Il pezzo deve essere sempre più preciso. La lavorazione sempre più efficiente. La marginalità…dovrebbe essere salvaguardata. Tre aspetti di una stessa questione, ovvero il processo produttivo. E il processo produttivo è irto di insidie perché, come ogni addetto ben sa, si tratta di “qualcosa” di veramente complesso, dove le variabili in gioco, e le loro correlazioni, quasi non si contano! La sfida, che non ci si può permettere di perdere, è quella del riuscire a tenere tutto, o almeno buona parte, sotto controllo, senza permettere che l’insorgere di criticità diventino un problema. La buona notizia è che c’è un alleato veramente potente: la Metrologia Industriale!
Renishaw, azienda inglese leader nella metrologia industriale, ha ben nota l’importanza di affrontare i problemi alla fonte, laddove si originano. Questa consapevolezza nasce dall’essere, prima di tutto, un’azienda manifatturiera, cliente primo delle soluzioni poi portare sul mercato, e questo all’interno dei propri stabilimenti produttivi, caratterizzati, fra l’altro, da elevati livelli di automazione e connettività, in modo da gestire in modo ottimale le lavorazioni del metallo. Grazie al know-how acquisito in-house, Renishaw è in grado di offrire un valido aiuto e supporto a tutte quelle aziende che intendono migliorare i propri processi produttivi, rendendoli stabili, efficienti e di qualità.
Patrizio Titotto, Industrial Metrology Business Manager Renishaw Italia, ha condiviso con Macchine Utensili il ruolo della metrologia industriale in un moderno sistema produttivo.
Un ruolo strategico
Fino a qualche anno fa “metrologia” faceva pensare essenzialmente alle attività da sala metrologica. Oggi si parla con sempre maggiore insistenza di metrologia industriale: una differenza che non è solo nei termini.
Oggi ha senso parlare di “Metrologia Industriale”, o Industrial Metrology, proprio perché ci si è resi conto che, per raggiungere i livelli di qualità e produttività desiderati, la sala metrologica non basta.
Analizzando un qualsiasi processo produttivo, se è inefficiente può innescare, come risultato, considerevoli perdite di redditività e competitività. Quali possono essere i “segnali” più evidenti? Le rilavorazioni dovute a non conformità, gli scarti di produzione, gli elevati costi della qualità, i ritardi nelle consegne, solo per citarne alcuni. Oggi, in un mondo sempre più orientato all’automazione, potere contare su processi automatizzati e produttivi è indispensabile comprendere le cause delle inefficienze ed eliminarle alla fonte. In questo scenario, il ruolo della metrologia industriale è strategico.
Implementare le tecnologie Renishaw può aiutare le aziende manifatturiere a prolungare la durata dei propri impianti e macchinari, ma anche a incrementare la produttività complessiva.
La metrologia industriale secondo Renishaw si può dire che sia a tutto tondo, toccando tutto ciò che coinvolge il processo produttivo. Essere voi stessi, nei vostri stabilimenti, i primi fruitori dei vostri sistemi di controllo e gestione, vi porta capire cosa realmente serve e dove serve
Certamente: possiamo verificare quotidianamente le nostre soluzioni, applicate al sistema produttivo. Per noi, fornitore e cliente al tempo stesso, è chiaro come un processo debba essere prevedibile, ripetibile e affidabile, se si vogliono produrre pezzi conformi. In caso contrario si ottengono inevitabilmente colli di bottiglia, ritardi e prodotti di scarsa qualità. E non va bene! Questo ci ha portato ad una schematizzazione attraverso una figura solida, una piramide, divisa in 4 layer, ognuno dei quali rappresenta una fase del processo produttivo. E ad ogni layer, ovvero ad ogni fase, sono associati i controlli relativi, in modo da rendere il processo produttivo stabile ed efficiente. Va sempre tenuto presente che l’obiettivo non deve essere quello di ridurre l’inefficienza, ma piuttosto quello di massimizzare l’efficienza.
