Lo scorso 17 maggio si è tenuto presso il Dipartimento di Meccanica del Politecnico di Milano il primo workshop dell’anno di PoliMill.
Giorgio Calzona, capo del reparto sospensioni, del team di corse specifica: «Il team Dynamis PRC è la squadra corse del Politecnico di Milano: ogni anno produce un prototipo da corsa per gareggiare negli eventi di Formula Student contro altre università a livello europeo e mondiale».
Il componente lavorato come due anni fa parte della sezione sospensioni, seguita Calzona specificando: «Il Dynamis gareggia con un prototipo elettrico con quattro motori, uno per gruppo ruota, solidali ai portamozzi. La cinematica è composta da uno schema double wishbone con pushrod, l’elastica prevede due gruppi molla-smorzatore disaccoppiati in beccheggio e rollio per ogni asse. La trasmissione dei carichi dal gruppo ruota ai braccetti in carbonio avviene tramite i terminali A-Arm, che si accoppiano al portamozzo con snodi sferici e tramite incollaggio ai tubi. Le tolleranze più rilevanti riguardano l’angolo relativo tra gli attacchi dei braccetti, per rispettare le quote nominali della cinematica e il diametro della sede dello snodo, affinché abbia la corretta interferenza. Tali prerequisiti permettono di rispettare l’ipotesi di lavoro dei tubi come bielle, minimizzando l’eccentricità del carico: ciò permette di alleggerire il sistema e di minimizzare i diametri dei tubi, il che favorisce la gestione degli ingombri».
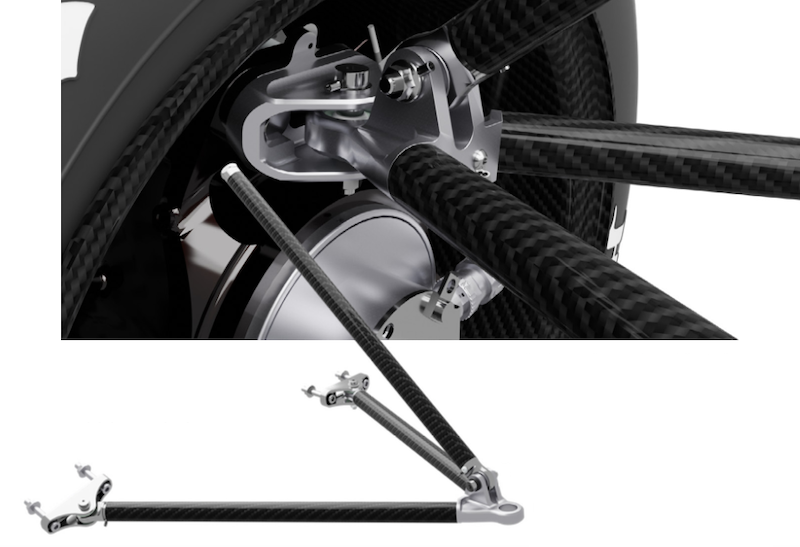
La programmazione e lavorazione del pezzo
Il pezzo lavorato fa parte di un lavoro più ampio commisionato dalla squadra corse al team di PoliMill a cui è stato richiesto di fabbricare tutti gli A-Arm, compresivi di pezzi di ricambio, per la stagione 2023-2024.
Una sfida questa, estremamente complessa, venendo da un contesto accademico in cui il gruppo è completamente autodidatta, una commessa vera e propria di fabbricare un componente di importanza focale per la macchina in serie con tolleranze centesimali non è stata presa alla leggera.
Le difficoltà affrontate hanno fatto riflettere sulle complessità di produrre un pezzo complesso a cinque assi al primo tentativo e si è deciso di riaffrontare la tematica di quanto ciò sia possibile narrandone la fabbricazione durante il workshop di maggio. La programmazione e lavorazione del pezzo si sono rivelate immediatamente molto complesse e hanno dato adito a una serie di problematiche, in particolare:
- Il materiale da lavorare era Al 7075. Una lega di alluminio estremamente prestante, leggera ma con carico di snervamento e durezza paragonabili a quelli di un acciaio. È una lega ampiamente utilizzata in ambito automotive e aerospace. Date le caratteristiche del materiale e la coppia massima al mandrino di 1.8 Nm a 27’000 RPM, la scelta delle strategie soprattutto in fase di sgrossatura ha richiesto uno studio attento e complesso.
- Le tolleranze strette da mantenere in maniera ripetitiva, non solo sul componente mostrato al Workshop ma su tutta la partita di 24 pezzi prodotti ha costretto il team a studiare anticipatamente le strategie di lavorazione in finitura, i parametri, del lubrorefrigerante e anche metodi di misura durante la lavorazione stessa per la verifica delle tolleranze chiave al corretto funzionamento dei componenti.
