L’ottimizzazione della produttività dei centri di lavoro dipende anche dalla giusta selezione e dalla corretta installazione dei cuscinetti. Timken propone otto fattori per massimizzare la produttività.
La definizione di produttività indica quanto una azienda sia efficiente nel convertire gli input in utili output. Quando si tratta di lavorazioni meccaniche, il modo migliore per ottenere ciò, nelle operazioni di rimozione del metallo, è ridurre il tempo di ciclo ed eliminare i tempi non programmati di inattività, nonché gli scarti di produzione.
Come ottenere più prodotti a un costo unitario inferiore e aumenterete i profitti?
Nella prima parte di questo articolo pubblicato sul numero di Maggio di Organi di Trasmissione (N.d.R.), si è discusso di come la selezione della giusta configurazione di cuscinetti per un mandrino di un centro di lavoro CNC possa ottimizzarne le prestazioni. La scorretta installazione, o la scelta del design e della configurazione errati, possono aumentare in maniera significativa il tempo di ciclo e potrebbero perfino causare l’arresto della macchina.
Come follow-up, questo articolo spiegherà passo-passo otto fattori critici che possono essere ottimizzati per massimizzare la produttività di lavorazione.
Otto fattori per massimizzare la produttività di lavorazione
1. Ciclo di lavoro
Sia che siate progettisti di mandrini per macchine utensili presso un costruttore di primo equipaggiamento o un’officina di manutenzione, riparazione e revisione, le esigenze dell’applicazione finale sono d’importanza cruciale quando si seleziona un cuscinetto.
La selezione del cuscinetto inizia con la definizione del ciclo di lavoro per la macchina CNC durante la produzione. Il ciclo di lavorazione include tutte le operazioni di fresatura, foratura, alesatura, maschiatura e tutte le altre attività nel ciclo della macchina, nessuna esclusa. Il tempo di ciclo si riferisce al tempo necessario per eseguire tali operazioni.
Come osservato in precedenza, un ciclo di lavoro può includere un’ampia gamma di operazioni, dalla sgrossatura (carichi elevati, velocità ridotte) alla finitura (velocità elevate, carichi ridotti) e tutto ciò che si trova nel mezzo. Anche se un centro di lavoro CNC è dotato di cuscinetti per mandrini ottimizzati per un determinato ciclo di lavoro al momento dell’acquisto, non vi è alcuna garanzia che gli stessi possano essere altrettanto ottimizzati per essere utilizzati in cicli di lavoro futuri. In molti oggi sostituiscono le linee di transfer con centri di lavoro CNC flessibili, a causa dei volumi più ridotti e delle più frequenti necessità di cambio tipo dei prodotti. Tuttavia, questo cambiamento spesso avviene modificando i cicli di lavoro.
2. Carichi e velocità dell’utensile
È importante conoscere, o stimare con una certa precisione, i carichi e le velocità dell’utensile, poiché diversi design e configurazioni di cuscinetti varieranno in termini di calore e stress generato in ciascuna condizione del ciclo di lavoro, le quali incidono direttamente sulla durata dei cuscinetti e sulla temperatura d’esercizio del mandrino.
Una volta definito il ciclo di lavoro, devono essere determinati i carichi e le velocità dell’utensile per ciascuna operazione. L’operazione di taglio e il materiale da lavorare determinano il tipo di utensile, la geometria, la profondità e la larghezza dell’asportazione, nonché la velocità di avanzamento. I carichi e le velocità dell’utensile dipendono dal fatto che la macchina stia effettuando un’operazione di sgrossatura o finitura. Il materiale del pezzo lavorato (sia che si tratti di acciaio, alluminio, titanio, nichel o altro) e la sua durezza incidono sui carichi e sulla velocità dello strumento.
Il metodo più affidabile e preciso per determinare i carichi e le velocità dell’utensile è interpretare i dati di processo delle operazioni effettive di taglio. Se vengono indicati la potenza effettiva del motore, la velocità del mandrino e il diametro dell’utensile, il carico di taglio può essere ottenuto impostando la potenza di taglio (forza dell’utensile x diametro dello stesso x velocità) pari alla potenza effettiva del motore e ottenendo la forza dell’utensile. Tuttavia, ciò vale solo se l’operazione di taglio e il materiale/la durezza del pezzo lavorato sono uguali. La raccolta di questi dati di processo nel corso del tempo è un investimento molto prezioso e può contribuire a eliminare le supposizioni derivanti dalla determinazione di carichi e velocità dell’utensile.
