OPS è la Suite modulare che Salvagnini propone per supportare le aziende nella gestione e coordinamento dei flussi produttivi di fabbrica. OPS agevola il processo di trasformazione digitale: è una soluzione flessibile e personalizzabile a seconda delle esigenze delle tecnologie disponibili e della familiarità con il digitale.
Quando si parla di Smart Factory il primo pensiero che viene spesso in mente è quello di una fabbrica iperconnessa, nella quale le macchine parlano tra loro, si scambiano flussi di dati e ottimizzano le attività per migliorare l’efficienza dei processi in stabilimento.
Ma chi sovrintende a questo incessante flusso di dati per fare in modo che tutto il processo sia sempre sotto controllo? Sono molto attuali i software e le piattaforme MES (Manufacturing Execution System) ma c’è qualcuno che già diversi anni fa ha sviluppato una soluzione più evoluta, espressamente dedicata al mondo della lavorazione della lamiera, per permettere all’imprenditore di fare le scelte giuste nel momento giusto.
Stiamo parlando di OPS (Order Processing System), una suite di moduli marchiata Salvagnini che permette di rendere “intelligente” questo percorso e ne consente il controllo dialogando e interagendo con tutte le macchine Salvagnini oltre che con gli ERP e MRP dentro e fuori dalla fabbrica.
Il cammino di OPS verso l’efficienza di processo è iniziato già nel 1993, quando Salvagnini sviluppò il prototipo di questa piattaforma per venire incontro alle esigenze specifiche di un cliente che aveva bisogno di rispondere alle richieste del mercato col “lotto uno”, e necessitava quindi di produrre parti completamente diverse l’una dall’altra in logica make to order.
Da allora OPS si è via via evoluto dal punto di vista funzionale, trasformandosi in una soluzione out of the box a prescindere dal settore industriale o dalle dimensioni dell’azienda in cui viene installato. Abbiamo avuto la possibilità di vedere OPS all’opera visitando il Campus Salvagnini di Sarego: ecco com’è andata.
OPS, al centro del processo produttivo
Caratteristica distintiva di OPS è quella di collocarsi esattamente al centro del processo produttivo, proprio come agirebbe una torre di controllo: in questo senso, nello sviluppo tipico di un flusso di produzione, l’informazione parte dall’ERP che genera una lista di produzione; questa passa a OPS che, appena ricevuta la lista, la rende disponibile al programmatore che viene così informato istantaneamente della pianificazione.
Successivamente, grazie all’integrazione seamless tra OPS e l’ecosistema software STREAM che consente la definizione del processo di produzione secondo la migliore sequenza delle lavorazioni, e tramite una serie di regole personalizzate per il cliente, OPS crea automaticamente i programmi di produzione. L’ordine di lavoro può essere sottoposto a modifiche manuali da parte del programmatore, oppure accettato e passato direttamente in produzione.
Creato l’ordine di lavoro, OPS lo trasferisce a bordo macchina indicando all’operatore quali sono le priorità di lavorazione. Il vantaggio è quindi l’assenza totale di errori dovuti a passaggi di informazioni non corrette, tempi morti e ritardi dovuti a emergenze dell’ultimo minuto.