Crediamo fermamente al nostro quadro esemplificativo, alla piramide, che quindi ha un nome: Processo Produttivo Pyramid™.
La piramide e i suoi livelli
La piramide mostra quindi come utilizzare vari livelli di controllo per rimuovere, in modo sistematico, le cause di inefficienza dei vari processi. Quindi c’è una sorta di “crescendo”, di percorso da seguire, se si vogliono raggiungere i risultati attesi: da dove si parte?
Vogliamo ottenere una produzione efficiente e pianificabile. Se dobbiamo costruire, da dove si parte? Dalla base, ovvero dai fondamentali.
I fondamentali rappresentano i “requisiti base” e sono controlli preventivi, che si fanno in anticipo, prima che parta la produzione. L’obiettivo è quello di ridurre la possibilità di eventuali errori, prima ancora che inizi la lavorazione. Quindi si controllano i macchinari, lo stato di salute della macchina utensile, perché una macchina poco accurata non può produrre pezzi precisi. Per contro, se la macchina è in ordine, i pezzi saranno conformi ed eventuali interruzioni non pianificate saranno ridotte al minimo.
Strumenti di controllo adeguati consentono check regolari delle condizioni, in modo da individuare le cause di eventuali errori, riducendo al minimo interventi di manutenzione di emergenza grazie alle attività di prevenzione. Renishaw offre questi strumenti, che sono essenziali per capire meglio le capacità di una macchina e per concentrare gli sforzi sul controllo delle prestazioni. Sono laser interferometrici, ballbar e, ultimamente, AxiSet™ Check-Up, un software per la corretta verifica dei punti pivot, cioè del setup dei centri di rotazione degli assi rotativi.
Con che frequenza vanno fatti i controlli fondamentali, sulla macchina?
Non esiste una regola perché molto dipende dal tipo di lavorazione, dal carico…In generale, si può dire “dalle condizioni”. Questo significa che potrebbe essere 1 volta alla settimana, o all’inizio della lavorazione di un nuovo lotto produttivo, ma anche alla fine di ogni giornata: si tratta di controlli che richiedono veramente solo pochi minuti.
Stabilito lo stato della macchina, effettuati eventuali aggiustaggi, il livello successivo dove ci porta?
Alla preparazione dei processi, cioè ai controlli predittivi, che si applicano appena prima di iniziare la lavorazione. In questa fase è un po’ come se si stabilissero i rapporti fra macchina utensile, pezzo e utensile, non durante la lavorazione, ma appena prima che inizi il taglio.
Vengono controllate le variabili causa di possibili inefficienze produttive come la posizione del pezzo, le dimensioni degli utensili e gli offset della macchina: la mancanza di opportune verifiche che potrebbe causare la produzione di componenti non conformi.
Si esegue dunque il presetting dell’utensile, la verifica della corretta impostazione del pezzo in macchina, l’impostazione della macchina tenendo presente che gli errori macchina non corretti sono un fattore dominante per la non conformità, e possono aumentare significativamente i tempi di preparazione, dato che i loro effetti possono essere facilmente confusi con altri tipi di variazioni.
Questi sistemi sono abbastanza consolidati in officina, anche se vengono utilizzati/sfruttati solo in parte; in genere si ha una maggior sensibilità verso questo tipo di controlli all’acquisto di una nuova macchina utensile. La preparazione dei processi resta indispensabile nel caso di lavorazioni 5 assi o multitask, mentre viene più facilmente trascurata, pur essendo un errore dalle possibili pesanti conseguenze, nel caso di macchine utensili “più povere”, tipo i torni a 2 assi.
A questo punto iniziamo la lavorazione: cosa succede? Lavoriamo il pezzo e poi lo si controlla?
Questo era il modo del passato di vedere la metrologia, dove solo a fine lavorazione, valutando la conformità o meno del pezzo, ci si poteva rendere conto se tutto era andato bene. Oggi possiamo fare di più: seguendo la nostra piramide, arriviamo al terzo layer, quello dei controlli di processo.
