Dopo il precedente articolo introduttivo, andremo qui ad approfondire quali siano i meccanismi di dettaglio che possono portare alla nascita delle tensioni residue, conoscenza fondamentale per poter impostare azioni preventive e correttive al fenomeno.
Come abbiamo avuto modo di vedere nello scorso articolo, le tensioni residue nei materiali metallici sono sempre una manifestazione macroscopica di una “disomogeneità” presente nel materiale.
Questa disomogeneità può riguardare una qualsiasi delle caratteristiche meccaniche o metallurgiche del materiale, e praticamente può essere originata da qualsiasi forma di lavorazione che comporti una trasformazione meccanica, metallurgica, chimica o termica.
Basta questo breve accenno per capire come la saldatura, in quanto processo che comporta la compenetrazione di materiali diversi mediante una trasformazione ad alta temperatura come è la fusione, presenti non una ma tutte le condizioni preliminari per l’instaurarsi di tensioni residue, tensioni che nell’ipotesi più fortunata possono dar luogo immediatamente a rotture o deformazione nei materiali interessati, ma che nell’ipotesi più pericolosa creano invece le condizioni per successive rotture precoci e apparentemente inspiegabili dei componenti saldati.
Ma cosa è la saldatura?
Semplificando al massimo, la saldatura è un processo nel quale due parti inizialmente separate acquistano una continuità fisica attraverso la fusione e successiva risolidificazione di materiale nella zona di contatto, realizzando quindi una compenetrazione fisica direttamente tra il materiale dei componenti da unire (saldatura autogena) oppure sfruttando un materiale di apporto in grado di compenetrarsi separatamente con il materiale dei componenti di partenza (saldatura eterogena).
A prescindere dal fatto che si sia utilizzato o meno un materiale di apporto, al termine del processo di saldatura nella zona della giunzione si possono individuare tre zone metallurgicamente distinte (figura 1):
- Zona fusa, ossia la zona costituita dalla solidificazione del materiale inizialmente portato allo stato liquido.
- Zona Termicamente Alterata (ZTA), ossia la zona che pur non avendo raggiunto la temperatura di fusione, ha comunque raggiunto una temperatura tale da causare una trasformazione metallurgica
- Zona termicamente inalterata, ossia la zona in cui le macro caratteristiche fisiche del materiale coincidono con quelle che aveva precedentemente alla saldatura.
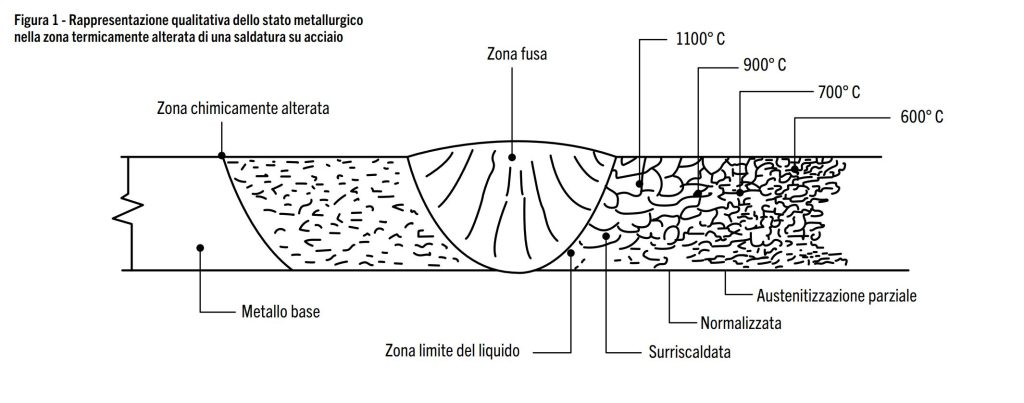
Materiali diversi, alterazioni metallurgiche diverse, transizioni termiche diverse: se per creare le condizioni di innesco delle tensioni residue è necessario che sia presente una qualche forma di discontinuità, dobbiamo riconoscere che davvero la saldatura di discontinuità ne offre un completo campionario!
Consideriamo ad esempio il caso di un acciaio bonificato: l’effetto combinato della temperatura raggiunta durante la saldatura e dalla successiva velocità di raffreddamento possono comportare un’alterazione metallurgica sotto forma di normalizzazione, austenitizzazione parziale o addirittura tempra.