Un approccio analitico può contribuire a verificare i dati di processo raccolti. Molti fornitori di utensili possono calcolare i relativi carichi e le velocità e forniranno assistenza nella scelta dell’utensile. Un metodo analitico alternativo per calcolare i carichi sull’utensile è quello di fare riferimento a un manuale sulle macchine utensili. Tra i tanti a disposizione, si segnala il “Technology of Machine Tools, 7th Edition”, di Steve Krar, Arthur Gill e Peter Smid. Le formule di calcolo presenti nel libro richiedono che l’utente inserisca la geometria dell’utensile, i parametri di taglio, i fattori di usura e altri elementi. L’utilizzo di queste formule richiede un buon livello di esperienza; in genere, il fornitore degli utensili avrà l’esperienza e le informazioni sulla geometria degli utensili necessarie per eseguire i calcoli ed ottenere così risultati ragionevolmente precisi.
Se nessuno degli input è noto e non vi sono dati di processo disponibili, i carichi di taglio possono essere stimati sulla base della capacità statica del cuscinetto. I carichi di taglio in genere variano tra il 5 % (finitura) e il 25 % (sgrossatura) della capacità statica del cuscinetto; le velocità variano tra il 10 % (sgrossatura) e il 90 % (finitura) della velocità del mandrino con potenza nominale massima. I valori possono essere mischiati e abbinati sulla base dell’operazione di taglio. Tuttavia, si tratta di stime molto approssimative che devono essere usate solo per una selezione iniziale dei cuscinetti.
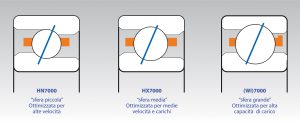
3. Design e configurazione dei cuscinetti
A livello commerciale, esistono sul mercato diversi cuscinetti a sfere a contatto obliquo per alte velocità/elevata precisione, disponibili in numerose serie dimensionali ISO. Nei mandrini delle macchine utensili, le serie 19 e 10 sono i più comuni.
The Timken Company offre tre diversi design di cuscinetto per la serie dimensionale 10 ISO: con sfere piccole HN7000 (serie HN), con sfere medie HX7000 (serie HX) e con sfere grandi 7000 (serie WI), mostrate nella figura 1.
Ogni design di cuscinetto ha dimensioni, numero di sfere e curvature delle piste chiaramente differenti che determinano la capacità, il limite di velocità e la rigidità del cuscinetto. In genere, il design del cuscinetto viene selezionato sulla base del tipo di taglio previsto: sgrossatura, finitura o polivalente (figura 2). Questo è solo il punto d’inizio; deve essere eseguita l’analisi per convalidare la selezione.
Il design del cuscinetto determina la dimensione della sfera, il numero di sfere e la curvatura della pista, mentre la configurazione del cuscinetto viene determinata dal materiale della sfera (acciaio/ceramica), dall’angolo di contatto (15° o 25°) e dal livello di precarico (ultraleggero, leggero, medio e pesante). Questa configurazione di cuscinetto definisce la capacità, il limite di velocità e la rigidità, ed è selezionata per ottimizzare le prestazioni sulla base delle velocità e dei carichi. Mentre il design del cuscinetto viene selezionato a seconda del tipo di taglio previsto, la configurazione si basa sul ciclo di lavoro. Il miglior modo per ottimizzare la configurazione è modellare il mandrino analiticamente.
Timken si serve di un software proprio per modellare con precisione il gruppo cuscinetti/albero con carichi, velocità e condizioni operative. Con questo modello di calcolo si ottengono i valori di stress da contatto tra le sfere e la pista, considerando il precarico iniziale, i carichi esterni e la forza centrifuga delle sfere causata dalla velocità orbitale.
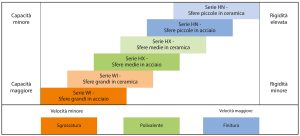
L’ottimizzazione può essere raggiunta modulando i diversi parametri di configurazione per ridurre al minimo la quantità di calore generato nell’applicazione. Il calore viene generato principalmente a causa dello strisciamento delle sfere lungo la pista che avviene prevalentemente in condizione di cuscinetto scarico. Il precarico ha l’impatto maggiore sulla generazione del calore e questo parametro in genere viene usato per ridurre al minimo strisciamento e slittamento. Il precarico è vincolato dal conseguente stress da contatto tra la sfera e la pista. In genere, il limite massimo accettabile è inferiore alla metà dello stress specifico richiesto per la deformazione plastica della pista di rotolamento.
Anche il materiale della sfera e l’angolo di contatto incidono sulla generazione di calore, ma hanno un impatto inferiore rispetto al precarico. Questi fattori in genere sono usati per perfezionare la configurazione sulla base del tipo di carico (assiale verso radiale) e dei requisiti di velocità. Ad esempio: se i carichi assiali sono dominanti nel ciclo di lavoro, allora sarà selezionato un angolo di contatto di 25°. Se i requisiti di velocità superano la classificazione per una sfera in acciaio, allora è necessario passare alla ceramica.
