Gli autori del paper propongono l’idea di utilizzare un innovativo processo di formatura ibrida in grado di creare complessi componenti multi-materiale. La soluzione proposta si ispira alla formatura idromeccanica: in questo processo la lamiera è trasformata dalla pressione idrostatica applicata tramite acqua o olio. L’idea è quella di utilizzare il materiale composito, riscaldato alla giusta temperatura, come mezzo per deformare la lamiera.
La manifattura della lamiera presenta un’ottima diffusione sul territorio nazionale, questo poiché è spesso alla base di molti prodotti anche di uso quotidiano.
Questa industria, specialmente negli ultimi anni, sta subendo una rapida evoluzione, grazie all’introduzione di nuovi processi e materiali più efficienti e avanzati. Con l’aumento della domanda di materiali leggeri, resistenti e a basso impatto ambientale, il settore della lamiera sta adottando sempre più frequentemente materiali compositi come alluminio insieme a fibre di vetro o di carbonio.
Per poter lavorare al meglio nuovi materiali, è però necessario sviluppare e ottimizzare processi dedicati. Le nuove tecnologie produttive unite ai nuovi materiali permettono di offrire interessanti sinergie in grado di aprire nuove opportunità per l’industria. I nuovi processi permettono infatti di ottenere forme e geometrie più complesse e accurate, una maggiore precisione e ridurre lo scarto di materiale.
L’obiettivo comune per produttori e clienti è quello di ottenere prodotti più avanzati, in grado di ridurre pesi ed impatti ambientali, pur offrendo le adeguate performance.
Componenti multi-materiale
La produzione di componenti leggeri sta diventando sempre più interessante, soprattutto nel settore dei trasporti, al fine di ridurre i consumi di carburante. Per raggiungere questi obiettivi, pur mantenendo attenzione al fattore economico, vengono spesso utilizzati progetti multimateriale. Lamiere di acciaio o alluminio insieme a materiali plastici e compositi offrono interessanti prestazioni.
Questi materiali, chiamati anche “ibridi”, offrono un’elevata rigidità e resistenza, soprattutto se vengono impiegate fibre di rinforzo lunghe (sopra i 10 mm). In ambito automotive esistono alcuni componenti “fail-safe”, ovvero critici per la sicurezza degli utilizzatori.
In questo caso, oltre alle tradizionali performance meccaniche, i componenti devono essere in grado di deformarsi, ad esempio in seguito ad un impatto, senza però rompersi. Così da permettere al guidatore di riconoscere l’anomalia e di fermarsi senza pericolo. I materiali compositi, da soli, non sono in grado di assolvere a questi requisiti. Tuttavia, un materiale ibrido metallo-composito è in grado di coniugare i vantaggi dei due mondi: offrendo resistenza strutturale, riduzione dei pesi e sicurezza.
Processo produttivo
Tradizionalmente, per produrre componenti multi-materiale, si hanno due opzioni. La prima possibilità (chiamata “post molding assembly” o PMA) è quella di assemblare i componenti di lamiera e composito, prodotti separatamente, in un terzo step. Questa soluzione presenta potenziali problemi di tolleranza e maggiori costi produttivi. L’alternativa classica (chiamata “in-mold assembly” o IMA) è quella di utilizzare la lamiera preformata come stampo per il materiale composito eliminando una fase del processo.
Tale alternativa riduce tempi e costi del processo, ma viene solitamente utilizzata per componenti semplici. Per sopperire ai limiti offerti dai processi tradizionali, gli autori del paper propongono l’idea di utilizzare un innovativo processo di formatura ibrida in grado di creare complessi componenti multi-materiale.
La soluzione proposta si ispira alla formatura idromeccanica: in questo processo la lamiera è trasformata dalla pressione idrostatica applicata tramite acqua o olio. L’idea è quella di utilizzare il materiale composito, riscaldato alla giusta temperatura, come mezzo per deformare la lamiera. Il processo completo (Figura 1) permette di unificare diverse fasi del processo e richiede semplicemente una pressa idraulica come macchinario produttivo.
Questo processo può infatti essere applicato in officine di lavorazione della lamiera con investimenti ridotti. Il materiale composito a fibra lunga può essere prodotto internamente o acquistato già pronto all’uso.
Valutazione del processo
Per validare la soluzione gli autori hanno applicato la proposta valutandola su diversi casi di studio. Sono stati progettati stampi sia per geometrie concave che per profili ad U con diversi parametri di profondità, raggi e terminazioni (Figura 2). La valutazione ha incluso anche parametri qualitativi al fine, ad esempio, di ridurre le grinze sui componenti finali.
