Dopo il precedente approfondimento “storico” vediamo qui più da vicino l’iter che oggi un’azienda deve seguire per essere in regola con i requisiti per lavorare in piena sicurezza.
“Il datore di lavoro” in primis, dopo aver formato adeguatamente i propri collaboratori preposti all’uso di determinati macchinari, deve porsi l’obiettivo di fornire loro apparecchiature e impianti intrinsecamente sicuri, nonché accertarsi che tali apparecchiature corrispondano a tutti i requisiti di sicurezza previsti dalla normativa (marcatura CE o requisiti di cui all’Allegato V e VI del D. Lgs.81/08 Testo Unico Salute e Sicurezza sul Lavoro).
Le indagini svolte a seguito di infortuni avvenuti sul luogo di lavoro hanno spesso evidenziato che questi avvengono a causa dell’assenza delle adeguate attrezzature di sicurezza obbligatorie per i lavoratori o, addirittura, a causa di un uso inappropriato delle stesse.
In questi casi il legislatore è molto attento alle dinamiche attraverso le quali avviene l’infortunio anche perché, nello specifico, le normative vigenti che regolamentano il settore della lamiera consentono di raggiungere livelli di sicurezza più che soddisfacenti in grado di calmierare o addirittura inibire l’infortunio. Questo vale anche per macchinari cosiddetti di “vecchia generazione”, costruiti in anni in cui non era necessario sottostare a determinate normative di sicurezza, perché sono state emesse delle linee guida in grado di colmare eventuali lacune normative “riportandole allo stato dell’arte”.
Quindi, laddove su un macchinario non sussistano i presupposti di garanzia di lavorare in totale sicurezza per l’operatore, nasce l’esigenza di intraprendere un percorso di adeguamento del macchinario stesso per poterlo allineare agli standard attuali che assicurano l’incolumità del lavoratore, avvicinando la macchina obsoleta ad una di “nuova generazione”.
Il datore di lavoro è pertanto tenuto a seguire pedissequamente le norme in materia di sicurezza che prevedono «l’obbligo di verificare costantemente, anche con il passare del tempo, la rispondenza delle attrezzature di lavoro rispetto all’epoca della loro produzione, ai requisiti previsti dalla legge in tema di sicurezza per i lavoratori (anche in conseguenza di innovazioni normative ed aggiornamenti tecnologici), fino al punto di non utilizzare l’attrezzo ove non sia possibile applicarvi apparati di protezione».
È bene precisare che:
- gli interventi di adeguamento non costituiscono una nuova immissione sul mercato e pertanto non richiedono procedure per la marcatura “CE”.
- gli adeguamenti, inoltre, possono essere eseguiti da ditte competenti e regolarmente iscritte alla CCIAA. Infatti, non esiste alcuna norma di legge che stabilisce i requisiti di tali soggetti: la loro scelta rientra tra le responsabilità del datore di lavoro il quale, dovesse ritenere che la propria azienda possegga professionalità e competenze adeguate, può provvedere autonomamente all’adeguamento delle proprie macchine. Dopo questi passi è comprensibile che, qualora accada un grave infortunio in cui il macchinario è la causa dell’incidente stesso, risulti necessario dimostrare alle autorità preposte alle indagini che il macchinario, oltre ad essere dotato di tutti i dispositivi di sicurezza installati adeguatamente sul macchinario e che siano in piena efficienza, non sia stato possibile installarvi un dispositivo di sicurezza con livelli tecnologici e di protezione maggiore.
Questa attività di “retrofitting” deve comprendere anche l’aggiornamento della documentazione tecnica, come ad esempio gli schemi elettrici, gli schemi idraulici, il manuale d’uso e di manutenzione.