Se l’acciaio di partenza ha invece un suo tenore austenitico, è possibile che l’apporto termico porti alla formazione di ulteriore austenite o alla sua scomparsa, cosi come velocità di raffreddamento diverse in zone adiacenti possono portare alla solidificazione in tempi diversi per zone diverse, riproducendo le criticità già viste a carico dei trattamenti termici.
La combinazione di questi meccanismi può portare anche a superare localmente il limite di snervamento del materiale lasciando zone localizzate deformate plasticamente e soggette al ritorno elastico delle zone adiacenti rimaste in campo elastico.
Possiamo quindi individuare tre diverse condizioni conseguenti a un raffreddamento differenziato tra zone adiacenti.
A titolo indicativo supponiamo di avere un elemento caratterizzato da parti massive collegate da una parte a parete sottile (figura 2): in termini qualitativi la parte a parete sottile arriverà a raffreddarsi quando le parti massive sono ancora in fase plastica.
Il successivo raffreddamento della parte massiva ne causerà la contrazione, con la conseguenza che l’elemento a parete sottile dovrà estendersi per non perdere la continuità strutturale, con diverse possibili conseguenze:
- Nel caso in cui l’allungamento richiesto alla parte a parete sottile rimanga all’interno dell’allungamento a snervamento, allora in questa zona del materiale si avranno le condizioni per una sollecitazione elastica di trazione (figura 3).
- Nel caso in cui conseguentemente al raffreddamento la sollecitazione elastica nella parte a parete sottile superi localmente il limite di snervamento, si ha la creazione di una sollecitazione elastica di ritorno, di segno opposto alla precedente e pertanto di compressione (figura 4).
- Se la deformazione differenziale è ancora maggiore e arriva a superare il limite di rottura, si verificano le cosiddette rotture a caldo della saldatura (figura 5).
A dire la verità è possibile anche una quarta opzione, ossia che la rigidezza della parte massiva sia sufficientemente bassa da permettere alla trazione esercitata dalla parete sottile di deformarla.
In questo caso l’energia che altrimenti sarebbe rimasta bloccata sotto forma di tensione residua si scarica sotto forma di deformazione, deformazione che può essere diretta perpendicolarmente o parallelamente al cordone di saldatura stesso (figura 6 e figura 7).
Questa ultima osservazione deve farci riflettere sull’opportunità di utilizzare maschere o bloccaggi per vincolare le parti durante la saldatura: è vero che questo garantisce la conformità geometrica del prodotto finale, ma è anche vero che, in assenza di successivi trattamenti termici di distensione, un sistema di vincoli cosi rigido impedisce alle tensioni residue di sfogarsi attraverso le deformazioni geometriche.
Problemi a scoppio ritardato
Come abbiamo visto, la saldatura può comportare deformazioni e rotture del cordone, fenomeni apparentemente comprensibili essendo quasi intuitivo che un ritiro del materiale fuso possa creare una “mancanza”.
Meno intuitivo è che tali fenomeni di frattura del materiale o di sua deformazione possono svilupparsi non solo durante la saldatura, ma anche successivamente durante il raffreddamento, durante trattamenti termici successivi alla saldatura stessa o addirittura con il componente a riposo, e comunque in apparente assenza di sollecitazioni meccaniche esterne.
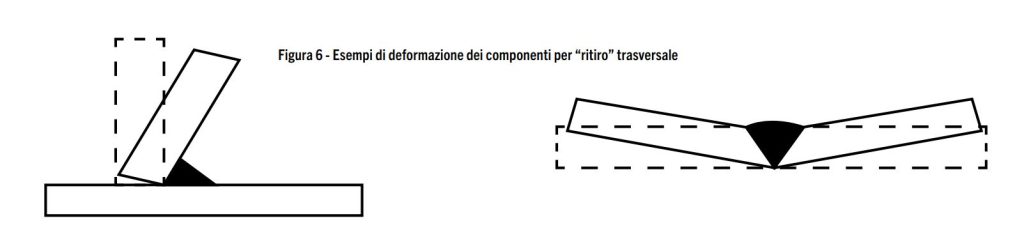
In realtà tutte queste rotture avvengono solo apparentemente in assenza di sollecitazioni: le sollecitazioni responsabili di tali effetti ci sono, è solo che non sono sollecitazioni applicate esternamente al corpo come quelle che siamo abituati a considerare, ma sono sollecitazioni che evidentemente nascono all’interno del materiale e si equilibrano all’interno del corpo steso senza manifestarsi esternamente: sono cioè quelle tensioni residue che abbiamo introdotto nel modello del paragrafo precedente.