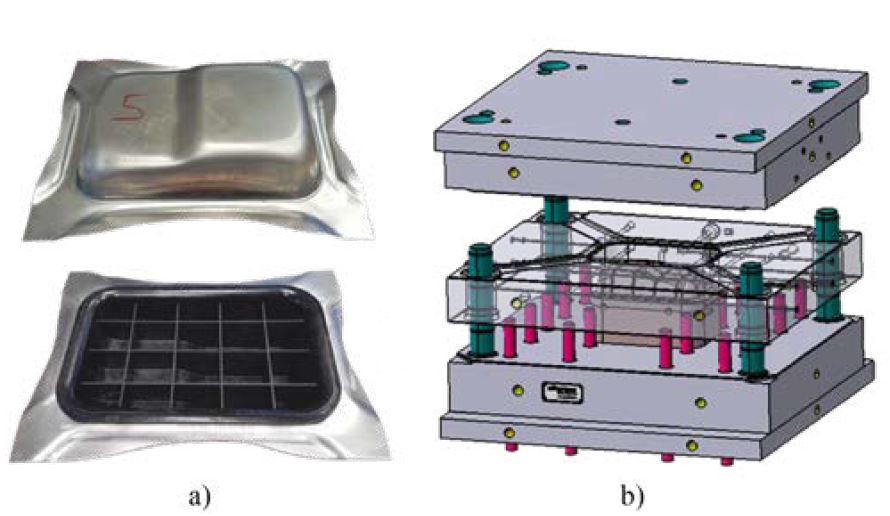
I parametri di processo quali temperatura, forza del premilamiera e del punzone sono stati ottimizzati nelle varie fasi della trasformazione. Diversi acciai sono stati impiegati in questo processo di formatura ibrida insieme a un composito a fibra lunga (fino a 25 mm) con matrice in nylon. I risultati in generale sono molto promettenti dato che la qualità di unione tra i due materiali è ottima.
Caso studio
Una volta terminata la fase più sperimentale di valutazione ed ottimizzazione del processo, gli autori decidono di applicare il processo proposto su un caso di studio industriale più realistico. Il componente in questione è il braccio longitudinale della sospensione posteriore multilink di un’automobile compatta (VW Golf 7 su piattaforma MQB). Per dimostrare le potenzialità del design ibrido il componente, tradizionalmente prodotto in acciaio, è stato ridisegnato per un multi-materiale di acciaio e composito.
Il componente originale è prodotto in acciaio ad alta resistenza SZBS 800 con lo spessore di 3.5 mm, quindi ridurre il peso è una sfida molto ambiziosa. Per procedere all’ottimizzazione del componente sono stati studiati tutti i possibili carichi usando un software FEM. Il limite di spessore della lamiera nel nuovo componente ibrido è stato fissato a 2 mm. Questa scelta è una pratica comune tra i produttori europei per garantire la sicurezza anche in caso di corrosione.
Per ottenere un design ottimizzato del componente alternativo è stata impiegata un’ottimizzazione topologica. Questa tecnica permette di ottenere un design ottimizzato per sopportare i carichi definiti dall’utente. Il risultato (Figura 3) è composto da una lamiera di acciaio da 2 mm e da uno strato di composito a fibra lunga dello spessore di 2 mm con nervature e rinforzi locali ottimizzati. Il peso di questo componente è di circa 1,2 kg ed è inferiore, rispetto all’originale, di oltre il 20%.
Per approfondire lo studio del componente sono stati impiegati, anche in questo caso, diversi materiali per quanto riguarda la lamiera. I prodotti sono poi stati scansionati in 3D e confrontati con il modello CAD desiderato. In generale si può notare che, aumentando la resistenza del materiale alcuni dettagli geometrici come, ad esempio, alcuni raggi acuti diventano meno precisi. Anche il ritorno elastico è tendenzialmente superiore per acciai più resistenti rispetto all’alluminio. Dagli autori sono state condotte anche analisi per quanto riguarda il materiale composito che mostrano l’importanza di progettare stampi appositi a seconda della combinazione di materiali scelta.
La richiesta di componenti leggeri è in continua crescita in questi ultimi anni. Per assolvere a questi compiti l’approccio multi-materiale diventa spesso interessante se non obbligatorio. La diffusione industriale di queste nuove soluzioni richiede però la diffusione di processi produttivi efficienti ed economici. Per questo gli autori propongono il processo di formatura ibrida, in grado di unire diverse fasi e lavorare con compositi a fibra lunga.

Questa soluzione appare funzionale con diverse combinazioni di materiali, anche per lamiere ad alta resistenza, definendo i corretti parametri di processo. I componenti così prodotti offrono performance valide come mostrato dai casi di studio. Inoltre tale innovativo processo può essere introdotto industrialmente con investimenti ridotti, risultando quindi una soluzione interessante per il mondo industriale di domani.
Fonte: Fang, X. F., Kloska, T., & Heidrich, D. (2022). Hybrid forming – a method for simultaneous forming of high strength metal sheet and long fiber reinforced plastic. Key Engineering Materials, 926, 700–709. https://doi.org/10.4028/p-s9255e