La possibilità di eseguire l’analisi sui carichi, sulle velocità e sulle condizioni ambientali elimina le incertezze relative alla selezione di un cuscinetto ideale per ottimizzare le prestazioni del mandrino.
4. Montaggio corretto
Dopo aver selezionato design e configurazione del cuscinetto, è importante che questo venga montato correttamente per ottenere le prestazioni desiderate. Le dimensioni delle sedi dell’albero e dell’alloggiamento e la loro forma geometrica sono fondamentali. Il precarico può cambiare radicalmente se i valori di accoppiamento raccomandati non rientrano nei limiti consigliati; è quindi importante che siano ottenuti gli accoppiamenti corretti in modo che il precarico venga applicato correttamente.
5. Accoppiamenti con alberi e alloggiamenti
Gli accoppiamenti fra albero per mandrini e cuscinetti sono progettati per operare a velocità pari o inferiori a 750.000 dN (dN = alesaggio in mm x velocità in giri/min) e richiedono il rispetto degli accoppiamenti indicati a catalogo (da leggermente libero a leggermente forzato, zero/zero nominale). Le facce del cuscinetto sono bloccate assialmente, e l’accoppiamento su alloggiamento è libero. Se il cuscinetto è nella posizione flottante nell’alloggiamento, l’accoppiamento deve risultare extra libero.
I cuscinetti per mandrini concepiti per operare sopra i 750.000 dN richiedono un accoppiamento forzato e l’entità dell’interferenza dipende dalla dimensione del cuscinetto, dalla velocità e dall’alesaggio dell’albero. Ciò è dovuto agli effetti della forza centrifuga che causa una crescita elastica, in direzione radiale, dell’anello interno e dell’albero. Se un cuscinetto che opera a queste velocità viene installato usando l’accoppiamento incerto raccomandato nel catalogo, allora tale accoppiamento diventerà libero alla velocità di progetto, con il rischio di maggiori errori di eccentricità e di rotazione relativa dell’anello interno sull’albero.
Timken offre ai clienti uno strumento per calcolare l’accoppiamento, in base alla velocità e il corrispondente offset del distanziale, per la sua linea di cuscinetti a sfere a contatto obliquo ad alta precisione; si tratta del Programma di selezione dei cuscinetti di precisione Timken (Timken Precision Bearing Selector, TPBS) che può essere scaricato dal sito di Timken. Il TPBS fornisce, inoltre, tutti gli accoppiamenti a catalogo, le rigidità dei cuscinetti e molto altro. Gli accoppiamenti degli alloggiamenti non cambiano in base alla velocità dell’albero.
6. Codice micron
I codici micron vengono forniti per tutti i cuscinetti in classe PS4 di Timken e indicano lo scostamento in negativo dell’alesaggio del cuscinetto rispetto al nominale (a catalogo) e lo stesso per il diametro esterno DE di un cuscinetto; tale valore viene espresso in micron (µm). Ciò consente ai tecnici di determinare l’esatto alesaggio e DE con un errore di +/- 1 µm e di eseguire una rettifica finale dell’alloggiamento del cuscinetto per ottenere un accoppiamento specifico con un’approssimazione di un micron.
I codici micron vengono anche usati per abbinare singoli cuscinetti a set di due o più. Idealmente, gli operatori potrebbero desiderare una serie con gli stessi codici micron per alesaggi e DE. Dal momento che questo non è possibile da un punto di vista della produzione, è consentita una tolleranza minima quando si creano le serie. Le tolleranze corrispondenti alle serie dipendono dall’alesaggio e dalla dimensione del DE. Maggiore è l’alesaggio o il DE, maggiore sarà il gruppo di codici micron consentito per la creazione della serie.
7. Dimensionamento geometrico e tolleranza
Progettazione e lavorazione ottimali sono di fondamentale importanza. Il rigoroso controllo degli accoppiamenti del cuscinetto rappresenta solo metà dell’opera: anche la forma geometrica dell’albero e dell’alloggiamento devono avere una tolleranza ridotta. A seconda della dimensione dell’alesaggio e del DE, la tolleranza è compresa tra 1 e 8 µm (in genere tra 2 e 4 µm). Questa precisione nella geometria va oltre l’alloggiamento del cuscinetto, nel senso che vale per tutti i componenti che sono adiacenti ai cuscinetti, come ghiere di bloccaggio, distanziali e coperchi finali.
