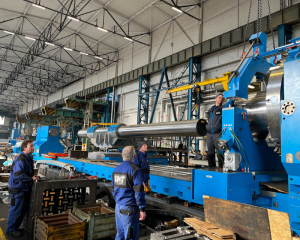
Home » Tornitura dei metalli: la nostra guida
Condividi
La tornitura è una lavorazione per asportazione truciolo nel quale il pezzo viene fissato ad un mandrino e posto in rotazione mentre l’utensile da taglio si muove lungo il pezzo dandogli la forma desiderata.
Sovente nella tornitura dei metalli la lavorazione avviene in due passaggi: nel primo, definito sgrossatura, si rimuove il grosso del sovrametallo tramite utensili in grado di resistere a forti sollecitazioni; nella seconda fase, definita finitura, il pezzo viene lavorato al fine di ottenere una superficie finale con dimensioni, tolleranze e rugosità previste.
La tornitura viene utilizzata principalmente per realizzare pezzi ascrivibili a solidi di rivoluzione che possono presentare varie caratteristiche quali fori filetti scanalature vari gradini di diametro conicità superfici sagomate.
Si tratta di una delle macchine utensili più antiche. Per quanto concerne la lavorazione dei metalli si impiegano torni di varie tipologie: torni orizzontali, torni verticali, torni a controllo numerico, centri di lavoro, torni plurimandrino ecc. Tutte queste macchine sono tuttavia accomunate da alcune caratteristiche: il pezzo da lavorare viene fissato ad un mandrino autocentrante il cui moto rotatorio è permesso da un motore elettrico; dall’altro lato della macchina è installata la torretta portautensili che può montare vari tipi di utensili di tornitura quali sgrossatori, finitori, troncatori o filettatori.
In molti casi dal medesimo lato del portautensili è presente un sostegno da contropunta la cui funzione è sorreggere il pezzo.
Quando è necessario lavorare pezzi lunghi e sottili che nel corso della lavorazione possono flettersi e di conseguenza compromettere la buona riuscita della tornitura vengono impiegati dei supporti, chiamati lunette, che sorreggono il pezzo limitandone le vibrazioni.
Tornio parallelo o universale: è il tipo più comune di tornio e viene utilizzato per lavorazioni generali di tornitura su pezzi cilindrici. Ha una disposizione semplice con un supporto fisso e un supporto mobile che sostiene il pezzo.
Tornio a fantina mobile: conosciuti anche come “torni svizzeri”, i torni a fantina mobile sono macchine specializzate nelle quali una boccola mobile si sposta lungo l’asse orizzontale, trainando il pezzo di lavoro nell’area di lavoro. Qui, una serie di utensili montati su un portautensili lineare, chiamato “pettine”, lavora il pezzo. Questi torni sono particolarmente adatti per la lavorazione di piccoli pezzi ad alta precisione, come le minuterie metalliche, con diametri generalmente compresi tra 32 e 40 mm.
Tornio a controllo numerico (CNC): questo tipo di tornio è controllato da un computer tramite un software CNC. Offre maggiore precisione e ripetibilità rispetto ai torni tradizionali e consente la produzione di pezzi complessi con geometrie precise.
Tornio per tornitura verticale: in un tornio verticale, il pezzo viene montato verticalmente anziché orizzontalmente. Questo tipo di tornio è particolarmente utile per pezzi di grandi dimensioni che non possono essere facilmente lavorati su un tornio orizzontale.
Tornio per tornitura automatica o a CNC multitasking: questo tipo di tornio è in grado di eseguire più operazioni di lavorazione, come tornitura, fresatura, foratura e filettatura, tutto in una singola macchina. Questo riduce i tempi di attrezzaggio e aumenta l’efficienza della produzione.
Tornio revolver: un tornio revolver è progettato per lavorazioni ad alta produttività. Ha più supporti utensili che possono essere rapidamente selezionati e utilizzati senza dover interrompere il processo di lavorazione.
Tornio per tornitura di precisione: questo tipo di tornio è progettato per lavorazioni che richiedono tolleranze molto strette e finiture superficiali precise. Solitamente hanno caratteristiche di alta precisione e strumenti specializzati per garantire risultati accurati.
Tornio per tornitura ad alta velocità (HST): i torni HST sono progettati per lavorazioni che richiedono velocità elevate e tempi di ciclo rapidi. Sono dotati di caratteristiche come mandrini ad alta velocità e avanzamenti rapidi per massimizzare la produttività. conosciuti anche come “torni svizzeri”, sono macchine specializzate nelle quali una boccola mobile si sposta lungo l’asse orizzontale, trainando il pezzo di lavoro nell’area di lavoro.
Le operazioni eseguibile tramite tornitura possono classificarsi in interne od esterne a seconda che l’utensile lavori la superficie del pezzo o lo scavi assialmente.
Tornitura: Un’utensile da tornitura si muove assialmente e radialmente lungo il pezzo in lavorazione. In tal modo rimuove il materiale per formare diverse caratteristiche quali: coni, smussi o “gradini”. Tipicamente viene applicata una piccola profondità di taglio radiale e vengono effettuate passate multiple.
Sfacciatura: l’utensile si sposta radialmente lungo l’estremità del pezzo rimuovendo un sottile strato di materiale al fine di ottenere una superficie liscia e piana.
Scanalatura: L’utensile si sposta radialmente sul lato del pezzo incidendo i solchi della scanalatura. Possono essere utilizzate passate multiple per realizzare solchi di diverse geometrie o scanalature più profonde.
Troncatura: L’utensile da taglio si sposta radialmente, analogamente a quanto accade per la scanalatura ma, raggiungendo il centro del pezzo, lo taglia separandone una sezione.