I controlli di processo possono essere definiti come “controlli attivi” perché verificano le fonti di variazione inerenti alla lavorazione, come l’usura degli utensili e gli sbalzi di temperatura, fornendo un feedback proprio durante l’avanzamento della lavorazione.
Impegnati a “far truciolo”, questo è solitamente il livello meno compreso dalle aziende e, di conseguenza, meno sfruttato, anche se, di fatto, le ispezioni in macchina costituiscono l’unico sistema per monitorare in-process lo stato del pezzo. In fondo si tratta di un modo per fornire alla macchina l’intelligenza necessaria per prendere decisioni, anche se non si tratta di intelligenza artificiale, riportando il processo in tolleranza ed eliminando gli effetti indesiderati delle derive. La retroazione immediata, in caso di non coerenza con le specifiche, porta ad un processo stabile e automatizzato, che minimizza l’intervento umano (possibile fonte di errori), riducendo drasticamente gli scarti o pezzi da rilavorare.
Le sonde per ispezioni dei pezzi, il sistema di riconoscimento utensili, il software Productivity+™, che integra le attività di presetting e taglio, adattano le operazioni di taglio del metallo all’effettivo materiale e alle condizioni ambientali grazie a un feedback automatizzato.
Un po’ come aneddoto, è interessante notare come Renishaw sia “nata” con il primo tastatore 3D, Touch Trigger Probe: da questa invenzione, lo spirito innovativo e l’attenzione verso le esigenze del mercato, non sono mai venuti meno.
Il pezzo è stato lavorato. Speriamo sia andato tutto bene, dato che sono stati attuati tutti i controlli finora previsti dalla piramide. Però la speranza non basta: come avere certezze?
A questo punto entra in gioco il livello più lato, la punta della piramide: siamo arrivati al controllo post process.
Col monitoraggio post-process si esamina la parte conclusiva del processo produttivo e dunque il pezzo finito rispetto alle relative specifiche, nonché la registrazione dei percorsi e dei risultati finali.
Le moderne tecnologie consentono di automatizzare i processi di ispezione anche per i pezzi più complessi, spesso con un’unica impostazione. In questo modo è possibile ridurre la presenza degli operatori specializzati, incaricati di supervisionare la qualità della produzione.
La verifica può essere eseguita direttamente in macchina mediante una sonda, presso la macchina con calibri o bracci articolati oppure su un dispositivo automatico fuori linea come una macchina di misura. Oltre alla tradizionale attività con macchina di misura in sala metrologica, il controllo eseguito in officina, ad esempio grazie alla nostra tecnologia di scansione a 5 assi REVO® ed il calibro versatile Equator™, è particolarmente interessante. Infatti l’utilizzo delle più recenti tecnologie a 5 assi consente di ispezionare i pezzi 3 volte più velocemente che in passato, mentre i sistemi di calibrazione versatili consentono di effettuare rapide ispezioni e di produrre feedback dei processi per pezzi di serie medie e grandi. Le moderne soluzioni di controllo post-process permettono di ottenere un sostanziale vantaggio produttivo rispetto alle tecniche tradizionali dato che maggiore rapidità di misura si traduce in un aumento della produttività senza rinunciare all’accuratezza
La metrologia si sta sempre più spostando verso l’officina: se prima la sala metrologica era slegata dall’ambiente produttivo, oggi è sempre più evidente il vantaggio della vicinanza, sia per una esigenza “fisica” (si evita il collo di bottiglia legato alle misure in sala metrologica), sia per la possibilità di retroazione verso la macchina utensile, con la possibile correzione in-process della lavorazione. Per esempio grazie al software IPC vengono messi in contatto il calibro Equator col controllo della macchina utensile in modo da effettuare in tempo reale eventuali aggiustamenti alla lavorazione, a fronte di misure fuori specifica.