- Infine, la simulazione è stata di enorme ausilio in quanto è risultata determinante per risolvere errori di programmazione e per prevedere difetti superficiali anche minimi nell’ordine dei pochi micrometri. Innanzitutto, per poter gestire in maniera più efficace, rapida e stabile possibile le significative operazioni di sgrossatura si è optato per la strategia Adaptive Roughing di Siemens NX. Quest’ultima è una strategia trocoidale avanzata simile in concezione a come funzionano gli algoritmi proprietari di VoluMill, essa si basa sì passaggi fresa caratterizzate da alte passate assiali e bassi impegni radiali, tipicamente tra il 3 e il 10% del diametro. Tali percorsi generati dal CAM sono generati con l’obiettivo di mantenere il più costante possibile il volume di materiale asportato generando così una lavorazione molto più stabile anche mentre si sgrossano feature curvilinee dove l’impegno fresa aumenta.
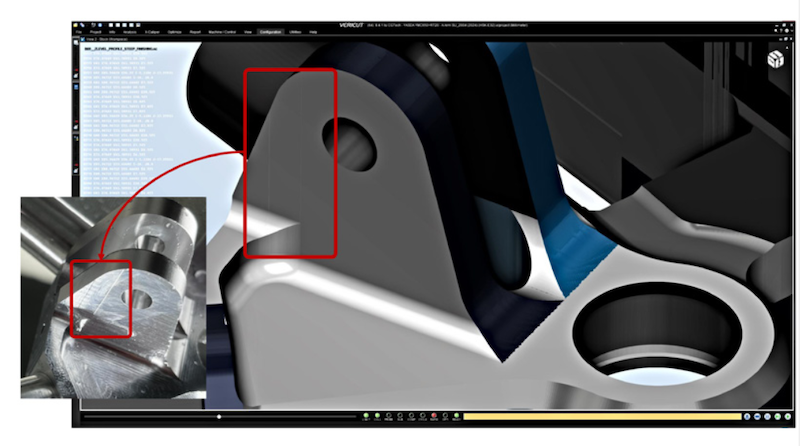
Il ruolo del refrigerante
La lubrorifregerazione ha svolto a sua volta un ruolo fondamentale permettendo di aprire in interpolazione elicoidale tutti i fori presenti sul componente e per una efficace evacuazione del truciolo. Le frese e le punte a forare infine sono state scelte in coordinazione con il personale specializzato di UMAC S.p.A., che ha fornito, ad esempio, la rompitruciolo Sandvik che ha permesso una sgrossatura efficace e veloce considerando i vincoli di potenza e coppia della macchina, una Yasda YMC650+RT20.
Infine, la simulazione, mediante il software Vericut, è stata pesantemente sfruttata per verificare la bontà delle operazioni programmate nel CAM prima di procedere a lavorare il pezzo in macchina.
Vericut simulando in maniera dettagliata la cinematica della macchina e sfruttando direttamente i parametri presi dal controllo ha potuto prevedere un serie di errori sia di programmazione che del postprocessore permettendo di arrivare alla lavorazione del primo pezzo con un programma completamente validato. Tanto è vero che la lavorazione è stata eseguita correttamente alla prima senza errori e con tutte le feature in tolleranza.
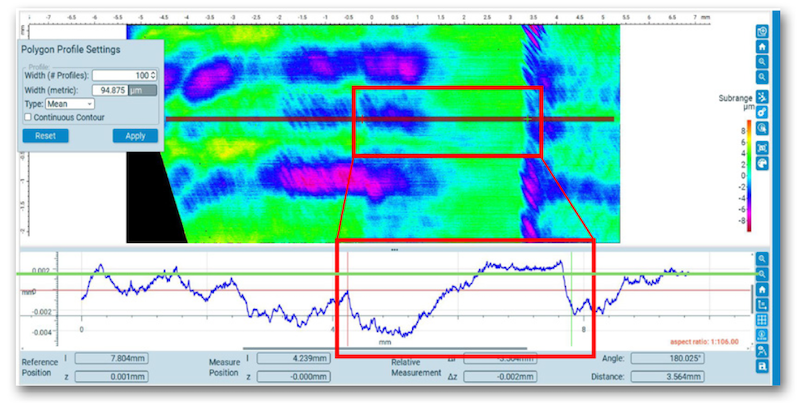
Simulazione del percorso utensile
La simulazione, però, ha permesso anche di poter eseguire delle analisi preliminari in termini di finitura superficiale del componente da lavorare. Vericut non è un FEM e non è in grado di simulare la dinamica della macchina utensile né tanto meno di riprodurre fenomenologie altamente complesse come vibrazioni, deflessioni utensile e simili. Il software però è in grado di simulare correttamente e nei minimi dettagli il percorso utensile prodotto dal CAM e tradotto in linguaggio macchina dal postprocessore.
