scansione rispetto a quella perpendicolare. Le tensioni medie equivalenti mostrano valori inferiori alla tensione di snervamento. Il modello termomeccanico FEA (finite element analysis) ha ulteriormente convalidato l’algoritmo di riparazione. Lo scopo della modellazione FEA è di calcolare la distribuzione delle tensioni residue e delle deformazioni nel campione riparato.
Durante il processo di produzione additiva, significative tensioni termiche residue e distorsioni possono essere indotte dai laser ad alta intensità in movimento. Le elevate tensioni residue termiche rappresentano un problema critico in quanto possono causare distorsioni, cricche, guasti da fatica, con conseguente impatto sulla qualità del prodotto riparato. La deformazione e la distribuzione delle sollecitazioni nel processo di fabbricazione additiva possono essere simulate con il metodo degli elementi finiti (FEA) impostando proprietà del materiale, specifiche condizioni e andando ad ottimizzare i parametri di progettazione al fine di ottenere prestazioni specifiche. Inoltre, è necessario monitorare e tracciare l’evoluzione delle sollecitazioni residue durante e in seguito la riparazione per ottenere una stampa di successo di componenti 3D complessi.
Conclusioni
Il processo LDMD si dimostra una tecnologia di produzione additiva molto promettente, in particolare per quanto riguarda la rimessa a nuovo di componenti critici, in passato difficili se non impossibili da riparare. Alcuni componenti risultano troppo piccoli per procedere alla riparazione mediante tecniche convenzionali, per il possibile danneggiamento delle parti stesse, soprattutto a causa della formazione di una ampia zona interessata dal calore. Il processo LDMD, invece, produce una zona scarsamente influenzata dal punto di vista termico, grazie al laser utilizzato come fonte di energia. Inoltre, le proprietà del laser lo rendono applicabile solo all’area in cui è effettivamente necessario intervenire. L’alta risoluzione ottenibile con il raggio laser rende possibile la creazione di parti miniaturizzate e la riparazione delle stesse con elevata precisione. Il successo della tecnologia LDMD può essere attribuito anche al rapido raffreddamento del processo. Un’altra proprietà unica è poi la possibilità di realizzare un nuovo pezzo su di un pezzo preesistente, garantendo una elevata integrità metallurgica. Abbiamo visto come i punti di forza del processo LDMD ne favoriscano l’uso per la riparazione, la rigenerazione e la modifica di componenti anche complessi, come le ruote dentate.
In futuro, grazie allo sviluppo ICT, si prevedono ulteriori evoluzioni ed applicazioni del processo in ambito industriale, in un’ottica di economia circolare e di risparmio delle risorse, con la possibilità di offrire agli operatori la flessibilità necessaria per modificare un progetto con facilità, intervenendo in fase di progettazione senza dover ricominciare da zero o convertire una macchina utensile o un’attrezzatura pre-esistente. Componenti obsoleti possono oggi già essere rigenerati modificandone il design. Il processo LDMD risulterà appropriato infine per estendere la vita utile dei componenti, depositando materiali ad alte prestazioni sulla superficie del componente stesso.
Giorgio De Pasquale, Dipartimento di Ingegneria Meccanica e Aerospaziale, Politecnico di Torino, Smart Structures and Systems Lab Elena Perotti, Senior data analyst