Filettatura: l’utensile filettatore si muove sulla superficie del pezzo, filettando il pezzo in rotazione.
Foratura: la punta penetra nel pezzo in lavorazione producendo un foro; contrariamente alla foratura tradizionale effettuata mediante il trapano, nella foratura assiale sul tornio la punta resta ferma, il moto rotatorio viene invece impresso al pezzo in lavorazione.
Alesatura e Barenatura: tramite la tornitura è possibile eseguire anche operazioni di rifinitura di fori; a differenza dei metodi tradizionali di alesatura e barenatura dove vengono impiegate macchine utensili quali il trapano o la fresatrice, quando eseguite sul tornio il moto rotatorio è impresso al pezzo da alesare/barenare mentre l’utensile resta fermo.
Maschiatura: il maschio entra assialmente nel pezzo in lavorazione tramite un foro preesistente asportando il materiale necessario per realizzare la filettatura interna.
Nella tornitura per ottenere la lavorazione desiderata è necessario impostare parametri che variano in funzione del metallo da lavorare, del materiale e dimensione dell’utensile impiegato ecc.
Tra i principali parametri da calcolare:
Nella tornitura verticale, il tornio è ruotato di 90° e si sviluppa in modo tale da orientare il mandrino verticalmente. Questo tipo di lavorazione è particolarmente indicata quando le dimensioni dell’oggetto ne renderebbero difficoltosa l’installazione in orizzontale e consente pertanto di realizzare componenti di grandi dimensioni che possono trovare impiego ad esempio nel settore navale o ferroviario.
In taluni casi la tornitura verticale può effettuarsi anche con mandrino sospeso orientato verso il basso (tornitura verticale pick-up); questa tecnica viene impiegata per realizzare pezzi rotondi in grande quantità e di apprezzabile qualità. In questa tipologia di lavorazione verticale solitamente il mandrino si occupa sia della lavorazione sia del caricamento del pezzo.
Nella tornitura CNC, acronimo di Computer Numerical Control, la lavorazione avviene come in un normale tornio ma il processo è interamente automatizzato e controllato da un computer.
Nella tornitura a controllo numerico l’operatore si limita ad inserire i dati di progetto nel programma e interviene solo nel caso di guasti. La lavorazione inoltre viene costantemente monitorata da sensori; in tal modo sono possibili tolleranze di centesimi o anche millesimi di millimetro.
Per riassumere, i principali vantaggi della tornitura CNC sono l’elevata precisione e ripetibilità del processo che lo rendono ideale per le lavorazioni di precisione o per le produzioni di serie; altro importante vantaggio è l’automazione della lavorazione che permette di ridurre il carico di lavoro per l’operatore e ridurre così errore umano e costo di manodopera.
Nella lavorazione plurimandrino, la testa, generalmente ad asse orizzontale, alloggia più mandrini portapezzo (fino a 12). Tali mandrini possono ruotare anche a velocità diverse permettendo la lavorazione contemporanea di più pezzi incidendo significativamente sulla velocità di lavorazione.
La tornitura plurimandrino permette infatti di utilizzare il medesimo utensile tagliente su più prodotti, prima di cambiarlo per passare ad una successiva fase di lavorazione, in tal modo i fermi macchina dovuti al cambio utensile vengono sostanzialmente ridotti. Altro importante vantaggio riguarda la possibilità di ridurre il controllo dell’operatore umano incidendo così anche sui costi di manodopera.
La tornitura monomandrino è una tecnica di lavorazione dei metalli che coinvolge l’uso di un tornio con un unico mandrino. Il mandrino è la parte rotante che tiene saldamente il pezzo di lavoro mentre viene lavorato. In pratica, significa che la macchina può lavorare solo su un pezzo alla volta. Questo tipo di tornitura è comunemente utilizzato per operazioni di base come la tornitura cilindrica e la tornitura facciale. Sebbene possa sembrare limitata rispetto a torni con più mandrini, la tornitura monomandrino è ancora ampiamente utilizzata in molte applicazioni industriali, specialmente per la produzione di pezzi a singola lavorazione o in piccole quantità.
Nella tornitura statica, contrariamente ai metodi fino a qui presentati, il pezzo da lavorare viene mantenuto fermo mentre il movimento è impresso all’utensile, il quale si muove intorno al pezzo grazie all’interpolazione degli assi di lavoro longitudinale e radiale e alla rotazione della testa stessa. Solitamente la tornitura statica viene impiegata per la lavorazione di tubi di grandi dimensioni che comportano pesi ed ingombri piuttosto rilevanti e difficili da gestire; impiegando questo metodo di lavorazione gli aspetti cinematici e dinamici della macchina vengono concentrati sulla testa di lavorazione semplificandone la gestione.
La produzione di minuterie metalliche di precisione rappresenta un aspetto cruciale nell’industria meccanica, dove pezzi di dimensioni ridotte come viti, piccoli alberi motore, componenti idraulici e impianti dentali richiedono estrema precisione.
La tecnologia di tornitura svolge un ruolo chiave in questo contesto, e tra le varie metodologie, la tornitura da barra si distingue per la sua efficacia nella lavorazione di lotti di pezzi simili. Questo approccio ottimizza la fase di caricamento del materiale poiché non richiede il caricamento individuale di ciascun pezzo grezzo; invece, il materiale è alimentato in modo continuo da una barra metallica.
Alla fine del processo, il pezzo viene separato dalla barra tramite un troncatore, un processo noto come decolletage.
La tornitura da barra può essere eseguita su torni a controllo numerico, plurimandrino e torni a fantina mobile, offrendo versatilità e capacità di lavorazione avanzate per la produzione di minuterie metalliche di precisione.