Così facendo si riesce al netto dei fenomeni dinamici poter vedere come le strategie e i parametri settati nel CAM hanno un effetto sulla lavorazione del pezzo. In seguito all’uso improprio di una operazione si è potuto riscontrare un difetto visivo sul pezzo che era stato predetto da Vericut in fase di simulazione, ovvero un minuscolo plateau largo circa 4 millimetri e, a detta del software, profondo 4 micron.
Successive analisi svoltesi mediante la G6 di Alicona, un avanzato microscopio a 5 assi, hanno permesso di validare queste misure predette da Vericut. Un risultato sbalorditivo che dimostra come strumenti digitali possano prevedere anche errori piccolissimi in termini di programmazione.
Il workshop si è concluso dopo la consueta demo live della lavorazione con una tavola rotonda volta a favorire la discussione sulle tematiche calde che coinvolgono il manifatturiero italiano quali la mancanza di personale specializzato, la difficoltà nel formare personale all’uso delle più recenti e avanzate tecnologie e software e cosa possono fare le università e le aziende per attrarre i giovani a questo settore che ha così tanto da offrire.
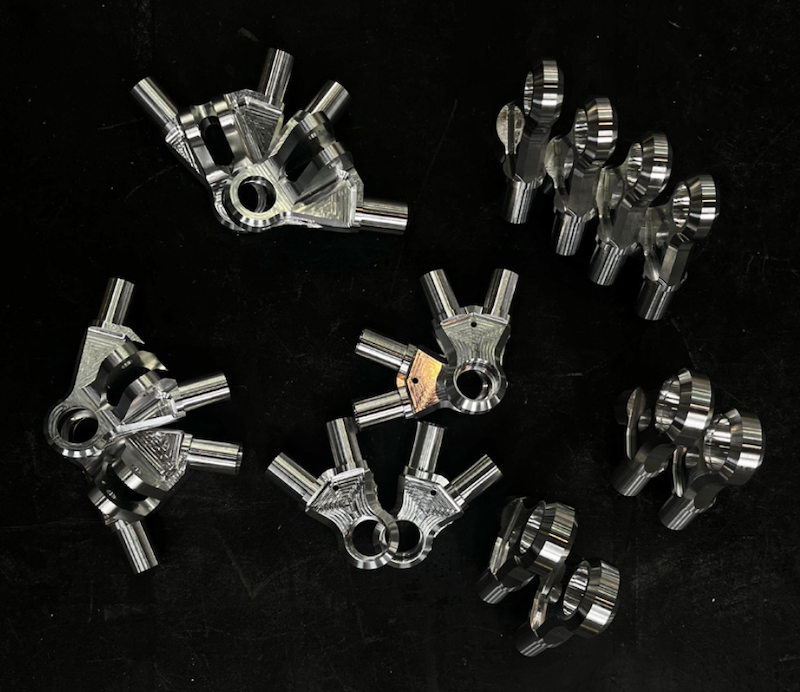
Conclusione
PoliMill, nel suo piccolo, cerca di contribuire il più possibile di contribuire a questo settore in molteplici maniere.
In primis formando giovani ingegneri nell’utilizzo di software avanzati come CAM e simulatori e trasmettendo il più possibile competenze che oggi come non mai non solo sono richieste ma necessarie alla sopravvivenza del settore.
In secundis il gruppo organizza workshop di digitalizzazione trasversale in cui operatori e capi produzione possono toccare con mano i benefici che comporta la digitalizzazione e i suoi strumenti. I workshop si svolgono nell’arco di tre giorni e i partecipanti si possono confrontare con un pool di esperti e partner PoliMill che possono permettere loro di approcciare le diverse tematiche trattate dalla scelta utensili alla simulazione, dalla analisi del lubrorefrigerante alla programmazione CAM.
Al di là del workshop la partnership di PoliMill con il reparto corse del Politecnico di Milano, il Dynamis PRC è un enorme traguardo per il gruppo che ha per la prima volta portato a termine una vera e propria commissione produttiva. Vedere una monoposta da corsa interamente progettata da giovani aspiranti ingegneri che correrà anche grazie al nostro contributo è un grande onore e piacere.
I partner industriali del gruppo di ricerca universitario
R.F. Celada, Ronchi-Ils, YASDA, Big Kaiser, CGTech, Bruker Alicona, Vection Technologies, Sandvik Coromant e ATS-Team3D. Il componente meccanico da realizzare è stato scelto di proposito identico a quello di due anni fa ovvero l’A-Arm del Dynamis, la squadra corse del Politecnico di Milano.