La fabbrica del futuro
Lo spirito innovativo di Renishaw, la voglia di guardare sempre avanti, anche precorrendo i tempi, dove vi stanno portando?
Noi pensiamo ai processi produttivi, quelli di oggi, ma guardando anche al domani. Con questo spirito, per esempio è nato Renishaw Central la nuova piattaforma per la gestione della connettività e dei dati di produzione volta ad ottimizzare la produttività, la capacità e l’efficienza delle attività produttive. L’obiettivo è quello di rendere l’officina più connessa e accrescere il livello di omogeneità, controllo e affidabilità, aiutando l’industria manifatturiera a raccogliere dati sui processi end-to-end e a utilizzarli per sviluppare un’architettura di sistema in grado di coprire l’intero stabilimento.
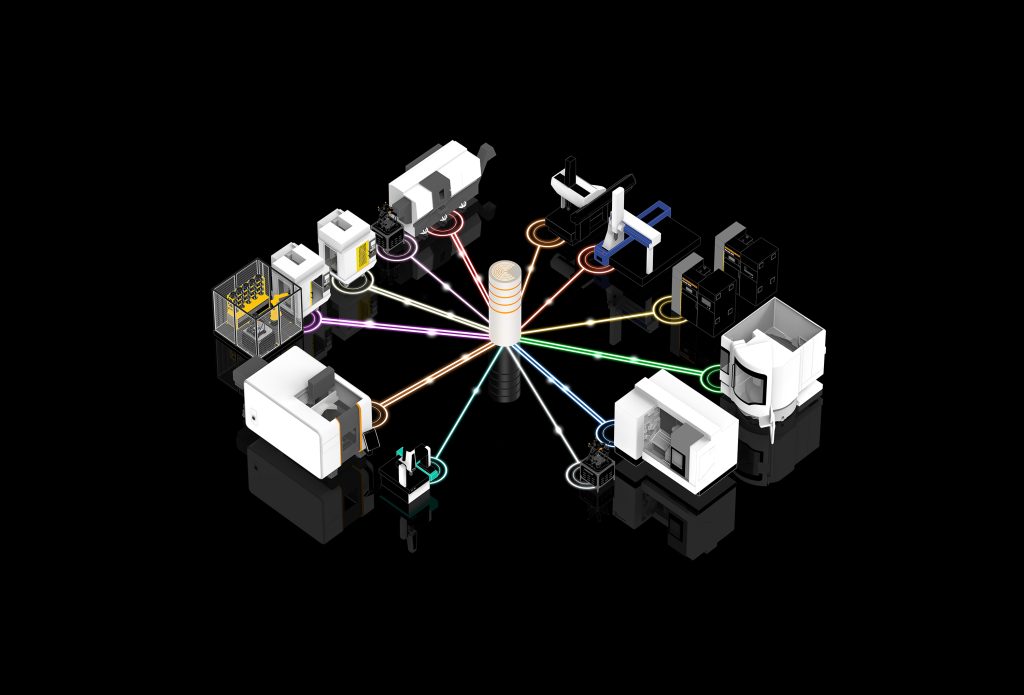
Renishaw Central raccoglie i dati sui processi di lavorazione e li rende disponibili a tutto lo stabilimento per consentire verifiche sul luogo di lavorazione. La piattaforma permette di valutare le prestazioni dei dispositivi presenti in officina, comprendere meglio come vengono utilizzati e verificare e convalidare la qualità dei pezzi. I dati sui dispositivi vengono visualizzati in tempo reale su una serie di dashboard molto intuitive, come è ormai prassi comune.
Grazie anche a Industria 4.0, oggi il mercato italiano sta capendo il ruolo della metrologia industriale in uno schema produttivo moderno. Le macchine utensili, sempre più evolute, obbligano ad un cambio di mentalità e, una volta visti i risultati, le aziende italiane sono molte più veloci di altre ad accettare il cambiamento, mettendolo a frutto!