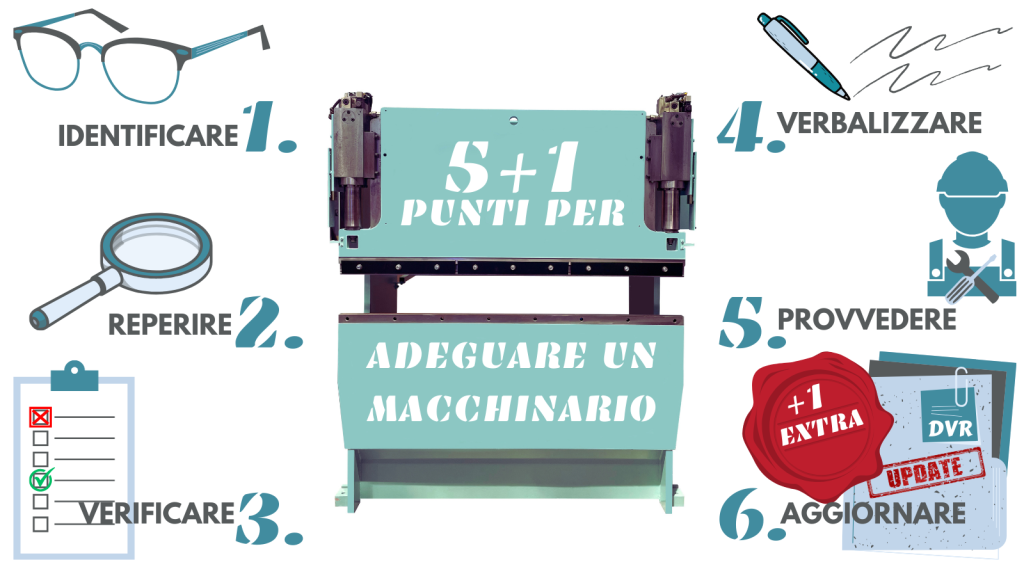
- Se la macchina fosse sprovvista del manuale d’uso e manutenzione è necessario predisporre schede con procedure o istruzioni operative nelle quali vengono riportate le norme comportamentali e le misure di sicurezza che gli operatori debbono rispettare durante l’uso della stessa.
- In caso di vendita dovrà essere rilasciata una dichiarazione di conformità ai requisiti di sicurezza citando le norme e, laddove possibile, le linee guida.
- Qualora venga rottamata sarà doveroso farlo attraverso aziende autorizzate allo smaltimento dei rifiuti. Non è possibile vendere una macchina non adeguata o come rottame utilizzando clausole del tipo “vista e piaciuta”, le quali non esonerano il venditore dalle proprie responsabilità.
Che iter deve seguire un’azienda per soddisfare appieno i requisiti di adeguamento dei propri macchinari per la messa in sicurezza?
Come prima cosa si rende necessario eseguire una sorta di censimento delle macchine di ciascun reparto con le informazioni necessarie per identificare tutte le attrezzature/macchine/impianti che potenzialmente potrebbero comportare un pericolo per la salute e/o la sicurezza dell’operatore durante il suo utilizzo.
Punto 1 – Identificazione dei macchinari destinati all’utilizzo durante determinate fasi lavorative
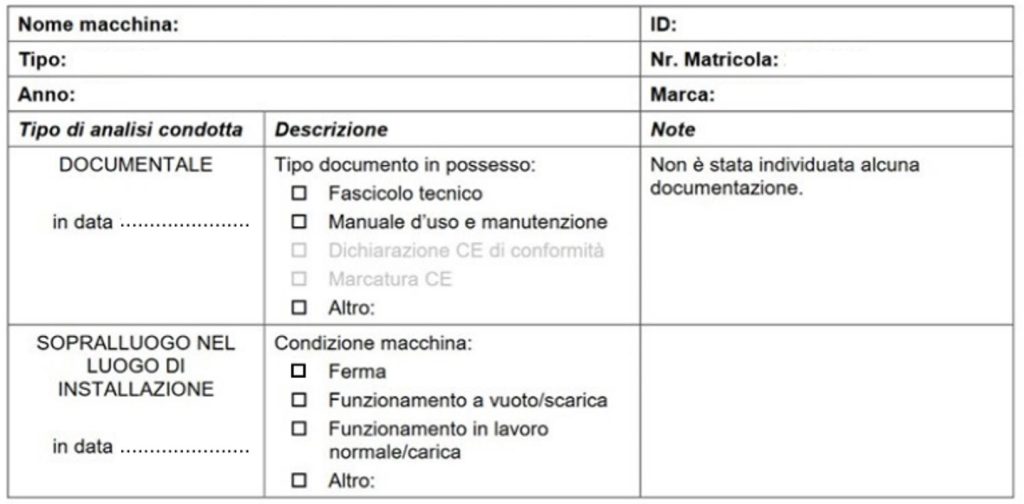
Un buon punto di partenza potrebbe essere quello di effettuare un sopralluogo presso ciascun reparto lavorativo schedando ogni macchinario mediante una fotografia evidenziando la targhetta identificativa per inserire poi le informazioni di ciascuna macchina all’interno di una tabella che ne riporti i dati fondamentali.
Punto 2 – Reperimento della documentazione tecnica a corredo del macchinario
Bisogna creare la storia dei macchinari; per questo il secondo punto è quello di reperire tutta la documentazione tecnica di ogni attrezzatura presente nell’azienda. In particolare, si dovrà controllare la presenza del manuale d’uso e manutenzione e delle dichiarazioni di conformità rilasciate dal costruttore con i relativi schemi elettrici /idraulici/pneumatici.
A fine lavoro si applicherà una targa sulla macchina che identifichi univocamente la stessa rispetto alle altre.