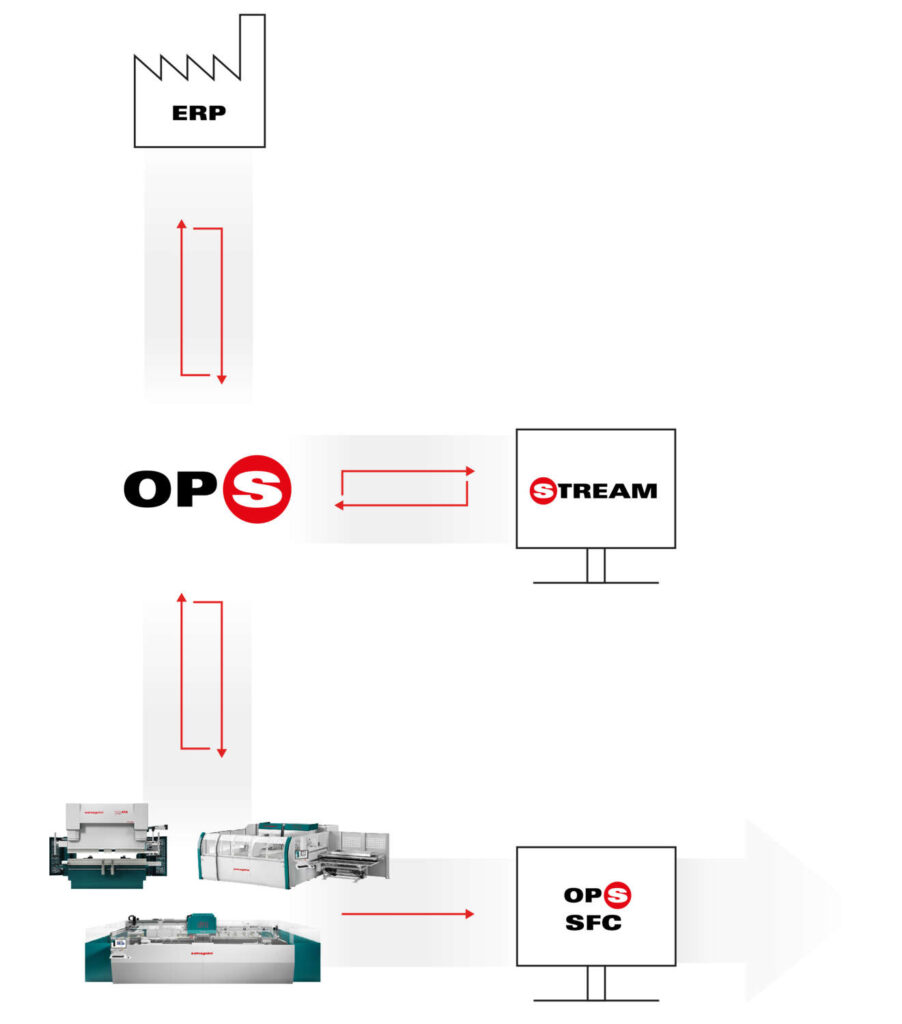
OPS, infatti, informa in tempo reale sul sopraggiungere di eventuali cambiamenti di produzione, cosicché l’operatore sia sempre aggiornato e possa intervenire per tempo evitando disagi e fermi macchina prolungati e garantendo la reattività necessaria a un ambiente di produzione moderno.
In più, ogni attività di produzione viene tracciata in real-time e inviata al gestionale, che mette così a disposizione del responsabile di produzione una fotografia istantanea del flusso di lavoro. Il livello di integrazione garantito da OPS permette maggior dinamicità, efficienza e reattività: le figure incaricate di gestire l’avanzamento del flusso produttivo, tipicamente programmatori e operatori di macchina, vengono costantemente guidate, anche nelle operazioni meno scontate.
Ultimo, ma solo in termini di posizionamento lungo la catena produttiva, è il modulo OPS SFC (Shop Floor Control), che dà supporto all’operatore nella fase di post-produzione: specificamente dedicato alla tracciabilità, questo modulo assiste l’operatore quando il pezzo è in uscita dalla macchina fornendo tutti i dettagli sulla sua provenienza e sulla sua destinazione successiva.
Grazie a OPS SFC ciascun operatore è in grado di conoscere “la storia” di ciascun singolo pezzo, riducendo il rischio di perdere singole parti o interi lotti produttivi.
La trasformazione digitale per tutti
Il tema della Digital Transformation è oggi la chiave dell’innovazione aziendale, ma non tutte le realtà si sentono pronte ad abbracciare un percorso di digitalizzazione completo. Ecco perché OPS, pensato come soluzione modulare e totalmente flessibile, si adatta ai diversi livelli di predisposizione digitale.
Può essere installato in versione entry level o arrivare ad un livello di integrazione completa, in piena ottica Industria 4.0. La configurazione di OPS può variare nel tempo, per adattarsi alle specifiche esigenze e per crescere al ritmo delle competenze digitali aziendali. Con questa soluzione, adattabile a tutte le diverse realtà, Salvagnini intende anche intercettare quella spinta – spesso generazionale – di chi individua negli aspetti gestionali un asset di sviluppo sempre più determinante per permettere alle aziende di compiere un salto di qualità.
Un’arma a supporto della lean manufacturing
In un’epoca in cui il mercato è ormai stabilmente soggetto a sensibili variazioni e l’eccezionalità rappresenta la nuova normalità sia per le grandi sia per le piccole aziende (sempre più evidente, ad esempio, nelle difficoltà di reperimento materiali, chip shortage, costo materie prime, costi dell’energia, ecc.) operare in “ottica Lean” non può più essere capacità esclusiva delle realtà più virtuose ma è diventato una condizione necessaria per restare competitivi, agendo direttamente sul time-to-market.
Ecco perciò che la suite OPS si inserisce perfettamente in questa nuova fase, affermandosi come lo strumento ideale per agevolare gli operatori ad acquisire e a rendere routinarie quell’insieme di buone pratiche finalizzate a un unico obiettivo: la produzione efficiente.
di Alessandro Ariu