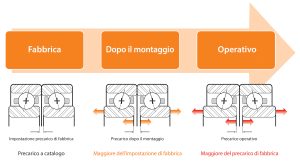
8. Dal precarico originale (dalla fabbrica) a quello operativo
Il precarico a catalogo del cuscinetto è direttamente ottenuto in fabbrica, ma cambia quando il set di cuscinetti viene installato sull’albero con un accoppiamento forzato. Quando l’anello interno viene pressato sull’albero, il diametro della pista aumenta a sua volta, causando lo scostamento verso l’esterno della faccia del cuscinetto dopo l’installazione; l’entità dello scostamento andrà ad aggiungersi al precarico di fabbrica (figura 3). Questo viene definito “telescoping”.
Inoltre, quando i cuscinetti sono in funzione ed è presente una differenza di temperatura tra gli anelli interni ed esterni, i parametri dimensionali (ovvero il precarico) aumentano ulteriormente. Se un mandrino sta per raggiungere prestazioni ottimali durante il funzionamento, il precarico dopo l’installazione deve prendere in considerazione le temperature operative.
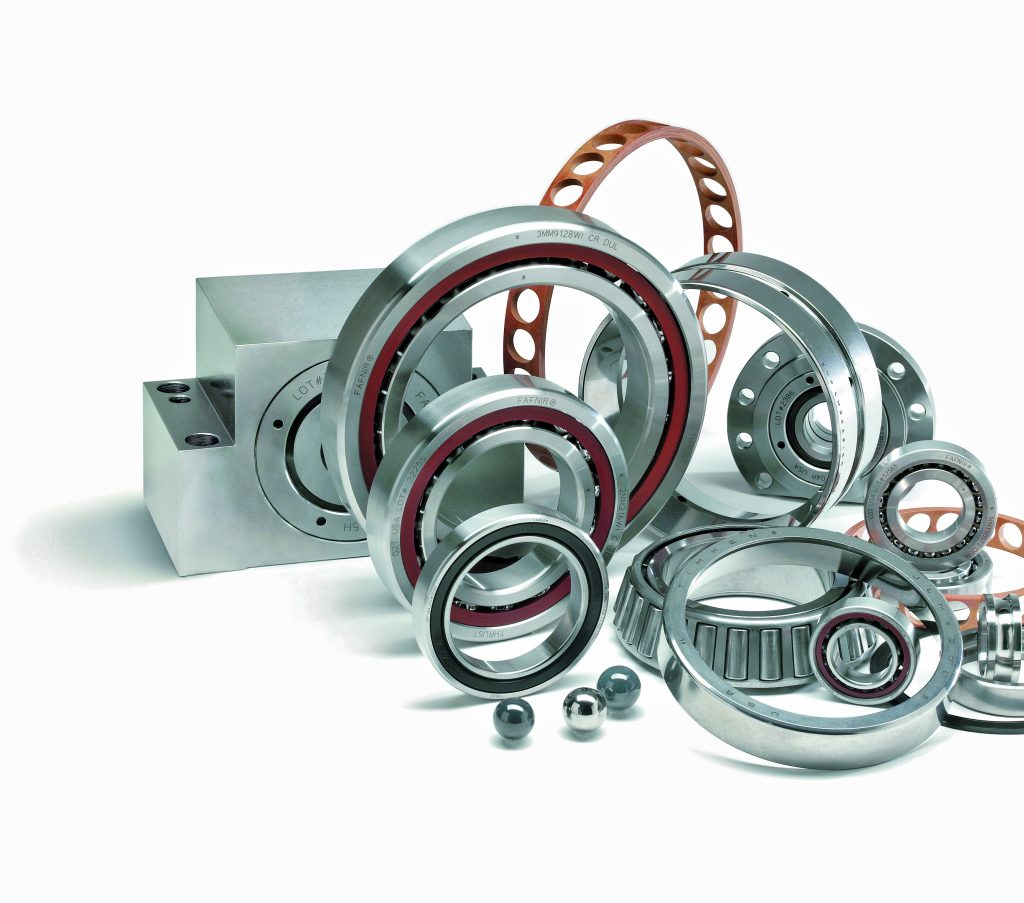
Per una produttività ottimizzata, il design del cuscinetto deve essere selezionato sulla base delle operazioni di fresatura previste, mentre la configurazione può essere ottimizzata modellando il ciclo di lavoro con l’obiettivo di ridurre il calore dovuto allo scorrimento e allo slittamento delle sfere. Inoltre, i cuscinetti devono essere installati correttamente sull’albero e nell’alloggiamento, con le sedi del cuscinetto che soddisfino le rigorose tolleranze dimensionali geometriche e gli accoppiamenti specifici usando i codici micron.
Seguendo questi otto fattori per massimizzare la produttività, è possibile garantire che i cuscinetti per mandrini possano operare come previsto; tali prassi aiutano gli operatori di macchine utensili a far funzionare i loro centri di lavoro CNC secondo quanto ci si aspetti.
(Eric Faust, Application Engineering Specialist, The Timken Company)