Punto 3 – Verifica dei requisiti di conformità delle attrezzature e conseguente identificazione dei pericoli
La fase successiva a quanto sopra elencato consiste nell’analisi e valutazione dei rischi. Questi andranno effettuati attraverso una verifica visiva e funzionale fatta macchina per macchina con il fine di conseguire i seguenti obiettivi:
- verificare se la macchina abbia subito modifiche che non rientrano nell’ordinaria e/o straordinaria manutenzione. In questo caso, le macchine devono essere sottoposte alla procedura di certificazione prevista dal D.P.R. 459/96 all’articolo 4 comma 7;
- accertarsi che siano stati rispettati i requisiti di conformità previsti dalla normativa (es. mancanza di carter di protezione, possibilità di accesso agli organi mobili);
- identificare ed eventualmente valutare i rischi derivanti dall’impiego delle attrezzature ai sensi della direttiva macchine 2006/42/CE (per attrezzature marcate CE) e ai sensi dell’Allegato V D.Lgs. 81/08 (per le attrezzature non CE).
Punto 4 – Stesura della relazione tecnica per la verifica di rispondenza della macchina alle normative vigenti
Per ciascuna macchina/attrezzatura non marcata CE che abbia subito modifiche deve essere redatta una relazione tecnica con lo scopo di verificare la rispondenza delle macchine alle normative di sicurezza vigenti, nonché individuare gli eventuali interventi necessari per il loro adeguamento.
Allegato V D.Lgs 81/08 = Requisiti di sicurezza delle attrezzature di lavoro costruite in assenza di disposizioni legislative e regolamentari di recepimento delle direttive comunitarie di prodotto o messe a disposizione dei lavoratori antecedentemente alla data della loro emanazione.
Allegato VI D.Lgs 81/08 = Disposizioni concernenti l’uso delle attrezzature di lavoro.
Ogni argomento trattato dai due allegati viene verificato sulla macchina, da qui, la verifica può restituire tre risultati:
- CONFORME: non sono necessari interventi di adeguamento.
- NON CONFORME: sono necessari interventi di miglioramento.
- NON APPLICABILE: la macchina non può essere adeguata.
Fase 5 – Eventuali provvedimenti tecnici se la macchina non risulta conforme
Se la macchina non risulta conforme (carente, quindi, di dispositivi o sistemi di sicurezza), è necessario adottare provvedimenti tecnici per renderla conforme sulla base di un’opportuna valutazione, eseguita da consulenti esperti, per la verifica dei requisiti ai sensi dell’Allegato V e Allegato VI del D.Lgs. 81/08.
Gli interventi di adeguamento devono essere mirati non solo e non necessariamente al ripristino dei dispositivi posseduti dalla macchina al momento dell’acquisto e che nel corso della vita produttiva sono stati rimossi o danneggiati, ma devono tenere conto dell’evoluzione tecnica che dall’epoca della costruzione sono intervenuti sino alla data dell’adeguamento.
La sostituzione di una macchina può essere una scelta condivisibile quando le condizioni di obsolescenza e di costo rendono conveniente questa soluzione.
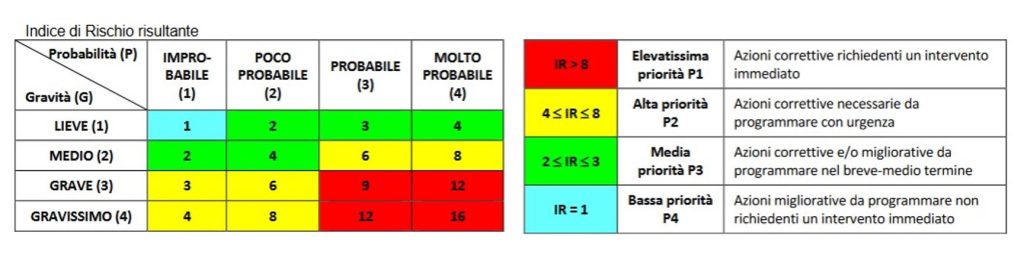
Anche se è molto raro, all’interno della valutazione dei rischi si potrebbero evidenziare rischi residui non eliminabili con la sola applicazione delle disposizioni dell’allegato V. In questo caso, i rischi residui dovranno essere gestiti mediante un’adeguata formazione degli operatori, che deve essere documentata e specifica per la macchina e che comprenda i rischi residui della stessa, oltre ad intervenire con “ridondanti” segnaletiche di sicurezza (UNI 7010).
Fase 6 – Aggiornamento del documento di valutazione dei rischi
Al termine degli interventi di adeguamento sarà infine necessario:
- aggiornare il Documento di Valutazione dei Rischi (DVR) con i nuovi punteggi di stima del rischio e la gestione dei rischi residui;
- effettuare adeguata formazione documentata degli operatori sull’utilizzo della attrezzatura e alla gestione di eventuali rischi residui.