Un modello che effettivamente è stato eccessivamente semplificato, sacrificando un po’ troppo la correttezza formale all’intuitività degli effetti: entriamo quindi un po’ più nel dettaglio di quelli che sono i meccanismi che possono portare alla nascita delle suddette tensioni residue.
Come abbiamo già avuto modo di vedere (o possiamo farlo tornando indietro all’articolo introduttivo nel numero precedente) le possibili origini delle disomogeneità che portano alla nascita delle tensioni residue sono 4:
- termica;
- meccanica (deformazione plastica);
- chimica;
- metallurgica (transizione di fase).
Nel caso specifico della saldatura, in realtà queste possibili origini si riducono a due, ossia quella termica e quella metallurgica.
Relativamente all’origine termica, si possono individuare due possibili meccanismi, eventualmente anche interagenti tra di loro:
- nel caso di sistemi multifasici (come ad esempio gli ottoni, gli acciai duplex o comunque con significativo tenore di austenite) la differenza tra i coefficienti di espansione termica in caso di variazioni di temperatura;
- la non contemporaneità del raffreddamento tra le diverse zone dello stesso componente precedentemente riscaldato, soprattutto in presenza di forti vincoli esterni che “blocchino” la deformazione complessiva del componente (e questo è il meccanismo utilizzato a scopo esemplificativo nel modello del paragrafo precedente).
Relativamente agli aspetti metallurgici, nel caso dei metalli ogni qualvolta ha luogo una variazione nella struttura cristallina del materiale, questo comporta variazioni volumiche dei singoli grani, che all’interno di un contesto più o meno rigidamente vincolato porta alla nascita di tensionamenti elasto-plastici nel materiale: questo ad esempio è quello che accade durante la saldatura di un acciaio temprato (o da tempra), con la coesistenza di ferrite, martensite, bainite, perlite, cementite ecc.
Tale effetto è ancora più accentuato nel caso ci si trovi di fronte al caso di strutture multifase come gli acciai duplex o comunque con significativi tenori di austenite, nel qual caso oltre alla variazione di volume intrinseca dei singoli grani si devono anche gestire la differenza di variazione di volume tra le diverse fasi, dimensionalmente ben più significativa.
A titolo esemplificativo, nella figura 8a è rappresentata prima la variazione di volume e di forma di un singolo grano di austenite che si trasforma in ferrite, con passaggio da struttura cubica a corpo centrato a struttura cubica a facce centrate. A seconda che la trasformazione avvenga con meccanismo di ricostruzione o di diffusione il nuovo grano risulta semplicemente un “ingrandimento” del precedente o una sua replica distorta.
Nella figura 8b si vede l’effetto dimensionale macroscopico della trasformazione da austenite a ferrite su un componente: nel caso in cui il componente sia privo di vincolo esterno il risultato è una deformazione, se il vincolo è invece presente il risultato è la nascita di tensioni interne.
Conclusioni
Punto di partenza per la trattazione di un qualsiasi aspetto legato alle tensioni residue è che tali tensioni all’interno di un materiale metallico nascono dalla presenza di “disomogeneità” interne.
Queste disomogeneità possono riguardare tutte le caratteristiche meccaniche o metallurgiche di un materiale, e in pratica ogni processo di lavorazione meccanica, metallurgica, chimica o termica influisce significativamente su tali tensioni residue.
Nel caso specifico della saldatura, questa è un processo che comporta la compenetrazione di materiali diversi mediante un processo ad alta temperatura come è la fusione, e pertanto risulta una forte causa di tensioni residue, in grado non solo di dare luogo a rotture e deformazione immediate, ma anche di dar luogo a pericolosi stati tensionali interni che, eventualmente sovrapposti alle sollecitazioni di esercizio, possono portare a rotture precoci e apparentemente inspiegabili dei componenti saldati in esercizio.
In ogni caso è evidente come il fenomeno delle tensioni residue derivi da una combinazione di effetti difficilmente prevedibili e meno che mai modellizzabili, e da qui l’opportunità di poter procedere alla verifica sperimentale degli stati di tensione residua eventualmente presenti.
Ecco quindi che la nostra prossima pubblicazione sarà indirizzata proprio a illustrare le diverse metodologie di misurazione delle tensioni residue presenti in un componente soggetto a saldatura: un ausilio fondamentale sia per la verifica qualitativa di singole saldature sia, soprattutto, per la messa a punto di processi di saldatura.